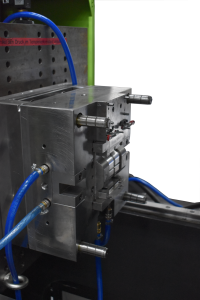
Foto (IWF): Bewegliche Werkzeughälfte des Spritzgießwerkzeuges
Die Kombination von Kunststoffen mit artfremden Materialien erfolgt im Wesentlichen über das An-, Hinter- und Umspritzen von metallischen Komponenten, die meist als Einleger für Arretierungspunkte in eine übergeordnete Struktur dienen.
Erste Ansätze für die gemeinsame Verarbeitung von Metallen und Kunststoffen als lasttragende Strukturbauteile zielen auf die vorteilhafte Kombination beider Materialien unter Ausnutzung der spezifischen Eigenschaften ab. Die metallische Komponente im hybriden Verbund sorgt für eine ausreichende Festigkeit und die geometrisch flexibel realisierbare Kunststoffapplikation bringt z.B. in Form von Rippen die nötige Steifigkeit auf.
Flächige Hybridbauteile benötigen aber häufig eine Faserverstärkung in der Kunststoffkomponente, um die Verbundsteifigkeit zu erhöhen. Meist kommen dazu in Abhängigkeit der Bauteilanforderungen flächige, vorimprägnierte, textile Halbzeuge wie Organobleche und Tapegelege oder kurzfaserverstärkte Kunststoffgranulate zum Einsatz. Aufgrund der im Vergleich zu Metallen hohen gerichteten mechanischen Eigenschaften können diese bei geeigneter Auslegung eine Wandstärkenreduzierung der Metallkomponente herbeiführen, wodurch das Bauteilgewicht reduziert und der Integrationsgrad der abzubildenden Bauteilfunktionen erhöht werden kann.
Im Sinne eines umweltbewussten Umganges mit Ressourcen und Energie ist es anzustreben, Teile des hybriden Verbundes mit nachwachsenden Materialen oder biobasierten bzw. biologisch abbaubaren Rohstoffen zu fertigen. Dazu bieten Holzfurniere ein hohes Potenzial. Aufgrund der Wachstumsrichtung des Holzes und der damit verbundenen Faserorientierung können gezielt mechanische Eigenschaften durch die Orientierung des Furniers eingestellt werden. Neben der damit erzielten belastungsgerechten Faserverstärkung bietet der Einsatz von Holzfurnieren eine wesentlich bessere Umweltbilanz im Vergleich zu üblichen Faserverstärkungen wie mittels Kohlenstoff- sowie Glasfasern oder die Verarbeitung von Stählen. Im Zuge von Nachhaltigkeitsaspekten wie der Kreislaufwirtschaft und der Entwicklung von biobasierten sowie bioabbaubaren Werkstoffen können Holzfurniere in Kombination mit Biokunststoffen einen Lösungsansatz bieten.
Um auch Märkte des Volumensegmentes zu adressieren, wird zur Hybridisierung von Holzfurniereinlegern mittels Kunststoffrippen das Spritzgießverfahren adressiert. Konventionelle Spritzgießwerkzeuge sind jedoch nicht auf den Werkstoff Holz und dessen Eigenschaften ausgelegt.
Im Rahmen des von der ZIM geförderten zweijährigen Forschungsprojektes WPPRO wird ein Werkzeug entwickelt, welches angepasst auf den Holzwerkstoff, ein Vorkonfektionieren, Umformen und Konsolidierung von Einzelfurnierlagen sowie das anschließende Anspritzen des Kunststoffes ermöglicht. Die Zielbauteile kombinieren die Flächenverstärkung des Schichtholzverbundes mit der Funktionalisierung durch Anbindungspunkte und Rippenverstärkungen sowie dem Kaschieren von Kanten. Die Einsparung dadurch entfallender, komplexer Vor- und Nachbearbeitung, macht den Prozess vor allem durch die Zeiteinsparung und Qualitätssteigerung wirtschaftlich.
Das auf Umformtechnik und Kunststoffspritzguss spezialisierte Unternehmen Werner Schmid GmbH aus Fulda übernimmt hierbei die Auslegung und Fertigung des Werkzeuges, während die Forschungsstelle, das Institut für Werkzeugmaschinen und Fertigungstechnik der Technischen Universität Braunschweig, die experimentellen Untersuchungen vornimmt.
Voruntersuchungen einzelner Prozessschritte
Zur Entwicklung des Werkzeugkonzeptes war es vorab notwendig das Zusammenspiel von Kunststoff und Holzwerkstoff in der geplanten Prozessabfolge zu analysieren, um werkzeugseitige Lösungen vorzuhalten. Dafür wurden zwei Prozesslinien untersucht, welche in Abbildung 1 dargestellt sind.
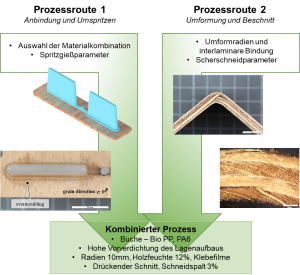
Abbildung1: Parallele Untersuchung unterschiedlicher Prozessrouten für die Ableitung des kombinierten Prozesses
In der Prozessroute „Anbinden und Umspritzen“ wurden vor allem die Anbindungsmechanik zwischen Polymer und Holzwerkstoff analysiert. Kernaspekte sind hier zum einen die vorliegenden Polaritäten der beiden Werkstoffgruppen, welche zur einer physikalischen Bindungsfestigkeit führen. Des Weiteren führt die druckbeaufschlagte Schmelze zur Ausbildung von makroskopischen Hinterschnitten im Weichholzanteil, welche für die im Vergleich höhere mechanisch basierte Bindungsfestigkeit verantwortlich sind.
Für die Verarbeitung im Spritzgießprozess muss das Holzhalbzeug durch Verpressen in der Kavität vorverdichtet werden. Dadurch wird ein ungewolltes Austreten von Kunststoffschmelze insbesondere an den Übergängen zwischen Holzwerkstoff und Spritzgießwerkzeug reduziert bzw. gänzlich vermieden. In ersten Untersuchungen zur Qualifikation der Anbindungsgüte zwischen Holzwerkstoffen und Polymeren wurden Buchenfurnier und Polyamid 6 miteinander verarbeitet. Aufgrund des polaren Charakters des Kunststoffes erfolgt eine physikalische Anbindung zwischen Holz und Polymer durch Wasserstoffbrückenbindungen. Zur Steigerung der Nachhaltigkeit wurde auch ein cellulosefaserverstärktes Polypropylen herangezogen. Aufgrund der unpolaren Polymerketten musste dies aber zuvor mit einem auf Maleinsäureanhydrid basierendem Haftvermittlersystem versetzt werden. In einem nächsten Schritt ist auch die Erprobung vollständig biobasierter Kunststoffe auf Basis von Polymilchsäure (PLA) geplant.
In der zweiten Prozessroute „Umformung und Beschnitt“ wurden mögliche Umformradien unter Einfluss der Holzfeuchtigkeit und der Haftung zwischen den Einzelfurnierlagen ermittelt. Zusätzlich dazu konnte eine Abhängigkeit der Schneidkräfte von der Faserorientierung durch wechselnde Orientierung der Einzellagen ermittelt werden. Diese Schneidkräfte von ca. 28 kN bei 80 mm Schnittkantenlänge bei einer Laminatdicke von 4 mm sind niedriger als die maximal aufbringbare Kraft während der Schließbewegung der zur Verarbeitung herangezogenen Spritzgießanlage und damit unkritisch für die Auslegung. Darüber hinaus ist die Schnittkantenqualität beispielsweise bestimmt durch den Grad von Ausbrüchen von Holzfasern an der Kante und abhängig von der Führung der Schneiden sowie deren Geometrie. Eine Auswirkung auf die Anbindung an die Schmelze im Kantenbereich ist damit zu erwarten und wird bei der Werkzeugevaluation untersucht. [https://doi.org/10.3390/f11060703]
Werkzeugkonzept
Basierend auf den Erkenntnissen der zwei Prozessrouten wurde das in Abbildung 2 dargestellte Konzept erarbeitet. Die Holzfurniere werden zu einem Mehrlagenaufbau geschichtet und im Werkzeug über Haltevorrichtungen positioniert. Im Schließprozess wird dieser Aufbau durch die Schließbewegung des Werkzeuges umgeformt. Durch eine geeignete kinematische Auslegung der Werkzeugteile wird nach erfolgter Umformung der Prozessschritt des Beschnittes durchgeführt. Dazu wird weiterhin die Schließbewegung der Anlage genutzt. Nach vollständigem Schließen kann der Kunststoff appliziert werden. Das Demonstratorbauteil vereint hierbei sowohl die Verrippung zur Steifigkeitsverbesserung als auch den polymeren Kantenabschluss.
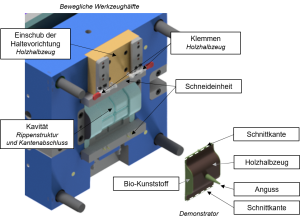
Abbildung 2: Bewegliche Werkzeughälfte inklusive der Funktionalisierung durch Haltevorrichtung und Schneideinheit
In 2023 soll die Evaluation der Prozessfähigkeit Aufschlüsse über das Konzept und die erreichbare mechanische Bauteilperformance in Abhängigkeit der Fertigungsparameter und Zustände der Halbzeuge, insbesondere der Holzfurniere, geben.
Dieses Projekt wird gefördert durch die AiF Projekt GmbH im Rahmen des zentralen Innovationsprogramm Mittelstand (ZIM) unter dem Namen „One-Shot-Spritzgießprozess für Holz-Kunststoff-Bauteile (WPPRO)“ mit einer Laufzeit über 2,5 Jahren von 2021 bis 2023. Wir danken dem Projektträger und den Projektpartnern für die gute Zusammenarbeit.
Ansprechpartner Technische Universität Braunschweig: Institut für Werkzeugmaschinen und Feritgungstechnik (IWF), Langer Kamp 19b, 38440 Braunschweig, Werner Berlin/Vicky Reichel
Ansprechpartner KMU: Werner Schmid GmbH, Fulda, Geschäftsführer Joachim Hauß