Graphen überzeugt durch außergewöhnliche mechanische, thermische und elektrische Eigenschaften und kann als funktioneller Füllstoff in Kunststoffen eingesetzt werden. Allerdings kann derweilen keine ausreichende Dispergierung des Graphens im industriellen Maßstab erreicht werden, wodurch die Nutzung dieser Eigenschaften in technischen Anwendungen behindert wird. Um die Dispergierung des Graphens zu verbessern, kommt im Rahmen der hier vorgestellten Untersuchungen die reaktive Extrusion zum Einsatz. Die Graphenpartikel werden mittels einer hochenergetischen Ultraschallbehandlung zunächst im Monomer dispergiert, wodurch die Zugfestigkeit des Materialverbundes gesteigert wird.
![Bild 1: Einfluss des Nanofüllstoffanteils auf den E-Modul und die Zugfestigkeit im Vergleich zum ungefüllten PP [10]](https://werkstoffzeitschrift.de/wp-content/uploads/2020/05/Bild1-300x111.png)
Bild 1: Einfluss des Nanofüllstoffanteils auf den E-Modul und die Zugfestigkeit im Vergleich zum ungefüllten PP [10]
Einleitung
Eine Graphenschicht besteht aus einer atomaren Lage kovalent gebundener Kohlenstoffatome und stellt somit eine zweidimensionale Struktur dar. Aufgrund der Abmessungen gehört Graphen zu der Gruppe der sogenannten Nanopartikel und weist eine spezifische Oberfläche von 2.626 m²/g auf [1]. Graphen ist in seiner Reinform das steifste und festeste bislang bekannte Material. Es weist einen Elastizitätsmodul (E-Modul) von 1 TPa auf und ist somit deutlich steifer als Stahl (210 GPa) [2]. Auch die Zugfestigkeit von Graphen ist mit 130 GPa um das Vielfache höher als die Zugfestigkeit von Stahl (310 bis 690 MPa) [2]. Zudem besitzt Graphen eine hohe elektrische und thermische Leitfähigkeit [3].
Aufgrund der hervorragenden physikalischen Eigenschaften eignet sich Graphen potenziell als Füllstoff zur Eigenschaftsmodifikation von Kunststoffen. Untersuchungen zeigen, dass bereits geringe Füllstoffanteile von weniger als 3 Gew.-% ausreichen, um deutliche Eigenschaftsverbesserung zu erzielen. Die Einarbeitung von Graphen erlaubt eine Steigerung der mechanischen Eigenschaften, der elektrischen und thermischen Leitfähigkeit sowie der Barriere- und Flammschutzeigenschaften [4]. Viele wissenschaftliche Publikationen behandeln die verschiedenen Herstellungsmethoden von Graphen und Graphen-basierten Kompositen und beschreiben die resultierenden Materialeigenschaften sowie die Dispergierung des Graphens beispielsweise in Abhängigkeit der Verarbeitungsmethode im Kleinstmengenmaßstab [5,6,7,8]. Da die geometrischen Randbedingungen der Schmelzemischaggregate im Kleinstmengenmaßstab mit den Aggregaten im Technikums- oder Industriemaßstab nicht vergleichbar sind, ist ein Ergebnistransfer nicht unmittelbar in die industrielle Praxis möglich.
Dies liegt in der fehlenden Skalierbarkeit begründet, da die Dispergierungsgüte signifikant durch das Verarbeitungsverfahren beeinflusst wird [9]. Bei der Herstellung und Weiterverarbeitung von Graphen-basierten Kompositen auf einem Doppelschneckenextruder werden keine überproportionalen Steigerungen der Eigenschaften bei geringen Füllstoffanteilen erzielt [10].
Der Einfluss des eingesetzten Nanofüllstoffs auf den E-Modul und die Zugfestigkeit eines Polypropylens (PP) des Typs 579S der Firma Sabic Europe B.V., Sittard, Niederland, ist in Bild 1 zu sehen. Als Graphen wird Nano Graphene Platelets (A.M.) der Firma Angstrom Materials Inc., Dayton, USA, verwendet. Laut Hersteller haben die Partikel eine Dicke von 10–20 nm und eine spezifische Oberfläche von mindestens 15 m²/g [11]. Der E-Modul steigt mit steigendem Nanofüllstoffanteil, da Teile der duktilen Kunststoffmatrix durch steifere Füllstoffanteile substituiert werden. Die Zugabe des Graphen ermöglicht bei einem Füllstoffanteil von 5 Gew.-% eine Steigerung des E Moduls auf 1724 MPa, was einer Steigerung von 33 % gegenüber dem ungefüllten PP entspricht. Die Zugfestigkeit wird jedoch nicht signifikant erhöht.
Die geringe Steigerung der Zugfestigkeit durch die Zugabe von Graphen ist auf mehrere Ursachen zurückzuführen [10]. Die verwendeten Graphen-Typen wurden durch chemische Exfolierung von Graphit hergestellt, sodass das Material mehrlagig vorliegt. Somit führen die Zugbeanspruchungen zu einem Abgleiten der Graphenschichten und zu einem frühen Versagen des Werkstoffverbundes. Weiterhin verbleiben auch, wie in Bild 2 zu sehen ist, nach einer Optimierung der Compoundierparameter Füllstoffagglomerate in der Kunststoffmatrix. Die Agglomerate stellen somit Schwachstellen dar. Ein weiterer Erklärungsansatz ist, dass eine unzureichende Anbindung zwischen Füllstoff und Matrix vorliegt. Zur Kompatibilitätsverbesserung müssen Anknüpfungspunkte durch funktionelle Hydroxylgruppen zwischen der Matrix und den Graphen gegeben sein.
![Bild 2: Beurteilung der Nanofüllstoff-Dispergierung nach der Compoundierung mithilfe von Dünnschnitten [10]](https://werkstoffzeitschrift.de/wp-content/uploads/2020/05/Bild2-300x104.jpg)
Bild 2: Beurteilung der Nanofüllstoff-Dispergierung nach der Compoundierung mithilfe von Dünnschnitten [10]
Für die reaktive Extrusion von PA6 wird ein Doppelschneckenextruder eingesetzt, der als chemischer Reaktor dient [12]. Aufgrund der hohen Reaktionsgeschwindigkeit kommt die anionische aktivierte Polymerisation zum Einsatz. Dafür werden neben dem Monomer Caprolactam ein anionischer Katalysator sowie ein Aktivator benötigt [12]. Aufgrund des thermodynamischen Gleichgewichts stellt sich abhängig von der Temperatur während der Polymerisation ein Gleichgewichtszustand zwischen Produkt (PA6) und Edukt (Caprolactam) ein. Das Restmonomer muss aus dem Produkt entfernt werden, da die niedermolekularen Bestandteile eine weichmachende Wirkung haben und zu einer signifikanten Verschlechterung der Zugfestigkeiten führen [13]. Dies kann mithilfe einer integrierten Entgasung während der reaktiven Extrusion erfolgen, wobei ein Restmonomergehalt von weniger als 4 Gew.-% im Produkt angestrebt wird.
Herstellung, Weiterverarbeitung und Analyse der hergestellten Compounds
Für die Polymerisation von PA6 im Doppelschneckenextruder kommt Caprolactam vom Typ AP-Nylon der Firma Brüggemann Chemical KG, Heilbronn, zum Einsatz. Zum Reaktionssystem werden zusätzlich 1 Gew.-% C20P (Aktivator) und 3 Gew.-% C10 (Katalysator) von der Firma Brüggemann Chemical eingesetzt. Als Graphen wird Nano Graphene Platelets (A.M.) der Firma Angstrom Materials Inc., Dayton, USA, verwendet. Laut Hersteller haben die Partikel eine Dicke von
10–20 nm und eine spezifische Oberfläche von mindestens 15 m²/g [11].
Bild 3 zeigt den schematischen Versuchsaufbau zur Verbesserung der Dispergierung mithilfe der reaktive Extrusion und einer Ultraschallbehandlung.
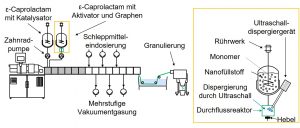
Bild 3: Schematischer Versuchsaufbau zur Verbesserung der Dispergierung durch eine Ultraschallbehandlung
Im ersten Prozessschritt wird das pulverförmige Graphen in die geschmolzene Monomer-Aktivator-Lösung gegeben. Die Vordispergierung des Graphens erfolgt innerhalb des Durchflussreaktors erfolgt mithilfe eines Ultraschall-Dispergiersystems der SinapTec Ultrasonic Technology SAS, Lezennes, Frankreich. Die Ultraschall-Sonotrode des Ultraschall-Dispergiersystems beschallt die Graphenlösung mit einer Leistung von ca. 750 W. Durch eine Variation der Beschallungsdauer werden unterschiedliche Energieeinträge in der Graphenlösung realisiert.
Im zweiten Prozessschritt werden die beiden Monomer-Gemische mithilfe von Feinprüf-Zahnraddosierpumpen des Typs 2,4 cm³/U der Firma Mahr Metering Systems GmbH, Göttingen, in den Doppelschneckenextruder des Typs ZSK26Mc der Coperion GmbH, Stuttgart, eindosiert. Der eingesetzte Doppelschneckenextruder hat einen Schneckendurchmesser von 26 mm und ein Länge-zu-Durchmesser-Verhältnis (L/D) von 56. Nach der Einarbeitung und der Polymerisation ermöglicht eine dreistufige Vakuumentgasung in Kombination mit einer dreistufigen Schleppmitteleindosierung die Entfernung des Restmonomers.
Bei der Herstellung der Referenzpunkte ohne Ultraschallbehandlung wird das Graphen in Pulverform mithilfe eines gravimetrischen Dosiersystems der Motan-Colortronic GmbH, Friedrichsdorf im Einzugsbereich in den Doppelschneckenextruder gefördert. Die eingesetzte Schneckenkonfiguration ist in eine Reaktionszone, welche eine Länge von
24 L/D vorweist, drei Entgasungszonen mit jeweils 6 L/D und eine abschließende Polymerzone unterteilt. Die Entgasungszonen sind von der Reaktionszone sowie untereinander durch gegenfördernde und damit vollgefüllte Zahnmischelemente getrennt. Die Herstellung der Komposite erfolgt mit einem konstanten Gehäusetemperaturprofil. Das erste Gehäuse wird auf eine Gehäusetemperatur von 170 °C, die Gehäuse 2-7 auf eine Temperatur von 260 °C, die Gehäuse 8-14 auf eine Temperatur von 220 °C und das Werkzeug auf eine Temperatur von 260 °C eingestellt. Als Schleppmittel wird destilliertes Wasser mit einem Durchsatz von 0,6 kg/h
dem Prozess jeweils zu Beginn der Entgasungszonen zugegeben.
Die Weiterverarbeitung der hergestellten Komposite zu Vielzweckprüfkörper Typ 1A
erfolgt unter konstanten Bedingungen auf einer Spritzgießmaschine des Typs IntElect 100-340 der Sumitomo Demag Plastics Machinery GmbH, Schwaig. Anhand der Prüfkörper werden die mechanischen Eigenschaften (E-Modul, Zugfestigkeit, Bruchdehnung) im Zugversuch nach DIN EN ISO 527 bestimmt [14].
Drehzahleinfluss auf die Festigkeit und Steifigkeit
Im ersten Schritt wird der Drehzahleinfluss, welche mit der eingebrachten Scherenergie korreliert, auf die Steifigkeit und Festigkeit des Materialverbundes analysiert. Die Ergebnisse der mechanischen Prüfungen (Bild 4) lassen keine signifikanten Unterschiede der Messwerte in Abhängigkeit der Drehzahl erkennen. Ein Erklärungsansatz ist, dass der Scherenergieeintrag nicht ausreicht, um die Graphenschichten voneinander zu trennen. Der mehrschichtige Aufbau der verwendeten Graphentypen ermöglicht ein leichtes Gleiten der Schichten bei geringen Spannungen, da nur geringe Bindungskräfte zwischen den einzelnen Schichten vorliegen. Daher lässt sich eine einwirkende Zugkraft auf das PA6 nicht über Schubkräfte auf die Graphene übertragen. Demnach ist auch bei der Verwendung der reaktiven Extrusion keine wesentliche Steigerung der Dispergierung mit steigender Drehzahl gegeben.
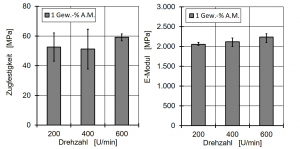
Bild 4: Zugfestigkeit und E-Modul in Abhängigkeit der Drehzahl ohne Ultraschallbehandlung
Einfluss der Beschallungsenergie auf die Festigkeit und Steifigkeit
Mithilfe einer Ultraschallbehandlung soll im Kunststoffverbund die Dispergierung der Graphene und damit eine Steigerung der Festigkeit und Steifigkeit erreicht werden. Der Einfluss der Vordispergierung und des Energieeintrages bei der Beschallung mit Ultraschall auf den E-Modul und die Zugfestigkeit ist in Bild 5 dargestellt.
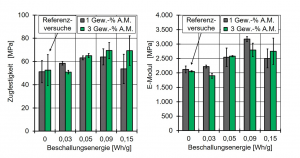
Bild 5: Einfluss der Beschallungsenergie auf den E-Modul und auf die Zugfestigkeit
Im Vergleich zu den konventionell hergestellten Graphen-basierten Kompositen resultiert mit steigender Beschallung mittels Ultraschalls eine Zunahme der Zugfestigkeit. Die Festigkeit steigt von 52,58 MPa (ohne Beschallungsenergie) auf 69,34 MPa (0,15 Wh/g) bei 3 Gew. % A.M. an. Der Anstieg könnte auf eine feinere Graphen-Dispergierung im Kunststoffverbund und damit einer geringeren Anzahl an großen Agglomeraten zurückzuführen sein. Tendenziell resultiert auch eine erhöhte Steifigkeit mit steigender Beschallungsenergie.
Zusammengefasst lässt sich ableiten, dass mit steigender Beschallungsenergie eine feinere Füllstoffdispergierung in der PA6-Matrix vorliegt. Jedoch steigt die Zugfestigkeit des Kunststoffverbundes nur leicht an, wodurch davon auszugehen ist, dass bei allen Versuchspunkte noch makroskalige Agglomerate vorhanden sind. In weiteren Untersuchungen wird diese Aussage überprüft. Weiterhin müssen zusätzliche Analysen zeigen, ob die Weiterverarbeitung im Spritzgießverfahren zu einer Reagglomeration führt oder ob eine unzureichenden Beschallungsenergie vorliegt.
Fazit und Ausblick
Die Ergebnisse dieser Untersuchung zeigen, dass das Potenzial von Graphen als funktioneller Füllstoff bei der Herstellung und Verarbeitung von Verbundwerkstoffen auf Graphenbasis unter industriellen Bedingungen derzeit nicht genutzt werden kann. Das in diesem Forschungsprojekt verwendete, kommerziell erhältliche Graphen entspricht aufgrund seines mehrschichtigen Aufbaus nicht einem idealen Graphen. Um eine signifikante Verbesserung der mechanischen Eigenschaften des Graphens bei niedrigstem Füllstoffgehalt zu erreichen, muss das Graphen bei der Herstellung und Verarbeitung der graphenbasierten Komposite exfoliert werden. Dies konnte unter den gegebenen Bedingungen nicht erreicht werden.
Lösungsansätze liegen in einer weiteren Erhöhung des Energieeintrages sowie die Verwendung eines passenden Lösemittels zur Anpassung der Oberflächenspannung im Monomer. Auf diese Weise soll die Dispergierung der Graphene weiter verbessert werden.
Dank
Das IGF-Vorhaben 20718 N der Forschungsvereinigung Institut für Kunststoffverarbeitung an der RWTH Aachen wird über die AiF im Rahmen des Programms zur Förderung der Industriellen Gemeinschaftsforschung und -entwicklung (IGF) vom Bundesministerium für Wirtschaft und Energie aufgrund eines Beschlusses des Deutschen Bundestages gefördert. Allen Institutionen gilt unser Dank. Zusätzlich bedanken wir uns bei der BASF SE, Ludwigshafen, Gustav Grolman GmbH, Neuss, sowie der Brüggemann Chemical KG, Heilbronn, für die Bereitstellung von Versuchsmaterialien.
Literatur
[1] KIM, H.; ABDALA, A.; MACOSKO, C.: Graphene/polymer nanocomposites. Macromolecules 43 (2010) 16, S. 6515–6530
[2] HABERHAUER, H.; BODENSTEIN, F.: Maschinenelemente: Gestaltung, Berechnung, Anwendung. Berlin: Springer-Verlag, 2014
[3] BALANDIN, A.: Thermal properties of graphene and nanostructured carbon materials. Nature materials 10 (2011) 8, S. 569–581
[4] KIM, I.; JEONG, Y.: Polylactide/exfoliated graphite nanocomposites with enhanced thermal stability, mechanical modulus, and electrical conductivity. Journal of Polymer Science Part B: Polymer Physics 48 (2010) 8, S. 850–858
[5] BAO, C.; SONG, L.; XING, W.; YUAN, B.; WILKIE, C.; HUANG, J.; HU, Y.: Preparation of graphene by pressurized oxidation and multiplex reduction and its polymer nanocomposites by masterbatch-based melt blending. Journal of Materials Chemistry 22 (2012) 13, S. 6088–6096
[6] CHATTERJEE, S.; NÜESCH, F.; CHU, B.: Comparing carbon nanotubes and graphene nanoplatelets as reinforcements in polyamide12 composites. Nanotechnology 22 (2011) 27, S. 275
[7] STEURER, P.; WISSERT, R.; THOMANN, R.; MÜLHAUPT, R.: Functionalized graphenes and thermoplastic nanocomposites based upon expanded graphite oxide. Macromolecular rapid communications 30 (2009) 4-5, S. 316–327.
[8] DU, J.; CHENG, H.: The fabrication, properties, and uses of graphene/polymer composites. Macromolecular Chemistry and Physics 213 (2012) 10-11, S. 1060–1077
[9] RODRIGUES, P.; SANTOS, R.; PAIVA, M.; COVAS, J.: Development of Dispersion during Compounding and Extrusion of Polypropylene/Graphite Nanoplates Composites. International Polymer Processing 32 (2017) 5, S. 614-622
[10] ADAMY, M.: Einsatz von Graphen als funktioneller Füllstoff bei der Schmelze-compoundierung. RWTH Aachen, Dissertation, 2019
[11] N.N.: Nano Graphen Platelests (A.M.). Datenblatt, Angstrom Materials Inc., Dayton, USA, 2020
[12] GREFENSTEIN, A.: Reaktive Extrusion und Aufbereitung: Maschinentechnik und Verfahren. München, Wien: Carl Hanser Verlag, 1996
[13] BECKER, G.; BRAUN, D.; BOTTENBRUCH, L.; BINSACK, R.: Polyamide Kunststoff-Handbuch – Technische Thermoplaste. München, Wien: Carl Hanser Verlag, 1998
[14] N.N.: DIN EN ISO 527-2: Kunststoffe – Bestimmung der Zugeiegenschaften – Teil 2: Prüfbedingungen für Form- und Extrusionsmassen. Berlin: Beuth Verlag, 2012
Autor*innen
Prof. Dr.-Ing. Christian Hopmann;
Tobias Horn, M.Sc.;
Dr.-Ing. Martin Facklam
Institut für Kunststoffverarbeitung (IKV) an der RWTH Aachen University