Mit additiven Fertigungsverfahren lassen sich aus virtuellen Modellen hochkomplexe, auf konventionellem Wege nicht herstellbare Bauteile werkzeuglos fertigen. Neben dem hohen Maß an Design- und Gestaltungsfreiheit ermöglichen diese Verfahren insbesondere die Realisierung individualisierter Produkte. Da einerseits die Verarbeitung anwendungsrelevanter technischer Kunststoffe möglich ist, andererseits die Prozessstabilität und die Reproduzierbarkeit der Bauteileigenschaften sich stetig verbessert und die Outputraten steigen, entwickelt sich die Additive Fertigung derzeit rasant von Rapid Prototyping hin zu Rapid Manufacturing Technologien. Maßgeblich beteiligt an diesem Wandel sind pulverbasierte additive Fertigungsverfahren. Merkmal dieser Verfahren ist der schichtweise Aufbau des Bauteils in einem Pulverbett. Die Bauteilherstellung erfolgt durch Auftragen einer dünnen Kunststoffpulverschicht auf ein Pulverbett und das anschließende lokale Verschmelzen der Pulverpartikel unter Wärmeeinwirkung. Schicht für Schicht werden so dreidimensionale Bauteile erzeugt. Das Pulverbett dient dabei gleichzeitig als Stützmaterial. Sind alle Schichten erstellt, wird das Pulverbett mit den Bauteilen abgekühlt, das lose Pulver abgetrennt und anteilig wiederverwendet.
Da keine Stützstrukturen benötigt werden, bieten diese Verfahren eine fast uneingeschränkte Designfreiheit. Außerdem ist es möglich gleichzeitig mehrere Bauteile in einem Bauraum herzustellen. Zusammen mit der hohen mechanischen Stabilität der resultierenden Kunststoffbauteile führt es dazu, dass pulverbasierte Verfahren aus der Masse der 3D Druckverfahren herausstechen und ein hohes Potential für Rapid Manufacturing aufweisen.
Die Liste der heute relevanten pulverbasierten additiven Fertigungsverfahren umfasst Selektives Lasersintern (SLS) sowie die mit IR-absorbierender Tinte arbeitenden InkJet-Verfahren Multi Jet Fusion (MJF) von HP und High Speed Sintering (HSS) von Voxeljet. In Abbildung 1 sind die wichtigsten Kenngrößen der SLS und InkJet Verfahren zusammengefasst.
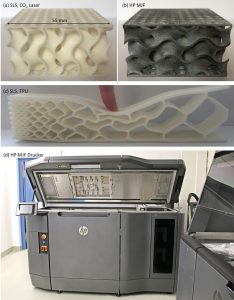
Abbildung 2: Additiv gebaute Gyroidstrukturen aus dem SLS (a) und HP MJF Drucker (b), Kernstruktur
aus Thermoplastischen Polyurethan (TPU) mit Härtegradient hergestellt im SLS Prozess (c), HP MJF Drucker und Processing Station (rechts) im Democenter der Additiven Fertigung der Neue
Materialien Bayreuth GmbH (d)
Selektives Lasersintern (SLS) Prozess
SLS bezeichnet ein additives Fertigungsverfahren, bei dem ein Kunststoffpulver mittels eines Lasers schichtweise zu einem Bauteil (Abbildung 2a und c) gesintert wird. Dabei erfolgt der Energieeintrag örtlich durch den Laserpunkt. Beim Druckprozess wird der Bauraum auf eine Temperatur knapp unter der Kristallitschmelztemperatur aufgeheizt. Diese hohe Temperatur im Bauraum führt bei Polyamid 12 (PA12) durch Nachkondensation zu Molekulargewichtsaufbau. Mit zunehmendem Materialdurchlauf ändert sich dadurch die Materialstruktur, so dass das überschüssige Pulvers im Pulverbett nur begrenzt wiederverwendbar ist.
Je nach Art des Systems werden unterschiedliche Lasertypen eingesetzt: Leistungsstarke CO2 Laser oder Diodenlaser mit deutlich geringeren Leistungen. Die Pulveroberfläche absorbiert nur einen Teil der durch den Laser aufgebrachten Energie. Daher werden teure CO2 Laser Systeme mit einer hohen Leistung verwendet, so dass unter Berücksichtigung des Absorptionsgrads genügend Energie zum Verschweißen eingebracht wird. SLS-Anlagen, die mit einem Diodenlaser ausgestatten sind, sind im Vergleich zu klassischen SLS-Anlagen deutlich günstiger. Die Verwendung eines Diodenlasers hat dafür einen Nachteil: die geringe Strahlungsenergie von max. 5 Watt erfordert spezielle IR-absorbierenden Additive im Kunststoffpulver, um den Absorptionsgrad der Laserstrahlung zu erhöhen und genügend Energie in das Material einzukoppeln und es damit zum Schmelzen zu bringen. Solche Systeme können
z. B. zur Herstellung kleiner Bauteile eingesetzt werden. Es werden Carbonbasierte Absorber dem Kunststoff beigemischt, wodurch die gedruckten Bauteile grau / schwarz sind und die Materialauswahl insgesamt eingeschränkt ist.
HP Multi Jet Fusion Technologie: Effiziente Fertigung von Kleinserien
HP MJF ist neben dem HSS Verfahren von Voxeljet eines der produktivsten Verfahren des 3D-Kunststoffsdrucks, das gegenwärtig zur Verfügung steht. Bei diesem Verfahren wird der Wärmeeintrag für das Verschweißen der Einzelschichten flächig über Infrarot-Strahlung und nicht punktweise durch einen Laser eingebracht. Das selektive Verschmelzen des Baumaterials wird durch lokales Aufbringen einer im Infrarot-Bereich absorbierenden Tinte realisiert. Dadurch wird der Absorptionsgrad nur lokal erhöht. Die Intensität der IR-Lampen ist so gewählt, dass es lokal zu einer Verschweißung kommt, an den anderen Stellen aber nicht genug Energie für ein Versintern eingetragen wird. Die Bauzeit ist nicht mehr von der Anzahl an Bauteilen pro Druckjob abhängig, sondern lediglich von der Gesamthöhe des Druckjobs. Dabei liegen die Aufbauraten je nach gewähltem Druckmodus in der Größenordnung 1 min/mm. Verbunden mit dem Drucksystem ist eine „Processing Station“ (Abbildung 2d), in der das gesamte Pulvermanagement vom Auspacken des Druckjobs bis zur Neubefüllung der Baueinheit mit Kunststoffpulver erfolgt. Der Anteil an Recyclingpulver – also Pulver, das schon einmal im Druckbett genutzt wurde – kann dabei auf bis zu 85 % gesteigert werden, da die Bauraumtemperatur im Vergleich zum SLS Prozess geringer ist. Die Aufbereitung des Pulvers erfolgt automatisch mittels integrierter Filtersysteme. Damit ist eine fast vollständige Umsetzung von Pulver in Bauteile möglich.
Die Bauteile weisen wie die SLS Bauteile eine hohe mechanische Belastbarkeit auf und sind aufgrund der im Prozess aufgetragenen Tinte schwarz (Abbildung 2b). Das Verfahren eignet sich zur effizienten Fertigung von Kleinserien, z. B. von Automobilbauteilen, Brillengestellen oder Kopfbügel für Schutzvisiere.
Anforderungen an Materialien und Prozesse für Rapid Manufacturing
Aktuell ist das Werkstoffspektrum für pulverbasierte Fertigung eingeschränkt. Für eine erfolgreiche industrielle Anwendung sind jedoch Kunststoffpulver erforderlich, welche sehr spezifische Anforderungen der Industrie abdecken können. Dazu gehören technische und Hochleistungsthermoplaste, biobasierte Polymere mit einer verbesserten Recyclingfähigkeit, biokompatible und flammgeschütze sowie farbige Materialien. Bei der Entwicklung neuer Materialien muss darauf geachtet werden, dass eine Reihe an Eigenschaften erfüllt ist. Dazu gehören zum einen der strukturelle Aufbau und die thermischen Eigenschaften des Kunststoffes, zum anderen die Pulvergröße, -form und -verteilung.
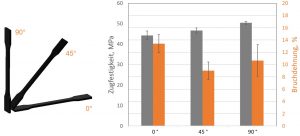
Abbildung 3: Einfluss der mechanischen Eigenschaften von PA12 Bauteilen als Funktion der Orientierung im Bauraum des HP MJF
Für den Einsatz additiver Fertigungsverfahren in der Serienproduktion ist es nötig, Zusammenhänge zwischen Material, Prozessparametern und Bauteileigenschaften herzustellen, um letztere vorhersagen und einstellen zu können. Dazu müssen z. B. auch Kennwerte der Maßhaltigkeit sowie der mechanischen und Oberflächeneigenschaften der Bauteile in Abhängigkeit der Positionierung und Orientierung im Bauraum ermittelt werden. In Abbildung 3 ist der Einfluss der Lage des Bauteils gefertigt aus PA12 im HP MJF Drucker in Abhängigkeit der Raumausrichtung auf die mechanischen Eigenschaften gezeigt. Während die Zugfestigkeit bei allen drei Winkelanordnungen (0°, 45% und 90%) nur geringfügige Unterschiede aufweist, ist die Bruchdehnung stark von der Orientierung abhängig und ist somit eine sensible Größe. Insgesamt bildet die Orientierung einen entscheidenden Faktor für die Ausbildung der Bauteileigenschaften (Zugfestigkeit, Maßhaltigkeit, Oberflächenrauigkeit) und muss bereits bei Erstellung des Druckjobs berücksichtigt werden.
Autor*innen
Julia Gensel, Thomas Neumeyer, Volker Altstädt
Neue Materialien Bayreuth GmbH, Bayreuth, Germany