Einleitung
Laufende Spezialdrahtseile für verschiedenste Anwendungen, beispielsweise im Kran-, Aufzug-, Bergbaubereich, sind in unterschiedlichen Drahtfestigkeiten verfügbar. Zusammen mit dem jeweiligen Seilaufbau und dem sich ergebenden metallischen Querschnitt bestimmen sie maßgeblich die Bruchkraft eines Drahtseiles. Diese ist gleichzeitig Basis für aktuelle normative Nachweise von Drahtseilen in Seiltrieben. Bei Berücksichtigung weiterer Seiltriebkomponenten ist es vielmals wirtschaftlicher, bei der Auslegung kleine Seildurchmesser und hohe Bruchkräfte auszuwählen. Dies führt häufiger zur Verwendung hoher Drahtfestigkeiten sowie weiter gesteigerter Bruchkraft durch den Einsatz verdichteter Seilkonstruktionen. Diese Verdichtung kann einerseits durch die sog. Litzenverdichtung vor der Verseilung und andererseits durch Hammerverdichtung des fertigen Drahtseiles realisiert werden. Hinsichtlich der Lebensdauer der Seile müssen jedoch hochfeste Drahtseile nicht zwangsläufig vorteilhaft sein. Durch eine Vielzahl von heutigen und auch früheren Versuchen sowie aufgrund von Erfahrungsberichten aus der Praxis, ist ein Trend festzustellen, dass höhere Festigkeiten und Verdichtungsgrade nicht zu einer längeren Lebensdauer führen. Aktuelle Untersuchungen innerhalb einer umfangreichen Versuchsreihe an der TU Dresden werden unter diesem Gesichtspunkt durchgeführt und sollen einen Beitrag leisten, die Zusammenhänge zwischen Drahtfestigkeit, Verdichtung und Lebensdauer besser in den vorhandenen Methoden zur Abschätzung der Betriebs- und Lebensdauer zu berücksichtigen. Die Betriebsdauer steht in der Seiltechnik für das Erreichen bestimmter Ablegekriterien und die Lebensdauer für das komplette Seilversagen. Für deren rechnerische Abschätzung in Seiltrieben stehen für Hersteller, Betreiber sowie wissenschaftliche Betrachtungen zwei Methoden zur Verfügung – die Methode nach Feyrer (Stuttgart) [Fey00] und die nach Jehmlich/Steinbach (Leipzig) [Jeh85], [Ste04]. Beide Herangehensweisen liefern für den durch Versuche abgedeckten Parameterbereich vergleichbare Ergebnisse. Schwerpunkt der hier vorgestellten Arbeiten ist die Weiterentwicklung der Methode Leipzig in Hinblick auf moderne Seilkonstruktionen, bei denen hohe Drahtfestigkeiten und die genannten Verdichtungsverfahren zum Einsatz kommen. Im Widerspruch dazu liefert die rechnerische Abschätzung mit den beiden genannten Methoden hingegen bei höheren Festigkeiten längere Lebensdauern. Neben einem umfangreichen Versuchsprogramm von Dauerbiegeversuchen sind auch weiterführende Untersuchungen hinsichtlich der Seildrähte Bestandteil der Betrachtungen. Derzeit liegen Ergebnisse von Dauer- und Umlaufbiegeversuchen sowie werkstoffanalytische Erkenntnisse vor.
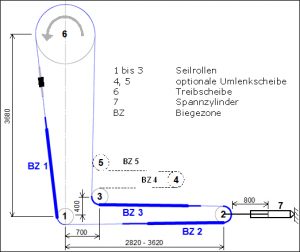
Abbildung 1: Dauerbiegeprüfstand für Drahtseile
Dauerbiegeversuche
Bei Dauerbiegeversuchen werden die Seile zyklisch unter einer bestimmten Last über Seilrollen hin und her gefahren, bis diese sog. Biegewechsel zu fortschreitenden Ermüdungsdrahtbrüchen und schließlich zum Versagen bzw. Riss des Seiles führen. Die hier beschriebenen Versuche werden an Seilprüfständen der TU Dresden durchgeführt. Eine beispielhafte Versuchsreihe wird mit zwei Seilkonstruktionen und mit jeweils zwei verschiedenen Drahtfestigkeiten durchgeführt. Für eine Erfüllung der beschriebenen Ziele war es wichtig, gleiche Seilkonstruktionen unterschiedlicher Fes-
tigkeit auszuwählen. Ausgewählt wurden daher die unverdichtete Konstruktion 8×19 W IWRC sowie 8xK26 WS IWRC mit verdichteten Außenlitzen.
Um eine breite Datenbasis zu schaffen, werden die Versuche für jedes der 4 Prüfseile mit 3 Sicherheitsfaktoren (Sicherheit gegen die rechnerische Bruchkraft) und 3 D/d-Verhältnissen (Seilrollendurchmesser D zu Seildurchmesser d) durchgeführt. Beide Parameter bestimmen maßgeblich die Betriebs- und Lebensdauer. Es ergeben sich 36 Dauerbiegeversuche innerhalb dieser Versuchsreihe. Bei jedem Versuch wird anhand der Drahtbruchentwicklung die nach normativen Kriterien definierte Ablegereife – Zustand des Drahtseiles bei dem es abgelegt/gewechselt werden muss – erfasst. Aufgrund der 3 unabhängigen Biegezonen im verwendeten Prüfstand nach Abbildung 1 können daraus bei jedem Versuch 3 Betriebsdauerwerte gewonnen werden, was zur statistischen Absicherung dient. Weiterführend wird jeder Versuch bis zum Versagen des Seiles in einer der 3 Biegezonen gefahren. Pro Versuch wird dementsprechend ein Lebensdauerwert gewonnen.
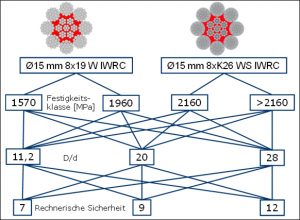
Abbildung 2: Versuchsplan
Abbildung 2 zeigt die Übersicht des Versuchsplans mit den wesentlichen Parametern. Die Seilrollen in dieser Versuchsreihe sind Stahlseilrollen mit gehärteten Rillen und mit standardisierter Rillenform nach DIN 15061-1. Die Biegelängen sowie die entstehende Seiltemperatur wurden in Anlehnung an die Oipeec-Recomendations beachtet [Oip88].
Lebensdauerabschätzung
Für einen Vergleich der Ergebnisse aus Versuchen mit der rechnerischen Abschätzung nach Methode Leipzig wird im Folgenden dargestellt, in welcher Weise die Nennfestigkeit des Drahtes in der Berechnung einfließt. Für eine vollständige Beschreibung der Abschätzungsmethode wird auf die VDI 2358, TGL 34022/3 und die Literatur, wie u. a. [Jeh85], [Gro09], [Ste04] verwiesen. Zusammenfassend wird aus den für die Seillebensdauer relevanten Parametern des Seiltriebs und des Seiles die sog. Anstrengung y der Seildrähte im Drahtseil aus Zug-, Druck- und Biegespannungen berechnet (Gleichungen (1) bis (4)). Die einfache lineare Zusammenfassung der einzelnen Spannungen wurde analog der Schubspannungshypothese als Vergleichsspannung in Übereinstimmung mit Lebensdauerversuchen definiert und stellte ein brauchbares Maß für die Beanspruchung der Seildrähte dar [Jeh85]. Die auf die Nennfestigkeit R der Seildrähte bezogene Summe der unterschiedlich konstanten und schwingenden Spannungsanteile im Bereich der berührten Drahtkuppen ist weiterhin die geeignete Modellgröße für die Versuchsauswertung in einparametrischen Wöhlerlinien [Ste04].
![Abbildung 3: Wöhlerliniensystem der Methode Leipzig nach [Ste04] – 1) Linie Grenzzustand PA=10% (Ablegereife); 2) Streuspann; 3) Linien Litzenbruch](https://werkstoffzeitschrift.de/wp-content/uploads/2021/03/Abb3-300x204.jpg)
Abbildung 3: Wöhlerliniensystem der Methode Leipzig nach [Ste04] – 1) Linie Grenzzustand PA=10% (Ablegereife); 2) Streuspann; 3) Linien Litzenbruch
Wird der Einfluss der Nennfestigkeit der Seildrähte auf die berechneten Biegewechselzahlen betrachtet, wird deutlich, dass bei gleicher Seilkraft und zunehmender Drahtnennfestigkeit die Anstrengung y sinkt und damit die berechneten Biegewechselzahlen NE steigen. Die Berechnung der Anstrengungen mit gleicher rechnerischen Sicherheit und höheren Drahtnennfestigkeiten, ergeben ebenfalls kleinere Werte und höhere Biegewechselzahlen. Dies ist durch den nichtlinearen Einfluss der Seilkraft im Druckspannungsanteil zu erklären. Einen beispielhaften Vergleich zeigt Tabelle 1, die einen Auszug aus den Parametern des Versuchsplanes darstellt.
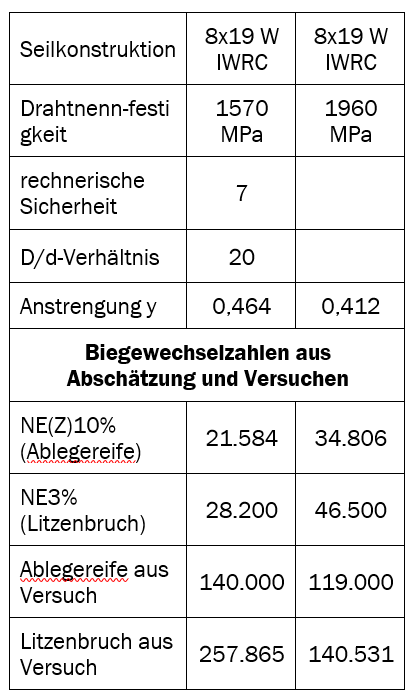
Tabelle 1: Gegenüberstellung von rechnerischer Abschätzung und Versuchswerten bei gleicher Sicherheit (Bsp.)
Zu erkennen ist ein deutlicher Unterschied in den berechneten Biegewechselzahlen. Die gegenläufigen Beobachtungen bei langjährigen Versuchen sowie Erfahrungsberichte waren Motivation der laufenden Versuchsreihe, die diesen Trend bisher bestätigt. Neben dieser Versuchsreihe werden auch weitere vorliegende Ergebnisse im Zuge der Betrachtungen ausgewertet.
Ergebnisse
Im Folgenden wird der derzeitige Ergebnisstand zusammenfassend dargestellt. Zum jetzigen Zeitpunkt sind 25 Dauerbiegeversuche abgeschlossen. Als Gegenüberstellung einiger bisheriger Ergebnisse sind in Abbildung 4 und 5 die Werte für die Betriebsdauern (Ablegereife) und Lebensdauern (Litzenbruch) dargestellt. Die Ergebnispunkte in Abbildung 4 sind dabei die Mittelwerte aus den Biegewechselzahlen bis zur Ablegereife der drei Biegezonen. Der in Tabelle 1 dargestellte Trend wird auch bei Betrachtung der weiteren Ergebnisse für beide Seilkonstruktionen deutlich.
Allerdings muss hier hervorgehoben werden, dass die Unterschiede zwischen der unverdichteten und der verdichteten Seilkonstruktion nicht allein mit der höheren Drahtnennfestigkeit in Verbindung stehen müssen. Einflüsse aus der Litzenverdichtung können ebenfalls für eine Verkürzung der Seillebensdauer in Frage kommen. Die getrennte Untersuchung vom Einfluss der Drahtnennfestigkeit und von Verdichtungsprozessen bedarf einer weiter gefassten Versuchsreihe, bei der auch Drahtseile vor und nach dem Verdichten in Kombination mit verschiedenen Drahtnennfestigkeiten getestet werden. Derartige Versuchsreihen sind derzeit in Vorbereitung und werden durch Drahtseilhersteller unterstützt.
Der dargestellte Umfang der Untersuchungen lässt daher noch keine abschließenden Rückschlüsse im Zusammenhang mit Verdichtungen zu. Zur Schaffung von Grundlagen für weitere Versuchsreihen von Dauerbiegeversuchen sind derzeit unterschiedliche Analysen von Seildrähten in Ausarbeitung, die in den folgenden Abschnitten vorgestellt werden.
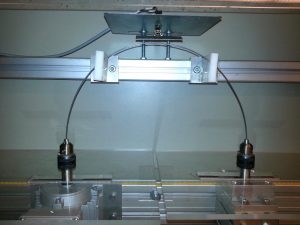
Abbildung 6: Versuchsaufbau eines Umlaufbie-geversuchs (OTH Regensburg)
Umlaufbiegeversuche
Bei Umlaufbiegeversuchen werden Drähte definiert gebogen und gleichzeitig in Rotation versetzt (siehe Abbildung 6). Relevant für eine Bewertung ist die Anzahl Umdrehungen bis zum Brechen des Drahtes. Eine systematische Untersuchung von Seildrähten durch [Bri00] mittels Umlaufbiegeversuche nach [Wol87] hat bereits gezeigt, dass mit steigender Drahtnennfestigkeit die Lebensdauer von Drähten leicht abnimmt.
Dies wurde im Kontrast zu den bisherigen Dauerbiegeversuchen gesehen, die in [Fey00] zusammengefasst sind. Bei diesen Dauerbiegeversuchen, gefahren mit gleicher durchmesserbezogener Seilzugkraft (S/d2), wurde ein mäßiger Anstieg der Seillebensdauer festgestellt. Die hier dargestellten aktuellen Dauerbiegeversuche werden bei gleicher Seilsicherheit, d. h. mit unterschiedlichem S/d2, gefahren, wodurch sie dennoch mit den bisherigen Erkenntnissen zu vergleichen sind.
Ergänzend zu den bisherigen umfassenden Versuchsreihen durch [Bri00] wurden Umlaufbiegeversuche an den Drähten der hier verwendeten Versuchsseile durchgeführt, um in erster Linie zu klären, welchen Einfluss Verdichtungsprozesse auf die dynamische Beanspruchbarkeit der Drähte haben. Dazu wurden mehrere Drahtproben aus den Versuchsseilen entnommen, gerichtet und an der OTH Regensburg geprüft. Zunächst war dabei unklar, inwiefern die Vergleichbarkeit durch das aufwändige Richten der verdichteten Drähte gegeben ist. Die Versuchsergebnisse zeigen jedoch für die hier geprüften Drähte, dass eine Reduktion der Umlaufbiegewechselzahlen von verdichteten gegenüber unverdichteten Drähten – hier nur Litzenverdichtung – nicht festzustellen ist. Wie Abbildung 7 zeigt, liegen die Ergebnisse nahezu auf einer Zeitfestigkeitsgeraden in der doppeltlogarithmischen Darstellung.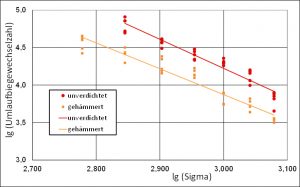
Abbildung 8: Umlaufbiegewechselzahlen von Drahtproben aus einem Drahtseil vor und nach Hammerverdichtung
Weitere Umlaufbiegeversuche an Drähten, die aus einem Drahtseil vor und nach einer Hammerverdichtung entnommen wurden, zeigen eine deutliche Reduktion der Umlaufbiegewechselleistung (vgl. Abbildung 8). Es wird angenommen, dass dies mit den durch den Hammerprozess entstandenen Kerben im Draht zusammenhängt. Vergleichende Dauerbiegeversuche an entsprechenden Drahtseilen liegen derzeit noch nicht ausreichend vor.
Die hier dargestellten Ergebnisse lassen keine unmittelbaren Rückschlüsse auf die Lebensdauer der Drahtseile im Dauerbiegeversuch zu. Bei Umlaufbiegeversuchen liegt in den Drähten reine wechselnde Biegespannung vor, wohingegen bei dem kombinierten Spannungszustand in den Drähten der Drahtseile auch Druck und Zugspannung wesentlich zur Drahtermüdung beitragen.
Werkstoffuntersuchungen
In direktem Zusammenhang mit der vorgestellten Versuchsreihe wurden am Institut für Werkstoffwissenschaft der TU Dresden Analysen ausgewählter Drahtproben durchgeführt. Ziel dabei war es den Einfluss von Verdichtungsprozessen auf das Ermüdungsverhalten von Drähten in laufenden Drahtseilen zu ergründen. Ein spröderes Ermüdungsverhalten von verdichteten oder gehämmerten Drähten konnte bei Dauerbiegeversuchen sowie in Schadensbegutachtungen oft vermutet werden. Dabei sind neben der kleineren Seillebensdauer vielmals typische stufenförmige Ermüdungsdrahtbrüche festzustellen (Abbildung 8), welche bei unverdichteten Seilen eher selten zu finden sind. Um diesen Effekt zu erklären wurden u. a. Schliffbilder und REM-Analysen durchgeführt.
Dabei konnten bereits in unverdichteten, nicht ermüdeten, aus dem Seil entnommenen Drähten Defekte in Ziehrichtung gefunden werden, die durch einen späteren Verdichtungsprozess ggf. zu lokalen Trennflächen (Delamination) führen können (vgl. Abbildungen 9 bis 11). Bereits bei früheren Umlaufbiegeversuchen in den 1970er Jahren am Institut für Bergbausicherheit Leipzig wurde aus Längsschliffbildern festgestellt, dass wahrscheinlich die ungenügende Schubbindung in der Ziehstruktur zur Ermüdungsrissbildung von innen heraus auch bei geringeren Biegebeanspruchungen führte. Dies wurde nicht weiter verfolgt und dokumentiert.
- Abbildung 9: Ermüdungsbruch am litzenverdichteten Draht
- Abbildung 10: Defekt im Längsschliff einer unverdichteten neuen Drahtprobe
- Abbildung 11: Ermüdungsdrahtbruch mit Trennflächen
In Bezug auf hammerverdichtete Drähte wurden Schliffbilder im Längs- und Querschliff untersucht.Die Untersuchungen sollen zeigen, inwiefern das ursprüngliche Ziehgefüge durch diesen Verdichtungsprozess verändert wird. Bisherige Erkenntnisse zeigen, dass weitestgehend das Gefüge in Drahtlängsrichtung erhalten bleibt, jedoch lokale Stellen der Drahtberührung durch Fließen verändert werden. Es kann eine Kornfeinung sowie eine Umstrukturierung des Ziehgefüges festgestellt werden, wie Abbildung 12 zeigt.
- Abbildung 12:
- Längsschliff eines hammerverdichteten Drahtes
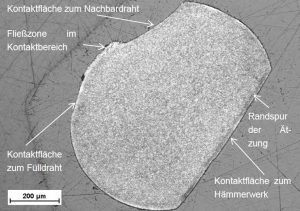
Abbildung 13: Querschliff eines Außendrahtes nach Hammerverdichtung
Abbildung 13 zeigt den Querschliff eines hammerverdichteten Drahtes. Erkennbar sind die einzelnen Fließzonen in den verschiedenen Kontaktbereichen zu Nachbardrähten bzw. zum Hammerwerk.
Der bisherige Erkenntnisstand der werkstoffanalytischen Untersuchungen zeigt durchaus Erklärungen für die Ausbildung verschiedener Ermüdungsdrahtformen. Insgesamt können jedoch keine gesicherten Rückschlüsse auf das Biegewechselverhalten der Drahtseile gezogen werden, da u. a. der Einflussfaktor Drahtnennfestigkeit noch nicht durch den vorliegenden Versuchsumfang abgedeckt wird. Eine erhöhte Wahrscheinlichkeit schnellerer Drahtbruchentwicklungen durch Anrisse aufgrund unterschiedlicher Kerbwirkungen infolge Verdichtungsprozesse kann vermutet werden.
Zusammenfassung
Die vorgestellten Tätigkeiten legen ihren Fokus auf die Anpassung/Validierung der Abschätzungsmethode Leipzig für laufende Drahtseile in Bezug auf den Einfluss der Drahtnennfestigkeit. Wesentliche Grundlage ist dabei die Auswertung vorhandener und fortlaufender Dauerbiegeversuche mit geeigneten Seilkonstruktionen. Nach derzeitigem Kenntnisstand ist hinsichtlich der Biegewechselleistung ein klarer Trend erkennbar, der im Vergleich zur rechnerischen Abschätzung gegenläufig ist. Die aktuellen Ergebnisse zeigen jedoch unter Berücksichtigung der bei laufenden Seilen bekannten Streuungen die grundsätzlich, bewährte Anwendbarkeit der Methode Leipzig. Eine in das zugrunde liegende mechanische Modell einzubringende Korrektur hinsichtlich der Drahtnennfestigkeit erscheint zum derzeitigen Zeitpunkt sinnvoll und ist Bestandteil weiterführender Arbeiten an der TU Dresden. Die ergänzenden Untersuchungen an Seildrähten zeigen, dass gegebenenfalls der weitere relevante Einfluss von Verdichtungsprozessen unabhängig betrachtet werden sollte. Bisher werden verdichtete Drähte mittels des Berührungsfaktors B in der Methode Leipzig berücksichtigt. Dieser ist eine durch Versuche gestützte Größe, die zusammen mit den anderen konstruktiven Parametern eine adäquate Betriebs- und Lebensdauerabschätzung auch für moderne Seilkonstruktionen ermöglicht.
Die Prüfseile wurden durch die Fa. DIEPA Drahtseilwerk Dietz GmbH & Co. KG zur Verfügung gestellt. Die Autoren bedanken sich an dieser Stelle für die freundliche Unterstützung dieser Versuchsreihe. Weiterhin gilt der Dank an Prof. Briem von der OTH Regensburg für die Unterstützung durch Umlaufbiegeversuche.
Literatur
[Bri00] Briem, U.: Umlaufbiegewechselzahlen von Seildrähten. DRAHT 51 (2000) 3, S. 73–77.
[Bri17] Umlaufbiegeversuche mit verdichteten Drähten I und II. Unveröffentlichte Untersuchungsberichte der OTH Regensburg, 2017, 2018.
[Fey00] Feyrer, K.: Drahtseile. Bemessung, Betrieb, Sicherheit. Springer Verlag Berlin Heidelberg, 1. Auflage 1994 und 2., überarbeitete und erweiterte Auflage 2000.
[Fey09] Feyrer, K.: Endurance of wire ropes in rope drives, calculation methods. International Journal of Rope Science and Technology 98 – 2009.
[Gro09] Gronau O. und Steinbach G.: Dimensioning of rope drives and operating time of wire ropes. OIPEEC Conference / 3rd International Stuttgart Ropedays – 18th and 19th March 2009.
[Jeh85] Jehmlich, G.: Anwendung und Überwachung von Drahtseilen. Berlin: Verlag Technik, 1985.
[Oip88] OIPEEC-Recommendation Nr. 1–6. OIPEEC-Bulletin 56, Torino Nov. 1988.
[Ste04] Steinbach, G.: Berechnung der Betriebsdauer von Drahtseilen in Seiltrieben. Technische Überwachung – TÜ Bd. 45 (2004) Nr. 4 – April.
[Wol87] Wolf, E.: Seilbedingte Einflüsse auf die Lebensdauer laufender Drahtseile. Diss. Universität Stuttgart, 1987.
Autoren:
Prof. Dr.-Ing. habil. Thorsten Schmidt
E-Mail: thorsten.schmidt@tu-dresden.de
Telefon: +49 351 463 32538
Dipl.-Ing. Martin Anders
E-Mail: martin.anders@tu-dresden.de
Telefon: +49 351 463 39207