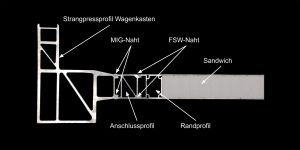
Bild 1: Detailansicht: Übergang zwischen Rahmenstruktur (links) und Sandwichboden (rechts)
Herausforderung Wagenkasten
In Personenzugwagen werden heute viel mehr Komfort- und Informationssysteme eingebaut als früher, die zulässige Achslast ist aber beschränkt. Die Trassenbenutzung wird künftig immer mehr gewichtsabhängig verrechnet, so dass Hersteller von Schienenfahrzeugen insgesamt noch stärker auf das Gewicht achten müssen. Dies erfordert innovative Leichtbaukonzepte, bei denen neben dem Einsatz leichter und hochfester Werkstoffe auch fortschrittliche Bauweisen notwendig sind. Zusammen mit dem Institut für Mechanische Systeme (IMES) an der Zürcher Hochschule für Angewandte Wissenschaften (ZHAW) haben der Sandwichelemente-Hersteller 3A Composites Mobility und das Fertigungstechnologieunternehmen Rapid Technic ein Forschungsprojekt zur Weiterentwicklung der Integrierten Sandwichtechnologie (ISTech) lanciert, um die Strukturanforderungen einer Zulassung im Eisenbahnbereich zu erfüllen.
Für die geforderte Einsatzdauer von über 40 Jahren sind im Bahnbereich Wagenkastenstrukturen als Schweißkonstruktionen aus Stahl oder Aluminium hergestellt. Bewährt hat sich die Bauweise aus Aluminium-Strangpressprofilen. Diese werden zu den Baugruppen Seitenwände, Dach und Bodengruppe zusammengeschweißt und dann zu einem Wagenkasten verbunden. Dies ist gegenüber früheren flugzeugähnlichen Bauweisen mit Rippen und Spanten kostengünstig. Dabei wird aber mehr Material und damit mehr Gewicht eingebaut, als es für die Festigkeit erforderlich wäre. Hier bieten Sandwichkonstruktionen mit Deckschichtdicken von rund 1 mm großes Gewichtoptimierungspotenzial.
Sandwichbauteile werden heute bereits erfolgreich in Bus- und Straßenbahnstrukturen sowie bei Lastwagenaufbauten eingesetzt, wobei die Verbindung mit der tragenden Rahmenstruktur in der Regel mit einer nachgiebigen Dickschichtklebung erfolgt. Durch die Klebung wird die Lastübertragung eingeschränkt, obwohl die Sandwichbaugruppen trotz ihrer geringen Masse hohe Lasten aufnehmen und damit den Wagenkasten wesentlich aussteifen könnten. Dazu sind sie aber in die Tragstruktur einzuschweissen. Dabei werden bei Eisenbahnwagen in ausgewählten Bereichen wie Boden- oder Deckenstrukturen lediglich die Pressstrangprofile durch eingeschweißte Sandwichpanels substituiert, bei grundsätzlich gleichen Schweißanschlüssen zu den benachbarten Baugruppen wie in der klassischen Integralbauweise. Dadurch lassen sich mehrere hundert kg pro Wagenkasten an Gewicht sparen, ohne an der generellen Bauweise etwas zu ändern. Zudem sind Strukturen mit durchgehend geschweissten Deckschichten bezüglich der Empfindlichkeit auf Witterungseinflüsse im Vorteil.
Erarbeitete Bauweise
Bild 1 zeigt den Aufbau: Rechts sind der Sandwichkern und die Deckbleche dargestellt. Diese sind flächig verklebt und mit dem Randprofil umrahmt. Diese Panelkonstruktion kann so nicht im Kastenbau verschweißt werden, da eine klassische Schweißnaht viel Wärme in das Panel einleitet und die Klebung und das Kernmaterial zerstören könnte. Deshalb wird das Anschlussprofil verwendet. Links dargestellt ist die Schnittstelle eines Pressstrangprofiles für den Kastenbau, rechts wird es durch Rührreibschweißnähte mit einem halb so großen Wärmeeintrag mit dem Panel verbunden. Durch Besäumen des Panels lassen sich die Abmessungen sehr genau kontrollieren. Ein PET-Schaum, Aluminiumwaben oder Aramidwaben sind als Sandwichkernmaterial möglich.
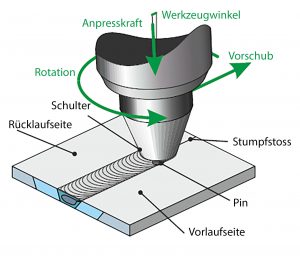
Bild 2: Schematische Darstellung des FSW-Prozesses (links) und FSW-Schweissung (rechts)
Schweiß- und Klebeprozess
Die Klebungen eines Sandwichs können durch die hohen herrschenden Schweißtemperaturen von klassischen MIG-Schweißprozessen thermisch zerstört werden. Umgekehrt besteht die Gefahr, dass die Festigkeit der Schweißnaht durch Klebstoffbestandteile stark vermindert wird. Um gleichwohl die Gewichtsvorteile von Sandwichbauteilen in hochbelasteten Schweißkonstruktionen nutzen zu können, muss der Klebebereich vom Schweißbereich getrennt und ein Schweißverfahren mit möglichst geringem Wärmeeintrag angewendet werden. Dazu eignet sich besonders das Rührreibschweißen (englisch: Friction Stir Welding, FSW, Bild 2), bei dem die Wärme durch Reibkräfte eines Werkzeugs auf die zu fügenden Teile erzeugt wird. Die Werkstoffe werden Temperaturen unterhalb des Schmelzpunktes ausgesetzt und durch eine Rührbewegung miteinander verknetet.
Beim Rührreibschweißen wird im Vergleich zu einer klassischen Schweißnaht nur wenig Energie eingebracht. Die Ergebnisse diverser Untersuchungen (Bild3) und praktischen Tests zeigen, dass die Kombination der Sandwichtechnologie und der Technologie des Rührreibschweißens machbar ist.
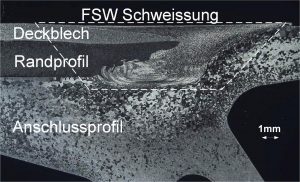
Bild 3: Herausforderung FSW-Naht über 3 Bauteile (Deckblech, Rand- und Anschlussprofil)
Festigkeitsabschätzung
Die wesentlichen Lastfälle für den Wagenkasten sind die Flächenbelastung auf den Boden und der Pufferdruck. Im Berechnungsmodell (Bild 4) wurde der klassische Aufbau des Bodens mit Pressstrangprofilen dem neuen integrierten Sandwichboden gegenübergestellt. Neben der Festigkeitsbewertung ging es auch um eine angemessene Art der Modellierung. Um praktikable Rechenzeiten zu erhalten, ist in einem Gesamtfahrzeugmodell die Diskretisierung von einzelnen Details nur begrenzt möglich. Deshalb werden detaillierte 3-D-Volumenmodelle der Anschlussgeometrie mit der Standard-Schalenelementemodellierung verglichen und Modellierungsregeln abgeleitet.
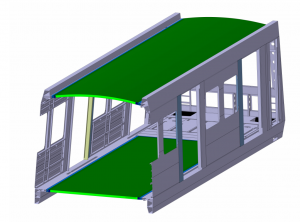
Bild 4: Typischer Wagenkastenaufbau einer Metro mit durch Sandwichstruktur gebildetem Boden- und Dachbereich
Die statischen sowie ermüdungsrelevanten Lastfälle zeigten gegenüber der bestehenden Konstruktion mit Strangpressprofilen keine kritischen Stellen.
Weiter wurden die Varianten des Wagenkastens mit den drei Kernwerkstoffen dem bestehenden Wagenkasten mit Pressstrangprofilen für einen Crashlastfall gegenübergestellt. Das in einer expliziten Simulation mit elastisch-plastischem Werkstoffmodell errechneten Crashverhalten zeigt eine höhere Crashlastaufnahme der Sandwichstruktur als die heute verwendeten Strangpressprofilbauweise.
Statische Tests und Ermüdungsuntersuchungen
Aus diversen Versuchsmustern entnommene Bauteilproben zeigten in statischen Test gleiche oder sogar höhere Festigkeiten als berechnet. Die am realen Bauteil geprüften Lastfälle basierten auf den im Wagenkasten vorherrschenden und festigkeitsrelevanten Belastungen. Die für die Zulassung der Fahrzeuge nötige Prüflast wurde im praktischen Test sogar um das 2.2-fache übertroffen.
Bei der dimensionierenden Schwingspielbreite in den Ermüdungstests sind bei keinen Proben nach dem Belastungszyklus von 1 Million Lastwechsel Schäden aufgetreten. Um eine Aussage über das Versagen bei Ermüdungslasten zu erhalten, wurde die Last erhöht und eine weitere Million Zyklen gefahren, bevor schließlich bei allen Proben ein Versagen eintrat. Das verteilte Schadensbild zeigt, dass die Auslegung der FSW-Schweißnahtverbindung nicht schlechter ist als der Rest der Konstruktion. Um einen guten Überblick zu erhalten, wurde für jede Probe eine äquivalente Spannung berechnet und Normenwerten gegenübergestellt. Alle Ergebnisse übertreffen die für die Zulassung von Schienenfahrzeugen nach Eurocode 9 relevanten Grenzwerte für eine durchgeschweißte klassische V-Naht (Bild 5).
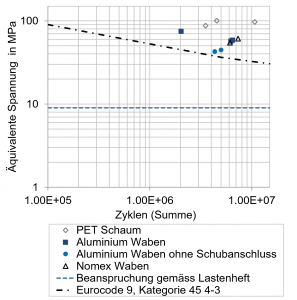
Bild 5: Äquivalente Spannungs-Schwingbreiten für die einzelnen Proben und Versagensarten sowie Referenzkurven und Auslegegrenzen
Optimierter Fertigungsprozess
Gleichzeitig wurde die Fertigungstechnologie so optimiert, dass sich die integrierten Sandwichelemente mit möglichst wenigen Arbeitsschritten herstellen lassen. Die Mehrkosten gegenüber einer klassischen Pressstrangprofilkonstruktion in integraler Bauweise liegen pro eingespartem Kilogramm unter 20 Euro. Bei einer Neukonstruktion können zusätzliche Vorteile bei der Wärme- und Schallisolation und Funktionsintegration genutzt werden.
Gewichtsvorteile
Die integrierte Sandwichtechnologie ermöglicht eine markante Gewichtseinsparung bei hochbelasteten Strukturen. Bei unverändert hoher Strukturfestigkeit sind durch die vorgestellte Sandwichtechnologie Gewichtsreduktionen bis 10 % realistisch, wenn Teile der Bodenplatte, des Dachs und Bereiche der Seitenwand mit dieser Bauweise ausgeführt werden. Eine Änderung der Grundkonstruktion und der Produktionsschritte des Wagenkastens ist nicht nötig. Dieser Leichtbauansatz senkt die Betriebskosten für Fahrzeuge und Schienen und leistet einen wichtigen Beitrag zur Energieeinsparung.
Ansprechpartner
Roland Fehr,
fehr@zhaw.ch