Einleitung
Die additiven bzw. generativen Fertigungsverfahren werden auch als „Rapid Prototyping“ oder „3D-Druck“ bezeichnet und sind in Deutschland innerhalb der VDI Richtlinie 3405 definiert. Je nach Anwendungsfeld grenzen sich die exakten Bezeichnungen dennoch voneinander ab. Demnach umfasst die generative Fertigung alle Verfahren, welche durch Fügen von Materialien die gewünschte Geometrie erzeugen bzw. die Bauteile aus mehreren Schichten generieren [Geb16]. Weitere Unterscheidungskriterien der additiven Verfahren sind technologisch begründete Unterschiede wie z. B. die verschiedenen Ausgangsmaterialien (Draht oder Pulver), sowie die Anwendung verschiedener Energiequellen für das Aufschmelzen des Schweißmaterials (Laserstrahl, Elektronenstrahl, Lichtbogen). Einen Überblick hierzu gibt Abbildung 1 welche außerdem die Art der Zuführung bzw. Bereitstellung des Schweißguts berücksichtigt.
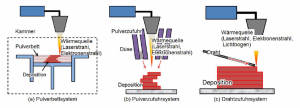
Abbildung 1: Einteilung additiver Fertigungsverfahren [Ogi18]
Drahtbasierte additive Fertigungsverfahren weisen hierbei eine höhere Prozessgeschwindigkeit, sowie günstigere Zusatzwerkstoffe und allgemein geringere Investitionskosten für Anlagen auf [Din11]. Auch die Materialeigenschaften der drahtbasierten additiven Fertigung sind vergleichbar mit anderen Fertigungsverfahren, z.B. kann dadurch eine Zugfestigkeit erreicht werden, welche mit geschmiedeten oder gegossenen Bauteilen vergleichbar ist [Bra10].
Die lichtbogenbasierte generative Fertigung bildet den Grundstock der Forschungsaktivitäten an der Professur Schweißtechnik der Technischen Universität Chemnitz. Ergänzt wird dies durch die generative Fertigung mittels Laserpulverauftragschweißen und Diffusionsschweißen. Im nachfolgenden werden die beiden Lichtbogenverfahren, WAAM (Wire+Arc Additive Manufacturing) und 3DPMD (3D Plasma Metal Deposition) näher betrachtet.
Drahtbasierte generative Fertigung mit Lichtbogen (WAAM)
![Schematische Darstellung des a) MSG Schweißens-WAAM [Din15] und des b) 3DPMD Verfahrens [Hoe17]](https://werkstoffzeitschrift.de/wp-content/uploads/2019/10/2-300x151.jpg)
Abbildung 2: Schematische Darstellung des a) MSG Schweißens-WAAM [Din15] und des b) 3DPMD Verfahrens [Hoe17]
Abhängig von der Dichte des drahtförmigen Zusatzwerkstoffes und der Bauteildimension können Abschmelzleistungen von mehr als 6 kg/h realisiert werden [Gra17, Gra18]. Dabei können alle drahtförmig zur Verfügung stehenden Zusatzwerkstoffe verwendet werden. Das Spektrum reicht dabei von verschiedenen Arten von Stählen, Nickel, Refraktärmetallen wie Titan sowie Leichtmetalle wie Aluminium oder Magnesium. Ein Beispiel ist die generative Herstellung von Magnesiumbauteilen aus der Legierung AZ31. Hierfür wurde durch den schichtweisen Auftrag (Ablauf siehe Abbildung 3a) von 20 Lagen AZ31 (Drahtdurchmesser 1,2 mm) ein 50 mm hohes Rohrsegmente mit einem Durchmesser von 60 mm hergestellt, welches in Abbildung 3b zu sehen ist. Die Drahtvorschubgeschwindigkeit betrug 5 m/min (ca. 58 A und 11 V) und die Schweißgeschwindigkeit 40 cm/min. Im Querschliff (Abbildung 3c) ist der homogene und gleichmäßige Lagenaufbau zu sehen, wobei die einzelnen Schichten gut erkennbar sind.
Da beim drahtbasierten additiven Fertigen Standardzusatzwerkstoffe verwendet werden können, ist die flexible Fertigung von verschieden großen Bauteilen kostengünstig realisierbar. Eine Herausforderung ist die additive Fertigung von kleinskaligen sowie Multimaterialbauteilen mittels WAAM, was nur eingeschränkt möglich ist.
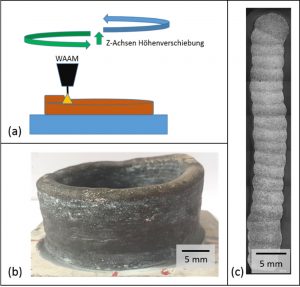
Abbildung 3: Generativ gefertigte Magnesiumstruktur mittels WAAM a) Prozessschema b) generativ gefertigtes Bauteil im Zustand wie geschweißt c) Makroaufnahme der Bauteilstruktur
Pulverbasierte additive Fertigung mit Lichtbogen (3DPMD)
Angelehnt an die Technologie des Plasma-Pulver-Auftragsschweißens (PTA) wurde von Hoefer et al. 2017 das 3D-Plasma-Metal-Deposition (3DPMD) Verfahren (Abbildung 2b) entwickelt und beschrieben [Hoe17]. Anstatt wie beim PTA-Verfahren lediglich das Grundmaterial inklusive eines zugeführten Pulvers aufzuschmelzen, um zum Beispiel eine Deckschicht zum Korrosions- oder Verschleißschutz zu applizieren, werden beim 3DPMD Verfahren dreidimensionale Strukturen im Sinne der additiven Fertigung hergestellt. Dabei gelten die hohe Prozessgeschwindigkeit, die geringeren Anforderungen an die Pulverqualität, sowie eine entstehende hohe Materialdichte als große Vorteile des PTA-Verfahrens. Während dem Bauprozess wird ein Metallpulver direkt unter dem Plasma-Lichtbogen zugeführt und aufgeschmolzen. Mit Hilfe geeigneter Handlingsysteme, in Kombination mit speziell entwickelter Software, entstehen schichtweise dreidimensionale Strukturen [Hoe17]. Dabei können bis zu vier unterschiedliche Pulver in einer Schweißlage eingebracht und deren Mengen definiert geregelt werden, womit zusätzlich die Definition von örtlich verschiedenen belastungsangepassten Bauteileigenschaften möglich ist.
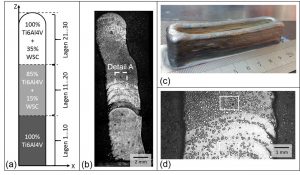
Abbildung 4: Additive Fertigung einer Hybridstruktur mittels 3DPMD a) Schematischer Bauteilaufbau b) Makroaufnahme der realen Bauteilstruktur c) generativ gefertigtes Bauteil im Zustand wie geschweißt d) Mikrostrukturaufnahme des Bereiches Detail A
Ein Beispiel hierfür ist die Einbringung von Wolframschmelzkarbiden in eine Matrix aus Ti6Al4V, wobei der Gehalt an Hartstoffen mit der Bauteilhöhe variiert werden kann, siehe Abbildung 3a. Die Fertigungszeit der in Abbildung 3c dargestellten Komponente mit den Abmessungen b*l*h=20*90*30 mm betrug t = 1.200 s. Abbildung 3b zeigt einen makroskopischen Querschnitt durch das Bauteil. Es ist festzustellen, dass ein definierter und homogener Lagenaufbau vorliegt. Des Weiteren ist die Verteilung der Verstärkungspartikel gleichmäßig, wie es die mikroskopische Bewertung bestätigt, Abbildung 3c. Neben der weitgehend freien Gestaltung der Bauteilgeometrie und der hohen Abschmelzraten von bis zu 6 kg/h ist der Prozess 3DPMD sehr gut zur Herstellung von Multimaterialbauteilen geeignet.
Zusammenfassung
Die Kapazitäten an der Professur Schweißtechnik der Technischen Universität Chemnitz im Bereich lichtbogenbasierter generativer Fertigung sollten in diesem Beitrag anhand zweier aktueller Beispiele gezeigt werden.
Zum einen wurde die generative Verarbeitung der Magnesiumlegierungen AZ31 mittels WAAM aufgezeigt. Hierdurch können zum Beispiel die Vorteile des klassischen Leichtbaus mit denen der bionischen Geometrieoptimierung verknüpft werden. Die Variation von Materialeigenschaften in Abhängigkeit von der Beanspruchung wurde ebenfalls aufgezeigt. Hierfür wurde ein Titanbauteil mit veränderlichem Gehalt an Verstärkungspartikeln in Anhängigkeit von der Bauteilhöhe mittels 3DPMD hergestellt.
Zusammenfassend konnte gezeigt werden, dass beide Verfahren (WAAM und 3DPMD) Sonderwerkstoffe generativ verarbeiten können und somit neue Möglichkeiten für die Konstruktion von hochbeanspruchten Bauteilen bieten.
Autoren:
Höfer Kevin, Hälsig André und Mayr Peter
Literaturverzeichnis
[Bra10] Brandl, E. u. a.: Additive manufactured Ti–6Al–4V using welding wire-comparison of laser and arc beam deposition and evaluation with respect to aerospace material specifications. Z. Physics Procedia. 10. (2010), Nr. 5, S. 595-606
[Clo18] Clone 3D Print & Production NN: SLS, Selective Laser Sintering. Homepage; Link: http://www.clone3d.co.nz/printer-and-plastic (Zugriff: 06.08.18)
[Din11] Ding, J. u. a.: Thermo-mechanical analysis of Wire and Arc Additive Layer Manufacturing process on large multi-layer parts. Z. Computational Materials Science. 25. (2011), Nr.50, S. 3315-3322
[Din15] Ding, D. u. a.: Wire-feed additive manufacturing of metal components-technologies, developments and future interests. Z. Int J Adv Manuf Technol. 32. (2015), Nr.81, S. 465-481
[Gra17] Graf, M.; Härtel, S.; Hälsig, A.: Numerische Auslegung des Mehrlagenschweißens als additives Fertigungsverfahren. SAXSIM 2017 http://www.qucosa.de/fileadmin/data/qucosa/documents/22594/Graf_SAXSIM_2017.pdf
[Gra18] Graf, M.; Pradjadhiana, K. P.; Hälsig, A.; Y. H. P. Manurung, B. Awiszus: „Numerical simulation of metallic wire arc additive manufacturing (WAAM)“- Vortrag und Tagungsbandartikel. In: Conference: PROCEEDINGS OF THE 21ST INTERNATIONAL ESAFORM CONFERENCE ON MATERIAL FORMING: ESAFORM 2018, May 2018, AIP Conference Proceedings 1960(1):140010, DOI 10.1063/1.5035002
[Hoe17] Hoefer, K.; Haelsig, A.; Mayr; P.: Arc-based additive manufacturing of steel components – comparison of wire- and powder-based variants. Welding in the World https://doi.org/10.1007/s40194-017-0527-9; International Institute of Welding 2017