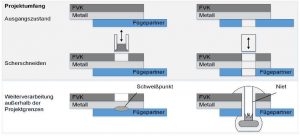
Abbildung 1: Projektumfang und Anwendungsgebiet gelochter Hybridbauteile; Widerstandspunktschweißen (links), Blindnietverbindung (rechts)
Hybride Bauteile aus Kunststoff und Metall rücken zunehmend in den Fokus von Forschung und Industrie. Ein hohes Leichtbaupotenzial macht diese Werkstoffkombination in vielen Anwendungsbereichen interessant. Die Vorteile der Hybridisierung beschränken sich jedoch nicht nur auf die optimale Nutzung der jeweiligen Materialeigenschaften. Vorzugsweise werden hybride Bauteile daher in Branchen mit gewichtsrelevanten Betriebskosten, wie beispielweise der Luft- und Raumfahrt, eigesetzt. Mit zunehmender gesellschaftlicher und politischer Bedeutung der Ressourceneffizienz sind diese entwicklungsintensiven Bauteile auch für die Automobilbranche relevant geworden. Die wichtigsten Herausforderungen sind hierfür wirtschaftliche Prozesse für die Großserie.
Das AiF-Projekt HYBMS leistet einen Beitrag zur Anpassung und Weiterentwicklung bestehender Fertigungsprozesse. Im Rahmen des Vorhabens wird untersucht, wie hybride Verbunde aus Metall und faserverstärkten Kunststoffen (FVK) möglichst schädigungsfrei, für deren Anbindung an andere Bauteile, vorbereit werden können. Hierbei kommen sowohl Durchgangslöcher für Schrauben und Niete als auch partiell von Kunststoff freigestellte Bohrungen für Schweißpunkte zur Anwendung (Abbildung 1). Des Weiteren können Löcher zur Durchführung von Kabeln und Leitungen in Bauteilen dienen. Als potenzielle Anwendungsfelder werden der automobile Karosseriebau und der Flugzeugbau gesehen.
Die trennende Bearbeitung von FVK mittels Fräsen, Bohren, Wasserstrahl- und Laserstrahlschneiden ist bereits etabliert. Das Scherschneiden hingegen wird vorrangig in der Blechbearbeitung eingesetzt, findet jedoch auch zunehmend Anwendungen bei FVK: Formteile aus Glasfasermatten-Thermoplasten (GMT) werden schon seit längerem in der Großserienfertigung schergeschnitten. Bohrungen und Durchbrüche sind mit diesem Verfahren ohne Schwierigkeiten bis zu Materialdicken von 4 mm möglich [SPUR97]. Jedoch eignet sich nicht jedes der genannten Verfahren für den Großserieneinsatz. Zielführend werden hier nicht die spanenden Verfahren, sondern die in der Blechbearbeitung bekannten zerteilenden Verfahren, wie das Scher- und Messerschneiden, gesehen [QI14].
Wie auch bei der spanenden Bearbeitung ergeben sich durch die auftretenden Prozesskräfte mögliche Schädigungen im Verbund. Es kann zu Delaminationen in der Verbindungschicht der Komponenten als auch in den Zwischenschichten des FVK kommen. Durch die auftretenden Schubspannungen an den Grenzschichten sind Ablösungen zwischen Metall und Kunststoff im Bearbeitungsbereich, das heißt an den Schnittflächen, zu erwarten. Solche eingebrachten strukturellen Schäden sind besonders in FVK kritisch. Ursprünglich kleine Delaminationen können sich unter Dauer- und vor allem Schwingungsbelastung ausbreiten und so zu bauteilversagen führen [NEU89].
Die Komplexität des Trennprozesses an hybriden Bauteilen steigt aufgrund des stark divergierenden Materialverhaltens von Metall und FVK. Die Bearbeitung von bereits gefügten Metall-FVK-Verbindungen und dessen Auswirkung sind bisher nur unzureichend untersucht worden. Das Projekt unterstützt hier den Aufbau des Prozessverständnisses und fördert vor allem die KMU als Zulieferbetriebe.
Im Rahmen des Projektes wurde zunächst ein schwingungsbasierter Prüfstand zur Beurteilung des Schädigungseintrags aufgebaut, der es ermöglicht zerstörungsfreie Proben- und Bauteilanalysen durchzuführen. Die derzeitigen Prüfverfahren können die Schnittqualität und damit Schädigung weder ausreichend quantitativ bewerten, noch sind diese geeignet eine große Probenanzahl mit minimalem Zeitaufwand zu prüfen. Für den Aufbau des Prüfstands wurden definiert geschädigte Proben gefertigt, die es erlauben den Prüfstand zu kalibrieren und erste Unterscheide von Schädigungsposition und -Größe zu erkennen.
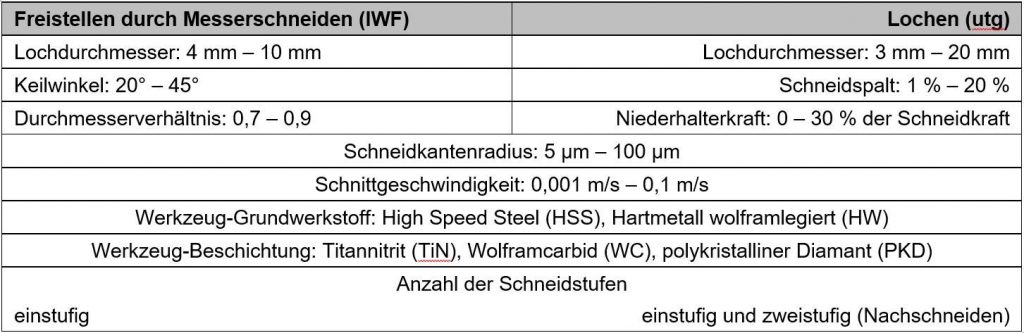
Tabelle 1: Prozessparameter für das Messerschneiden und das Scherschneidverfahrens
Mit dem Prüfstand werden nachfolgend die Verfahren Messerschneiden und Scherschneiden qualifiziert. Durch Parametervariation werden signifikante Stellgrößen und Einflussparameter auf den Schädigungseintrag bestimmt. Die relevanten zu untersuchenden Größen sind in Tabelle 1 aufgeführt. Anschließend werden diese optimiert und dienen so als Grundlage für eine serienfähige Prozessentwicklung.
Für die Schädigungsbewertung war der Aufbau eines neuen Mess- und Prüfsystems erforderlich. Der Mechanismus der Prüfeinheit nutzt die im Vergleich zu ungeschädigten Proben veränderte akustische Rückmeldung geschädigter Probekörper. Die Reibungseffekte an den Schädigungen und die damit einhergehende Absorption der in den Schichtverbund eingebrachten Energie, verändert sich das akustische Dämpfungsverhalten des Bauteils (Abbildung 2). Somit steht das akustische Verhalten im direkten Zusammenhang mit der Schädigung und ist zur Prozessoptimierung nutzbar.
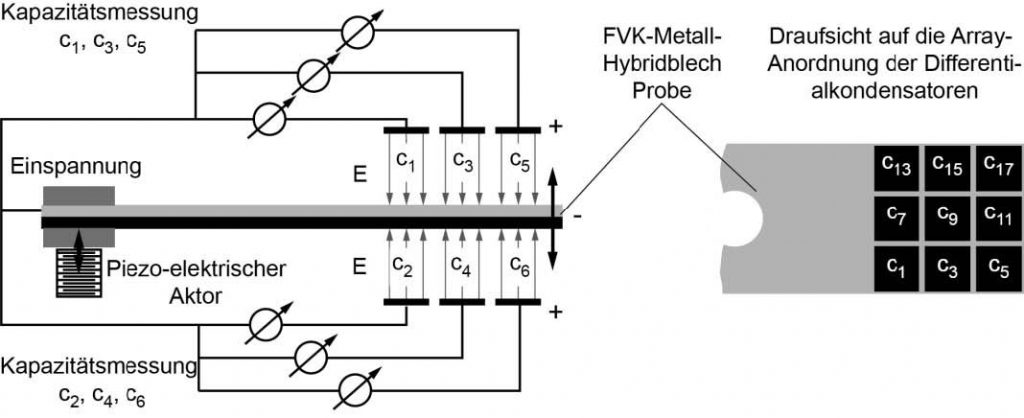
Abbildung 2: Konzept des Prüfstands zur Bestimmung des Dämpfungskennwertes
Die Auslegung, Erprobung und Optimierung des Messer- uns Scherschneidverfahrens ist das zweite Hauptziel des Forschungsvorhabens. Das Messerschneiden an hybriden Verbunden steht vor allem vor werkzeugbedingten Herausforderungen. Neben den Untersuchungen zum Schneidwinkel und der Prozessgeschwindigkeit, wurde die Standfähigkeit der Werkzeuge untersucht. Weiterhin wurden unterschiedliche Konzepte zur Schneidbutzenabfuhr bewertet.
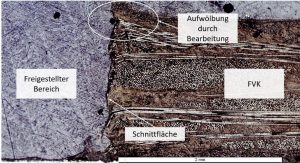
Abbildung 3: Effekte des Freistellverfahrens auf die Bearbeitungszone
Die Schnittergebnisse beider Verfahren zeigen, dass die Schädigung des Verbundes im Bereich von ≤ 1 mm liegt. Das Stanzverfahren hat durch die Lochung des gesamten Verbundes einen größeren Schädigungseinfluss, sichtbar als Einzug der Schnittkante (Abbildung 3). Das Messerschneiden beeinflusst die Bearbeitungszone durch eine geringe Aufwölbung des FVK.
Im Zuge der Zugänglichkeitsbewertung wurde das Stanzverfahren richtungsabhängig untersucht. Wird der Verbund stahlseitig schergeschnitten, hat dies einen hohen Kanteneinzug zur Folge. Wird der Verbund FVK-seitig getrennt tritt, ein hoher Anteil Ausfransung (FVK) auf (Abbildung 4).
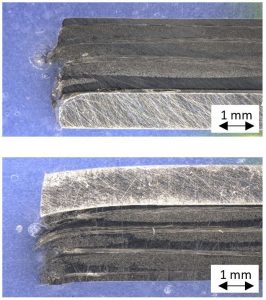
Abbildung 4: Variation der Anschnittseite:oben FVK-Stahl; unten Stahl-FVK
Das Projekt HYBMS 19156N1 wurde durch das Bundesministerium für Wirtschaft und Energie (BMWi) über den Projektträger AiF gefördert und durch die Fördervereinigung EFB begleitet. Die Förderung dient der Förderung kleiner und mittelständischer Unternehmen. Das Förderprogram dient der Förderung des IWF – Institut für Werkzeugmaschinen und Fertigungstechnik der TU Braunschweig und des utg – Institut für Umformtechnik und Gießereiwesen der TU München.
Kontakt:
TU Braunschweig
Institut für Werkzeugmaschinen und Fertigungstechnik
Vicky Reichel
v.reichel@tu-braunschweig.de
TU München
Institut für Umformtechnik und Gießereiwesen
Florian Steinlehner
florian.steinlehner@utg.de
Literaturhinweise
- [NEU89] Neubert, Harald: Anwendung thermometrischer Methoden bei der Prüfung Kohlenstoffaser-verstärkter Kunststoffe. Dissertation. Universität-Gesamthochschule-Essen, 1989
- [QI14] Qi, Zhenchao u. a.: Critical thrust force predicting modeling for delamination-free drilling of metal-FRP stacks. In: Composite Structures, Bandnr. 107, S. 604-609, 2014.
- [SPUR97] Spur, Günther; Liebelt, Stefan: Lagebericht: Verfahren zur GMT-Bearbeitung: ein Technologievergleich. In: Kunststoffe, 87 (4), S. 442-449, 1997.