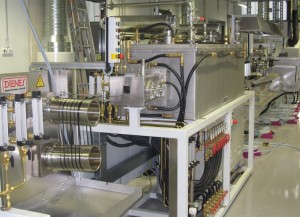
Abb.: Hochtemperaturofen und Oberflächenbehandlungstrecke der Carbonisierungsanlage
Einzigartige Prozesstechnik am HPFC Denkendorf
Verbesserte Carbonfasern aus alternativen Präkursor-Materialien. Dieses ist eines der Forschungsziele am Denkendorfer High Performance Fiber Center (HPFC). Im Mittelpunkt steht dabei ein weltweit einzigartiges Anlagenkonzept. Besondere verfahrenstechnische Prozessschritte ermöglichen es, verbesserte Carbonfasern durch strukturelle Änderungen in molekularer Größenordnung hervorzubringen – kontrolliert und reproduzierbar.
Dabei werden Carbonfasern technisch in mehreren Verfahrensschritten erzeugt. Ausgangsmaterial ist meist Polyacrylnitril. Im Rahmen von Forschungsarbeiten werden am Institut für Textilchemie und Chemiefasern Denkendorf (ITCF) neben Acrylnitril auch die wirtschaftlich interessanten und billigen Präkursoren Lignin, Cellulose und Polyethylen als Alternativen für die Carbonfaserherstellung eingesetzt.
Als erster Verfahrensschritt werden die Ausgangsmaterialien in einer Schmelzspinnanlage zu sogenannten Präkursorfasern versponnen. Diese müssen nun in zwei weiteren Arbeitsschritten – und in zwei getrennten Anlagenbereichen – in Carbonfasern umgewandelt werden.
Die Präkursorfasern müssen vor der eigentlichen Carbonisierung in einem Hochtemperaturofen erst stabilisiert bzw. vernetzt werden. Dieser Schritt ist notwendig, um die Molekülstrukturen derart zu ändern, daß die Fasern die spätere thermische Belastung während der Carbonisierung aushalten – und nicht zu Staub zerfallen. Für die Vernetzung stehen gleich mehrere Verfahren zur Verfügung. In einer separaten Pilotlinie wird die Stabilisierung unter Sauerstoff durchgeführt. Das Verfahren ist auch in der industriellen Produktion gängig und technisch zuverlässig. In einem Umluftofen mit vier separat beheizbaren Zonen reagieren die Präkursor-Materialien mit Sauerstoff. Bei der Reaktion entstehen Abspaltungsprodukte, die abgeführt werden. Die Stabilisierung unter Sauerstoff ist ideal geeignet, um Polyacrylnitril-basierte Präkursorfasern und einige alternative Präkursoren zu stabilisieren. Doch für weitere Materialien und Zielsetzungen ist ein anderes Verfahren das Mittel der Wahl:
Als Besonderheit der Anlagen am ITCF sind alternativ gleich zwei Elektronenstrahlanlagen verfügbar. Die Stabilisierung der Präkursorfasern unter Elektronenbeschuss hat zwar das gleiche Ziel wie die Sauerstoffstabilisierung. Der Weg ist jedoch ein anderer. Chemische Doppelbindungen werden im Ausgangsmaterial der Faser geöffnet und reagieren an anderen Stellen unter Ausbildung neuer Bindungen. Die Moleküle der Faser vernetzen. Die Faser wird stabilisiert – für den späteren Schritt der Carbonisierung.
Eine der Elektronenstrahlanlagen befindet sich direkt hinter der Spinndüse. Dadurch können die Fasern unmittelbar nach dem Ausspinnen gehärtet werden. Ein großer Vorteil für die weitere Prozessführung: die Fasern verlieren ihre Sprödigkeit, lassen sich einfacher wickeln belastbarer handhaben.
Dem Polyethylen als Präkursormaterial für Carbonfasern ist ein eigener Anlagenteil vorbehalten. Dieses Polymer ließ sich bisher nur unzureichend stabilisieren. Verbesserte Carbonfasereigenschaften verspricht man sich am ITCF durch eine chemische Vorbehandlung des Polyethylens in speziell konstruierten und bisher einzigartigen Reaktionskammern. In diesen wird das Polyethylen für die folgende Stabilisierung derart modifiziert, daß die Struktur der Fasern für die nachfolgende Carbonisierung optimiert wird. Die Kammern werden im Rahmen des FP7-Projektes der EU „NEWSPEC“ installiert.
Zusätzlich steht in der Stabilisierung eine zweite Elektronenstrahlanlage für die Vernetzung verschiedener Polymere bereit.
Die eigentliche Carbonisierung der Fasern erfolgt in einer eigenen Prozesslinie. Sie besteht aus einer Ofenstrecke für die Carbonisierung und einer Oberflächen-Nachbehandlungseinheit. In einem Pyrolyseofen werden bei Temperaturen bis zu 1300°C unter Sauerstoffausschluss chemische Verbindungen gespalten. Die Spaltprodukte werden abgeführt. Im Folgenden durchfahren die Fasern einen Hochtemperaturofen, der bei Temperaturen von bis zu 2000°C für die endgültigen Strukturen der entstehenden Carbonfasern verantwortlich ist. Hier wird die Orientierung und Ausbildung der Graphitschichten innerhalb der Fasern beeinflußt.
Auch einzigartig ist die besondere Fadenführung, die es erlaubt, zwischen den Öfen die Fadenspannung definiert einzustellen. Eine optimale Fadenspannung ermöglicht eine hochgradig orientierte Ausrichtung der Kettenmoleküle innerhalb der Fasern. Für die sich anschließende Hochtemperaturbehandlung bedeutet dieses eine Optimierung der Faserstruktur – mit verbesserten mechanischen Eigenschaften der Carbonfasern.
Nach der Carbonisierung durchläuft die Carbonfaser eine elektrochemische Behandlung. Ihre Oberfläche wird in einem galvanischen Bad mit funktionellen Gruppen versehen. Dieses ist von Vorteil, wenn sie als Verstärkungsfaser in Verbundwerkstoffen eingesetzt werden soll. Hierdurch wird die Faser-Matrix-Haftung und damit die Festigkeit des Verbundwerkstoffes erhöht.
Die Kombinationsmöglichkeit der einzelnen Anlagenkomponenten ist in dieser Art einzigartig. Durch einen modularen Aufbau der Anlagen können einzelne Komponenten nach Bedarf in den Prozess integriert oder fortgelassen werden. Die Entwicklung von Carbonfasern mit neuen Eigenschaftsprofilen und aus alternativen Präkursormaterialien wird dadurch in bisher nicht realisierbarem Maße ermöglicht.
Weitere Informationen zum Thema:
Dr. Erik Frank
Neue Materialien, Textile Solarzellen, Carbonfasern
(Carbonisierungstechnikum)
Tel. 0711 / 9340-133
erik.frank@itcf-denkendorf.de