In zahlreichen gegenwärtigen und potentiellen Anwendungen kann von der Entwicklung von Multimaterial-Technologien profitiert werden. Durch Auf- und Anbringen von unterschiedlichen Materialien an strategischen Punkten im und um das Bauteil können gewünschte Eigenschaften gezielt realisiert oder verstärkt und Funktionen direkt integriert werden. Die Industrie nutzt Multimaterial-Designs in zahlreichen Anwendungen wie selbstverständlich.
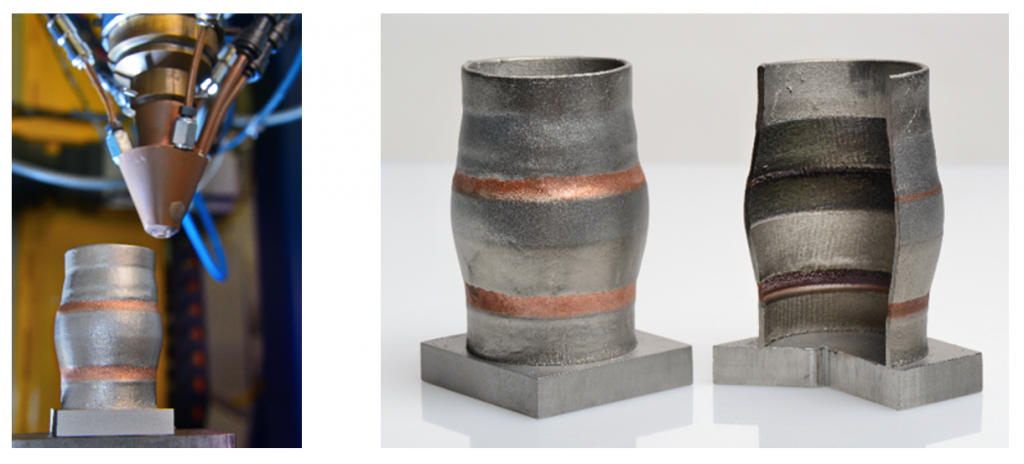
Bild 1: Rotationssymmetrisches Multimaterial-Bauteil bestehend aus Cu-, Ni- und Fe-Basislegierungswerkstoffen
Beschichtungen stellen als 2D-Applikation eine umfassend etablierte Multimaterial-Anwendung dar. Im Automobilbereich werden Stahlteile mit hoher Festigkeit mit Aluminium- und Magnesiumteilen gefügt, Energiespeicher bestehen aus Nickel-, Kupfer- und Silberverbindungen, Geldmünzen aus zwei Legierungen sind Alltag. Gefügt wird durch Schweißen, Kleben und mechanische Verbindungstechnik. Daneben existiert eine große Anzahl Anwendungen, deren stetig steigende Anforderungen mit Einzelmaterial-Technologien zukünftig nicht mehr oder nur unzureichend erfüllt werden können und damit perspektivische Einsatzgebiete für hybride oder Multimaterial-Bauteile sind. Beispiele reichen von Wärmeleitfähigkeit in Kühlkanälen, hoher Härte oder Verschleißbeständigkeit in mechanisch belasteten Bauteilen, hoher Temperaturbeständigkeit in Turbinenkomponenten über thermische Isolationen, di-elektrische und magnetische Eigenschaften in Antennen, chemische Eigenschaften in Brennstoffzellen und Batterien bis hin zu akustische Eigenschaften in Soundsystemen.1) Die Verbesserung der Leistungsfähigkeit von Komponenten durch integrative Bauteilgestaltung kann je nach Anwendungsfeld Verlängerungen der Standzeit, Reduzierung von Gewicht und Verkleinerung von Bauräumen durch kompakte Verdichtung von Funktionen unterstützen.
Der Einsatz von 3D-Multimaterialbauweisen entspricht somit einer funktional und ökonomisch attraktiven, jedoch auch technisch herausfordernden Fertigungsvariante. Die intelligente Kombination verschiedener Werkstoffe in Form von Multimaterialien und Hybridbauteilen mit konventionellen Verfahren erfordert eine je nach Anwendungsfall komplexe und kostenintensive Aneinanderreihung von unterschiedlichen Herstellungs-, Nachbearbeitungs- und Füge- oder Montageschritten. Die jeweiligen Kontaktbereiche stellen sowohl für thermische oder elektrische Übergänge als auch für mechanische Belastbarkeit Schwachstellen dar. Mit AM (Additive Manufacturing) ist die Möglichkeit gegeben, Multimaterialbauteile in einem einzigen Fertigungsschritt herzustellen. Während kommerzielle Maschinen für das AM mit pulverbettbasiertem Schmelzen (Laser Powderbed Fusion, LPBF oder Electron Beam Melting, EBM) derzeit noch auf die Verarbeitung eines Materials limitiert sind, kann durch die selektive Pulverzufuhr des Pulverdüse-basierten Direct Energie Deposition (DED)-Verfahrens sequenziell mit einer frei wählbaren Anzahl metallischer Werkstoffe gearbeitet werden. Die Pulver werden mittels Laserstrahlung lokal aufgeschmolzen und Bahn für Bahn zu einem intermetallisch verbundenen Bauteil geformt. So können auch artungleiche Werkstoffe werkzeuglos miteinander kombiniert werden. Für das DED ist ein weitreichendes Spektrum an Werkstoffen einsetzbar. Grundsätzlich geeignet sind nahezu alle schweißbaren Materialien. Typischerweise werden Gusswerkstoffe eingesetzt wie beispielsweise Aluminium-Siliziumlegierungen, Kupfer, Stähle oder Nickelbasis-Legierungen. 2) Insbesondere durch Entwicklung von Materialien speziell für AM wird die Werkstoffpalette ausgehend von Anforderungen nach besseren Eigenschaften z.B. hinsichtlich spezifischer Festigkeit, Temperatur- und Oxidationsbeständigkeit jedoch laufend erweitert bis hin zu Materialien, die konventionell erst gar nicht verarbeitbar sind.
In einem internen Projekt wurden am Fraunhofer ILT Untersuchungen zur Fertigung von Multimaterial-Bauteilen bestehend aus Fe-Basis (316L), Cu-Basis (Hovadur CCZ) und Ni-Basis (Inconel® 718) Pulvern durchgeführt. Durch variables Mischen unterschiedlicher Pulvermaterialien im Prozess ist auch das Einstellen von Gradienten im Bauteil möglich, wodurch sanfte Materialübergänge realisiert werden können. Auf diese Weise können teilweise auch Werkstoffe, die beispielsweise aufgrund von Bildung intermetallischer Sprödphasen oder stark unterschiedlicher Wärmeausdehung als unverträglich gelten, miteinander verbunden werden. Im gezeigten Beispiel war so möglich, in dünnwandigen Strukturen (ca. 1 mm) Cu- und Fe-Basis-Material spannungsarm aufeinander aufzubauen, sodass Rissbildung unterbunden wurde. Als ein konkretes Anwendungsbeispiel können Kühlstrukturen bereits während des Fertigungsprozesses stoffschlüssig in das Volumen eines Bauteils eingefügt werden. In einer Studie wurde anhand einer einfachen geometrischen Struktur die Einbettung von wärmeleitfähigen Kupferbahnen aus Hovadur CCZ in ein Volumen aus einer Ni-Basislegierung (Inconel® 625) aus dem Turbomaschinenbau demonstriert.
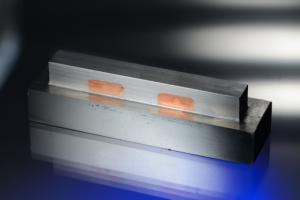
Bild 2: Multimaterial-Bauteil aus Inconel® 625 mit Cu-Inlay (Hovadur CCZ)
Durch den dreidimensional flexiblen Verlauf der Kühlstrukturen können Wärmesenken in thermisch belasteten Bauteilbereichen gezielt generiert und somit die Lebensdauer des Werkstücks wesentlich verlängert werden. Die geometrische Designfreiheit wird begrenzt durch eine minimale Auflösung von ca. 200 µm und Einschränkungen bei der Gestaltung von Überhangsbereichen bzw. Hinterschneidungen. Schwerkraftbedingt sind realisierbare Winkel abhängig von den Manipulationsmöglichkeiten der eingesetzten Maschine. Nicht zuletzt durch die vollständige Automatisierbarkeit des DED ist das perspektivische Anwendungsspektrum für mit diesem additiven Fertigungsverfahren hergestellte Multi-Materialbauteile groß. Derzeitige Herausforderungen liegen in der Bereitstellung der Prozesstechnik um sehr schnelle Materialwechsel umzusetzen und somit die theoretisch punktuelle Auflösung auch praktisch zu Erzielen. Im DED wird dies durch den Einsatz eines Rapid-Powder-Switch möglich.3) Hinsichtlich der Bauteilauslegung, die heutzutage durch CAD erfolgt, wird die Weiterentwicklung entsprechender Softwaremodule, die den partiellen Einsatz unterschiedliche Werkstoffe berücksichtigen, immer wichtiger. Auch die Prüftechnik steht vor neuen Herausforderungen: die Eigenschaften eines Bauteils bei Verwendung von Multi-Materialien können nicht mehr aus der Kenntnis der Eigenschaften eines einzelnen Werkstoffs vorhergesagt werden und sind erst nach der Formgebung bestimmbar. Zukünftig ist zudem die Kombination nicht nur metallischer Materialien miteinander, sondern auch die Integration von Keramiken und Kunststoffen in einem einzigen Fertigungsschritt denkbar – auch wenn diese Vision in weiter Ferne scheint, ist sie Aufgabe der Forscher von heute.
Autor*innen:
Silja-Katharina Rittinghaus und Andreas Weisheit,
Fraunhofer-Institut für Lasertechnik
Literatur:
1) Mohammad Vaezi, Srisit Chianrabutra, Brian Mellor & Shoufeng Yang (2013) Multiple material additive manufacturing – Part 1: a review, Virtual and Physical Prototyping, 8:1, 19-50, DOI: 10.1080/17452759.2013.778175
2) Kelbassa I, Wohlers T, Caffrey T. Quo vadis, laser additive manufacturing? J. Laser Appl. 2012;24(5):50101.
3) H. Dickler & S. Tharmakulasingam: Powder on Demand – Rapid-Powder-Switch enhances economic efficiency in laser metal deposition and paves the way for new processing strategies, Laser Tech J. 14(5), 15-17 (November 2017); DOI: 10.1002/latj.201700028