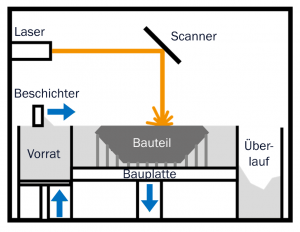
Abbildung 1: Prinzipaufbau einer Maschine des
Laserstrahlschmelzens
Chancen und Herausforderungen der additiven Fertigung
Additive Fertigungsverfahren gewinnen in den letzten Jahren zunehmend an Bedeutung. Als Gründe hierfür sind die wirtschaftliche und flexible Produktion kleiner Losgrößen, der Wegfall des Bedarfs an Bearbeitungswerkzeugen sowie die Realisierbarkeit von komplexen und bionischen Geometrien zu nennen. Zahlreiche Unternehmen setzen den schichtweisen Bauteilaufbau bereits zur Fertigung von Prototypen oder zur Fertigung von komplexen Funktionsbauteilen in Kleinserie ein. Dadurch werden Produktionskosten gesenkt, der Produktentstehungsprozess beschleunigt und neue Geschäftsfelder erschlossen. Die Anwendung additiver Fertigungsverfahren ist auch mit Herausforderungen verbunden. So erschwert insbesondere die prozessbedingt hohe Oberflächenrauigkeit metallbasierter additiver Fertigungsverfahren deren breite industrielle Anwendung. Die mit der notwendigen Bauteilnachbearbeitung einhergehenden Kosten können sich aufgrund der häufig sehr zeitaufwendigen und manuellen Tätigkeiten auf bis zu einem Drittel der bauteilbezogenen Gesamtkosten belaufen. Daher müssen die verfahrensspezifischen Gestaltungsprinzipien bei der Bauteilkonstruktion berücksichtigt werden und geeignete Nachbearbeitungsverfahren anwendungsspezifisch ausgewählt werden, um eine hohe Bauteilqualität und Produktivität der Nachbearbeitung zu erzielen.
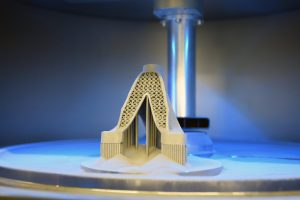
Abbildung 2: Mittels Laserstrahlschmelzen gefertigtes Bauteil nach dem Fertigungsprozess
Das Laserstrahlschmelzen
Beim Laserstrahlschmelzen, dem am häufigsten eingesetzten additiven Fertigungsverfahren für metallische Bauteile, werden Schicht für Schicht Metallpulver aufgeschmolzen und so sukzessiv Bauteile mit einer relativen Dichte von typischerweise über 99,9 % gefertigt. Der Fertigungsprozess zeichnet sich durch einen zyklischen Ablauf ab: Nach einem Auftrag einer Schicht Metallpulver wird der Querschnitt des zu fertigenden Bauteils selektiv mittels Laser belichtet (vgl. Abbildung 1). Durch das Aufschmelzen und das anschließende Erstarren des Metallpulvers nimmt das Bauteil Schicht für Schicht seine endgültige Form an. Anschließend wird die Bauplatte um eine Schichtdicke nach unten gefahren, bevor erneut eine Schicht Metallpulver aufgetragen wird und der Prozess von neuem beginnt.
Notwendigkeit der Nachbearbeitung
Nach dem Fertigungsprozess des Laserstrahlschmelzens können Bauteile nicht direkt aus der Maschine entnommen und ohne Nachbearbeitung eingesetzt werden (vgl. Abbildung 2). Die notwendigen Verfahrensschritte zur Nachbearbeitung additiv gefertigter Bauteile werden entsprechend der VDI 3405 in verfahrensspezifische und anwendungsspezifische Nachbearbeitungsschritte untergliedert (vgl. Abbildung 3) [1].
![Abbildung 3: Entstehung von thermischen Verzug beim Laserstrahlschmelzen in Folge hoher Temperaturgradienten in Anlehnung an Klahn [3]](https://werkstoffzeitschrift.de/wp-content/uploads/2020/09/Abbildung3-300x77.png)
Abbildung 3: Entstehung von thermischen Verzug beim Laserstrahlschmelzen in Folge hoher Temperaturgradienten in Anlehnung an Klahn [3]
![Abbildung 4: Abhängigkeit der Oberflächenqualität von der Orientierung der Bauteiloberfläche in Anlehnung an VDI 3405 [4]](https://werkstoffzeitschrift.de/wp-content/uploads/2020/09/Abbildung4-2-300x111.png)
Abbildung 4: Abhängigkeit der Oberflächenqualität von der Orientierung der Bauteiloberfläche in Anlehnung an VDI 3405 [4]
![Abbildung 5: Nachbearbeitungsschritte zur An- wendung von mittels Laserstrahlschmelzen ge-fertigten Bauteilen, in Anlehnung an VDI 3405 [1]](https://werkstoffzeitschrift.de/wp-content/uploads/2020/09/Abbildung5-300x300.png)
Abbildung 5: Nachbearbeitungsschritte zur Anwendung von mittels Laserstrahlschmelzen ge-fertigten Bauteilen, in Anlehnung an VDI 3405 [1]
Steigerung der Oberflächenqualität
Ein weiterer Grund für die Komplexität und die hohen Kosten der Nachbearbeitung additiv gefertigter Bauteile ist die prozessspezifische Oberflächenrauigkeit des gefertigten Bauteils. Diese ist insbesondere auf die begrenzte Auflösung des Fertigungsprozesses in Folge des Schicht-für-Schicht-Bauteilaufbaus, die Einschweißtiefe des Lasers und den Anhaftungen von Stützstrukturen zurückzuführen. Häufig ist die prozessspezifische Oberflächenrauigkeit additiv gefertigter Bauteile für deren direkte Anwendung als Ersatzteil oder Serienbauteil zu hoch. So weisen Oberflächen von Bauteilen, die mittels Laserstrahlschmelzen gefertigt wurden, typischerweise einen arithmetischen Mittenrauwert Ra von 5 bis 10 µm und eine gemittelte Rautiefe Rz von 20 bis 50 µm auf. Dabei ist die Oberflächenqualität insbesondere von der Orientierung der jeweiligen Fläche abhängig (vgl. Abbildung 5). Dies ist bei der Orientierung der Bauteile bei der Fertigung im Rahmen der Prozessvorbereitung zu berücksichtigen, um den prozessseitigen Nachbearbeitungsaufwand auf ein Minimum zu reduzieren.
Für eine kostengünstige Erzielung der geforderten Oberflächenqualität ist die Auswahl eines geeigneten Nachbearbeitungsverfahrens von großer Bedeutung. Hierbei ist zu berücksichtigen, dass durch die Nachbearbeitungsverfahren eine Vielzahl an Prozess- und Bauteilcharakteristika beeinflusst werden. So werden neben den verschiedenen Kennwerten der Oberflächenrauigkeit auch bspw. die Bauteilform durch die Verrundung von Kanten und die Bauteilabmessungen durch den Abtrag von Material verändert. Dabei gilt, dass je länger ein Bearbeitungsverfahren angewandt wird, die Oberflächenqualität bis zu einem verfahrensspezifischen Maximum verbessert wird – allerdings auch die Kantenverrundung, der Materialabtrag sowie die Kosten für die Nachbearbeitung steigen. Für die Nachbearbeitung stehen dem Anwender eine Vielzahl an Verfahren, wie bspw. das Druckluftstrahlen, das Gleitschleifen oder das Elektropolieren, zur Verfügung. Tabelle 1 gibt einen Überblick über die Charakteristika einer Auswahl von Nachbearbeitungsverfahren. Diese können in Abhängigkeit der jeweiligen Verfahrensparameter zusätzlich variieren.
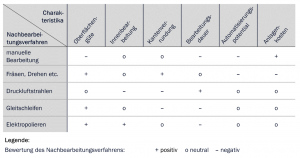
Tabelle 1: Charakteristika verschiedener Nachbearbeitungsverfahren
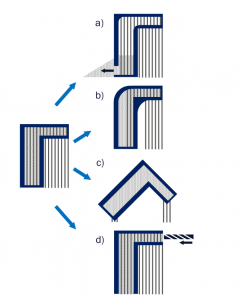
Abbildung 6: Gestaltungsrichtlinien für das Laserstrahlschmelzen
a) zur Entfernung von Pulver
b) zur Reduzierung von Eigenspannungen
c) zur Reduzierung des Bedarfs an Stützstrukturen
d) zur Realisierung der Werkzeugzugänglichkeit
Reduzierung des Nachbearbeitungsaufwands durch geeignete Bauteilkonstruktion und Prozessvorbereitung
Bereits in der Konstruktion und der Prozessvorbereitung kann durch Berücksichtigung von entsprechenden Gestaltungsrichtlinien der Nachbearbeitungsaufwand stark reduziert werden. Andernfalls kann deren Nicht-Beachtung zu einem Abbruch des Fertigungsprozesses aufgrund bspw. einer Bauteilablösung oder einer Kollision mit dem Beschichter und damit zu einem erhöhten Bauteilausschuss führen. Um die Entfernbarkeit des Metallpulvers aus Hohlräumen und filigranen Strukturen zu vereinfachen, sind scharfe Kanten bei innenliegenden Geometrien zu vermeiden und Öffnungen zur Pulverentfernung vorzusehen (vgl. Abbildung 6). Weiterhin kann durch die Vermeidung von Querschnittssprüngen oder dem Einsatz von Stützstrukturen und Versteifungsrippen einem Bauteilverzug in Folge von thermisch-induzierten Eigenspannungen entgegengewirkt werden. Da Stützstrukturen insbesondere bei überhängenden Flächen mit einem Winkel von über 45° gegenüber der Bauplatte benötigt werden, kann durch eine geeignete Orientierung des Bauteils der Bedarf an Stützstrukturen und damit der Aufwand der Nachbearbeitung signifikant reduziert werden. Zudem muss eine Zugänglichkeit von spanenden Werkzeugen zur Entfernung der Stützstrukturen berücksichtigt werden.
Häufig erfolgt im industriellen Umfeld sowohl die Bauteilauslegung und Prozessvorbereitung als auch die Auswahl der Nachbearbeitungsverfahren für das Laserstrahlschmelzen auf Basis von Erfahrungswerten und der Historie. Aus diesem Grund untersucht der Lehrstuhl Umweltgerechte Produktionstechnik der Universität Bayreuth in Zusammenarbeit mit der Projektgruppe Prozessinnovation des Fraunhofer IPA systematisch die Einflüsse verschiedener Nachbearbeitungsverfahren im Rahmen einer Benchmark-Analyse. Im Zusammenspiel mit einer geeigneten Bauteil- und Prozessauslegung können so die anwendungsspezifischen Bauteilanforderungen kostengünstig und reproduzierbar erzielt werden.
Referenz
[1] Additive Fertigungsverfahren – Grundlagen, Begriffe, Verfahrensbeschreibungen, VDI 3405, 2014.
[2] Bay, C.; Mahr, A.: Anwendersicherheit beim Laser-Strahlschmelzen von Metallpulvern im Rahmen der VDI-Richtlinie 3405, 2019.
[3] Klahn, C. et al.: Entwicklung und Konstruktion für die Additive Fertigung. Grundlagen und Methoden für den Einsatz in industriellen Endkundenprodukten. Würzburg: Vogel Business Media, 2018.
[4] Additive Fertigungsverfahren – Konstruktionsempfehlungen für die Bauteilfertigung mit Laser-Sintern und Laser-Strahlschmelzen, VDI 3405 3, 2015.
Autoren
Alexander Mahr
Projektgruppe Prozessinnovation des Fraunhofer Instituts für Produktionstechnik und Automatisierung (IPA)
Mail: alexander.mahr@ipa-fraunhofer.de
Tel. 0921 78516-228
Christian Bay
Universität Bayreuth – Lehrstuhl Umweltgerechte Produktionstechnik
Mail: christian.bay@uni-bayreuth.de
Tel. 0921 78516-226