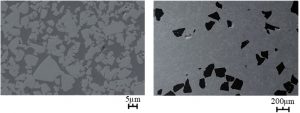
Abbildung 1. Mikrostrukturen von Hartmetall (links) und CBN-Verbundstoff (rechts) dargestellt, wobei
die unterschiedlichen Maßstäbe zu beachten sind.
Hintergrund
Bei der abrasiven Bearbeitung von Metallen können auf Werkstückoberflächen Qualitätsabweichungen aufgrund von Beschädigungen am Werkzeug auftreten. Manchmal sind Kratzer auf den Werkstücken infolge des Ausbrechens der harten abrasiven Körner zu beobachten. Das unerwartete Abbrechen der Körner resultiert ansatzweise aus geometrischen Unregelmäßigkeiten oder der inhomogenen Verteilung der abrasiven Körner in der Matrix infolge des Herstellungsprozesses. Es wird bereits daran gearbeitet, eine bessere Homogenität der abrasiven Körner zu erreichen, jedoch zielen bisherige Maßnahmen meistens auf die Verbesserung des Herstellungsprozesses. Es ist bisher noch eine praktische Herausforderung, Qualitätsabweichungen zu kontrollieren bzw. zu reduzieren. Es wird ein neuartiges Konzept von Hartmetallwerkzeugen mit definierten geometrischen Merkmalen und homogenen Verteilungen der Schneidkanten für die Feinbearbeitung vorgeschlagen. Die Oberfläche der Hartmetallwerkzeuge, deren Topographie die der konventionellen abrasiven Werkzeuge reproduziert, entsteht durch Lasertechnik präzise im Mikrobereich. In der Folge könnten Herstellkosten im Vergleich zu konventionellen abrasiven Werkzeugen, z.B. aus Diamanten oder CBN, reduziert werden.
Hartmetall vs. herkömmliches abrasives Material
Bei der abrasiven Bearbeitung von Metallen wird das zu bearbeitende Material durch eine Vielzahl winziger und scharfer Schneidkanten von harten abrasiven Körnern entfernt, die durch Abrichten aus der Werkzeugoberfläche hervortreten. Diese Verbundwerkstoffe werden normalerweise unter hoher Temperatur und/oder hohem Druck hergestellt, wobei harte Körner in ein „weiches“ z.B. metallisches, keramisches oder kunstharziges Bindemittel eingebettet werden. Die Körner sind üblicherweise harte Substanzen wie Diamant, kubisches Bohrnitrid (CBN), Korund (Al2O3) oder Siliciumcarbid (SiC) sowie Hartmetalle, nämlich Wolframcarbid (WC), früher Widia (abgeleitet von Wie Diamant) als Markennamen genannt, wurden zuerst mit dem Ziel hergestellt, sie als Ersatz für Diamanten in der Metallbearbeitung zu verwenden.
Bislang werden Hartmetalle erfolgreich in der Metallbearbeitung eingesetzt, insbesondere mit einer breiten Anwendung beim konventionellen Zerspanen bzw. beim Zerspanen mit geometrisch bestimmten Schneiden, wie Drehen und Fräsen. Bei der Feinbearbeitung, genauer der Zerspanung mit geometrisch unbestimmten Schneiden, ist die Anwendung von Hartmetallen jedoch begrenzt, obwohl beide d.h. sowohl Hartmetalle als auch abrasive Verbundwerkstoffe, einige mikrostrukturelle Ähnlichkeiten aufweisen (Abbildung 1). Hartmetalle werden üblicherweise nicht bei der Feinbearbeitung verwendet, da die Abmessung der Karbide oft weniger als 5 µm und üblich im Bereich vom Submikron bis zum Mikron beträgt, was ungefähr eine Größe kleiner als die der abrasiven Körner ist. Darüber hinaus wird die Zerspanungswirkung der einzelnen Carbide der Hartmetalle nicht individuell einfach auftreten und Hartmetall sind deswegen eher als ‘Bulk‘ verwendet, z.B., Schneidplatten der Werkzeuge für geometrische bestimmte Zerspanungsverfahren.
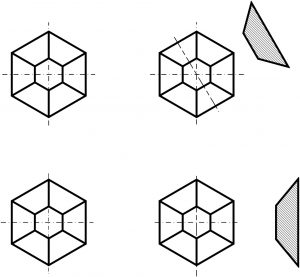
Abbildung 2. Design mit definierten sechseckigen Pyramiden auf Hartmetall-Werkzeugoberflächen.
Design der Hartmetall-Werkzeuge
Um die o.g. Defizite zu beseitigen, wird ein neues Konzept eines Hartmetallwerkzeugs zur Feinbearbeitung vorgeschlagen: auf den Hartmetalloberflächen werden künstlich harte Körner mit bestimmten geometrischen Merkmalen erzeugt. Einerseits können diese Kornanaloga ähnliche Abmessungen wie die üblichen abrasiven Körner haben, d.h. zwischen 10 µm und 200 µm, andererseits können die Formen der künstlichen Körner nach Vorgabe ausgelegt werden, z.B. wie in Abbildung 2, wobei die Querschnitte der Körner sechseckig sind. Zusätzlich werden die mechanischen Eigenschaften dieser künstlichen Körner verstärkt, da sie Carbid und Bindemittel in winzigen Volumen verbinden. Aus makroskopischer Sicht wird auf diese Weise eine Vielzahl winziger Schneidkanten auf die Arbeitsflächen von Hartmetallen geformt, und diese winzigen extrudierten Schneidkanten ähneln den Schneidkanten abrasiver Körner (Abbildung 3).
Herstellung von winzigen Schneidkanten auf Hartmetallen
Die Mikrobearbeitung von Hartmetallen unter Verwendung traditioneller Schneidmethoden ist aufgrund ihrer harten und spröden Natur schwierig und herausfordernd. Von daher wurden Verfahren wie das Funkenerodieren (EDM) bereits erfolgreich für Hartmetalle implementiert. Jedoch ist die Präzision durch das elektrische Funkenverfahren stark eingeschränkt. Dies führt häufig zu geringfügigen thermischen Effekten auf die mikrostrukturelle Integrität der fertigen Oberflächen, wie Oxidation, Poren oder sogar Risse.
Durch die neu entwickelte Laser-Oberflächenstrukturierungstechnologie, insbesondere mit Ultrakurzpulslasern (meist in Pikosekunden oder Femtosekunden) wird die präzise Bearbeitung von harten Materialien möglich. Die üblichen thermischen Nebenwirkungen, die durch EDM entstehen, können wirksam reduziert, insbesondere eine bessere Oberflächenintegrität erreicht werden. Durch die präzise Bewegungssteuerung der Laserstrahlen wird die Produktionsgenauigkeit verbessert, sie ermöglicht die Bearbeitung von Hartmetall im Mikrobereich. Aus technischer Sicht kann eine Topographie mit definierten geometrischen Merkmalen auf Hartmetalloberflächen erzeugt werden (Abbildung 3).
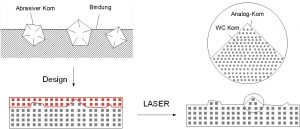
Abbildung 3. Schematische Darstellung der Replikation von Schleifkörnern auf Hartmetallen
Einige Ergebnisse: Herstellung von sechseckigen Pyramiden auf Hartmetallen
Die Pyramiden, die bisher im Kontext eines DFG-geförderten Forschungsprojekts hergestellt wurden, haben eine gute Übereinstimmung mit dem ursprünglichen Design hinsichtlich Maß- und Formgenauigkeit im Mikromaßstab erreicht. Wie in Abbildung 4 gezeigt, sind diese sechseckigen Pyramiden beispielsweise regelmäßig und intakt auf der Hartmetalloberfläche verteilt. Sie zeigten durchschnittliche Seitenlängen von 60 μm (unten) und von 25 μm (oben) sowie eine durchschnittliche Höhe von 25 μm.
Die Oberflächeninspektion und die Querschnittsanalyse zeigten eine hervorragende Integrität der Oberfläche und der Suboberfläche. Die Oberflächenmorphologie wurde durch die Laserstrahlen nicht verschlechtert. Das laserstrukturierte Hartmetallwerkzeug konnte eine verbesserte und glattere Oberfläche erzielen als herkömmliche abrasive Werkzeuge, die unter den gleichen Schnittbedingungen getestet wurden. Ein Vergleich der Oberflächenverbesserung ist in Abbildung 6 gezeigt. Durch das Hartmetallwerkzeug konnte die Rauheit bespielweise verbessert werden: Ra von 4 µm auf 1 µm und Rz von 25 µm auf 10 µm.
- Abbildung 4. Hergestellte Pyramiden und Vermessung der geometrischen Merkmale
- Abbildung 5. Oberflächeninspektion und Querschnittsanalyse einer Pyramide
- Abbildung 6. Vergleich der Oberflächenverbesserung durch: laserstrukturiertes Hartmetallwerkzeug (links), und vergleichend das CBN-Schleifwerkzeug (rechts)
Dank
Die Ausarbeitung dieses Konzepts erhielt die Förderung der Deutsche Forschungsgemeinschaft (DFG) durch das Projekt (425923019) „Laseroberflächenstrukturierte Hartmetalle für den Einsatz in abrasiven Bearbeitungsprozessen“.
Referenz
[1] Fang, S., 2020, Morphological study of a cubic boron nitride (CBN) cutting tool and characterization of its wear scenarios in abrasive machining process, Ceramics International, 46/11:19491–19498, DOI:10.1016/j.ceramint.2020.04.302.
[2] Fang, S., Pérez, V., Salán, N., Baehre, D., Llanes, L., 2020, Surface Patterning of Cemented Carbides by Means of Nanosecond Laser, Materials and Manufacturing Processes, 35/2:123–129, DOI:10.1080/10426914.2019.1628268.
[3] Fang, S., Llanes, L., Bähre, D., 2018, Laser surface texturing of a WC-CoNi cemented carbide grade: Surface topography design for honing application, Tribology International, 122/2:236–245, DOI:10.1016/j.triboint.2018.02.018.
Autor*innen:
Shiqi Fang (Dr.-Ing.),
shiqi.fang@uni-saarland.de
Dirk Bähre (Univ.-Prof. Dr.-Ing.)
Lehrstuhl für Fertigungstechnik,
Universität des Saarlandes,
66123 Saarbrücken