Nachhaltige Materialentwicklungen ohne Einbußen beim Design und Komfort sind seit einigen Jahren ein wesentlicher Innovationstreiber bei der Herstellung von Verkleidungsteilen im automobilen Innenraum. Sichtbare Naturfaseroberflächen sind ebenso Stand der Technik wie druckelastische Bauteile. Bislang war es aber noch nicht möglich, beides ansprechend miteinander zu kombinieren. Bauteile mit angenehmen soft-touch Eigenschaften sind derzeit noch aus Mehrstoffsystemen mit weichen Zwischenschichten aufgebaut. Letztere können häufig nur mit erheblichem Kosten- und Energieaufwand gefertigt werden und deren Materialien (PVC-Slushhäute, isocyanatbasierte Schäume, Abstandgewirke) lassen sich nur schwer recyceln und sind daher mit den Nachhaltigkeitszielen schwer zu vereinbaren.
Im Rahmen eines Forschungsvorhabens hat das Thüringische Institut für Textil- und Kunststoff-Forschung e.V. Prozesse und Materialien untersucht, um ansprechende, druckelastische bzw. soft-touch Oberflächen auf Basis von Naturfaserverbundwerkstoffen zu entwickeln (Abb. 1).
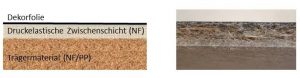
Abb. 1: Materialaufbau
Zur Herstellung der druckelastischen Schichten kamen bekannte Vliesbildungsverfahren wie beispielsweise die Krempeltechnologie mit anschließender Vernadelung zum Einsatz. Eine weitere Variante ist die Nutzung der Airlaidtechnologie zur Herstellung von Vliesen auf Basis cellulosischer Kurzfasern (Zellstoff) auch in Kombination mit PES-basierten Bindefasern. Zur Beurteilung des Eindruckverhaltens wurde der Eindruckweg bei vorgegebener Kraft (25 N, Druckstempel: Halbkugel Ø 20 mm, Prüfgeschwindigkeit 5 mm/min) mit einer Universalprüfmaschine bestimmt (siehe Abb. 2).
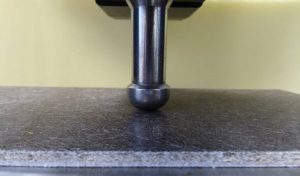
Abb. 2: Bestimmung des Eindruckwegs bei 25 N (Druckstempel: Halbkugel Ø 20 mm, Prüfgeschwindigkeit 5 mm/min
Durch die gezielte Auswahl von Fasern mit unterschiedlichen Feinheiten wie Kenaf (grob), Flachs (mittel) und Cellulose (fein) sowie die Kombination mit geringen Anteilen an PES-Fasern lassen sich die druckelastischen Eigenschaften und das Eindruckverhalten gezielt beeinflussen. Mit Blick auf das Gesamtbauteilgewicht sollte die druckelastische Schicht maximal 400 g/m² aufweisen (Abb. 3).
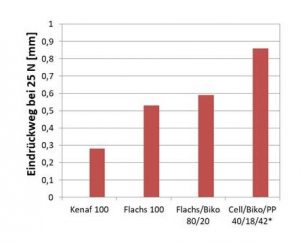
Abb. 3: Eindrückweg verschiedener naturfaserbasierter Vliesschichten (alle 400 g/m² und mit 150 µm PP-Dekorfolie)
Die erforderliche Beständigkeit der Oberflächen wird durch den Einsatz einer geeigneten PP-Dekorfolie (Standardfolien für automobile Anwendungen) erzielt. Je nach Designanforderung kann diese für eine Naturfaseroptik auch transparent/transluszent sein. Hierfür wird die druckelastische Vliesschicht zunächst in einer Doppelbandpresse mit der Dekorfolie kaschiert. Dieses Verfahren erwies sich aufgrund der gleichmäßigen Temperatur- und Druckverteilung als besonders geeignet. Die Trägerkaschierung erfolgt im Pressverfahren. Um die druckelastischen Eigenschaften der Schicht während des Konsolidierens zu erhalten, muss der Werkzeugspalt gegenüber eines Standard-Naturfaserträgers sowohl in der Fläche als auch an den Flanken und Kanten angepasst werden (Abb. 4). Dabei lassen sich im Vergleich zu den etablierten Verfahren (Slushhautherstellung und Hinterschäumen) Werkzeug- und Prozesskosten einsparen.
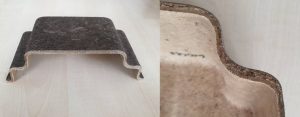
Abb. 4: 3D-Demobauteil
Aufgrund der Materialbasis (Natur- oder Cellulosefasern, PP und gegebenenfalls PES-Fasern) können sowohl die Produktionsabfälle als auch die Bauteile am Ende ihrer Nutzungsdauer recycelt werden. Dazu werden diese geshreddert, compoundiert und stehen anschließend als spritzgießfähiges Naturfaserverbundmaterial für neue Anwendungen, beispielsweise zum Hinterspritzen von Naturfaserträgern, wieder zur Verfügung (Abb. 5).
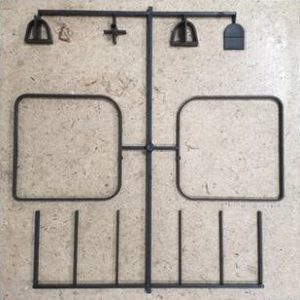
Abb. 5: hinterspritzter Naturfaserträger, Gesamtfasergehalt des SG-Materials: 20 Gew.-%
Dieses Material verfügt über Festigkeits- und Steifigkeitswerte, die einen Wiedereinsatz für Komponenten im Automobilinnenraum ermöglichen und im Bereich der Schlagzähigkeit durch den PES-Faseranteil deutliche Vorteile aufweisen (Abb. 6). Bevorzugte Bauteile können Inserts für Türverkleidungen oder Anbauteile im nichtsichtbaren Bereich sein.
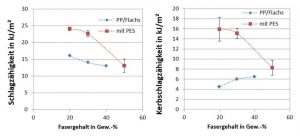
Abb. 6 Schlagzähigkeit recycelter Versuchsmaterialien in Abhängigkeit des Gesamtfasergehaltes (bestehend aus Naturfasern und PES-Fasern)
Danksagung
Die Autoren danken der EuroNorm GmbH für die finanzielle Förderung des Forschungsvorhabens 49MF170061, das als Fördermaßnahme des Bundesministeriums für Wirtschaft und Energie im Rahmen der „FuE-Förderung gemeinnütziger externer Industrieforschungseinrichtungen – Innovationskompetenz (INNO-KOM) – Modul: Marktorientierte Forschung und Entwicklung (MF)“ erfolgte.
Autoren:
Katrin Ganß, Dr. Thomas Reußmann, Ines Orlob
Kontakt:
Katrin Ganß,
Thüringisches Institut für Textil- und Kunststoff-Forschung e.V.
Abt. Textil- und Werkstoff-Forschung
Breitscheidstr. 97,
07407 Rudolstadt
E-Mail: ganss@titk.de,
Tel.: 03672-379315