Einleitung
Im Zuge der globalen Klimakrise rückt das Thema Leichtbau in allen Bereichen des Transportwesens zunehmend in den Fokus. Dies gilt auch für den Schiffbau, der heutzutage noch überwiegend auf dem Einsatz von Stahl basiert. Im Vergleich zu diesem Material besitzen Faserverbundwerkstoffe (FVW) aufgrund ihrer sehr guten spezifischen mechanischen Eigenschaften ein hohes Leichtbaupotenzial. Aus diesem Grund bietet ihr Einsatz die Möglichkeit zur Einsparung von Kraftstoff und damit zur Verringerung von CO2-Emissionen. FVW zeichnen sich darüber hinaus im Vergleich zu Stahl durch weitere Vorteile wie große Gestaltungsfreiheit, hohen Korrosionswiderstand sowie gute thermische und akustische Dämmung aus. Im Sport- und Freizeitbereich bestehen Boote deshalb zu großen Teilen aus Verbundwerkstoffen. Im kommerziellen Schiffbau ist der Einsatz von FVW allerdings sehr problematisch.
Problemstellung
Um die äußerst strengen Brandschutzbestimmungen der UN-Konvention SOLAS (Safety of Life at Sea) der Internationalen Seeschifffahrts-Organisation (International Maritime Organization – IMO) zu erfüllen, müssen im Schiffbau nichtbrennbare, stahl-äquivalente Werkstoffe eingesetzt werden [1]. Hintergrund der strikten Konvention in der Fahrgastschifffahrt ist das hohe Gefährdungspotential der Passagiere im Brandfall infolge der schwierigen Evakuierungssituation auf hoher See.
In Faserkunststoffverbunden (FKV) üblicherweise eingesetzte organische Matrixsysteme (z.B. Epoxid- oder Polyesterharze) erreichen bei Temperaturen über 500°C ihren Flammpunkt und verbrennen unter starker Wärmefreisetzung. Bei dieser exothermen Reaktion entstehen für den Menschen toxische Rauchgase. Außerdem kann es zum sogenannten brennenden Abtropfen kommen. Hierdurch können sich Brände beispielsweise auch von höher zu tiefer gelegenen Decks ausbreiten. Aus diesen Gründen erhalten die Materialien keine Zulassung für Bereiche mit den höchsten Brandschutzklassen. Die einzige Möglichkeit zur Erreichung der strengen Zulassungen im Schiffbau besteht in der Substitution der organischen Matrizes durch anorganische, nichtbrennbare Systeme, die keine negativen Begleiterscheinungen unter Flammeinwirkung besitzen.
Es existieren zwar verschiedene, als Matrixsysteme für FVW geeignete, anorganische Materialien und diese lassen sich auch prinzipiell ähnlich wie klassische Reaktionsharze verarbeiten. Zwei Komponenten werden in einem bestimmten Mischungsverhältnis zusammengebracht und härten (bei Raumtemperatur) kalt aus, indem sie chemisch miteinander reagieren. Die genauen Inhaltsstoffe der Komponenten sind aber häufig unbekannt oder unterliegen strenger Geheimhaltung, so dass von den Herstellern nur fertige Bauteile bezogen werden können. Deshalb mangelt es grundsätzlich an wesentlichem Basiswissen zum Einsatz anorganischer Matrixsysteme. Wichtige Prozessparameter und deren Auswirkungen auf die Fertigung und Aushärtung der Materialien sind unbekannt. Es ist nicht klar, welche Faserhalbzeuge eingesetzt und welche Faservolumengehalte realisiert werden können. Außerdem fehlen mechanische Kennwerte der Matrixsysteme sowie der anorganischen FVW für die Auslegung von Bauteilen.
Zielsetzung des Forschungsprojekts
Um FVW im Schiffbau einsetzen zu können, haben das Fraunhofer Institut für Großstrukturen in der Produktionstechnik (IGP) und die Technische Universität Clausthal zusammen mit Vertretern aus der Industrie das Forschungsprojekt AnorKomp initiiert. Das angestrebte Ziel des Vorhabens besteht in der Schaffung von Anwendungsgrundlagen für die Fertigung und den Einsatz von FVW auf Basis einer nichtbrennbaren, kalthärtenden, anorganischen Matrix vor allem für schiffbauliche Anwendungen. Hierzu sollen wissenschaftliche sowie anwendungsorientierte Kenntnisse in den Bereichen Material (Faser, Matrix, Additive, etc.), Fertigung (Verfahren, Prozessparameter) und Verbundwerkstoff (mechanische, technologische, chemische Eigenschaften) aufgebaut werden.
Ausgewählte Projektarbeiten und Ergebnisse werden im Folgenden vorgestellt.
Entwicklung eines anorganischen Matrixsystems
Ein zentraler Bestandteil des Projekts ist die Entwicklung eines kalthärtenden, anorganischen Matrixsystems. Hierbei fällt die Wahl auf die Klasse der Geopolymere – amorphe bis semi-kristalline, dreidimensionale, alumosilikatische Materialien, die sich bei niedrigen Temperaturen oder bei Raumtemperatur bilden [2]. Zu deren Synthese werden ein reaktiver pulverförmiger Feststoff, der genügend amorphes Silizium- und Aluminiumoxid enthält, und eine alkalische Aktivatorlösung als Bindemittel benötigt. Bei der chemischen Reaktion der beiden Komponenten, der sogenannten Geopolymerisation, härtet das Stoffgemisch zu einem wasserbeständigen Alumosilikatnetzwerk aus [3].
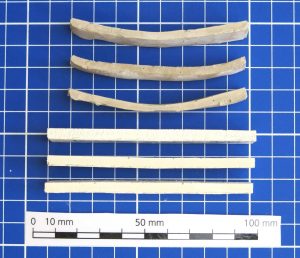
Abbildung 1: Drei durch Eigenspannungen verformte Probekörper (oben) – hergestellt aus einer empirischen Mischung der beiden Komponenten Natronwasserglas und Metapor® – und drei mit der optimierten Rezeptur hergestellte Probekörper (unten)
Ausgangsbasis der Matrixentwicklung sind alkalisches Natronwasserglas, eine flüssige Lösung von Natriumsilikaten, als Aktivator und das Produkt Metapor®, ein Stoff auf Basis von amorphem Alumosilikat, als reaktiver pulverförmiger Feststoff. Eine empirische Mischung der beiden Komponenten führt zu einer Aushärtereaktion. Die Festigkeitsbildung setzt allerdings erst nach sehr langer Zeit ein. Außerdem kommt es bei der Herstellung von Probekörpern zu starken inneren Eigenspannungen, die die Probekörper deutlich verformen (Abbildung 1, oben) oder sogar zerstören.
Zur Beschleunigung der Festigkeitsbildung erweist sich ferrit-freier Weißzement als geeignet, zur Reduzierung der Eigenspannungen das Mineral Wollastonit – ein Calciummetasilikat, welches hauptsächlich als Füllstoff wirkt. Durch die Zugabe dieser beiden Komponenten reduziert sich die Topfzeit aber so stark, dass eine Fertigung faserverstärkter Bauteile nicht möglich ist. Deshalb wird dem Wasserglas Natriumhydroxid (NaOH) in Plätzchenform als Verzögerer beigemischt. NaOH erhöht die Topfzeit, beeinträchtigt aber die darauffolgende Aushärtung nicht. Zur Beschleunigung der Festigkeitsbildung kommt schließlich wasserfreies Calciumsulfat (auch Anhydrit genannt) zum Einsatz. Dieses löst sich langsam in der Mischung auf, so dass die Topfzeit nicht verkürzt wird. Erst nach der Auflösung reagiert es mit dem freien Aluminiumoxid und den Calciumionen zu Ettringit, einer Phase, die auch jungem Zement seine Festigkeit verleiht.
Die Rezeptur des anorganischen Matrixsystems wird anhand der sechs Inhaltsstoffe – Wasserglas, Natriumhydroxid, Metapor, Wollastonit, Weißzement und Anhydrit – anschließend iterativ weiterentwickelt, bis ein optimales Ergebnis bezüglich Verarbeitung, Aushärtung und mechanischer Eigenschaften gefunden wird. Verformungen infolge von inneren Eigenspannungen treten bei der Herstellung von Probekörpern in der Folge nicht mehr auf (Abbildung 1, unten).
Abschließend soll auch die thermische Stabilität des anorganischen Matrixsystems nachgewiesen werden. Zu diesem Zweck kommt ein Bunsenbrenner zum Einsatz (Abbildung 2, links). Das reine Matrixmaterial übersteht eine 15-minütige thermische Beanspruchung bei etwa 1150 °C ohne Schaden zu nehmen. Im Laufe der Zeit beginnen lediglich die unteren 2 mm des Probekörpers zu glühen. Der restliche Teil erreicht keine Temperatur, bei der ein Aufglühen einsetzt. Weiterhin kommt es zu keiner Verformung, sondern nur zu einer oberflächlichen Verfärbung des Probekörpers (Abbildung 2, rechts). Damit übertrifft die Temperaturbeständigkeit des Matrixmaterials sogar die Beständigkeit speziell verarbeiteter und veredelter Hochtemperaturfasern aus Alkalisilikatglas, die bei maximal 1100 °C liegt [4].
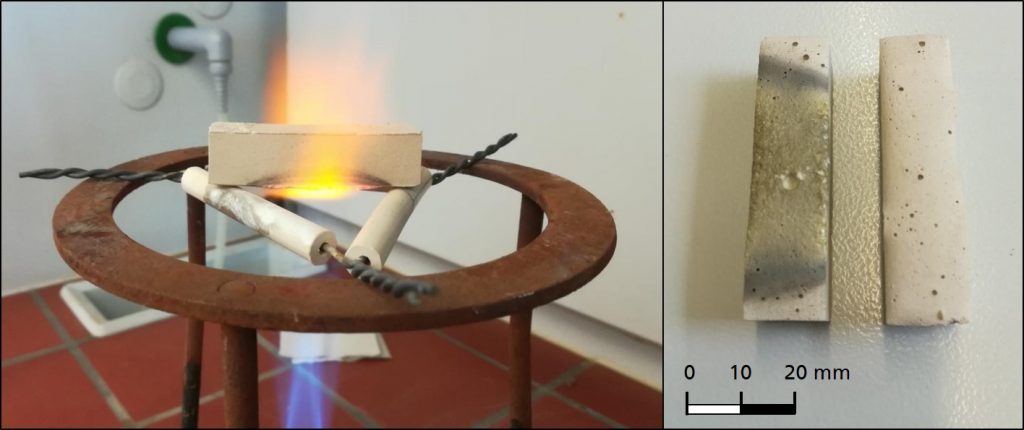
Abbildung 2: Nachweis der thermischen Stabilität des anorganischen Matrixsystems unter Einsatz eines Bunsenbrenners (links), Vergleich eines thermisch beanspruchten und eines nicht beanspruchten Probekörpers (rechts)
Herstellung und Prüfung anorganischer FVW
Auf Basis der optimierten Rezeptur werden glasfaserverstärkte Laminate für Drei-Punkt-Biege- und Zugprüfungen hergestellt. Die Fertigung erfolgt im Handlaminierverfahren in einer Form aus Silikon (Abbildung 3). Das Material besitzt eine exzellente Trennwirkung und vereinfacht aufgrund seiner Flexibilität die Entformung der ausgehärteten Laminate. Als Faserhalbzeuge dienen spezielle offenmaschige Gewebe – von der Fa. Gustav Gerster GmbH – mit alkaliresistenten (AR-)Glasfasern sowie Wirrfasermatten mit E-Glasfasern (Abbildung 4). Gelege werden nicht verwendet, da sich deren Faserbündel, Rovings genannt, mit dem anorganischen Matrixsystem kaum tränken lassen.
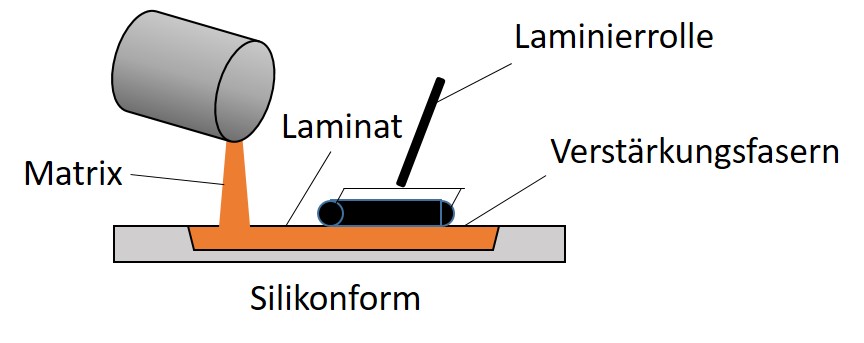
Abbildung 3: Schematische Darstellung der Laminatfertigung im Handlaminierverfahren
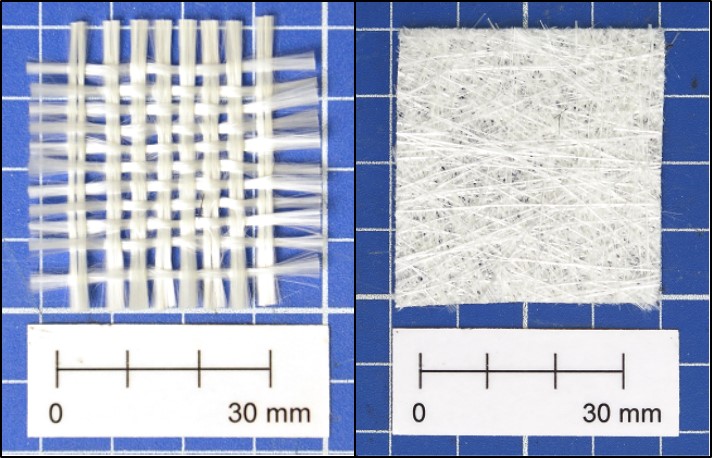
Abbildung 4: Offenmaschiges AR-Glas-Gewebe (links) und E-Glas-Wirrfasermatte (rechts)
Die Faservolumengehalte (FVG) j der vier Laminate (Übersicht in Tabelle 1) liegen alle in einem vergleichbaren Bereich um etwa 12%. Sie werden über die Lagenzahl n, das Flächengewicht der Faserhalbzeuge FG, die Dicke der Laminate d (Mittelwert aus acht Messungen) und die Dichte der Glasfasern ρf (2,6 g/cm³) rechnerisch nach Gleichung 1 [5] bestimmt:
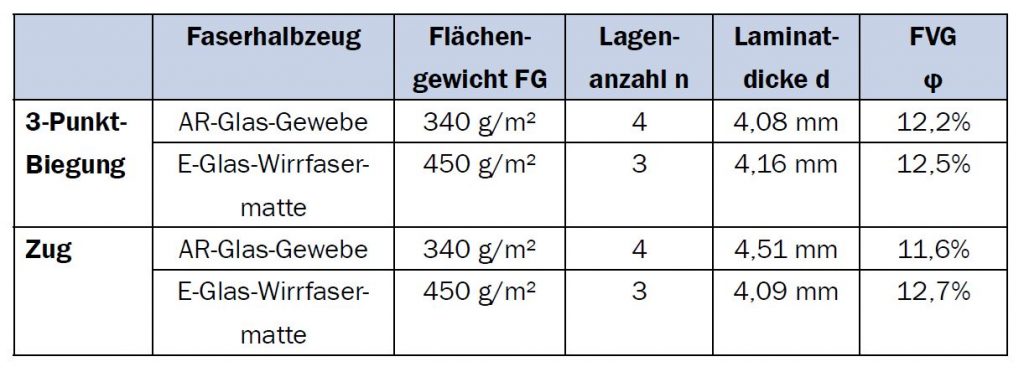
Tabelle 1: Übersicht der gefertigten glasfaserverstärkten Laminate
Nach der Aushärtung werden aus den Laminaten Probekörper für die Biege- und Zugprüfungen präpariert. Die Zugproben (150 mm x 25 mm x ca. 4 mm) werden nach dem Zuschnitt beidseitig mit Aufleimern aus glasfaserverstärktem Kunststoff (GFK) verstärkt, welche der materialgerechten Krafteinleitung dienen und verhindern sollen, dass die Proben in der Einspannung versagen. Die Biegeproben (90 mm x 15 mm x ca. 4 mm) müssen nach dem Zuschnitt nicht zusätzlich bearbeitet werden.
Die Ergebnisse der Prüfungen zeigen erwartungsgemäß, dass aufgrund der gerichteten Fasern mit der Gewebeverstärkung in der Regel höhere mechanische Eigenschaften erreicht werden können als mit den Wirrfasermatten.
Bei der Betrachtung der Biegeeigenschaften zeigt sich, dass die Festigkeit des Gewebelaminats mit 38,3 MPa etwa 45 % über der des Wirrfaserlaminats mit 26,4 MPa liegt (Abbildung 5). Der Biege-Modul – bestimmt im linearen Bereich der Spannungs-Dehnungs-Verläufe zwischen 0,1 und 0,5 % Randfaserdehnung – ist mit nur 2.000 MPa aber fast 30 % geringer. Das Wirrfaserlaminat besitzt ein Biege-Modul von fast 2.900 MPa. Im Gewebelaminat liegen die Rovings aufgrund der Faserarchitektur – mit sich kreuzenden Kett- und Schussfäden – nicht vollständig gestreckt vor. Zu Beginn der Biegebeanspruchung dominiert deshalb die Festigkeit der Matrix. Die Wirrfasermatten zeigen mit ihren nicht gerichteten Fasern, die sich beim Laminieren teilweise auch in Dickenrichtung orientieren, in dieser Hinsicht zunächst eine bessere Verstärkungswirkung. Nach etwa 1 % Randfaserdehnung versagen die Wirrfaserproben dann aber bereits, während die Gewebeproben mehr als die doppelte Bruchdehnung ertragen können (Abbildung 6).
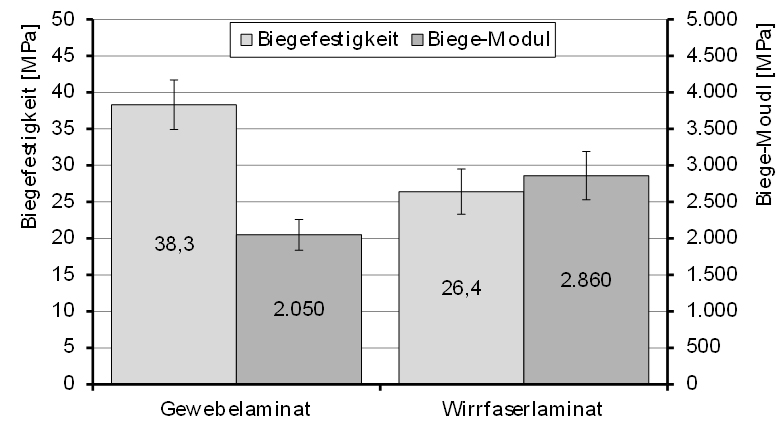
Abbildung 5: Biegeeigenschaften gewebe- und wirrfaserverstärkter Laminate
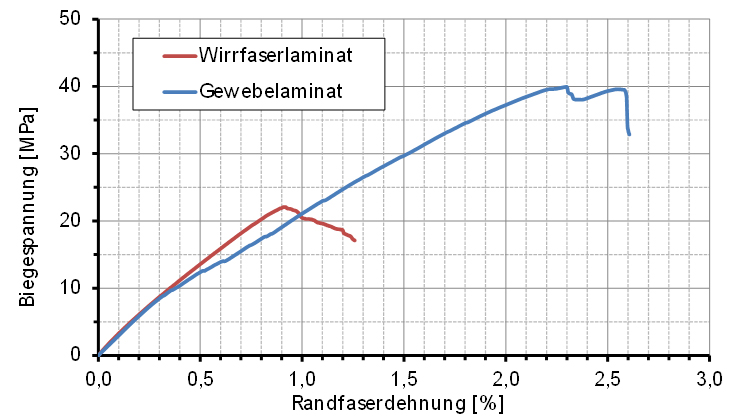
Abbildung 6: Exemplarische Biegespannungs-Randfaserdehnungs-Verläufe
Unter Zugbelastung ist die Festigkeit des Gewebelaminats mit 42,4 MPa mehr als dreimal so hoch wie die des Wirrfaserlaminats mit 13,0 MPa (Abbildung 7). Die Orientierung der Fasern macht sich hier trotz mangelhafter Faser-Matrix-Anbindung deutlicher bemerkbar. Bruchbilder der gewebeverstärkten Proben (Abbildung 8) zeigen vollständig trockene Rovings, die aus der Matrix herausgezogen werden (Pull-Out) und anschließend reißen. Im Rahmen weiterer Projektarbeiten wurden deshalb verschiedene Ansätze zur Verbesserung der Faser-Matrix-Anbindung untersucht. Der E-Modul des Gewebelaminats – bestimmt im linearen Bereich der Spannungs-Dehnungs-Verläufe – liegt mit knapp 4.000 MPa ebenfalls etwa 40 % über dem des Wirrfaserlaminats mit etwa 2.800 MPa.
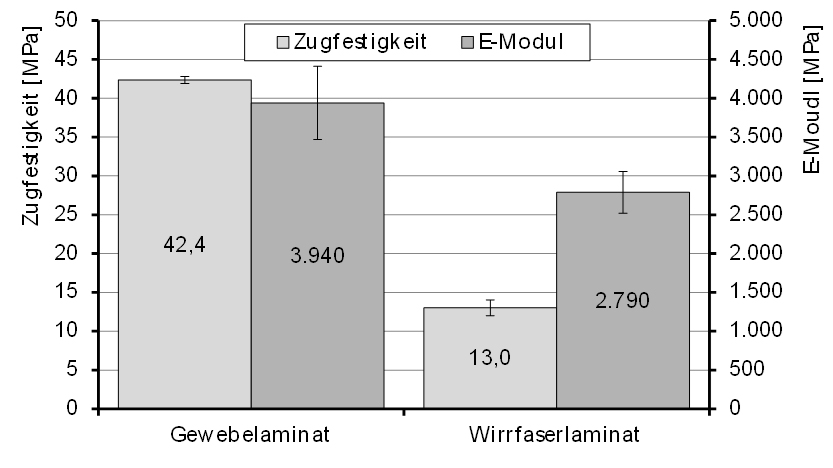
Abbildung 7: Zugeigenschaften gewebe- und wirrfaserverstärkter Laminate
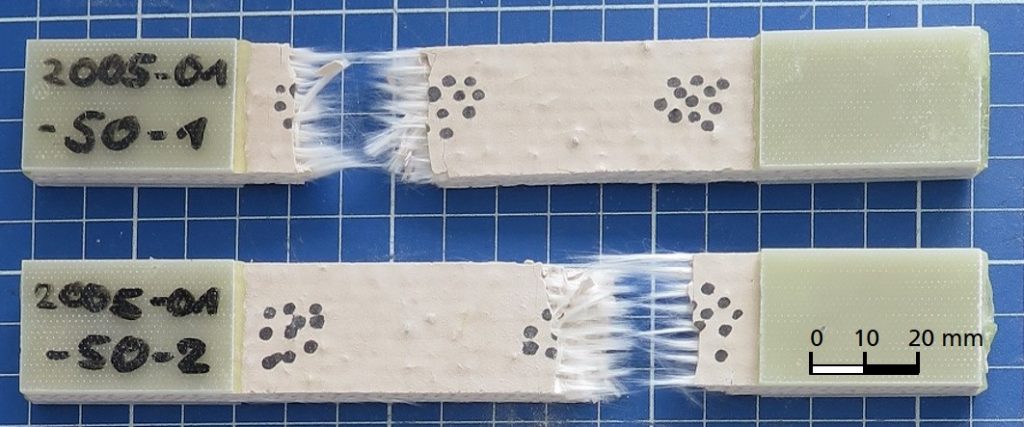
Abbildung 8: Exemplarische Bruchbilder gewebeverstärkter Zugproben
Fertigung eines Demonstratorbauteils
Die Wahl für das abschließende Demonstratorbauteil des Forschungsvorhabens fällt auf den – nach seinem Entwickler Verner Panton benannten – Panton Chair. Ein Exemplar des freischwingenden Stuhls aus Kunststoff dient bei der Fertigung als Laminierform. Zunächst werden zehn Lagen des Glasfasergewebes der Fa. Firma Gustav Gerster GmbH entsprechend der Kontur der Stuhlrückseite ausgeschnitten. Die Gewebezuschnitte werden anschließend Lage für Lage auf dem Kunststoffstuhl drapiert und mit einem jeweils neu angerührten Ansatz des Matrixsystems getränkt und imprägniert. Nach Fertigstellung der letzten Lage wird der gesamte Stuhl in Folie eingewickelt, um eine zu schnelle Feuchtigkeitsabgabe des Matrixmaterials zu verhindern und der Rissbildung vorzubeugen. Nach der etwa 24-stündigen Aushärtung wird der Stuhl entformt, d.h. von seiner Kunststoffform getrennt. Anschließend werden auf der Vorderseite ungetränkte Stellen nachträglich mit neuem Matrixmaterial bearbeitet. Das fertige Exemplar (Abbildung 9) kann nach dem erneuten Aushärten genutzt werden.
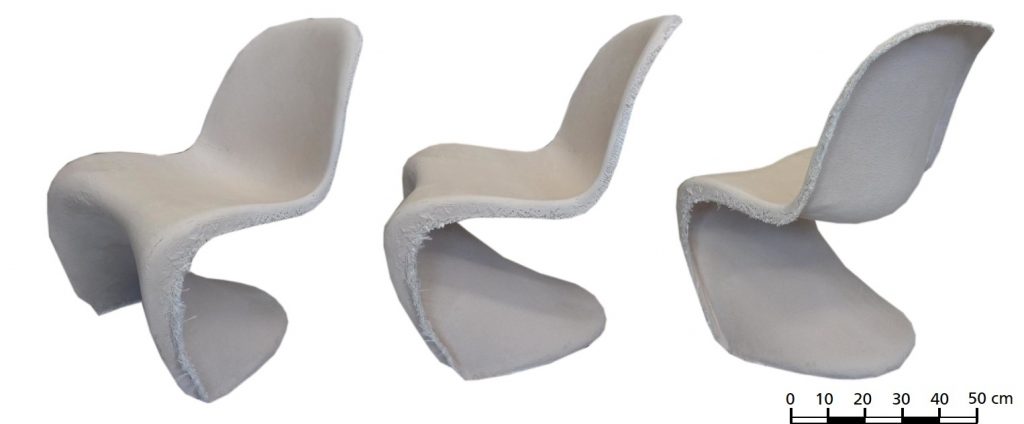
Abbildung 9: Panton Chair aus anorganischem Verbundwerkstoff (verschiedene Perspektiven)
Fazit
Im Forschungsprojekt AnorKomp konnte eine neue Rezeptur für ein kalthärtendes, anorganisches Matrixsystem entwickelt werden, das die Schaffung von Anwendungsgrundlagen zur Fertigung und zum Einsatz nichtbrennbarer FVW ermöglichte. In Rahmen der in diesem Artikel vorgestellten, ausgewählten Projektarbeiten wurden Laminate mit verschiedenen Faserhalbzeugen hergestellt und deren mechanische Kennwerte in Biege- und Zugprüfungen ermittelt. Schließlich konnte anhand eines Demonstratorbauteils die Eignung des FVW auch für komplexe dreidimensionale Strukturen demonstriert werden. Mögliche Einsatzbereiche im Schiffbau werden in nichttragenden Bauteilen – wie beispielsweise Verkleidungen oder Abdeckungen – im Innenbereich gesehen.
Das IGF-Vorhaben Nr. 19858 BG „Entwicklung nichtbrennbarer, faserverstärkter Kompositbauteile auf Basis kalthärtender, anorganischer Matrixsysteme und Ermittlung der Fertigungs-, Material- und Bauteileigenschaften“ der Forschungsvereinigung Schiffbau und Meerestechnik e.V. (FSM) wurde über die AiF im Rahmen des Programms zur Förderung der Industriellen Gemeinschaftsforschung (IGF) vom Bundesministerium für Wirtschaft und Energie aufgrund eines Beschlusses des Deutschen Bundestages gefördert.
Autor
Simon Backens
E-Mail: simon.backens@igp.fraunhofer.de
Tel.: +49 381 49682-24
Referenz
[1] Job, S.: 2015. Why not composites in ships? Reinforced Plastics 59, 2, 90–93.
[2] Davidovits, J.: 2017. Geopolymers: Ceramic-Like Inorganic Polymers. Journal of Ceramic Science and Technology, 8, 335–350.
[3] Vogt, O. ; Ukrainczyk, N. ; Koenders, E.: 2017. Geopolymere als Spezialbaustoff. Nachrichten aus der Chemie 65, 12, 1198–1202.
[4] Teschner, R.: 2013. Glasfasern. Springer-Verlag, Berlin, Heidelberg.
[5] Schürmann, H.: 2005. Konstruieren mit Faser-Kunststoff-Verbunden. VDI-Buch. Springer-Verlag, Berlin, Heidelberg.