Aufgrund der noch jungen Verfahren zur additiven Herstellung metallischer Bauteile gibt es entlang der additiv-subtraktiven Fertigungskette eine Menge Prozesserfahrung zu sammeln und Verständnis über die Wechselwirkungen aufzubauen. Im Rahmen des öffentlich geförderten Cornet/IGF-Forschungsvorhabens „Advanced Processing of Additively Manufactured Parts (Ad Proc Add)” (IGF-Fördernummer: EBG 255) beschäftigt sich das Institut für Spanende Fertigung (ISF) an der Technischen Universität Dortmund mit der Feinbearbeitung additiv hergestellter Bauteile und der wissenschaftlichen Analyse der Wechselwirkungen zwischen additiven Herstellverfahren und subtraktiver Bearbeitung mit geometrisch unbestimmter Schneide. Die Kooperation mit anderen internationalen Forschungseinrichtungen (IfW Universität Stuttgart, GFE Schmalkalden, IFT TU Wien, Fotec FH Wiener Neustadt, IWF ETH Zürich, Inspire AG ETH Zürich, Department of Mechanical Engineering KU Leuven, Thomas More University College) ermöglicht hierbei den Austausch unterschiedlicher Werkstücke aus verschiedenen Materialien und unterschiedlicher additiver Herstellverfahren. Neben der Betrachtung von verschiedenen metallischen Werkstoffen, wie Edelstahl (1.4404), Werkzeugstahl (1.2709), Aluminium (AlSi10Mg) und Baustahl (S355), kommen als additive Fertigungsverfahren das pulverbettbasierte Schmelzen von Metall mittels Laserstrahl (PBF-LB/M; engl.: Powder Bed Fusion – Laser Beam / Metal) sowie das Lichtbogen¬drahtauftragsschweißen (WAAM; engl.: Wire-Arc Additive Manufacturing) zum Einsatz.
Die Notwendigkeit der Nachbearbeitung der additiv gefertigten Bauteile ergibt sich bereits aus der Oberflächenrauheit, die aus der additiven Fertigung resultiert, und eine Abhängigkeit zur Orientierung der Fläche im Raum aufweist. Auf Basis des im Entwurf DIN EN ISO /ASTM 52902 vorgesehenen Testbauteils zur Erfassung der Oberflächenbeschaffenheit additiv gefertigter Bauteile lässt sich unabhängig vom Material festhalten, dass eine Nachbearbeitung der Bauteiloberflächen für funktionale Bauteilflächen unumgänglich ist. Die gemittelten Rautiefen liegen hier für die Gesamtheit der gemessenen Proben bei Werten von Rz= 20 bis 200 µm. Die große Spannweite der Messwerte lässt sich hierbei nicht ausschließlich auf die unterschiedlichen Werkstoffe zurückführen, da sowohl der niedrigste als auch der höchste Rz-Wert für den gleichen Werkstoff gemessen wurden. Allerdings wurden hierbei zum einen unterschiedliche Neigungswinkel der Oberfläche wie auch unterschiedliche Pulverbett-Schmelzanlagen betrachtet, womit auch die Prozessparameter variieren. Neben der Oberflächenbeschaffenheit zeigen weitere Testbauteile, dass auch aufgrund der auftretenden Maß- und Formabweichungen eine Nachbearbeitung für additiv erzeugte Bauteile mit Funktionsflächen unumgänglich ist.
Im Rahmen von experimentellen Untersuchungen wurden hierzu Versuche zum Schleifen, Nassstrahlspanen und Microfinishen durchgeführt, um die Wechselwirkungen entlang der additiv-subtraktiven Prozesskette zu erfassen und die Möglichkeiten zur Feinbearbeitung additiv hergestellter Bauteile zu untersuchen. Hierbei zeigten Untersuchungen zum Flachschleifen, dass die Aufbaurichtung des Werkstücks für die betrachteten Werkstoffe keinen Einfluss auf die Prozesskräfte und Prozessergebnisse hat. Detailanalysen von einzelnen gesammelten Schleifspänen deuten jedoch auf Veränderungen hinsichtlich der Spanbildung hin. Dies könnte für härtere Werkstoffe oder auch bei Betrachtung des Werkzeugverschleißverhaltens durchaus einen Einfluss der Aufbaurichtung auf den Prozess bedeuten. Darüber hinaus wurden beim Schleifen von Werkzeugstahl (1.2709) Poren offengelegt, die als Fehlstellen die Oberflächenqualität negativ beeinflussen. Verstärkt wurde die Offenlegung der Poren und Fehlstellen im Schichtaufbau durch Bearbeitung mittels Nassstrahlspanen. Für das Nassstrahlspanen wird auf Basis der Untersuchungen grundsätzlich empfohlen, eine Schleifbearbeitung vorzuschalten, da bei Bearbeitung der As-Built-Oberfläche neben Welligkeiten auch höhere Oberflächenrauheiten auftreten.
Da für rotationssymmetrische Oberflächen grundsätzlich andere Rahmenbedingungen gelten, wurden zusätzlich Zylinder-Bauteile additiv gefertigt und hinsichtlich der Wechselwirkungen mit spanenden Feinbearbeitungsverfahren untersucht. Aufgrund der Restriktionen, horizontal gelegene Rundkörper und Bohrungen additiv herzustellen, dies ist nur mittels Supportstrukturen möglich, wurde die Aufbauorientierung nur beiläufig betrachtet. Sofern entsprechende Supportstrukturen vorliegen, müssen diese abgetrennt werden, was an der Umfangsfläche eines Zylinders erheblichen Mehraufwand im Vergleich zur Stirnseite bedeutet. Eine geringe Neigung der Aufbaurichtung um 30° lässt sich noch ohne zusätzliche Supportstrukturen realisieren, weist jedoch keine Unterschiede in der anschließenden Spanenden Bearbeitung mittels Außenrundschleifen und Microfinishen auf.
Für die Feinbearbeitung mittels Microfinishen mit Band wurden unterschiedliche Kornwerkstoffe bei der Bearbeitung von Edelstahl (1.4404), Werkzeugstahl (1.2709) und Aluminiumlegierung (AlSi10Mg) gegenübergestellt. Während sich für Werkzeugstahl die Kornwerkstoffe Diamant (D) und Siliziumkarbid (SiC) als geeignete Schneidmittel herausstellten, eignet sich für Edelstahl SiC und für die Aluminiumlegierung Diamant. Aluminiumoxid (Al2O3), auch ein gängiger Schneidstoff beim Microfinishen mit Band, konnte für keinen der Werkstoffe vergleichbare Ergebnisse erzielet werden. Die über drei Prozessstufen mit sukzessive abnehmender Korngröße durchgeführte Microfinishbearbeitung ermöglichte den Abtrag der zuvor erzeugten Schleiftopographie und die Herstellung einer Plateauoberfläche mit sich kreuzenden Honriefen.
In der abschließenden Abbildung sind rasterelektronenmikroskopische Aufnahmen der additiv-subtraktiv erzeugten Oberflächen für Edelstahl Proben (1.4404) dargestellt. Die subtraktive Prozesskette beinhaltet hier das Nassstrahlspanen sowie Schleifen-Nassstrahlspanen für ein prismatisches Bauteil und Schleifen-Microfinishen für ein zylindrisches Bauteil. Das Institut für Spanende Fertigung möchte sich abschließend bei den beteiligten Forschungspartnern für die Kooperation und beim Industriekonsortium für das Interesse und die Unterstützung bedanken und freut sich auf zukünftige spannende und spanende gemeinsame Forschungsprojekte.
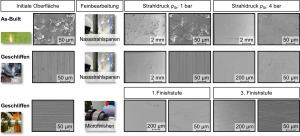
Abbildung 1: REM Aufnahmen additiv-subtraktiv erzeugter Oberflächen aus Edelstahl (1.4404)
Das Cornet/IGF-Vorhaben EBG 255/2 der Forschungsvereinigung VDW-Forschungsinstitut e.V. wurde über die AiF im Rahmen des Programms zur Förderung der Industriellen Gemeinschaftsforschung und -entwicklung (IGF) vom Bundesministerium für Wirtschaft und Technologie aufgrund eines Beschlusses des Deutschen Bundestages gefördert.
Autoren:
M. Tilger, D. Biermann
Institut für Spanende Fertigung (ISF), Technische Universität Dortmund