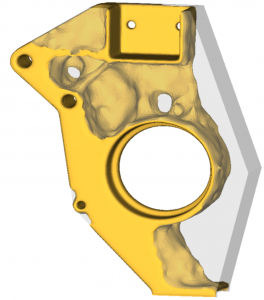
Abbildung 1: : Bauraum und Designvorschlag
Additive Fertigung und Topologieoptimierung versprechen eine nachhaltige und ressourcenschonende Realisierung und Fertigung hochkomplexer Bauteile, um dies zu erreichen müssen jedoch konstruktive, als auch verfahrenstechnische Aspekte beachtet werden. Der vorliegende Artikel beschäftigt sich mit dem Einfluss der Supportstrukturen auf Materialeffizienz und Dauer des Fertigungsprozesses.
Die additive Fertigung als realer Arm der Digitalisierung steht im Besonderen auch für einen ressourceneffizienten Produktionsprozess sowie für eine hohe Materialausnutzung. Entsprechend der möglichen geometrischen Gestaltungsfreiheiten verspricht sie beliebig komplexe Geometrien Near-Net-Shape fertigen zu können. In der Realität werden hierfür jedoch Supportstrukturen benötigt, um die gewünschte Form entsprechend abbilden zu können, bzw. eine Maßhaltigkeit während der Formgebung zu gewährleisten. Die Menge und Art der notwendigen Supportstrukturen unterscheiden sich hierbei nicht nur abhängig von der spezifischen Geometrie des Bauteils sowie deren Platzierung im Bauraum, sondern werden eben auch maßgeblich von dem eingesetzten Verfahren zur additiven Fertigung beeinflusst.
Das Verfahren bestimmt dabei hauptsächlich welche Funktion die Supportstrukturen erfüllen müssen, wobei hier zwischen grundsätzlich zwischen mechanischen und thermischen Supportstrukturen differenziert werden kann. Der erstgenannte Typ wird dabei bei allen Verfahren verwendet, welche keinen selbststützenden Aufbau der Geometrie ermöglichen, beispielsweise das Filamentablageverfahren (FDM, Fused Deposition Modelling) oder die Stereolithographie (SLA). Hier werden die Stützen benötigt, um zum einen den Aufbau der Struktur zu ermöglichen und zum anderen, Verzügen entgegen zu wirken. Allgemein werden sie dort benötigt, wo Strukturen zu dünn oder Überhänge zu groß werden, sich die Struktur also nicht mehr selbst stützen kann.
Die Pulverbettverfahren hingegen, denen etwa das Laserstrahlschmelzen als prominentester Vertreter zuzuordnen ist, sind aufgrund ihres Pulverresvervoirs selbststützend im Aufbau und können daher auf Supportstrukturen zur Bauteilabstützung verzichten. Jedoch erfolgt in diesem Prozess die Formgebung durch lokales Aufschmelzen des Metallpulvers mit einem oder mehreren Lasern. Entsprechend hoch ist der Energieeintrag in die Strukturen und entsprechend essentiell ist ein ausreichend hoher Wärmetransport notwendig, um die Energie aus dem Bauteil abzuleiten und damit thermische Verzüge und hohe Eigenspannungen zu vermeiden.
Bedingt durch die neue Art der Fertigungsrestriktionen wie auch der Fertigungsmöglichkeiten unterscheidet sich die Gestaltung von Bauteilen für die additive Fertigung stark von den konventionellen Methoden. Ansätze für geeignete Strategien werden dabei unter dem Begriff Design for Additive Manufacturing (DfAM) zusammengetragen. Beispielsweise gibt die VDI-Norm 3405 Konstruktionsrichtlinien als Unterstützung für den Produktentwickler.
Neben diesen verfahrenstechnischen Aspekten ist ebenso das Bauraum-Layout maßgeblich für die Menge der benötigten Supportstrukturen verantwortlich. Liegt der Fokus auf einer möglichst hohen Ausnutzung des Bauraums, so ergeben sich für den Druckjob andere Restriktionen, als dies im Rapid Prototyping für einzelne Stückzahlen der Fall ist. So ergibt sich potentiell der Optimierungskonflikt aus Bauraum- und Materialausnutzung.
Nichtsdestotrotz besteht der große Mehrwert der additiven Fertigung darin, sich sehr nahe an mathematisch optimale Designlösungen annähern zu können. Hier zeigt sich besonders im Bezug auf die Umsetzung von Leichtbaustrategien die Verknüpfung aus additiver Fertigung und Topologieoptimierung als vielversprechend. Die Topologieoptimierung beschreibt dabei die ideale Verteilung von Material innerhalb eines vorher definierten Bauraums (Abb.1) unter Berücksichtigung von äußeren Lasten und Randbedingungen.
Beispielsweise kann die Steifigkeit bei einem definierten Zielvolumen für den vorgesehenen Lastfall maximiert werden. Das Ergebnis solcher Optimierungen sind allgemein Designvorschläge und daher nicht als finale Produkte zu betrachten. Das ist auch darin begründet, dass sich die Vorschläge kaum oder nur mit sehr hohem Aufwand über konventionelle Fertigungsmethoden herstellen lassen. Mithilfe der additiven Fertigung besteht nun die Möglichkeit deutlich näher an diesen theoretischen Optima zu bleiben und damit Leichtbaustrategien bzw. Materialeinsparung effizienter umzusetzen.
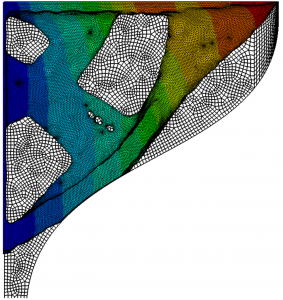
Abbildung 2: Designraum und Topologieoptimierter
Designvorschlag
Im nachfolgenden Beispiel wird die Steifigkeit eines Regalhalters bei 50 % Zielvolumen optimiert (Abb.2). Für die Topologieoptimierung wird die am Lehrstuhl für Konstruktionslehre und CAD entwickelte Freeware Z88Arion® eingesetzt. Der optimierte Designvorschlag ist in Abb. 2 dargestellt. Es ist deutlich zu sehen, dass diese Geometrie nicht für konventionelle formative oder subtraktive Verfahren geeignet ist und daher die Additive Fertigung das Produktionsverfahren der Wahl ist. Das Ergebnis liefert nun einen Vorschlag, um bei gleicher Steifigkeit die Hälfte des Materials einzusparen, idealerweise nicht nur im Endprodukt, sondern bereits auch in der Fertigung.
Entsprechend ist es nur wenig sinnvoll von nachhaltiger Produktentwicklung zu sprechen, wenn zwar im finalen Produkt Material eingespart wird, dies aber fertigungsbedingt als Ausschuss anfällt. Daher besteht die Aufgabe darin, das gewählte Bauteil so zu fertigen, dass möglichst wenig Stützstrukturen entfernt werden müssen und natürlich auch im Sinne des Rapid Manufacturing die Herstellungszeit möglichst gering ist.
Im vorliegenden Fall wurden drei Konfigurationen zur Bauteilorientierung exemplarisch untersucht und der Anteil der Stützstrukturen am Gesamtmaterialverbrauch, sowie die Druckzeit und Materialeinsparung im Vergleich zum initialen Bauraum ausgewertet, die Ergebnisse sind in Tab. 1 zusammengefasst.
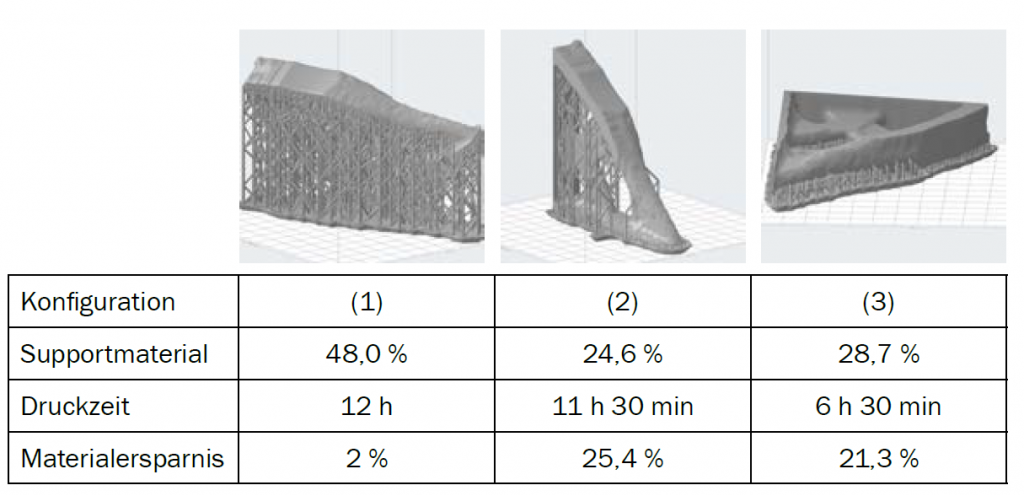
Tabelle 1: Optimierter Regalhalter mit drei verschiedenen Stützstruktur Konfigurationen.
Es ist deutlich zu erkennen, dass die Orientierung innerhalb des Bauraums maßgeblichen Einfluss auf die Anzahl der benötigten Stützen aufweist. Dies liegt daran, dass Strukturen mit Überhängen von mehr als 45°, siehe Abb 3., gestützt werden müssen und entsprechend je nach Orientierungswinkel dieser Anteil stark variieren kann.
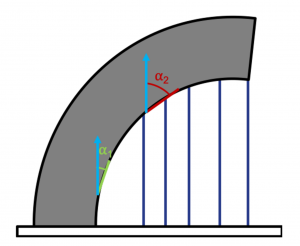
Abbildung 3: Stützstrukturen in Abhängigkeit
des Überhangwinkels
Die Druckzeit skaliert nicht linear mit dem Volumen des benötigten Materials, sondern ist vielmehr abhängig von der Anzahl der benötigten Schichten, also der maximalen Länge in Aufbaurichtung des Bauteils. Dies lässt sich gut im Vergleich der Konfigurationen (2) und (3) in Tab.1 veranschaulichen. An dieser Stelle ist es nun wichtig zu verstehen, dass der Herstellungsprozess additiver Bauteile nicht nach dem Druckvorgang endet, sondern, wie bei allen anderen Produktionsverfahren auch, die Nachbearbeitung einen wichtigen Prozessschritt darstellt. Im konkreten Fall beinhaltet dieser das Entfernen der Supportstrukturen, sowie das Schleifen und Polieren von Funktionsflächen. Aufgrund der geometrischen Komplexität stellt dies bisweilen einen äußerst zeitaufwändigen Prozess dar. Nachdem nun Funktionsflächen in der Regel ohnehin nachbearbeitet werden müssen, bietet es sich also an, die Stützstrukturen an diesen Flächen auszurichten.
So zeigt sich, dass bei Minimierung der Schichtanzahl zwar ebenso die Druckzeit minimiert wird, dabei aber der Aufwand für die benötigte Nacharbeit deutlich erhöht wird, es ist hier demnach im Einzelfall abzuwägen, welche Konfiguration geeigneter ist. Unter dem Aspekt einer möglichst hohen Packungsdichte des Bauraums, ist dabei ohne Frage Konfiguration (2) deutlich besser geeignet.
Im Hinblick auf die tatsächliche Materialersparnis im Prozess zeigt sich, dass unter Umständen lediglich 2 % Material eingespart werden können. Im Fall der beiden weiteren Konfigurationen kann diese zwar deutlich verbessert werden, jedoch muss auch hier etwa die Hälfte des eingesparten Volumens für notwendige Stützstrukturen eingeplant werden. Wodurch in Summe die Materialausnutzung des Prozesses bei etwa 75 % liegt.
Entsprechend ist es für eine effiziente und ressourcenorientierte Nutzung der Additiven Fertigung notwendig zum einen die Druckzeit zu minimieren und zum anderen gleichzeitig den Anteil der Supportstrukturen verfahrenstechnisch, wie auch konstruktiv, gering zu halten. Daher forscht der Lehrstuhl Konstruktionslehre und CAD unter anderem im Forschungsprojekt OptiOnEn (Optimale One Click Entwicklung) an der Berücksichtigung von Fertigungsrestriktionen in der Topologieoptimierung, um damit einen wichtigen Beitrag im Rahmen eine zukunftsorientierte, ressourcenschonende Produktentwicklung zu leisten.
Dieser Beitrag entstand im Kontext des Forschungsvorhabens OptiOnEn, gefördert durch den Europäischen Fond für Regionale Entwicklung (EFRE) und die Oberfrankenstiftung
Autor*innen
Tobias Rosnitschek, Bettina Alber-Laukant, Frank Rieg
Lehrstuhl für Konstruktionslehre und CAD,
Universität Bayreuth,
Universitätsstraße 30,
95447 Bayreuth
tobias.rosnitschek@uni-bayreuth.de