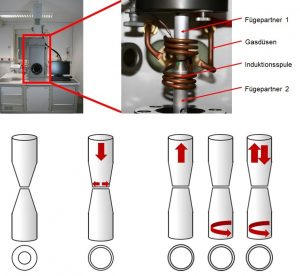
Abbildung 1: Aufbau des Grundversuchs zur Charakterisierung der Verbindung beim Walzplattieren (oben) ([Autoren] nach [Mik14]) und schematische Versuchsdurchführung (unten)
Stoffschlüssiges Verbinden durch Walzplattieren
Die hohen Anforderungen an moderne Bauteile, zum Beispiel im Bereich des Leichtbaus und der Energieeffizienz, können immer seltener durch monolithische Werkstoffe erfüllt werden. Hier greift das Walzplattieren als ein etabliertes Verfahren für das stoffschlüssige Verbinden verschiedener metallischer Werkstoffe an. Dies ermöglicht anwendungsgerechte Kombinationen physikalischer, chemischer oder mechanischer Werkstoffeigenschaften. In der Praxis werden allerdings Prozessgrenzen in Bezug auf kombinierbare Werkstoffe und realisierbare Schichtdickenverhältnisse beobachtet. So können stark unterschiedliche Festigkeiten der Verbundpartner oder ungünstige Schichtdickenverhältnisse zu stark unterschiedlicher Längung führen. Somit wird eine Verbindungsentstehung erschwert oder verhindert und es kann zu periodischem Aufreißen der schwächeren Schicht kommen. Um diese Zusammenhänge systematisch untersuchen und besser verstehen zu können, wurden am IBF realitätsnahe Simulationsmodelle und ein Grundversuch entwickelt, mit dem die Entstehung der stoffschlüssigen Verbindung entsprechend den Bedingungen im Walzspalt quantitativ nachvollzogen werden kann.
Verbindungsentstehung beim Walzplattieren
Sowohl beim Kaltwalzplattieren als auch beim Warmwalzplattieren werden die Verbundpartner zwischen konventionellen Flachwalzen gewalzt. Dies führt sowohl zu hohen Drucknormalspannungen als auch zu einer Oberflächenvergrößerung in der Kontaktfuge. Entsprechend der Modellvorstellung von Zhang und Bay [Zha97] führt die Oberflächenvergrößerung zu einem Aufreißen der Deck- und Oxidschichten, sodass die Druckspannung die neuen, rein metallischen, Oberflächen in direkten Kontakt bringen kann. Dies führt zur Entstehung der stoffschlüssigen Verbindung. Diese erste Verbindung kann durch weiteres Auswalzen und durch Diffusion, sei es zwischen den Walzstichen beim Warmwalzplattieren oder durch eine anschließende Glühung beim Kaltwalzplattieren, verstärkt werden.
Grundversuch zur Verbindungsentstehung
Entsprechend der beschriebenen Modellvorstellung sind die wichtigsten Einflussgrößen auf die Verbindungsentstehung der Oberflächenzustand, die Temperatur der Verbundpartner, die durch das Walzen erzeugte Oberflächenvergrößerung und die Kontaktspannungen einschließlich eventueller tangentialer Verschiebungen der Fügepartner. Darüber hinaus wird in der Praxis beobachtet, dass die gerade entstandene Verbindung bereits am Walzspaltaustritt wieder aufreißen kann.
Daher muss der Grundversuch in der Lage sein, sowohl die Verbindungsentstehung als auch -trennung unter walztypischen Belastungen abzubilden. Dies ermöglicht der in einem Torsionsplastometer realisierte Versuchsaufbau (Abbildung 1, oben). Hier werden zwei in der Verbindungszone konisch zulaufende Proben unter Druck oder Überlagerung von Druck und Torsion miteinander verbunden. Anschließend werden sie unter verschiedenen Spannungszuständen auf ihre Verbindungsfestigkeit geprüft (Abbildung 1, unten).
So kann die Festigkeit des Verbundes für eine Vielzahl von Materialkombinationen und Oberflächenzuständen in Abhängigkeit der Prozessbedingungen (Temperatur, Oberflächenvergrößerung, Kontaktdruck, etc.) und der Art der Belastung quantitativ ermittelt werden.
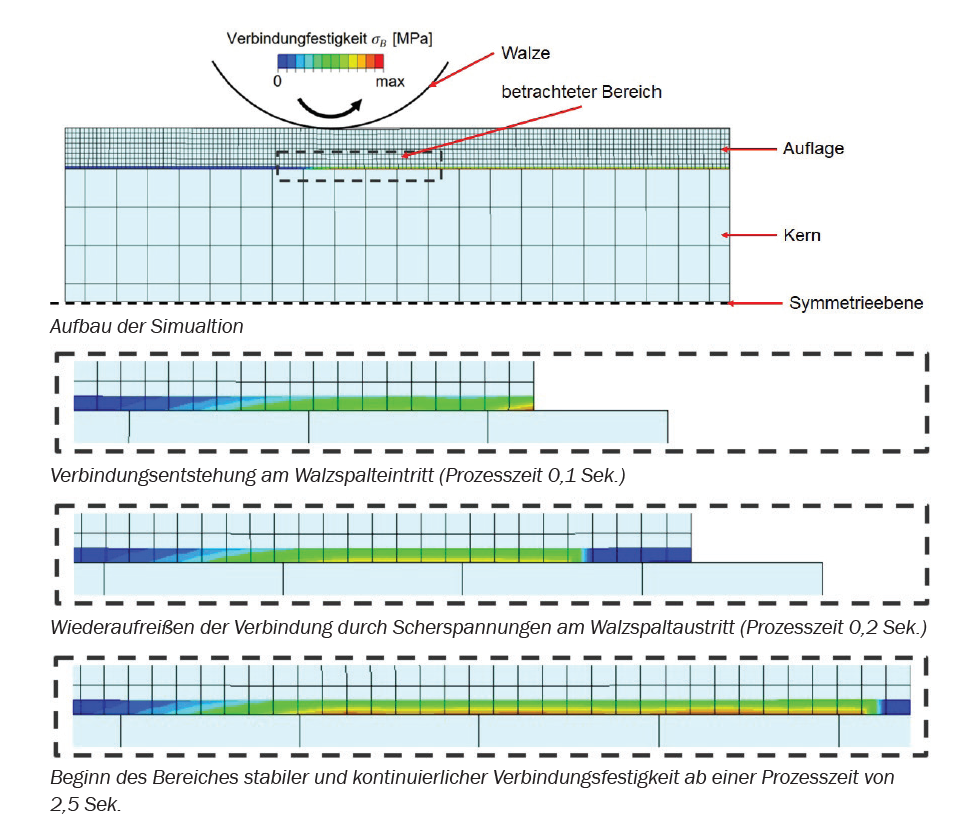
Abbildung 2: Beispiel einer Simulation der Verbindungsentstehung mittels einer geeigneten Subroutine
Simulation des Walzplattierens
Die aus dem Grundversuch ermittelten Kennwerte werden über eine geeignete Subroutine zur Simulation des Walzplattierens mit der FE-Simulationssoftware Abaqus genutzt. Damit kann die Verbindungsentwicklung während des Walzspaltdurchgangs inklusive Temperaturverlauf simuliert werden.
Beispielhaft zeigt Abbildung 2, dass die Verbindung unter den vorliegenden Bedingungen am Kopf der Bramme zunächst wieder aufreißt bevor sich dann eine kontinuierliche Verbindung einstellt.
Unterschiede in der Längung der Schichten
Zwei wesentliche Einflussgrößen, die die Längung der einzelnen Schichten beeinflussen, sind zu erwarten:
a) Es ist anzunehmen, dass bei gleichen Schichtdicken der weichere Partner stärker längt.
b) Es ist anzunehmen, dass das Verhältnis der jeweiligen Schichtdicke zur „gedrückten Länge“ – der Kontaktlänge zwischen Walze und Plattierpaket, die abhängig von Höhenabnahme und Walzenradius ist – wesentlich ist, da die gedrückte Länge auch vorgibt, wie tief die plastische Zone in Dickenrichtung ausgeprägt ist.
Es konnte am Beispiel des Warmwalzplattierens von Aluminiumbarren aus Reinaluminium (AA1050) und einer höherfesten Legierung (AA2024) in Simulation und Experiment gezeigt werden, dass die Längungsunterschiede durch eine Angleichung der Fließspannung beider Partner deutlich reduziert werden konnten [Mel14]. Diese Plattierung wird heute u.a. in der Luft- und Raumfahrt verwendet, wobei eine sehr dünne Schicht des AA1050 als Korrosionsschutz zur Umgebung dient. Die Angleichung der Fließspannung erfolgte durch eine gezielte Abkühlung der weicheren Schicht nach Entnahme des am Brammenkopf verbundene Pakets aus dem Ofen. Allerdings zeigten die für Dickenverhältnisse bis etwa 1:5 durchgeführten Untersuchungen auch, dass nur bei identischen Dicken beider Schichten und zugleich in etwa gleicher Fließspannung überhaupt kein Längenunterschied mehr auftritt.
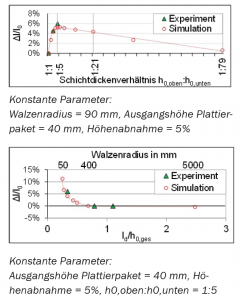
Abbildung 3: Graphische Darstellung der Simulationsergebnisse zum Einfluss des Schichtdickenverhältnisses h0,unten:h0,oben (oben) und der gedrückten Länge ld (unten) auf die Längungsunterschiede zwischen zwei Schichten identischer Fließspannung ([Autoren] nach [Mel17]
Es zeigte sich, dass die Erhöhung des Schichtdickenverhältnisses h0,oben:h0,unten nach dem Durchlaufen eines Maximums zu einer Verringerung der Längungsunterschiede führt. Ebenso verringerten sich die Längungsunterschiede mit zunehmender gedrückter Länge ld (Abb. 4) [Mel17].
In einem weiterführenden Projekt werden diese Erkenntnisse aktuell auf das Kaltwalzplattieren dünner Bänder vom Coil übertragen. Beispielhaft hierfür wird die Materialpaarung aus härterem Reinnickel (Ni99,2) und dem weicheren AA1050 untersucht. Diese Kombination ist für eine potentielle Anwendung im Bereich des Batteriegehäusebaus geeignet. Ni99,2 wird als Schutz vor der Batteriesäure und AA1050 als preisgünstigere Leichtbaukomponente eingesetzt. Hierbei soll die Angleichung der Fließspannung durch konduktive Durchlauferwärmung des festeren Ni99,2 vor dem Walzspalt erfolgen.
33. ASK Umformtechnik
Weitere Informationen zum Walzplattieren und einen inspirierenden Rahmen für intensiven Erfahrungsaustausch zu diesem und anderen Themen der Umformtechnik bietet das 33. ASK Umformtechnik vom 28.-29. März 2019 unter dem Motto „Ideen Form geben“ im Eurogress in Aachen.
Neben den herausragenden Plenarvorträgen werden ausgewählte Themenbereiche der Entwicklung umformtechnischer Prozesse, Maschinen, Produkte und Simulationsmethoden für Stahl und NE-Metalle in parallelen Gruppen und im Messeforum vertieft behandelt.
Referenzen
[Mel14] Melzner, Alina; Hirt,G.: Roll Bonding ot two materials using temperature to compansate the material strength difference. Advanced Materials Research, 966-967, 2014, 471-480
[Mel17] Melzner, A.; Hirt, G.: Investigation on the Elongation Differences of Aluminum in Two Layer Roll Bonding. Esaform Tagungsband, 2017
[Mik14] Mikoweit, A.; Bambach, M.; Pietryga, M.; Hirt, G.: Development of a testing procedure to determine the bond strength in joining-by-joining processes. Advanced Material Research, Vol. 966-967, 2014, S. 481-488
[Zha97] Zhang, W.; Bay,N.: Cold Welding Theoretical Modeling of the Weld Formation. Welding Journal Supplement, 10, 1997, S. 417-430
Autoren:
Paul Simon, Alina Melzner und Gerhard Hirt, Institut für Bildsame Formgebung, RWTH Aachen University