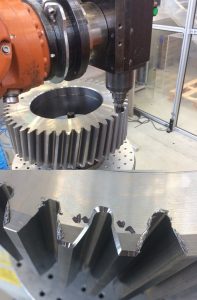
Abbildung 1: Zahnradbearbeitung mit Industrieroboter
Einleitung
Industrieroboter sind dank ihrer Flexibilität und daraus resultierenden vielseitigen Einsetzbarkeit fester Bestandteil im industriellen Umfeld. Dies gilt sowohl für den Bereich der Handhabung, als auch zunehmend für Fertigungsaufgaben. Besonders aus wirtschaftlichen Gesichtspunkten ist der Einsatz von Industrierobotern in der Fertigung interessant. Zum einen weisen Industrieroboter einen großen Bearbeitungsraum im Vergleich zur Aufstellfläche auf. Zum anderen sind die Investitionskosten und somit auch die erzielbaren Maschinenstundensätze geringer, als die einer Werkzeugmaschine [1]. Weiterhin können Robotersysteme problemlos mit externer Sensorik ausgestattet werden und somit zu digital integrierten Bearbeitungssystemen werden. Roboter werden in zunehmendem Maße für maschinelle Bearbeitungen eingesetzt, die bisher Werkzeugmaschinen oder auch speziellen Bearbeitungsmaschinen vorbehalten waren. So liegt beispielsweise großes Potenzial in der Automatisierung bisher manuell durchgeführter Bearbeitungsprozesse, wie zum Beispiel dem Entgraten und Schleifen [2].
Anwendungsfelder
Das Entgraten von Bauteilen ist ein Prozessschritt, der in einer Vielzahl von Industriezweigen nach wie vor manuell umgesetzt wird. Vor allem bei kleinen Losgrößen, ständig wechselnden Bauteilen oder starken geometrischen Abweichungen zwischen den Bauteilen ist eine automatisierte Lösung zur Kantenbearbeitung bisher schwer umsetzbar.
Mit den Genauigkeitsanforderungen von 0,2 bis 0,5 mm stellt die Gussindustrie einen wichtigen Markt für die Roboterzerspanung dar [3]. Der Anteil von Entgrat- und Fräsprozessen und die dafür benötigte Zeit sind in der Gussindustrie hoch. Primär- und Sekundärgrate sowie auch Anguss und Steiger von Rohgussteilen lassen sich mit Hilfe von robotergeführten Werkzeugen wirtschaftlich entfernen. Produkte, wie beispielsweise Getriebegehäuse und Motorblöcke, lassen sich durch den Einsatz von IR sehr viel wirtschaftlicher bearbeiten als es manuell möglich wäre [4]. Weitere Anwendungsfelder sind z. B. Bauteile aus Tiefziehprozessen oder Zahnräder.
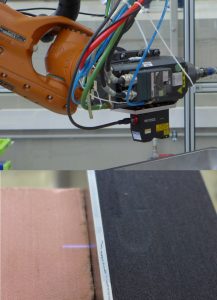
Abbildung 2: Bahnkorrektur für Kantenbearbeitung durch Linienlaser
Herausforderungen
Trotz der Fortschritte seit den ersten Forschungsvorhaben in den 1990er Jahren, bestehen nach wie vor zwei Hauptprobleme bei der spanenden Bearbeitung mit IR. Zum einen führt ihre geringe Steifigkeit – 1 N/μm im Vergleich zu mehr als 50 N/μm bei Werkzeugmaschinen [5] – zu einer statischen Abdrängung des Werkzeugs von der einprogrammierten Sollbahn und dadurch zu einer verringerten Maßhaltigkeit des Bauteils. Zum anderen treten Werkzeug- und Maschinenschwingungen auf die sich nicht nur negativ auf die Oberflächenqualität, sondern auch auf das Verschleißverhalten des Werkzeugs und die Lebensdauer des Maschinensystems auswirken können. Neben der geringen Steifigkeit und den Maschinenschwingungen sind vor allem die Roboterprogrammierung, die Aufspannung und die Bauteiltoleranzen Hürden für die Umsetzung automatisierter Kantenbearbeitungen mit einem Industrieroboter. Die Programmierung des Robotersystems ist nach wie vor eine der größten Hürden bei der Erschließung neuer Anwendungsfelder. Oftmals schrecken die Anwender vor der ihnen unbekannten Programmierung zurück oder rechnen mit enormen Mehraufwand für Schulung und Weiterbildung der Mitarbeiter. Ein selbstlernendes und anpassungsfähiges System könnte diese Barriere durchbrechen. Auch sind Bauteiltoleranzen eine nicht zu vernachlässigende Herausforderung. Schwanken die geometrischen Abweichungen der zu entgratenden Bauteile, kommt es bei einer fest programmierten Bearbeitungsbahn zu Bearbeitungsfehlern und somit zu fehlerhaften Bauteilen. Für eine automatisierte Lösung muss das System demnach die Abweichungen selbstständig kompensieren und eine gleichbleibende Bauteilqualität liefern.
Zahnradbearbeitung
Bei der Herstellung von Zahnrädern müssen im Anschluss an die Fräsbearbeitung oft Grate entfernt und die Kanten durch eine definierte Fase gebrochen werden. Dies wird derzeit ausschließlich manuell durchgeführt. Dabei kommen verschiedene Fräs-, Schleif-, Bürst- und Polierwerkzeuge zum Einsatz. In der Industrie besteht der Bedarf, häufig wiederkehrende Entgrat- und Anfasoperationen mit hoher Prozesssicherheit maschinell durchzuführen. Ziel ist es, Kosten für manuelle Nacharbeitung zu senken, die Reproduzierbarkeit von Arbeitsergebnissen zu erhöhen sowie die Bearbeitungsdauer möglichst zu reduzieren.
Am Fraunhofer IPK wurde eine automatisierte Kantenbearbeitung für Zahnräder erprobt und umgesetzt. Ziel war eine möglichst einfache Programmerstellung ohne tiefgreifende Programmierkenntnisse des Robotersystems. Für die Programmerstellung wurden die Konturzug-Koordinaten (Stirnschnitt) in eine Matlab-Umgebung geladen. Anschließend erstellt diese Umgebung basierend auf den übergebenen Daten ein Bearbeitungsprogramm. Für eine automatisierte Bearbeitung benötigt das Programm lediglich den Durchmesser des Zahnrades. Anschließend wird der zu bearbeitende Zahn voll automatisch über eine Mittelung eingemessen und das Bearbeitungsprogramm startet. Durch eine externe Drehachse können die übrigen Zähne durch eine Taktung bearbeitet werden.
Tiefziehbauteile
Bauteile aus Tiefziehprozessen weisen prozessbedingte Bauteiltoleranzen auf. Diese Abweichungen stellen an nachfolgende automatisierte Prozesse hohe Anforderungen. Eine automatisierte Bearbeitung mit definierten Kanten muss auf die veränderten geometrischen Bedingungen reagieren können. Bei geringen Abweichungen ist der Einsatz von nachgiebigen Spindeln eine gängige Lösung. Jedoch treten nicht selten ungewünschte Fräsmarken auf. Für den Einsatz von starren Spindeln muss das Bearbeitungsprogramm auf sich verändernde Bauteile reagieren und die Bearbeitungsbahn anpassen. Für diesen Zweck kann das Robotersystem mit einem externen Sensor ausgestattet werden. Am Fraunhofer IPK wurde das System um einen Linienlaser an der Spindel erweitert und das Bearbeitungsprogramm zweigeteilt. In einem ersten Programmdurchlauf wird die Bauteilkante durch den Linienlaser vermessen und die Abweichung zum originalen Bearbeitungsprogramm an jedem einzelnen Bahnpunkt ermittelt. Im weiteren Verlauf werden alle Bahnpunkte automatisiert korrigiert und somit das Bearbeitungsprogramm an die geometrischen Abweichungen des Bauteils angepasst. Anschließend kann das aktualisierte Programm gestartet und das Bauteil bearbeitet werden. Durch diese Kompensationsvariante können auch große Bauteiltoleranzen automatisiert ausgeglichen werden, ohne das eine ständige manuelle Änderung der Bearbeitungsprogramme notwendig ist. Somit ist der Programmieraufwand sehr gering und das System reagiert eigenständig und automatisch auf sich ändernde Bauteilabmessungen.
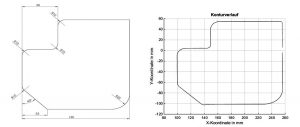
Abbildung 3: Vergleich Originalkontur und Positionsdaten
Kraft-Momenten-Regelung
Auf Basis vorhandener Kraft-Momenten-Sensoren kann der Roboter eine gewisse Intelligenz erlangen und mit Hilfe der richtigen Programmierung Bearbeitungsprogramme selbstständig erstellen. Das Fraunhofer IPK arbeitet aus diesem Grund an einer intuitiven Programmierumgebungen und selbstlernenden Systemen zur automatischen Kantenbearbeitung. Mit Hilfe der Kraft-Momenten-Steuerung wurden zwei verschiedene Systeme für die automatisierte Bahngenerierung umgesetzte. In der ersten Variante wird das Robotersystem von dem Bediener manuell an das Bauteil geführt und die Bauteilkante mit dem Messwerkzeug abgefahren. Der Bediener hält den Roboter dabei z. B. an der Spindel oder dem Werkzeughalter und führt das System mittels Muskelkraft. Dabei werden die Positionsdaten aufgenommen und von etwaigen Störquellen, wie Rauschen oder niederfrequenten Schwingungen, durch Linearisierung bereinigt. Anschließend erfolgt eine Radiuskorrektur der Messdaten. Diese ist nötig, um mit nur einem Messtaster Werkzeuge mit verschiedenen Radien verwenden zu können. Die Differenz der Positionsdaten der Ist-Kontur weichen hierbei aktuell maximal um 0,1 mm von der numerisch verarbeiteten Kontur ab. Aus den aufgenommenen Positionsdaten wird vollautomatisch ein Bearbeitungsprogramm erstellt. Hierfür müssen lediglich die gewünschten Werkzeugdaten und Vorschübe eingetragen werden.
Da die manuelle Führung des Robotersystems keine vollautomatisierte Lösung bietet und der Benutzer eine potentielle Fehlerquelle darstellt, wurde die bestehende Lösung weiterentwickelt. Die Handführung wurde durch eine Selbststeuerung des Systems ersetzt. Der Roboter fährt die Messspitze selbstständig an einen Startpunkt und anschließend in eine definierte Richtung. Mit Erreichen der Bauteilkante wirkt eine Kraft auf die Messspitze. Übersteigt die Kraft ein Maximum, weicht das System in eine definierte Richtung aus und hält gleichzeitig eine definierte Kraft aufrecht. Durch diese Regelung folgt der Roboter der Bauteilkante automatisch. Gleichzeitig können die Positionsdaten aufgezeichnet und anschließend in ein Bearbeitungsprogramm überführt werden. Im Moment funktioniert diese Programmerstellung bei 2D Konturen. Eine Überführung auf 2,5D und 3D ist derzeit in der Erprobung.
Zusammenfassung
Robotersysteme sind durch ihre Flexibilität, den großen Arbeitsraum und den vergleichsweise geringen Anschaffungskosten prädestiniert für die Überführung manueller in automatisierte Prozesse. Jedoch bestehen nach wie vor eine Vielzahl von Herausforderungen aber auch Vorurteile gegenüber der Technik. Die Forschung stellt sich diesen Herausforderungen und kann dabei eine Vielzahl an Lösungen und Konzepten anbieten. So brauchen zukünftige Anwender nicht mehr vor der komplexen Programmierumgebung erschrecken und weiterhin auf manuelle Prozesse setzen. Roboteranwender erkennen diesen Trend und bieten alternative Steuerungskonzepte mit bekannten Oberflächen und Befehlen an. Zusätzlich bietet die Sensorik eine Vielzahl an Möglichkeiten von alternativen Steuerungskonzepten bis hin zu selbstlernenden Systemen. So wird der Programmieraufwand verringert oder entfällt ganz.
Die Bearbeitung von Bauteilen mit großen Toleranzen und geometrischen Abweichungen ist ebenfalls kein Ausschlusskriterium für eine automatisierte Bearbeitung. Optische Sensoren, Lasertechnik oder Kraft-Momenten-Regelung erlauben die Reaktion auf Veränderungen in der Bauteilgeometrie. Gleichzeitig bieten diese Lösungen eine automatisierte Anpassung der Bearbeitungsprogramme. Ein Eingreifen der Benutzer oder sogar eine ständige Anpassung der Programme ist somit nicht mehr notwendig.
Die entwickelten Zusatztools des Fraunhofer IPK helfen zwar, die Leistungsfähigkeit zu steigern, aber sie ermöglichen noch keine generelle Qualifizierung der Industrieroboter für die Bearbeitung. Industrieroboter können vor allem die manuellen Prozesse und Portalfräsmaschinen bei der Bearbeitung von großflächigen Strukturen substituieren. Die Fraunhofer-Institute IPK, IFAM und LBF haben sich dieses Anwendungsgebietes angenommen, eine neue serielle Fräskinematik mit dem Namen „Flexmatik 4.1“ zu entwickeln. Aktuell befindet sich das System im Aufbau und soll Ende 2019 fertiggestellt sein. Die Flexmatik wird sich maßgeblich von aktuellen Industrierobotern unterscheiden, um den hohen Anforderungen der Zerspanung gerecht zu werden. Dafür wird der Einsatz von Direktantrieben, topologieoptimierten Strukturbauteilen, einer Temperaturkompensation, einer adaptiven Schwingungsregelung, innovativer Sensoriken und einer G-Code-basierten Steuerung umgesetzt.
Autoren:
M. Sc. Christian Mohnke,
Dr.-Ing. Sascha Reinkober
Fraunhofer-Institut für Produktionsanlagen und Konstruktionstechnik IPK
Pascalstr. 8-9, D-10587 Berlin
Tel. +49 (0)30 / 39006-354
Fax +49 (0)30 / 391-1037
E-Mail: christian.mohnke@ipk.fraunhofer.de
Internet: www.ipk.fraunhofer.de
Literatur
[1] Uhlmann, E.; Reinkober, S.; Mohnke, C.: Individuelle Fertigung durch den Einsatz von Industrierobotern. wtWerkstattstechnik online 106 (2016), H. 7/8.
[2] Schreck, G.; Manthei, M.: Roboter statt Werkzeugmaschine. Fraunhofer IPK Kundenmagazin FUTUR 02, 2012, S. 8 – 9.
[3] Weigold, M.: Kompensation der Werkzeugabdrängung bei der spanenden Bearbeitung mit Industrierobotern. Diss., Technische Universität Darmstadt, Aachen: Shaker, 2008.
[4] Dipl. Ing Laempe GmbH: „Humaner“, flinker Kostensenker. Rationalisierung durch roboterbestückte Gussputzzelle. Fachzeitschrift Maschine + Werkzeug Heft 6 (2006), S.35 – 39.
[5] Wang, J.; Zhang, H.; Pan, Z.: Machining with flexible manipulators: critical issues and solutions. In: Huat, L.K. (Hrsg.): Industrial Robotics: Programming, Simulation and Applications. Augsburg: Pro Literatur, 2006, S. 515–536