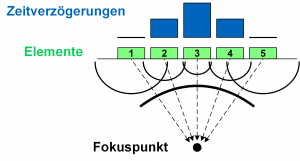
Abbildung 1: Beispiel einer fokussierten Wellenfront mit einem Phased-Array-Prüfkopf
Einleitung
Die weltweite Nachfrage nach kohlenstofffaserverstärkten Kunststoffen (CFK) wird, aktuellen Marktprognosen zur Folge, auch in den nächsten Jahren weiter deutlich ansteigen. Vor allem die hohen gewichtsspezifischen Festigkeits- und Steifigkeitseigenschaften dieser Materialien übertreffen die mechanischen Kennwerte vieler traditioneller Werkstoffe um ein Vielfaches. Deshalb sind CFK-Laminate besonders attraktiv für verschiedenste Leichtbauanwendungen in der Luft- und Raumfahrtindustrie, im Automobilbereich und zunehmend auch im Energiesektor.
Zwangsläufig entstehen während der Produktion oder im Betrieb von Faserverbundstrukturen Fehlstellen, wie Delaminationen, Porosität, Faserondulationen und Schäden, die z. B. durch Vogel- oder Blitzschlag verursacht werden. Wird hierdurch die Materialfestigkeit auf ein unzulässiges Maß reduziert, so kann dies unter Umständen zu einem katastrophalen Bauteilversagen führen. Es ist deswegen erforderlich, zuverlässige zerstörungsfreie Prüfverfahren (ZfP) zur Qualitätssicherung von sicherheitskritischen Strukturen einzusetzen. Die große Herausforderung, vor der Anwender dabei oft stehen, ist die Auswahl einer oder oft auch mehrerer ZfP-Techniken, um eine bestimmte Prüfaufgabe zielführend zu lösen. Insbesondere bildgebende Verfahren, die in der Lage sind, auch kleinste Fehlstellen in CFK schnell zu detektieren, gewinnen dabei zunehmend an Bedeutung. So werden neben der Ultraschallprüfung häufig auch thermografische oder radiographische Methoden (wie z. B. die Computertomografie) eingesetzt. In zwei früheren Artikeln in dieser Zeitschrift (Ausgaben 01/2017; S. 16 f. und 02/2017; S. 30 ff.) wurde bereits ein Überblick über verschiedene ZfP-Verfahren zur CFK-Prüfung gegeben und deren effizienter Einsatz im Produktionsprozess erörtert. Der hier vorliegende Beitrag konzentriert sich auf einen Teilaspekt davon – auf moderne Ultraschall-Rekonstruktionsverfahren.
Ultraschallprüfung
Die Ultraschallprüfung ist ein etabliertes und effektives Prüfverfahren, um Faserverbundwerkstoffe zu testen. Viele besonders relevante und festigkeitsmindernde Fehlstellen, wie Impactschäden oder unzulässig hohe Porositätsgrade lassen sich zuverlässig detektieren aber auch weiterführend charakterisieren (siehe z. B. Ausgabe 02/2018; S. 22 f.). So kann zum Beispiel die Tiefenlage und die Größe einer Delamination sehr gut quantifiziert werden.
CFK-Laminate stellen jedoch eine große Herausforderung für die Ultraschallprüfung dar. Die inhärente Heterogenität dieser Materialien verursacht Gefügerauschen in den Ultraschallsignalen wodurch die Nachweisgrenze für kleine Fehlstellen verschlechtert wird. Ferner wird in Faserverbundwerkstoffen der Schall stärker abgeschwächt als in metallischen Konstruktionswerkstoffen, was sich negativ auf die Prüfbarkeit von sehr dicken Laminaten auswirkt. Außerdem hat die elastische Anisotropie dieser Werkstoffe winkelabhängige Ausbreitungsgeschwindigkeiten der Ultraschallwellen zur Folge. Zur Prüfung genutzte Longitudinalwellen breiten sich mit rund 3.000 m/s senkrecht zur Bauteiloberfläche bzw. zu den Laminatlagen aus. Parallel zur Faserrichtung können, je nach Fasertyp, allerdings Werte von über 10.000 m/s erreicht werden. Da konventionelle Ultraschallprüfgeräte meist nur für den Einsatz an isotropen metallischen Werkstoffen konzipiert sind, eignen sich diese nicht für die Berücksichtigung anisotroper Schallgeschwindigkeiten. Zudem variiert die Winkelabhängigkeit je nach Materialsystem, Lagenaufbau oder Betrachtungsrichtung und ist dem Prüfer in der Regel unbekannt. Um die praktische Prüfbarkeit von Faserverbundwerkstoffen mit konventioneller Gerätetechnik dennoch zu ermöglichen, werden Schallwellen üblicherweise senkrecht zu den Laminatlagen in das Bauteil eingebracht. In dieser Raumrichtung liegt eine annähernd konstante Schallgeschwindigkeit vor, wodurch komplexe Wellenausbreitungsphänomene nur noch eine untergeordnete Rolle spielen und prüftechnisch gut beherrschbar werden.
Ultraschall-Rekonstruktions-verfahren
Fortschrittliche, bildgebende Ultraschall-Rekonstruktionsverfahren finden seit wenigen Jahren zunehmenden Einsatz in der Prüfpraxis. Ausgelöst wurde dieser Trend durch eine Steigerung der zur Verfügung stehenden Rechenleistung und durch eine bessere Automatisierung der Prüfung. Mit entsprechenden Algorithmen können herkömmlich aufgezeichnete Ultraschall-Echosignale zu hochaufgelösten Abbildern (2D oder 3D) des Bauteilinneren verarbeitet werden. Ähnlich wie bei der Röntgen-Computertomografie müssen dabei sehr große Datenmengen in kurzer Zeit verarbeitet werden. Häufig anzutreffende Vertreter dieser Algorithmen sind die Synthetic Aperture Focusing Technique oder die Total Focusing Method. Diese können die oben erörterte komplexe Wellenausbreitung in CFK-Laminaten berücksichtigten, vor allem die anisotrope Schallgeschwindigkeit. Dadurch ergeben sich insbesondere Vorteile für die Ultraschallprüfung von sehr dicken CFK-Laminaten, wie sie beispielsweise für Rotorblätter in Windkraftanlagen immer häufiger eingesetzt werden. Verglichen mit der konventionellen Ultraschallprüfung, ermöglichen die oben genannten Ultraschall-Rekonstruktionsalgorithmen auch bei geringeren Prüffrequenzen eine höhere Auflösung bei der Bildgebung.
Full Matrix Capture
Full Matrix Capture (FMC) ist eine spezielle Technik zur Datenerfassung mit einem Ultraschall-Phased-Array-Prüfkopf. Diese Wandler bestehen aus mehreren kleinen piezoelektrischen Einzelelementen (häufig 16, 32, 64 oder 128), die individuell zum Senden- und Empfangen von Ultraschallwellen angesteuert werden können. Regt man, wie bei der klassischen Phased-Array-Prüfung üblich, eine Teilmenge dieser Elemente definiert zeitversetzt an, so überlagen sich die emittierten Elementarwellen konstruktiv zu einer gemeinsamen Wellenfront (Abb. 1). Diese kann entweder auf eine bestimmte Bauteiltiefe fokussiert sein und/oder um einen bestimmten Winkel geschwenkt werden, wodurch z. B. die Ortsauflösung lokal erhöht wird oder mehr Flexibilität bei der Prüfung erreicht wird.
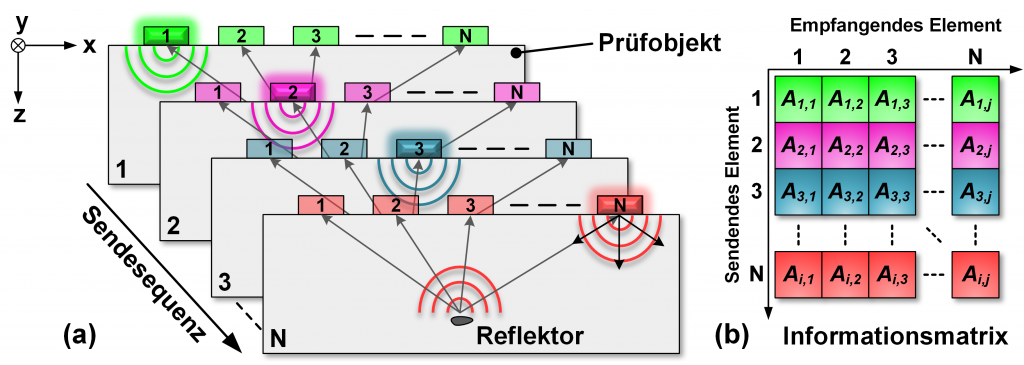
Abb. 2: (a) Messprinzip der Full-Matrix-Capture-
Technik und (b) Organisation der aufgezeichneten Signale in der Informationsmatrix.
Bei FMC wird jedoch ein anderer Ansatz gewählt: Während der ersten Sendesequenz (Abb. 2) wird nur Array-Element 1 zum Senden angeregt. Durch die sehr schmale Elementbreite (ca. 0,2 mm – 2,0 mm) wird eine breit divergierende (d. h. eine nichtfokussierte) Wellenfront emittiert, welche jedes Volumenelement des Prüfobjektes durchdringt oder an möglichen Fehlstellen reflektiert wird. Gleichzeitig befinden sich alle N Prüfkopfelemente im Empfangsmodus, um diese Echos getrennt voneinander aufzuzeichnen (aufgrund der unterschiedlichen Empfängerpositionen werden mögliche Reflektorechos zu unterschiedlichen Zeitpunkten von den Sensorelementen registriert). Die gespeicherten Signale können in der sogenannten „Informationsmatrix“ organisiert werden, wobei die erste Sendesequenz die erste Matrixzeile füllt (Abb. 2b). Wiederholt man diesen Prozess derart, dass jedes Element einmal als Sender fungiert, so wird die Matrix nach wenigen Millisekunden mit N2 Echosignalen vollständig gefüllt („full“). Für eine gängige Prüfkopfgröße mit
z. B. 64 Elementen bedeutet dies 4096 Zeitsignale, die an jeder Prüfkopfposition aufgezeichnet werden und anschließend bildgebend verarbeitet werden. Der wesentliche Vorteil, der sich aus einem aufgezeichneten Full-Matrix-Capture-Datensatz ergibt, besteht darin, dass man mit den Daten der Informationsmatrix beliebige Schallfelder digital nachbilden oder verschiedene Rekonstruktionsalgorithmen anwenden kann.
Total Focusing Method
Die Total Focusing Method (TFM) ist ein bildgebender Rekonstruktionsalgorithmus für einen vollständigen FMC-Datensatz. Im ersten Schritt der Berechnung wird der gewünschte Rekonstruktionsbereich in ein Pixel- bzw. Fokuspunktraster unterteilt (Abb. 3). Für einen bestimmten Bildpunkt wird aus allen N² Signalen der Informationsmatrix jeweils ein Amplitudenwert zu einem bestimmten Zeitpunkt t ausgelesen, welcher der Schalllaufzeit einer Wellenfront (von Senderelement zu Fokuspunkt zu Empfängerelement) entspricht. Befindet sich an einem synthetischen Fokuspunkt auch ein Reflektor (z. B. ein Riss), so werden hohe Echoamplituden aus den Zeitsignalen abgegriffen und aufsummiert (konstruktive Interferenz). Wenn lokal kein Reflektor vorliegt, überlagern sich die Rauschanteile der Zeitsignale destruktiv. Wird der Vorgang für alle Bildpunkte wiederholt, so ergibt sich folglich eine hochaufgelöste Abbildung des Prüfvolumens, indem mögliche Reflektoren mit einem hohen Signal-Rauch-Abstand dargestellt werden können. Bei der Total Focusing Method werden somit die Signale sämtlicher Sender-Empfänger-Kombinationen eines Arraysensors in allen („total“) Bildbereichen digital fokussiert. Ein vergleichbares aber keineswegs praktikables Prüfergebnis könnte man mit der klassischen Phased-Array-Prüfung realisieren. Hierfür müsste man mit allen N Prüfkopfelementen sequenziell in jedem Punkt des Prüfvolumens eine Fokussierung der Ultraschall-energie realisieren, woraus sich aber eine viel zu lange Prüfzeit ergeben würde.
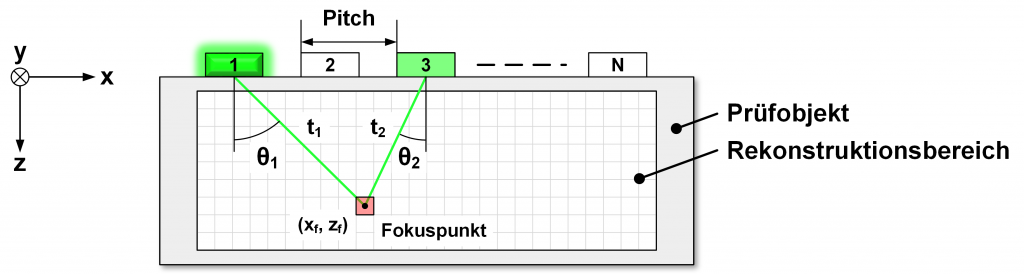
Abb. 3: Prinzip der Total Focusing Method für
eine Sender-Fokuspunkt-Empfänger-Kombination.
Die laufzeitkorrigierte TFM-Berechnung ist auf die genaue Kenntnis der Schallgeschwindigkeit im Prüfmedium angewiesen. Ansonsten überlagern sich mögliche Echosignale im Berechnungsprozess destruktiv und wodurch Fehlstellen unerkannt bleiben können. Für isotrope Konstruktionswerkstoffe ist die Schallgeschwindigkeit in der Regel bekannt oder kann experimentell einfach bestimmt werden. Für CFK-Laminate muss im TFM-Algorithmus berücksichtigt werden, dass die Gruppengeschwindigkeit von Longitudinalwellen in der x-z-Ebene vom Winkel dominiert wird (vgl. Abb. 3). Ausgehend von 0° steigt diese von 3000 m/s bis hin zu Werten von über 10.000 m/s bei 90° an (d.h. parallel zu den Fasern). Diese winkelabhängige Geschwindigkeit muss vor einer FMC/TFM-Prüfung analytisch, simulativ oder experimentell bestimmt werden. Analytische oder simulative Berechnungen können nur angewandt werden, wenn die Steifigkeitsmatrix des Materialsystems bekannt ist. Experimentelle Methoden können auch an unbekannten CFK-Materialien angewandt werden oder dienen zur Absicherung der errechneten Werte.
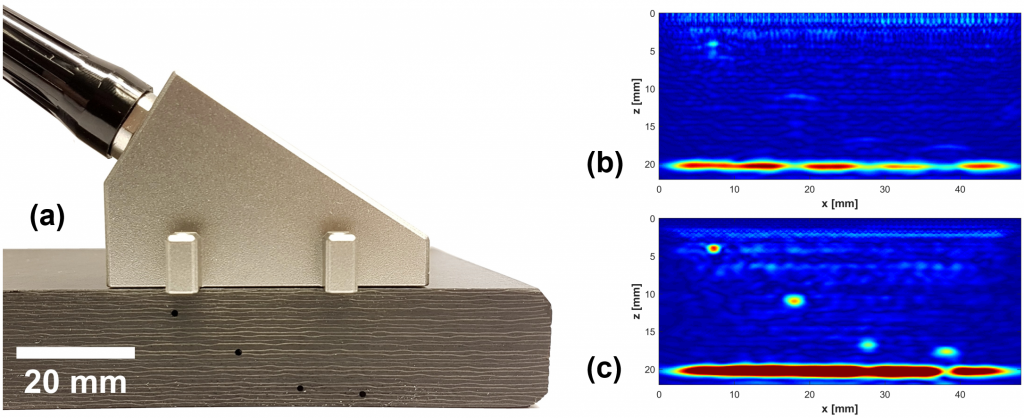
Abb. 4: (a) Phased-Array-Prüfkopf auf einem 20-mm-dicken CFK-Laminat. (b) TFM-Rekonstruktion mit als isotrop angenommenen Schallgeschwindigkeit und (c) unter Berücksichtigung der anisotropen Schallgeschwindigkeit.
Abb. 4 zeigt zwei TFM-Rekonstruktionsergebnisse eines 20-mm-dicken CFK-Laminats mit vier künstlichen Fehlstellen (Bohrungen mit einem Durchmesser von 1 mm). Bei der Berechnung des ersten TFM-Bildes wurde im Algorithmus eine konstante Schallgeschwindigkeit im Material angenommen. Die Bohrungen sind somit nicht bzw. nur sehr schwach zu erkennen. Fließt die winkelabhängige Schallgeschwindigkeit in den Rekonstruktionsprozess mit ein, so können alle vier Bohrungen eindeutig im Ergebnis abgebildet werden.
Fazit
Mit Rekonstruktionsalgorithmen wie der Total Focusing Method können hochaufgelöste Ultraschallergebnisbilder mit hohem Signal-Rausch-Abstand berechnet werden. Dieser Algorithmus basiert auf der konstruktiven Interferenz von Fehler-echos und auf der destruktiven Überlagerung von Gefügerauschen in den aufgezeichneten Zeitsignalen, welche bei CFK-Laminaten besonders ausgeprägt sind. Berücksichtigt man bei der Rekonstruktion die anisotrope Schallgeschwindigkeit im Medium, so ergeben sich Vorteile gegenüber der konventionellen Ultraschallprüfung. Aufgrund der starken Schallschwächung bei mehreren Zentimeter dicken CFK-Werkstoffen ist es oft notwendig, niedrigere Prüffrequenzen zu wählen. Das wirkt sich positiv auf die Eindringtiefe der Ultraschallwellen aus, aber negativ auf die erreichbare Auflösung und Sensitivität gegenüber kleinen Fehlstellen. Dem wirkt der TFM-Algorithmus entgegen.
Jan-Carl Grager¹ ²
Christian U. Große ²
Siemens AG, Corporate Technology, München ¹
Technische Universität München, Lehrstuhl für Zerstörungsfreie Prüfung, München ²
Kontakt E-Mail: jan-carl.grager@tum.de