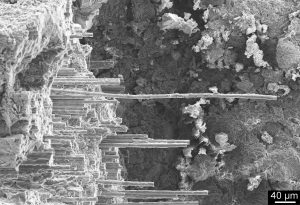
Abbildung 1: Bruchfläche eines CMC; Fasern wurden aus dem Gefüge herausgezogen und ermöglichen damit schadenstolerantes Verhalte
Keramische Faserverbundwerkstoffe
Verbundwerkstoffe aus keramischen Fasern umgeben von einer keramischen Matrix werden in der Fachwelt als CMC (Ceramic Matrix Composites) bezeichnet und sind eine sehr junge Werkstoffklasse. Im Vergleich zu metallischen oder polymeren Verbundwerkstoffen, dienen die Fasern in CMC nicht der Erhöhung der Festigkeit oder Steifigkeit, sondern ermöglichen durch den Faser-Pull-Out (Verbrauch von Energie beim Risswachstum) ein quasiduktiles oder auch schadenstolerantes Verhalten (Abbildung 1). Defekte, welche in dichten Hochleistungskeramiken zum katastrophalen Versagen führen würden, werden durch CMC ohne weiteres ertragen und ermöglichen den Einsatz in sicherheitsrelevanten Anwendungen.
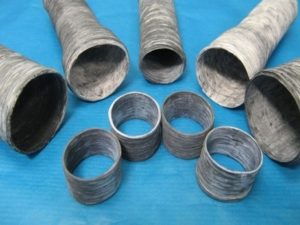
Abbildung 2: Gewickelte Geometrien aus SiC-Fasern mit SiCN-Matri
Weiterhin ergeben sich durch die Fasern besondere Möglichkeiten der Formgebung. Mittels Wickeltechnologie, Weben, oder Laminieren von Fasergelegen, lassen sich große und dünnwandige Bauteile fertigen (Abbildung 2).
Die Kombination aus Formenvielfalt und Schadentoleranz bei gleichzeitig sehr guter Hochtemperaturstabilität prädestiniert diese Werkstoffe für den Einsatz in energieerzeugenden Gasturbinen, Flugzeugtriebwerken und in der Brennertechnik. Forschungsschwerpunkte bei der Entwicklung von CMC sind am Fraunhofer Institut für keramische Technologien und Systeme IKTS vor allem die Matrixzusammensetzung sowie Faserbeschichtungen für ein schadenstolerantes Verhalten und deren Herstellungsprozesse.
Korrosion bei hohen Temperaturen
Obwohl CMC für extremste Bedingungen geeignet sind, zeigen auch sie besonders im Langzeiteinsatz korrosionsbedingte Schädigungen. Hierbei ist zu unterscheiden, ob der Werkstoff oxidisch oder nicht-oxidisch ist. Oxidische CMC (OCMC) bestehen aus Aluminiumoxid- oder Mullit-Fasern in einer Matrix aus Zirkonoxid, Aluminiumoxid oder Mullit (oder auch Mischungen). Sie sind für den Langzeiteinsatz bis zu 1150°C geeignet und finden derzeit beispielsweise Anwendung als Komponenten in der Heißgasführung in den neuesten Flugzeugtriebwerken oder als Brennerdüsen in Ofenanlagen. Aufgrund ihrer oxidischen Natur erfahren sie keine Schädigung durch Oxidation, jedoch führt der in Brenngasen enthaltene Wasserdampf zur Bildung von flüchtigen Hydroxiden an der Oberfläche, welche im Gasstrom abtransportiert werden. Diese sogenannte Heißgaskorrosion führt zu einem messbaren Materialabtrag, welcher die Stabilität des Bauteils verringern kann.
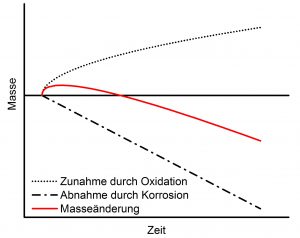
Abbildung 3: Masseänderung von nicht-oxidischen Keramiken während der Heißgaskorrosion; Überlagerung von Massezunahme durch Oxidation und Masseabnahme durch Korrosion
Nicht-oxidische CMC bestehen wiederum aus Kohlenstoff- oder Siliziumcarbidfasern, welche in einer Matrix vornehmlich aus Siliziumcarbid oder Siliziumcarbonitrid eingebettet sind. Sie sind bis zu 1400°C langzeitstabil und finden derzeit Anwendung in Raketentriebwerken und militärischen Flugzeugturbinen. Neueste zivile Flugzeugturbinen sollen in Zukunft mit rotierenden Schaufeln aus diesen Werkstoffen ausgerüstet werden. Im Vergleich zu OCMC kann bei nicht-oxidischen CMC eine Schädigung durch Oxidation erfolgen. Je nach Material- und Herstellungsvariante kann zwar eine gewisse Oxidationsbeständigkeit durch Selbstpassivierung erreicht werden, jedoch führt wasserdampfinduzierte Heißgaskorrosion zum Abbau der oxidischen Passivierungsschicht und ähnlich den OCMC zu einem schädigenden Materialabtrag (Abbildung 3).
Eine weitere Form der Korrosion wird durch Sande und Flugasche ausgelöst. Sie bestehen vornehmlich aus Calcium-, Magnesium-, Aluminium- und Siliziumoxid (CMAS). Naturereignisse wie Vulkanausbrüche und Wüstenstürme führen dazu, dass diese Oxide in Flugzeugtriebwerke und deren heißeste Bereiche gelangen und sich dort ablagern. Infolge chemischer Wechselwirkungen werden die mechanischen Eigenschaften der CMC dadurch deutlich verschlechtert.
Korrosionsschutz
Das Fraunhofer IKTS entwickelt und testet Beschichtungsmaterialien, welche die Langzeitbeständigkeit von CMC deutlich erhöhen. Mithilfe einer in Europa unikalen Testanlage (Abbildung 4) ist es möglich, realitätsnahe Korrosionsbedingungen in Gasturbinen abzubilden. So wird beispielsweise die Eignung von neu entwickelten Materialsystemen als Korrosionsschutzschicht (EBC: Environmental Barrier Coating) evaluiert. Ist ein Material ausreichend stabil in Heißgasatmosphäre, erfolgt die Untersuchung als Beschichtung auf entsprechenden CMC-Substraten. Neben der Bestimmung der Masseänderung dienen Gefügeanalysen der Aufklärung von Schädigungsmechanismen (Abbildung 5). Dabei spielen Korrosion, chemische Wechselwirkungen zwischen Beschichtung und Substrat sowie die thermophysikalischen Eigenschaften der Materialien eine große Rolle.
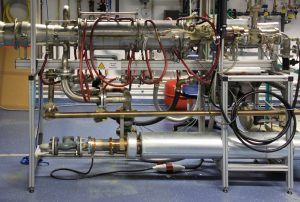
Abbildung 5: Teststand (HTBR, High Temperature Burner Rig) zur Untersuchung des Korrosionsverhaltens in strömendem Heißgas
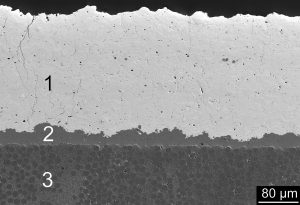
Abbildung 4: Rasterelektronenmikroskopische Aufnahme eines Systems aus Korrosionsschutzschicht (EBC; 1) und Haftschicht (Bondcoat, 2) auf nichtoxidischem CMC (3)
Die Weiterentwicklung von Beschichtungssystemen erfolgt unter Beachtung der realen Einsatzbedingungen von CMC, welche mechanische Lasten, Thermoschock, große Temperaturdifferenzen und vieles mehr umfassen. Dies führte beispielsweise zur Entwicklung eines EBC-Materials mit selbstheilenden Eigenschaften. Kleinste Partikel in einer korrosionsstabilen Matrix oxidieren bei Kontakt mit dem Sauerstoff in der Brenngasatmosphäre und dehnen sich dabei aus. Das führt dazu, dass die Sauerstoffdiffusion im Material deutlich verringert wird und auftretende Risse wieder verschlossen werden.
Eine sehr aktuelle Herausforderung besteht bei der Entwicklung von Schichtsystemen für den Einsatz in Flugzeugtriebwerken. Sande und Flugasche (CMAS) zeigen deutliche Schädigungen an gängigen EBC-Materialien. Aus diesem Grund werden am Fraunhofer IKTS aktuell neue Beschichtungsmaterialien zum Korrosionsschutz mit erhöhter Toleranz gegenüber CMAS erforscht.
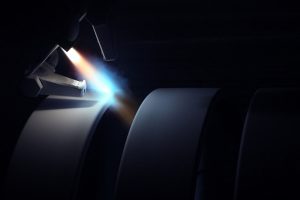
Abbildung 6: Atmosphärisches Plasmaspritzen (APS)
Beschichtungstechnologie für CMC
Nicht nur die EBC-Materialien sondern auch die Methodik des Aufbringens haben großen Einfluss auf den Korrosionsschutz. Gute Schichthaftung, Homogenität und ein möglichst einfaches Verfahren sind dabei von Hauptinteresse für industrielle Kunden. Aus diesem Grund arbeitet das IKTS hauptsächlich über Tauchbeschichtung (Dip Coating) und atmosphärisches Plasmaspritzen (APS). Um die Möglichkeiten der Schichtentwicklung voll auszuschöpfen werden dennoch auch weitere Beschichtungstechnologien in Zusammenarbeit mit Partnern aus der Forschung und der Industrie untersucht.
Kontakt
Fraunhofer-Institut für keramische Technologien und Systeme IKTS
Winterbergstraße 28, 01277 Dresden
Autoren: Willy Kunz, Katrin Schönfeld, Dr. Hagen Klemm