Teil 1: Perspektiven durch heiß-isostatisches Pressen
Pulvermetallurgische Herstellung
Pulvermetallurgisch hergestellte Bauteile (PM) sind im Bereich des Motorenbaus, bei Getriebeteilen sowie im Werkzeug- oder Formenbau etabliert. Beim konventionellen Pressen und Sintern werden wasserverdüste, spratzige Metallpulver mit Additiven und weiteren Legierungselementen gemischt und in Pressformen zu Grünkörpern verdichtet, die bereits annähernd die endgültige Form aufweisen (near netshape). Während der Festphasensinterung unter Vakuum, Inertgas oder reduzierenden Atmosphären verbinden sich die Pulverpartikel durch Diffusion und stellen das Gefüge und die mechanischen Eigenschaften ein. Pressen und Sintern wird als ein kostengünstiges Herstellungsverfahren für hohe Stückzahlen eingesetzt. Auch der Metallpulverspritzguss (MIM) ermöglicht Serienfertigung, typischerweise jedoch für kleine, komplex geformte Teile mit hoher Oberflächengüte und Maßhaltigkeit. Sehr feine Metallpulver werden mit thermoplastischen Bindern versetzt und unter erhöhten Temperaturen und hohem Druck in Spritzgusswerkzeuge gepresst. Die Grünteile werden thermisch oder chemisch entbindert und unter starker Sinterschwindung gesintert. Für Anwendungen, die herausragende mechanische Eigenschaften oder harte Werkstoffe erfordern, die durch Spanen, Schmieden oder Gießen nicht verarbeitet werden können, wird auf das Verfahren des heiß-isostatischen Pressens (HIP) zurückgegriffen. Kapseln, welche die Bauteilgeometrie abbilden, werden hierbei aus Stahlblech geschweißt, mit sphärischem, gasverdüstem Metallpulver gefüllt, evakuiert, verschlossen und bei hohen Temperaturen und Drücken zu voller Dichte konsolidiert. Zuletzt wird die Kapsel, die nur als Hilfsmittel zur Verdichtung genutzt wurde, entfernt.
Chancen additiver Fertigungstechnologien
Additive Fertigungsverfahren erfahren momentan große Aufmerksamkeit und ein starkes Interesse in Forschung und Industrie. So werden derzeit 18 Technologien zur additiven Herstellung metallischer Bauteile unterschieden, wobei über 140 Anlagenhersteller um Marktanteile kämpfen [1]. Die Vorteile der additiven Fertigung (AM) sind unbestritten; die Nachteile, wie beispielsweise hohe Prozesskosten oder eingeschränkt reproduzierbare und homogene Werkstoffeigenschaften, gilt es noch zu überwinden. Ein Ansatz ist die Verbindung der additiven Fertigung mit dem bereits etablierten pulvermetallurgischen HIP-Verfahren, so dass beide Verfahren voneinander profitieren und neue Möglichkeiten eröffnet werden. Dies lässt sogar eine AM-Kleinserienproduktion als Ergänzung zur MIM-Fertigung wirtschaftlich erscheinen.
Kombination von AM und heiß-isostatischem Pressen
HIP kann als reine Nachbehandlung von AM-Bauteilen eingesetzt werden, um Dichte, Gefüge und resultierende mechanische Eigenschaften zu verbessern. Dies wird im Folgenden anhand einiger Einblicke in aktuelle Forschungsprojekte und konkreter Bauteile beschrieben. Darüber hinaus wird demonstriert, wie HIP auch als Teil der Prozesskette zur Kostenreduktion beitragen kann.
Binder Jetting Bauteile für Kleinserien
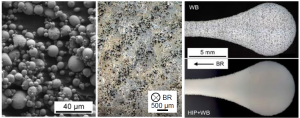
Abbildung 1: a) Sekundärelektronenbild des 17-4PH Pulvers, b) geätztes Gefüge nach Sinterung BR=x/Baurichtung, Schliff durch Zugproben nach H900 Wärmebehandlung (WB) sowie nach HIP+WB
Der Binder Jetting Technologie (BJT) stellt geringe Anforderungen an die Pulver und erlaubt hohe Baugeschwindigkeiten. In einem gemeinsamen Projekt des Fraunhofer IFAM Bremen und dem Institut für Werkstoffanwendungen im Maschinenbau (IWM) an der RWTH Aachen University wurden feine MIM-typische Pulver aus dem martensitischen ausscheidungshärtenden Stahl 17-4PH zur Proben- und Bauteilfertigung ausgewählt, siehe Abbildung 1. Der lokale Bindereindruck in das Pulverbett verklebt die Metallpartikel, sodass Grünkörper entnommen, von überschüssigem Pulver befreit, entbindert und unter Wasserstoffatmosphäre gesintert werden können. Der schichtweise Bindereintrag zeigt sich im resultierenden Gefüge nach Sinterung. Metallografische Schliffe, mit einigen Zehntel-Grad Abweichung zur Aufbauebene (x-y-Ebene) präpariert, Abbildung 1b), legen abwechselnd Bereiche mit hoher und relativ niedriger Porosität offen. Eine Wärmebehandlung führt zu feinen Ausscheidungen, die Härte und Festigkeit steigern, aber die Porenstruktur nicht beeinflussen. Die HIP-Nachbehandlung hingegen reduziert die Porosität signifikant wie Abbildung 1c) belegt.
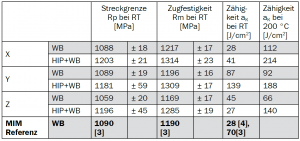
Tabelle 1: Gegenüberstellung der erzielten Kennwerte von BJT-Proben mit MIM-Referenzwerten, WB=H900 Wärmebehandlung nach ASTM
Die Porenverteilung in Abhängigkeit der Belastungsrichtung erklärt schließlich die deutlich schlechtere Festigkeit und Zähigkeit in z-Richtung, als in x- oder y-Richtung. Diese Tendenz bleibt zwar nach HIP-Nachbehandlung bestehen. Insgesamt werden die mechanischen Eigenschaften jedoch so stark erhöht, dass typische MIM-Referenzwerte trotz starker Streuung sicher erreicht werden, siehe Tabelle 1. Die Zähigkeit in Hochlage ab 200 °C wird durch HIP sogar verdoppelt.
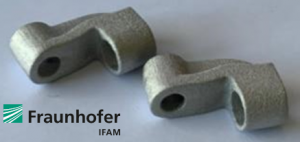
Abbildung 2: MIM-typisches Bauteil „Roller
Support“ (ITB Precisietechniek B.V.) aus 17-4 PH, hergestellt über Binder Jetting
Bei der Bauteilherstellung wird die anisotrope Sinterschwindung durch Sintersimulation bereits beim Binder Jetting Druckprozess berücksichtigt. Typische MIM-Teile wie in Abbildung 2 können auf diese Weise über die Binder Jetting Prozesskette hergestellt werden. Die Oberflächenrauheit, derzeit um einen Faktor 4 schlechter, als bei MIM-Teilen (Ra < 1 µm), weist jedoch noch Optimierungspotenzial auf.
Innengekühlte Hartmetallwerkzeuge
Die laserbasierte additive Fertigung von Wolframkarbid-Kobalt (WC-Co) stellt eine Herausforderung insbesondere hinsichtlich der Rissfreiheit, der Dichte sowie der Homogenität des Werkstoffgefüges dar. Im Rahmen des Projektes „Additive Fertigung von Zerspanwerkzeugen aus Wolframkarbid-Kobalt“ fertigen und untersuchen das IWM der RWTH Aachen University, das Fraunhofer Institut für Lasertechnik ILT und das Werkzeugmaschinenlabor WZL der RWTH Aachen University Zerspanwerkzeuge aus WC-Co [5]. Die Geometriefreiheit des LPBF Prozesses erlaubt es die Position und die Form der Kühlkanäle nach thermischen Randbedingungen im Betrieb auszulegen. Die aktuellen Ergebnisse zeigen, dass die LPBF-Prozessparameter noch hinsichtlich der Oberflächenrauheit angepasst werden müssen, Abbildung 3.
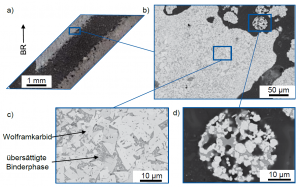
Abbildung 3: a) Lichtmikroskopische Aufnahme eines Kühlkanals in einem WC-Co Volumenkörper hergestellt mit LPBF, BR: Baurichtung, b) Rasterelektronische Aufnahme im Randbereich des Kühlkanals, c) WC-Co Gefüge nach dem LPBF Prozess, d) WC-Co Pulverpartikel nach dem LPBF Prozess
Nicht aufgeschmolzenes Pulvermaterial, welches aus den Kühlkanälen entfernt wird, entspricht dem Zustand vor dem LPBF-Prozess und kann wiedereingesetzt werden. Das WC-Co-Gefüge besteht aus der Wolframkarbidphase und einer übersättigten Binderphase. Eine Sinter-HIP Nachbehandlung, bei 1380 °C und 50 bar, führt zur Reduktion der Porosität und Kornvergröberung. Außerdem fördert die Nachbehandlung die Wiederausscheidung von Wolfram und Kohlenstoff, sodass die Binderphase der in konventionell gesinterten Hartmetallen entspricht, Abbildung 4.
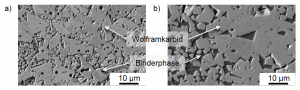
Abbildung 4: Rasterelektronische Aufnahme des WC-17Co Gefüges nach LPBF: a) as-built, b) nach Sinter-HIP
Verbundbauteile durch AM+HIP
Durch eine kombinierte Fertigungsroute aus AM und konventionellem Pulver-HIP werden vollkommen neue Möglichkeiten eröffnet. Hierbei erfolgt die Fertigung der HIP-Kapseln automatisiert durch AM und hebt geometrische Beschränkungen, die bislang durch die manuelle Kapselfertigung bestehen, auf. Es können nahezu beliebig komplexe Bauteile realisiert werden. Die Kapsel dient nun als integraler Bestandteil des Bauteils ist, weshalb das aufwändige Entfernen des Kapselwerkstoffes entfällt. Die Bauteiloberfläche kann darüber hinaus durch die Verwendung von korrosions- und/oder verschleißbeständigen Werkstoffen für die Kapsel funktionalisiert werden. Eine aufwändige Oberflächenbeschichtung kann so ersetzt werden. Mit Hilfe der numerischen Geometrieoptimierung kann die HIP-Schwindung der Bauteile über die gesamte Prozesskette abgebildet werden, sodass sich eine Kapselgeometrie vor dem HIP Prozess berechnen lässt, bei der nach dem Prozess und dem damit einhergehende Schwindung endkonturnahe Bauteile vorliegen. Dieser ressourcensparende Ansatz erweitert somit das Anwendungsspektrum des HIP und führt zu einer deutlichen Effizienzsteigerung im Bereich der additiven Fertigung, da nur eine leere Hülle gefertigt wird. Die grundlegende Machbarkeit der Kombination aus AM und HIP wurde von IWM und IFAM Bremen in einem abgeschlossenen Projekt bereits nachgewiesen [6]. Hierbei wurde mittels LPBF eine Kapsel aus korrosionsbeständigem austenitischen Stahl X5CrNiMo17-12-2 gefertigt und mit dem Werkzeugstahl 56NiCrMoV7 gefüllt und einem HIP Zyklus unterzogen. Das so entstandene Verbundbauteil, das Segment einer Extruderschnecke für die Kunststoffverarbeitung, ist in Abbildung 5 dargestellt. Im Rahmen des aktuellen Projektes „Maß-HIP-3D“ erfolgt eine Erweiterung des Werkstoffspektrums auf verschleißbeständige Materialien. Alternativ zu LPBF wurden dabei die AM Verfahren Binder Jetting und Elektronenstrahlschmelzen ausgewählt, da diese bei der rissfreien Verarbeitung harter Werkstoffe Vorteile bieten.
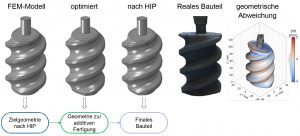
Abbildung 5: Numerische Optimierung der Kapselform, reales Bauteil nach HIP (Coperion GmbH), Vergleich von Real- und Zielgeometrie
Förderung
Die IGF-Vorhaben 19733 N, 20805 N, 18968 N und 21074 BG der Forschungsgesellschaft Stahlverformung e.V. wurden über die AiF im Rahmen des Programms zur Förderung der industriellen Gemeinschaftsforschung (IGF) vom Bundesministerium für Wirtschaft und Energie aufgrund eines Beschlusses des Deutschen Bundestages gefördert.
Referenzen
[1] ampower GmbH, Metal Additive Manufacturing technology landscape, Version 5.0, März 2020
[2] Herzog et al.; Abschlusszusammenfassung zum Forschungsprojekt IGF 19733 N „3DP für MIM“ http://dx.doi.org/10.18154/RWTH-2021-01204
[3] Metal Powder Industries Federation, MPIF Standard 35-MIM, 2016
[4] Suri et al., Powder Metallurgy 49:1, 40-47, 2006, DOI: 10.1179/174329006X89317
[5] Fries et at., Steel research int., 91:1900511, pp. 1-7, 2020, DOI: 10.1002/srin.201900511
[6] Riehm et al., Abschlusszusammenfassung zum Forschungsprojekt IGF 18968 N „HIP+AM für Verbundbauteile“, 2019, DOI: 10.18154/RWTH-
2019-05106
Autor:innen
Simone Herzog (s.herzog@iwm.rwth-aachen.de),
Sofia Fries, Markus Mirz, Anke Kaletsch, Christoph Broeckmann
Institut für Werkstoffanwendungen im Maschinenbau (IWM),
RWTH Aachen University