Einleitung
Nachdem in den Teilen 1 und 2 dieser Artikelserie auf typische Fehlerarten in Klebverbindungen sowie auf deren Schadensbewertung eingegangen wurde, wird in diesem dritten Teil nun aufgezeigt, welche Möglichkeiten bestehen, entsprechende Fehler in Klebverbindungen zerstörungsfrei zu detektieren. Insbesondere im Schiffbau, der durch metallische Bauweisen und schweißtechnische Fügeverfahren geprägt ist, besteht noch immer eine große Skepsis gegenüber geklebten Verbindungen. Um den Befürchtungen eines Totalausfalls einer sicherheitsrelevanten Klebverbindung entgegen zu wirken, besteht die Möglichkeit, diese während des Einsatzes zerstörungsfrei zu prüfen, um ggf. entstandene Schäden oder Fehlstellen frühzeitig zu erkennen und Reparaturmaßnahmen einzuleiten. Dieses Vorgehen wird bei Schienenfahrzeugen und Windkraftanlagen bereits im Rahmen wiederkehrender Prüfungen erfolgreich praktiziert.
Zerstörungsfreie Prüfung von Klebverbindungen
Zur Erprobung von zerstörungsfreien Prüfverfahren (zfP) und zur Bestimmung von Nachweisgrenzen unterschiedlicher Fehlerarten und Imperfektionen in Klebverbindungen ist es üblich, vergleichende Untersuchungen an fehlerfreien und fehlerbehafteten Klebungen durchzuführen [VAL17]. Das Prinzip eines zfPs beruht in den meisten Fällen auf einer geeigneten minimalen Anregung des Prüfobjekts, z.B. mittels eines Impulshammers oder Ultraschallwellen, um Informationen über eine zuvor definierte Eigenschaft zu erhalten. Wichtig ist dabei, dass die für die Prüfung notwendige Anregung nicht zu einer Beschädigung führt, so dass das Bauteil nach bestandener Prüfung in Betrieb genommen werden bzw. bleiben kann [JÜN10]. Gegenüber Bauteilen und Komponenten mit klar definierten Systemgrenzen, für die die strukturelle Integrität bzw. Freiheit von volumenartigen Fehlern wie Rissen, Lunkern etc. entscheidend ist, kommt bei Klebverbindungen erschwerend hinzu, dass die Klebschicht in der Regel an zwei Fügepartner anschließt und daher auch flächige Fehlerarten wie Haftungsverlust von Bedeutung sind. Insbesondere sind hier sogenannte Kissing Bonds zu erwähnen, deren Nachweis hohen apparativen Aufwand erfordert [JEE17]. Um diese Fehler zu detektieren, unterscheidet [GRE20] zwischen folgenden zfP:
- Radiologische Prüfverfahren (Röntgenstrahl- und Gammastrahldefektoskopie),
- akustische Prüfverfahren (Klang-, Ultraschall- und Schallemissionsprüfung),
- thermografische Prüfverfahren (Wär-mefluss-, Wärmewellenanalyse und Videothermografie),
- elektromagnetische Prüfmethoden (magnetische Rissprüfung, Schichtdickenmessung und magnetoinduktive Prüfung),
- Rissprüfung (Endoskopie, Sicht-, Penetrier-, Dichtigkeits-, Magnetpulver- und Fluoreszenzprüfung),
- Mikrowellenprüfung (Transmissions- und Reflexionsverfahren) und
- optische Prüfmethoden (Holografie, Laser-Speckle-Interferometrie, Shearographie, Laserextensometrie u. a.),
wovon aber nur ausgewählte Verfahren auf Grund des apparativen Aufwands oder der Umgebungsbedingungen auf Werften und Schiffen zur Anwendung bei der Untersuchung von Klebverbindungen geeignet sind. Da sich hochelastische Dickschicht- und hochfeste Strukturklebstoffe sowohl in ihren Eigenschaften als auch in ihren Anwendungsgebieten teilweise stark unterscheiden, werden diese in den nachfolgenden Abschnitten gesondert untersucht.
Hochelastischer Dickschichtklebstoff
Zur Detektion von Fehlern in hochelastischen Dickschichtklebungen wurden neben der Sichtprüfung, auch ein Grauwertkorrelations-Messverfahren zur Ermittlung der flächigen Dehnungsverteilung auf der Klebschicht, das Ultraschall (US-) -Prüfverfahren sowie die Thermografie-Prüfung angewandt. Beispielhaft werden hier die Ergebnisse der thermografischen Untersuchungen dargestellt.
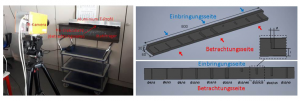
Abbildung 1: Versuchsaufbau Thermografie mit bauteilähnlichem Probekörper (links), Schnitt durch Klebschicht mit zylinderförmigen Volumenfehlern (Durchmesser Ø, Abstand t zur Betrachtungsseite)
Wie bereits in VAL17 erwähnt, beruhen zfP auf dem Vergleich fehlerfreier und fehlerbehafteter Bereiche einer Klebung. Zur rationellen Einbringung von verschiedenen volumenartigen Fehlern mit dazwischen liegenden ungestörten Klebschichtbereichen wurde ein bauteilähnlicher Probekörper, wie in Abbildung 1 dargestellt, konzipiert und hergestellt. Dieser Probekörper ist einer Klebverbindung zwischen einer Schiffsrumpfstruktur aus Stahl und einem Deckshaus aus Aluminium nachempfunden. Die Breite der Klebschicht beträgt 60 mm und deren Dicke 30 mm. Die verschieden volumenartigen Fehler, die über Formelemente von der Einbringungsseite in die Klebschicht eingebracht wurden, verteilen sich über eine Länge des Probekörpers von 800 mm. Die Volumenfehler variieren in Bezug auf ihren Durchmesser (4 mm ≤ Ø ≤ 20 mm) und den Abstand zur Betrachtungsseite (5 mm ≤ t ≤ 40 mm). Der ganz rechts liegende Fehler (Ø10/t0) erstreckt sich über die gesamte Klebschichtbreite ähnlich einer Durchgangsbohrung. In Blickrichtung auf die Betrachtungsseite sind bis auf diesen durchgängigen Volumenfehler die anderen zurückliegenden Volumenfehler in der Klebschicht visuell nicht erkennbar.
In dem Versuchsaufbau (Abbildung 1 links) wird die Betrachtungsseite der Klebschicht mit einer Infrarot (IR)-Kamera (TAURUS 110k SM Pro, IRCAM GmbH, Erlangen) in einem Arbeitsabstand von 0,8 m observiert. Dieser Arbeitsabstand, der in Vorversuchen ermittelt wurde, stellt für den vorliegenden Anwendungsfall einerseits in Bezug auf das Auflösungsvermögen/Genauigkeit und andererseits auf die nutzbare Beobachtungsbreite (ca. 600 mm) als ein guter Kompromiss dar. Nach möglichst homogener thermischer Anregung der Betrachtungsseite mit einer Heißluftpistole auf ca. 40–50°C Oberflächentemperatur ergaben sich die in Abbildung 2 aus Einzelmessungen montierten IR-Bilder mit zugehörigen Temperaturgrafen entlang der blau eingezeichneten Messlinien in der Klebschicht.
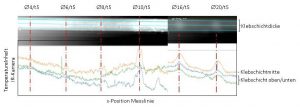
Abbildung 2: IR-Bild der Klebschicht (oben) und drei Temperaturgrafen (unten) entlang der blau eingezeichneten Messlinien für den linken Abschnitt des Probekörpers mit Volumenfehlern unterschiedlicher Durchmesser und gleichem Oberflächenabstand. x-Positionen der Volumenfehler durch senkrechte rote Strichpunktlinien gekennzeichnet.
Wie in dem linken Teil des Bildes erkennbar ist, führt die Anregung mit einer Heißluftpistole oft zu keiner homogenen thermischen Anregung, ist aber dafür mit sehr einfachem Equipment realisierbar. Bessere Resultate lassen sich mit einer Wärmestrahlungsquelle erzielen. Für den Temperaturverlauf in der Klebschichtmitte (orange Kurve) findet man an den Positionen mit Volumenfehlern jeweils eine lokal höhere Temperatur als in dem unmittelbaren Umgebungsbereich. Diese Temperaturerhöhung ist eine Folge der schlechteren Wärme(ab)leitung in die Klebschichttiefe, da die in den Fehlstellen vorhandene Luft deutlich weniger Wärme ableiten kann als der Klebstoff. Daher kommt es jeweils vor den Fehlstellen zu einem Wärmestau, der sich als eine Zone erhöhter Temperatur in den IR-Bildern darstellt. Gut ist diese lokale Temperaturverteilung für die beiden größten Fehlstellen (Ø15/t5 und Ø20/t5) als hellere Bereiche zu erkennen. Gegenüber der Temperatur in der Klebschichtmitte ist der Bereich ober- und unterhalb der Fehlstelle deutlich kühler. Auf diese Weise ist es möglich, auch Informationen über die Position einer möglichen Fehlstelle in Dickenrichtung der Klebschicht zu erlangen. Der detektierbare Fehlerdurchmesser (Ø 6) entspricht für den untersuchten hochelastischen Klebstoff etwa der Tiefe des Volumenfehlers (t5).
In Abbildung 3 ist das Messergebnis des rechten Abschnitts des Probekörpers mit Volumenfehlern Ø 10 und unterschiedlichen Oberflächenabständen dargestellt. Bis auf den Volumenfehler, der die gesamte Klebschicht durchdringt (Ø 10/t0), sind keine weiteren Fehler eindeutig nachweisbar. Jedoch sind in der rechten Nachbarschaft des Fehlers Ø10/t15 gewisse Anomalien der Temperaturverläufe erkennbar, die u.U. auf den Fehler hindeuten. Insgesamt ist jedoch festzustellen, dass die erkennbare Tiefenlage des Fehlers dem Durchmesser entspricht.
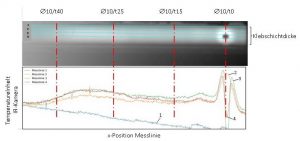
Abbildung 3: IR-Bild der Klebschicht (oben) und vier Temperaturgrafen (unten) entlang der blau eingezeichneten Messlinien für den rechten Abschnitt des Probekörpers mit Volumenfehlern gleicher Durchmesser aber unterschiedlichen Oberflächenabständen. x-Positionen der Volumenfehler durch senkrechte rote Strichpunktlinien gekennzeichnet.
Adhäsionsfehler, die als dünne Volumenfehler durch Aussparungen von 0,05 mm Dicke in der Klebschicht angrenzend zum Stahlsubstrat eingebracht wurden, konnten mittels der Thermografieprüfung nicht ermittelt werden. Jedoch war es möglich, solche Fehler mittels Ultraschall-Prüfung zu detektieren, worauf an dieser Stelle aber nicht weiter eingegangen werden soll.
Interessant ist es noch zu erwähnen, dass mit einer wesentlich preisgünstigeren IR-Kamera (TIM 640, Micro-Epsilon, Ortenburg) ähnliche Befunde ermittelt werden konnten. Abbildung 4 zeigt ein Falschfarben IR-Bild des Probekörpers, aufgenommen mit einem Arbeitsabstand von 1,6 m, welches Volumenfehler als Hellbereiche innerhalb der sich gelb abzeichnenden Klebschicht erkennen lässt. Trotz der geringeren Auflösung der Kamera und des doppelt so großen Arbeitsabstands haben die Messergebnisse einen vergleichbaren Informationsgehalt wie die mit der Taurus IR-Kamera ermittelten.
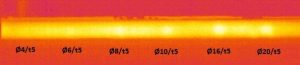
Abbildung 4: IR-Bild, Kamera: TIM 640, Arbeitsabstand:1,6m, Volumenfehler, Erwärmung der Betrachtungsseite mit Heißluftpistole
Hochfester Strukturklebstoff
Neben den bei den hochelastischen Dickschichtklebstoffen vorgestellten Untersuchungen werden u.a. die Schwingungsanalyse (akustisch) und die Röntgenprüfung (radiologisch) sowohl an fehlerfreien als auch fehlerbehafteten Probekörpern mit hochfesten Strukturklebstoffen durchgeführt. Dafür werden Imperfektionen gezielt in Probekörper eingebracht, um diese zfP an den Probekörpern zu testen und deren Eignung in Bezug auf die Fehlerdetektion zu prüfen. Die eingebrachten Imperfektionen repräsentieren Luft- bzw. Materialeinschlüsse und Kissing Bonds und werden mit Hilfe der in den vorherigen Artikeln vorgestellten Methoden in verschiedenen Ausprägungen hergestellt.
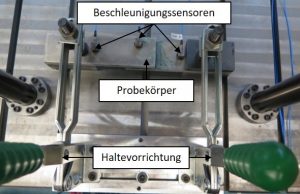
Abbildung 5: Versuchsaufbau der Schwingungsanalyse mit fixiertem Probekörper
Bei der Schwingungsanalyse müssen Beschleunigungssensoren auf der Oberfläche des zu untersuchenden Verbunds aufgebracht werden (vgl. Abbildung 5). Mit Hilfe eines Impulshammers wird die Probe angeregt, woraufhin Schwingungen entstehen, die sich in dem Probekörper ausbreiten. Diese Schwingungen werden von den Beschleunigungssensoren erfasst und können über eine Software ausgewertet werden. So lassen sich für den Verbund charakteristische Peaks über ein Frequenzband, für das die Beschleunigungssensoren ausgelegt sein müssen, darstellen. Dies repräsentiert gewissermaßen den Fingerabdruck des Probekörpers. Imperfektionen in Klebungen beeinflussen die Ausbreitung der Schwingungen, weshalb sich Unterschiede zwischen fehlerfreien und fehlerbehafteten Proben einstellen. In den Versuchen werden u.a. eine fehlerfreie Probe (Referenz) sowie zwei fehlerbehaftete Proben (Polystyrolkugeln in einem 4×6-Muster in der Klebschicht sowie Kissing Bonds mit Hilfe von PTFE-Folie) untersucht.
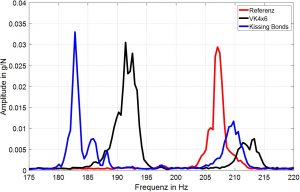
Abbildung 6: Peaks der Probekörper mit verschiedenen Fehlstellen
Wie auf Abbildung 6 zu erkennen ist, verschieben sich aufgrund der Fehlstellen die Peaks in einen anderen Frequenzbereich. Damit sind sie deutlich von dem Peak der Referenzserie zu unterscheiden und klar als fehlstellenbehaftet einzuordnen. Voraussetzung für die Unterscheidung zwischen einer fehlerfreien bzw. fehlerbehafteten Probe ist eine hinreichend große Datenbasis an Messungen an fehlerfreien Probekörpern. Des Weiteren müssen während der Messungen Vorkehrungen getroffen werden, um möglichst alle Störeinflüsse auf den Probekörper zu eliminieren, sodass z.B. die Vibrationen eines laufenden Motors oder Schritte von vorbeilaufenden Personen nicht die Ergebnisse beeinflussen.
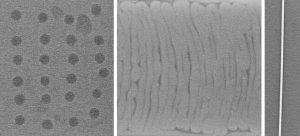
Abbildung 7: Polystyrolkugeln im 4×6-Muster (links), Lufteinschlüsse zwischen Klebraupen (mittig) und Stahldraht (rechts) in Klebschicht
Bei der Röntgenprüfung wird der zu untersuchende Verbund mit Hilfe einer Röntgenröhre durchstrahlt. Hinter dem durchstrahlten Bereich muss ein spezieller Film platziert werden, der die Informationen während des Versuchs speichert. Mittels eines Auslesegeräts können diese Informationen im Nachhinein digitalisiert und am Computer durch eine Software bearbeitet und ausgewertet werden. Bei der Auswertung zeigt sich, dass sich sowohl Luft- als auch Materialeinschlüsse ab einer gewissen Dicke farblich auf dem Bild abheben (vgl. Abbildung 7). Je höher die Dichte des eingeschlossenen Materials, desto eher wird es sichtbar. Dies ist gut beim Stahldraht zu beobachten, der auf dem Bild deutlich hervorsticht. Die PTFE-Folie, welche zum Simulieren von Kissing Bonds verwendet wird, kann mit diesem Verfahren nicht detektiert werden. Diese ist nur 0,1 mm stark und zeigt die Grenzen des Verfahrens auf. Die Fehlstellen haben erst ab einer definierten Dicke genug Einfluss auf die Röntgenstrahlen, um auf dem Film sichtbar zu werden. Die PTFE-Folie erweist sich als zu dünn, um mittels Röntgenstrahlung sichtbar gemacht werden zu können. Die anderen Fehlstellen können hingegen in sehr detaillierten Aufnahmen kenntlich gemacht werden. Jedoch erfordert dieses Verfahren viel Aufwand in Bezug auf die Sicherheit und den Personenschutz, welche durchgängig akribisch sichergestellt und überprüft werden müssen. Ein Überblick der beiden vorgestellten zfP sowie deren Eignung in Bezug auf die Detektion von definierten Fehlstellen in hochfesten Strukturklebstoffen ist in Tabelle 1 aufgeführt.

Tabelle 1: Eignung der zfP für Fehlstellen in hochfesten Strukturklebstoffen
Zusammenfassung und Fazit
In dieser dreiteiligen Artikelserie wurden zunächst typische Fehler und Imperfektionen in Klebverbindungen, wie sie u.a. im Schiffbau ausgeführt werden und auftreten können, ermittelt und geclustert. Zur Ermittlung des Schädigungspotenzials und der Kritikalität der Fehler wurden diese gegenüber fehlerfreien Klebverbindungen vergleichend bewertet. Dabei kam heraus, dass insbesondere große Volumen- und Adhäsionsfehler (Haftungsverlust zu den Substraten) die mechanischen Eigenschaften der Klebung signifikant degradieren können. Mit Hilfe der in diesem dritten Teil der Artikelserie vorgestellten und erwähnten zerstörungsfreien Prüfverfahren konnten Möglichkeiten aufgezeigt werden, sowohl volumenartige Imperfektionen als auch Adhäsionsfehler der Klebstoffe zu den Substraten zu detektieren. Mit der thermografischen Untersuchungsmethode konnten bei direkter Beobachtung der hochelastischen Klebschichtoberfläche Volumenfehler im Inneren der Klebschicht mit einem Durchmesser detektiert werden, der etwa der Tiefenlage des Fehlers entsprach (t = Ø 5mm). Bei hochfesten Strukturklebstoffen konnten sowohl mit der Schwingungsanalyse als auch mit der Röntgenprüfung verschiedenste Volumenfehler zuverlässig detektiert werden. Bei Adhäsionsfehlern, die sehr geringe Dicken aufweisen, kann dies mit der Röntgenprüfung nicht durchgehend gewährleistet werden.
Das IGF-Vorhaben Nr. 19870 BG „Inspektionsmethoden für die wiederkehrende Prüfung hochelastischer Dickschicht Ø und Strukturklebungen in Schiffbauanwendungen“ der Forschungsvereinigung Schiffbau und Meerestechnik e.V. (FSM) wird über die AiF im Rahmen des Programms zur Förderung der Industriellen Gemeinschaftsforschung (IGF) vom Bundesministerium für Wirtschaft und Energie aufgrund eines Beschlusses des Deutschen Bundestages gefördert.
Referenzen
[VAL17] Valeske, B., Nondestructive Characterization and Evaluation of Adhesive Bondings, Oral presentation, SIP-IMASM2017, https://www.tia-nano.jp/Other/SIP-IMASM/2017/materials/Oral/TIA-FhG-2_Valeske.pdf
[JÜN10] Jüngert, A.: Untersuchung von GFK-Bauteilen mit akustischen Verfahren am Beispiel der Rotorblätter von Windenergieanlagen, Dissertation, Universität Stuttgart, 2010, http://dx.doi.org/10.18419/opus-6342
[JEE17] .Jeenjitkaew C., Guild, F.J., The analysis of kissing bonds in adhesive joints, International Journal of Adhesion and Adhesives, Volume 75, June 2017, Pages 101-107
[GRE20]: Grellmann, W., Bierögel, C., Reincke, K. (Hrsg.), Wiki „Lexikon Kunststoffprüfung und Diagnostik“ 2020, Version 10, http://wiki.polymerservice-merseburg.de
Forschungseinrichtung 1:
Fraunhofer-Institut für Fertigungstechnik und Angewandte Materialforschung IFAM,
Bemen
Dr.-Ing. Oliver Klapp
E-Mail: oliver.klapp@ifam.fraunhofer.de
Tel.: +49 421 2246-479
Forschungseinrichtung 2:
Fraunhofer-Institut für Großstrukturen in der Produktionstechnik IGP,
Rostock
Christopher Wald
E-Mail: christopher.wald@igp.fraunhofer.de
Tel.: +49 381 49682-564