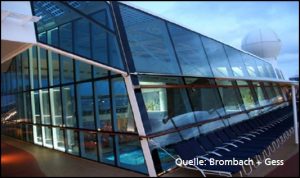
Abbildung 1: Scheibenklebungen im Kreuzfahrtschiffbau
Einleitung
Die Klebtechnik rückt als innovatives Fügeverfahren des 21. Jahrhunderts im Schiffbau zunehmend in den Vordergrund. Seinen Anwendern offeriert sie vielversprechende Vorteile, u.a. die Möglichkeiten, verschiedene Werkstoffe miteinander zu verbinden und Zusatzfunktionen wie Abdichtung, Isolation, Schwingungs- und Geräuschdämpfung elegant durch die Auswahl geeigneter Klebstoffe zu integrieren. Doch warum bleibt der Fügetechnik der große Durchbruch im Schiffbau aktuell noch verwehrt?
Problemstellung
Um die dauerhafte Zuverlässigkeit einer Klebverbindung im Betrieb sicherzustellen und Schadensfälle zu vermeiden, sind neben der sorgfältigen Planung und Ausführung, abhängig von den Sicherheitsanforderungen an die Klebverbindung, auch präventive Überwachungs- und Inspektionsmaßnahmen erforderlich. Denn beim Kleben handelt es sich gemäß der ISO 9001 um einen speziellen Prozess. Das bedeutet, dass der Fertigungsprozess nicht zu einhundert Prozent zerstörungsfrei prüfbar ist, da die Herstellung komplexen Randbedingungen unterliegt und Fertigungsfehler nie gänzlich auszuschließen sind. Entgegen des Bestrebens von Werften und Klebstoffherstellern, die Klebtechnik auch im Schiffbau weiter voranzutreiben, sind praktische Anwendungsfälle, mit Ausnahme der Scheibenverklebungen (vgl. Abbildung 1), eher selten und besitzen meist Unikatcharakter. Das resultiert aus der im Schiffbau fehlenden einheitlichen Festlegungen der Klassifikationsgesellschaften darüber, wie Klebverbindungen ausgelegt und ausgeführt werden sollten. Zudem fehlen Methoden und Erfahrungen, wie Schäden überhaupt erst erkannt werden können und welche Auswirkungen diese mit sich bringen. In anderen Industriezweigen ist das Kleben als Fügeverfahren für sicherheitsrelevante Verbindungen erprobt und weitaus etablierter. Dort liegen bereits entsprechende Erfahrungen und Richtlinien, wie z.B. im Schienenfahrzeug- [DIN 6701-Teil 4] oder Windenergieanlagenbau [Sachverständigenrat Bundesverband Windenergie e.V.: Grundsätze für die „Wiederkehrende Prüfung von Windenergieanlagen“. 2012], hinsichtlich der Qualitätssicherung vor. Eine Übertragbarkeit auf den Schiffbau ist aufgrund der oftmals nicht standardisierten Anwendungen und extremen Umgebungsbedingungen jedoch nicht ohne weiteres möglich. Aufgrund der regelmäßigen Dockung, die Schiffe z.B. im Vierjahres-Turnus durchlaufen müssen und in der sie umfänglich untersucht werden, könnten Wartungsintervalle für Klebverbindungen grundsätzlich leicht implementiert werden. Eine solche Regelung ist für Klebverbindungen momentan jedoch nicht vorhanden. Ohne diese Richtlinien mit Vorgaben zu anzuwendenden Prüfverfahren und -intervallen werden Fehler bzw. Imperfektionen, die aus der Herstellung oder aus dem betrieblichen Einsatz einer Klebung resultieren können, nur teilweise oder zu spät bzw. gar nicht erkannt, was dann zu unvorhersehbarem Versagen ggf. mit Sach- und sogar Personenschäden führen kann. Unter diesen Gegebenheiten leidet auch die Klebtechnik hinsichtlich des Einsatzes im Schiffbau, weshalb oft auf die konventionellen, durch langjährige Erfahrungen gestützten Fügeverfahren zurückgegriffen wird.
Zielsetzung des Forschungsprojekts
Um die Klebtechnik im Schiffbau weiter zu etablieren, haben das Fraunhofer Institut für Fertigungstechnik und angewandte Materialforschung (IFAM) in Bremen und das Fraunhofer Institut für Großstrukturen in der Produktionstechnik (IGP) in Rostock in Zusammenarbeit mit Vertretern aus der Industrie das Forschungsprojekt „Inspektionsmethoden für die wiederkehrende Prüfung hochelastischer Dickschicht- und Strukturklebungen in Schiffbauanwendungen (kurz: Klebschichtinspektionsmethoden) “ ins Leben gerufen. Das ausgewiesene Projektziel ist die Akzeptanz zum Einsatz der Klebtechnik im Schiffbau durch ein geeignetes Risikomanagement zu fördern und damit langfristig die Sicherheit von hochelastischen und strukturellen Klebverbindungen auch unter harschen maritimen Umgebungsbedingungen sicherzustellen. Hochelastische Dickschichtklebstoffe, wie sie beispielsweise vielfach beim Einkleben von Scheiben zur Anwendung kommen, unterscheiden sich hinsichtlich ihres Werkstoff- und Verformungsverhaltens von hochsteifen und -festen Strukturklebstoffen, die gegenwärtig als Halterungen für Ausrüstungsgegenstände oder als Bodenfundamente Anwendung finden. Die durchzuführenden Arbeiten werden daher im Hinblick auf die Klebstofftypen den jeweiligen Fachkompetenzen der Forschungsstellen eingegliedert. Das Fraunhofer IFAM ist während der Projektlaufzeit der primäre Ansprechpartner für die hochelastischen Dickschichtklebungen. Das Fraunhofer IGP widmet sich den strukturellen Klebungen. Um den größtmöglichen Nutzen für den Schiffbau zu erreichen, sieht der wissenschaftliche Lösungsweg bei der Bearbeitung des Projekts eine enge Zusammenarbeit mit der maritimen Branche, bestehend u.a. aus Werften, Klebstoffherstellern, Ausrüstern und einer regelsetzenden Klassifikationsgesellschaft, vor.
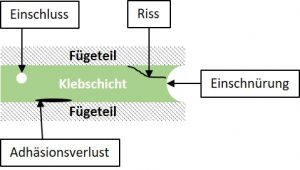
Abbildung 2: Charakteristische Schadenstypen einer Klebverbindung nach dem Herstellungsprozess
Identifikation und Klassierung typischer Schäden von Klebverbindungen
Um das Forschungsziel zu erreichen, müssen zunächst relevante Klebverbindungen im Schiffbau und anderen Branchen untersucht werden. Mittels Hospitationen, Besichtigungen und zusammen mit den Vertretern der maritimen Branche werden charakteristische Schadenstypen von Klebverbindungen im Herstellungsprozess und während des Betriebs identifiziert. Besonders kritisch sind dabei Imperfektionen, die unbewusst während des Herstellungsprozesses der Klebung in diese eingebracht werden. Diese können sich während des Betriebs vergrößern oder unterstützen die Bildung weiterer Fehlstellen, was sich negativ auf die mechanischen Eigenschaften der Klebverbindung auswirkt. Beispiele für Schäden im Herstellungsprozess sind Luft- und Materialeinschlüsse, Adhäsionsverluste oder Einschnürungen und Risse (vgl. Abbildung 2). Einschlüsse und Adhäsionsverluste lassen sich u.a. auf eine verunreinigte Klebumgegbung zurückführen. Einschnürungen können leicht in die Klebung gebracht werden, indem ein Arbeiter z.B. überschüssigen Klebstoff unachtsam mit einem Spatel entfernt und so Kerben in den Rand der Klebschicht bringt. Können derartige Schäden an geklebten Strukturen äußerlich entdeckt werden, besteht häufig Unklarheit darüber, wie in solchen Fällen weiter zu verfahren ist. Die gesammelten Fakten und Erfahrungen aus der Branche unterstreichen die Notwendigkeit eines geeigneten Risikomanagements, um Schäden frühzeitig zu erkennen und zu bewerten, so dass erforderliche Reparaturmaßnahmen entsprechend der Dringlichkeit eingeleitet werden können.
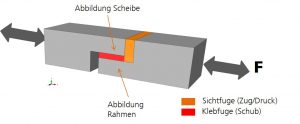
Abbildung 3: Bauteilähnliche Probe zur
Abbildung einer Scheibenklebung
Experimentelle Untersuchungen zur Ermittlung des Schädigungspotenzials
Um die Auswirkungen von unterschiedlichen Schäden auf die Klebverbindung zu untersuchen, werden vergleichende experimentelle Laborversuche an fehlerfreien und fehlerbehafteten Klebungen durchgeführt, um Abminderungsfaktoren und das Schädigungspotenzial spezifischer Imperfektionen ableiten zu können. Dabei ist es essentiell, Proben mit definierten Fehlstellen reproduzierbar herstellen zu können. Je nach Klebstofftyp werden Verfahren erarbeitet, um verschiedene Imperfektionen unterschiedlicher Ausprägung und Lage gezielt in die Prüfkörper einzubringen, um daraufhin deren Einfluss auf die mechanischen Eigenschaften zu untersuchen.
Für die Untersuchungen der Klasse der hochelastischen Dickschichtklebstoffe wird eine bauteilähnliche Probenform verwendet, die in dem AiF Projekt „Einbeziehung geklebter Fensterbänder und Glasfronten in die Festigkeit von Schiffen“ IFG Nr. 18465 N entwickelt worden ist (vgl. Abbildung 3). Nach Clusterung der im Feld beobachteten Klebfehler für diese Klebstoffklasse konnten vier typische generische Fehlerarten abgeleitet werden. Diese sind:
- „Volumenfehler“ in der Klebschicht und Sichtfuge, die Lufteinschlüsse oder unvollständig gefüllte Bereiche repräsentieren, ausgeführt als zylindrische Hohlräume über die gesamte Breite der Klebung mit verschiedenen Durchmessern (rote Bereiche in Abbildung 4, 1.).
- „Adhäsionsfehler“ in den Grenzschichten der Klebschicht und Sichtfuge zu den Fügeteilen repräsentieren einen Haftungsverlust, ausgeführt als kreisrunde zentrische Zonen mit unterschiedlichen Durchmessern und haftungsverhindernder Beschichtung (2.).
- „Riss-Fehler“ in der Klebschicht und Sichtfuge über die gesamte Breite der Klebung und mit unterschiedlicher Tiefe repräsentieren mechanische Beschädigungen (Einschnitte) oder einklebte z.B. Maskierfolien (3.).
- „Fehlbildung der Kleb- und Sichtfuge“ repräsentieren nicht passgenau gefügte Bauteile, dargestellt durch veränderte Überlappungslängen und Sichtfugenbreiten gegenüber der Referenzgeometrie (4.).
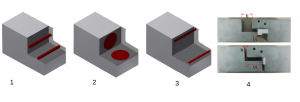
Abbildung 4: Generische Fehlerarten implementiert in Probeform aus Abbildung 3: 1: Volumenfehler, 2: Adhäsionsfehler, 3. Risse an freien Flächen und Kanten der Klebung, 4. Fehlbildungen der Kleb- und Sichtfuge
Im Rahmen des Projekts werden geeignete Fertigungsmethoden entwickelt, um die in Abbildung 4 dargestellten generischen Fehlerformen reproduzierbar in die bauteilähnliche Probenform einbringen zu können. So werden die Volumenfehler durch Passstifte, die in die Klebung mit eingearbeitet werden, realisiert. Nach Aushärtung des Klebstoffs lassen sich die Stifte, die zuvor mit einem Trennmittel behandelt wurden, leicht aus der Klebung entfernen, sodass der Volumenfehler entsteht. Adhäsionsfehler werden durch präzise herstellbare kreisrunde selbstklebende PTFE-Folien erzeugt, die auf die Klebflächen der Fügeteile aufgeklebt werden. Durch die niedrige Oberflächenenergie der Folien kann der Klebstoff keine nennenswerte Haftung dazu aufbauen. Risse werden mittels definierter Einschnitte unterschiedlicher Tiefe in den ausgehärten Klebstoff der Klebung eingebracht. Variationen der Überlappungslänge bzw. Sichtfugenbreite der bauteilähnlichen Probenform lassen sich durch Abstandhalter aus PTFE mit unterschiedlichen Breiten einfach und reproduzierbar realisieren.
Bei den Strukturklebstoffen werden, ähnlich zu den Fehlstellen bei hochelastischen Dickschichtklebungen, drei typische Fehlstellen auf die Auswirkungen auf die mechanischen Eigenschaften der Klebverbindungen untersucht:
- „Einschlüsse“ in der Klebschicht
- „Adhäsionsverlust“ in der Grenzschicht der Klebschicht
- „Einschnürungen“ im Randbereich der Klebschicht
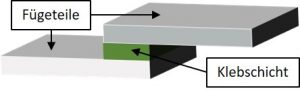
Abbildung 5: mit Klebstoff gefügte Aluminiumfügteile
Wie auf Abbildung 5 dargestellt, werden dazu zwei Aluminiumfügeteile miteinander verklebt und die Imperfektionen in die Klebschicht eingebracht. Die Fehlereinbringung wird nachfolgend erklärt und ist zudem schematisch in Tabelle 1 dargestellt.
Die Einschlüsse werden mit Hilfe von Polystyrolkugeln simuliert und sollen Gasblasen darstellen. Aufgrund ihres hohen Luftanteils und ihrer Form sind sie sehr ähnlich zu diesen. Die Polystyroleinschlüsse werden einerseits als Vollkugeln und andererseits als Halbkugeln in die Klebschicht gebracht. So schwächen sie sowohl die Adhäsions- (Halbkugeln) als auch die Kohäsionszone (Vollkugeln) der Klebung maximal. Die Polystyrolkugeln werden in verschiedenen Ausprägungen auf die Oberfläche des Fügeteils (Halbkugeln) bzw. in die Klebschicht (Vollkugeln) gebracht. Diese verdrängen somit ca. 2% bis 20% des ursprünglichen Klebstoffvolumens, abhängig von der Ausprägung.
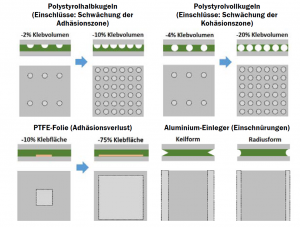
Tabelle 1: Imperfektionen in Klebverbindungen
(grau: Fügeteile | grün: Klebstoff | weiß: Einschlüsse/Einschnürungen | orange: PTFE-Folie)
Wie bei den hochelastischen Dickschichtklebstoffen wird Polyetrafluorethylen (PTFE)-Folie verwendet, um Adhäsionsverluste zu simulieren. Auch hier werden verschiedene Ausprägungen untersucht. Die PTFE-Folie verdeckt somit etwa 10% bis 75% der Klebfläche.
Weiterhin wird der Einfluss von Einschnürungen in der Klebschicht untersucht. Für dieses Projekt werden eine Keil- und eine Radiusform verwendet. Um diese in die Klebschicht zu bringen, werden Einleger aus Aluminium gefräst. Beim Aushärten des Klebstoffs können diese in die Bereiche, in denen Einschnürungen hervorgerufen werden sollen, eingebracht werden.
Mit Hilfe der vorgestellten Proben mit unterschiedlichen Fehlerausprägungen ist es möglich, diese systematisch zu untersuchen, um somit das Schädigungspotential zu ermitteln. Dazu sind die Proben in zerstörenden Versuchen zu untersuchen, um die mechanischen Eigenschaften der Klebverbindungen zu ermitteln. Die Beschreibung der Prüfungen sowie die daraus gewonnenen Erkenntnisse sind in dem weiterführenden Artikel „Inspektionsmethoden für die wiederkehrende Prüfung hochelastischer Dickschicht- und Strukturklebungen in Schiffbauanwendungen –Teil 2 (Ermittlung von Abminderungsfaktoren)“ in der nächsten Ausgabe dargestellt.
Autoren:
Oliver Klapp
E-Mail: oliver.klapp@ifam.fraunhofer.de
Tel.: +49 421 2246-479
Christopher Wald
E-Mail: christopher.wald@igp.fraunhofer.de
Tel.: +49 381 49682-564