Autoren: Dr. Wolf Georgi, Dr. Jonny Kaars, Reza Kaboli, Prof. Peter Mayr
Einleitung
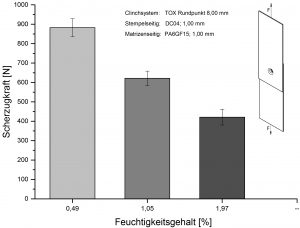
Abbildung 1: Maximal übertragbare Kräfte einer Einpunkt-Clinchverbindung zwischen Metall und Kunststoff in Abhängigkeit der Restfeuchte des Kunststofffügepartners zum Fügezeitpunkt
Die Fügetechnik ist nach DIN 8580 ein Teil der Fertigungsverfahren und hat die Aufgabe, Lösungen für das Verbinden verschiedenster Werkstoffe bereitzustellen. Die Palette der Fügeverfahren wird dabei ständig weiterentwickelt und an neue Werkstoffsituationen angepasst. Der aktuelle Trend zum Leichtbau stellt dabei auch große Herausforderungen an die Fügetechnik. So sind auf der einen Seite thermische Fügeverfahren zu nennen, die für hoch- und höchstfeste Stähle geeignet sein müssen oder an das Fügen von Leichtmetallen angepasst werden müssen. Auf der anderen Seite stehen mechanische Fügeverfahren, welche es ermöglichen metallische Werkstoffe, natürliche Werkstoffe oder auch Kunststoffe nicht nur mit sich selbst sondern auch untereinander zu verbinden. Die Auswahl, welches Fügeverfahren für die jeweilige Fügeaufgabe in der eigenen Produktion zu verwenden ist, stellt dabei eine große Herausforderung an die Produzenten dar. Die Professur Schweißtechnik an der Technischen Universität Chemnitz beschäftigt sich unter anderem mit Prozess-Struktur-Eigenschaftsbeziehungen bei Fügeaufgaben im Leichtbau. Im vorliegenden Artikel wird ein kleiner Einblick in verschiedene Projektschwerpunkte der Professur gegeben. Hierbei werden auch Themen angesprochen, die den Fügeprozess im Vorfeld und übergeordnet betrachten. Weiterführende Informationen sind unter https://www.tu-chemnitz.de/mb/SchweiTech/ zu finden.
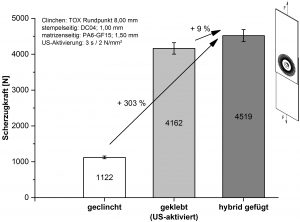
Abbildung 2: Steigerung der maximal übertrag-
baren Kräfte durch das Hybridfügeverfahren
Clinch-Schmelzkleben
Leichtbau beim mechanischen Fügen
Der Leichtbau nimmt immer mehr eine Schlüsseltechnologie, nicht nur im Bereich des Automobilbaus, ein. Der Werkstoffleichtbau stellt dabei eine Methode dar, bei welcher Schwermetalle durch dünnere hochfeste Metalle, durch Leichtmetalle oder durch Kunststoffe ersetzt werden. Die verschiedenen Materialien werden so in einem Produkt angeordnet und kombiniert, dass die jeweiligen Eigenschaften zu einer verbesserten Gesamtkonstruktion führen. Das Verbinden dieser artfremden Werkstoffe stellt dabei neue Herausforderungen an die Fügetechnik dar. Bisherige Lösungen sind oftmals nicht wirtschaftlich, energieintensiv, führen zu geringen Verbindungsfestigkeiten oder schädigen einzelne Werkstoffe.
Ein Forschungs- und Entwicklungsschwerpunkt der Professur Schweißtechnik ist das Weiterentwickeln von bestehenden Fügeverfahren, die beanspruchungsgerecht auf diese Werkstoffkombinationen abgestimmt werden. Als erstes Beispiel soll hier das Clinchen vorgestellt werden.
Das Clinchen ist ein seit Jahrzehnten in der Fügetechnik eingeführtes Fertigungsverfahren. Charakteristisch für das Clinchen ist eine überlappende punktförmige Verbindung. Es gibt eine große Varianz der Clinchverbindungsarten, wie z.B. das Rundpunktclinchen, das balkenförmige Clinchen oder auch einseitig flache Clinchverbindungen. Das dominierende Merkmal, welches den Bestand einer Clinchverbindung sichert, ist der Formschluß, welcher im Inneren der Verbindung durch einen so genannten Hinterschnitt gewährleistet wird. Für Metall-Kunststoff-Verbindungen wird das Clinchen bisher nicht großserientauglich eingesetzt. Dies liegt hauptsächlich daran, dass kalt umgeformte Kunststoffe zeitlich reversibel sind, das heißt sie relaxieren nach der Umformung mit der Zeit. Dieser Vorgang wird als Kriechen bezeichnet und läuft bei Kunststoffen bereits bei Raumtemperatur ab. Es kommt bei Nichtbeachtung dieser Eigenschaften zu einem sehr schnellen Lösen dieser Verbindungen.
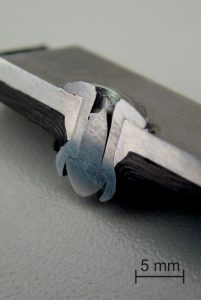
Abbildung 3: Querschliff einer FDR-Verbindung zwischen Magnesium und GFK
Eine Möglichkeit dies zu verzögern, ist das vorherige Einstellen des Kunststoffes auf eine bestimmte Restfeuchte. In umfangreichen Grundlagenuntersuchungen wurde nachgewiesen, dass eine Clinchverbindung zwischen Metall und konditioniertem Kunststoff nicht nur dauerhaft hält sondern auch um bis zu 50 Prozent höhere Lasten übertragen kann (Abbildung 1) [1, 3].
Eine weitere Steigerung der Lastübertragbarkeit solcher Verbindungen ist durch die Kombination zweier Fügeverfahren zu einem Hybridfügeverfahren realisierbar (Abbildung 2). Dabei wird zum Beispiel das mechanische Fügeverfahren Clinchen mit dem adhäsiven Fügeverfahren Schmelzkleben kombiniert. Beim Clinch-Schmelzkleben wird in einem speziellen Werkzeug koaxial zum Clinchpunkt ein Ultraschall torsional eingekoppelt, welcher den Kunststoff an der Grenzfläche zwischen Metall und Kunststoff örtlich aufschmilzt und eine Schmelzklebverbindung herstellt. Nach kurzer Schalleinwirkzeit kühlen die Fügepartner unter definiertem Druck ab. Das Clinchen kann vor oder nach dem Schmelzkleben erfolgen. Die Lastübertragbarkeit der hybrid hergestellten Verbindungen ist in Summe größer als die der jeweils elementar hergestellten Verbindungen. Weiterhin hat dieses Verfahren den Vorteil, dass die derart hergestellten Fügeverbindungen sofort einsatzbereit sind und mit sehr schnellen Taktzeiten hergestellt werden können. Weiterführende Informationen sind in [2] zu finden.
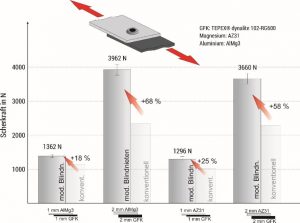
Abbildung 4: Vergleich der ertragbaren Lasten
zwischen FDR und herkömmlichen Blindnietver-
bindungen
Ein weiteres modernes Verfahren zum Verbinden von Metallen mit Kunststoffen mit und ohne Faserverstärkung ist das Flow-Drill- Riveting (FDR). Es handelt sich hierbei um ein modifiziertes Blindnietverfahren, welches kein vorheriges Lochen der Fügepartner benötigt. Der Verbinder (Niet) wird mittels Rotation durch die beiden Fügepartner getrieben. Durch eine spezielle Kopfgeometrie wird dabei das verdrängte Metall zu einer Hülse umgeformt, welche eine weitere Steigerung der ertragbaren Lasten einer derartigen Verbindung ermöglicht.
Es entstehen bei diesem Verfahren keine Späne und die Fügezeit beträgt lediglich ca. 2 Sekunden. Die ertragbaren Lasten liegen um ca. 60 % höher als bei herkömmlichen Blindnietverbindungen (Abbildung 4).
Dabei wird durch Formen, und nicht durch Bohren oder Stanzen, faserschonend ein Loch in den Kunststofffügepartner eingebracht. Die Fasern werden dadurch verdrängt und weniger Fasern durchtrennt.
Simulation
Numerische Simulationsverfahren nehmen heute für die Lösung komplexer Aufgaben ingenieurwissenschaftlicher Problemstellungen eine wichtige Position ein. Aufgrund der vielfältigen Anwendungsmöglichkeiten hat die numerische Simulation eine große Verbreitung gefunden und wird heute in vielen Bereichen der technischen Anwendungen erfolgreich angewandt. Auch für das Gebiet der Fügetechnik sind numerische Verfahren zur Lösung verschiedenster Problemstellungen nicht mehr wegzudenken. Sie ermöglicht die relativ rasche Durchführung von komplexen Berechnungen und die Betrachtung des Werkstoff- und Konstruktionsverhaltens unter verschiedenen Bedingungen und Belastungen. Die Numerische Simulation ist dabei ein wesentliches Werkzeug für die Entwicklung von Prozessen und Produkten für die Fertigungsplanung und verkürzt Entwicklungszeiten und -kosten.
In der Fügetechnik kann die Simulation prinzipiell in drei Gebiete unterschieden werden:
- Thermodynamische und kinetische Berechnungen zur Ermittlung des Werkstoffverhaltens
- Strömungsmechanische Berechnungen
- Strukturmechanische Berechnungen
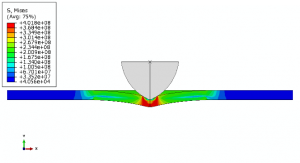
Abbildung 5.1: Berechnete Spannungsfelder des Durchdringungsvorganges beim FDR mittels eines
axialsymmetrischen Modelles
Im Zusammenhang mit der Entwicklung des oben vorgestellten FDR-Prozesses sind umfangreiche strukturmechanische Berechnungen mittels der Finite-Elemente-Software ABAQUS durchgeführt worden. ABAQUS ist ein kommerzielles Programmpaket, mit dem sich Probleme der Festkörper-Statik und -Dynamik, der Wärmeleitung, des Elektromagnetismus und der Fluiddynamik untersuchen lassen. Zudem betrachtet das FEM-Programm das Werkstoffverhalten unter verschiedenen Belastungen im thermomechanisch-gekoppelten Zustand. Zur detaillierten numerischen Betrachtung des Einflusses der Fügekopfgeometrien auf die Durchdringung und Hülsenausbildung wurden verschiedene Simulationsmodelle entwickelt. Dabei kamen im Wesentlichen drei verschiedene Modelle zum Einsatz. Ein axialsymmetrisches Modell (Abbildung 5) mit ALE-Vernetzung (arbitrary lagrangian eulerian) und ein dreidimensionales Modell mit CEL-Formulierung (Coupled Eulerian-Lagrangian), welche thermomechanisch gekoppelt waren. Weiterhin wurde der FDR-Prozess in verschiedene Teilmodelle zerlegt, um somit den Berechnungsaufwand zu reduzieren.
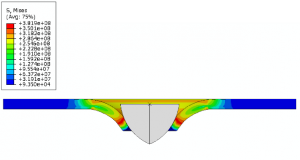
Abbildung 5.2
Bei der Simulation des Durchdringungsvorgangs des FDR-Prozesses wurden zwei unterschiedliche Ansätze betrachtet: die Lagrange- und die Euler-Formulierung. Die Lagrange-Formulierung bezieht sich auf Kontinuums Elemente, denen ein Material fest zugeteilt wird. Die Bewegung des Kontinuums wird als eine Funktion der Zeit und der Materialkoordinate definiert. Das Material des Elements bewegt sich in Abhängigkeit vom Stoffgesetz mit den Knoten mit. Dabei entsteht eine Verformung des Elements, sodass es leicht ist, freie Flächen zu verfolgen und Randbedingungen anzuwenden. Das Netz wird aber mit hohen Spannungsgradienten verzerrt und kann somit zu einem Berechnungsabsturz führen. Im Gegensatz dazu dient die Eulersche Vernetzung als Hintergrundvernetzung. Das Material bewegt sich durch das Netz und jedes Element erhält einen Füllgrad. Die Vernetzung selbst bleibt dabei gleich, während das Material sich innerhalb des Netzes verformt.
Leichtbau beim thermischen Fügen
Wenn von Leichtbau die Rede ist, denkt man in der Regel an Kohlefasern, Titan, komplizierte Bauteile, Rennsport oder vielleicht Luft- und Raumfahrt. Dabei sind wir täglich von zahlreichen Produkten umgeben, welche durch hochgradigen Leichtbau mit einem der ältesten Werkstoffe der Menschheit geprägt sind: Dem Stahl. Sicher, Stahl hat eine hohe Festigkeit, Stahlbauteile sind aber auch schwer, oder?
Die Belastbarkeit eines Bauteiles wird durch dessen Geometrie und den Werkstoff definiert: Aus der Bauteilgeometrie ergibt sich die einer Belastung zugeordnete mech. Spannung, welche als Beanspruchung des Werkstoffes wirksam wird. Der Werkstoff wiederum verfügt über nur eine begrenzte Beanspruchbarkeit, und begrenzt somit im Umkehrschluss den maximalen Betrag der Belastung. Wird diese überschritten, versagt das Bauteil. Demnach kann ein Bauteil seine vorgesehene Funktion erfüllen, indem durch angepasste Geometrie die Beanspruchung bis unter die Beanspruchbarkeit gesenkt wird, oder aber ein Werkstoff mit höherer Beanspruchbarkeit gewählt wird. Erstere Maßnahme erhöht i.d.R. das Bauteilvolumen und damit dessen Masse, die Zweitere bedingt meist Werkstoffe mit höherer Dichte. Also muss die Dichte mit einbezogen werden, wenn das Leichtbaupotential eines Werkstoffes bewertet werden soll, z.B. durch die spezifische Festigkeit (Festigkeit geteilt durch Dichte). Verschiedene klassische Leichtbauwerkstoffe haben diesbezüglich ganz unterschiedliche Eigenschaften, siehe Abbildung 6. Unerwartet wird der vermeintliche Primus ‚Kohlefaser‘ um Längen vom Polyethylen-Derivat „Dyneema“ übertroffen, die Metalle erreichen nur 5 % (AlMg1SiCu) bis 10 % (Ti6Al4V, 22MnB5) der spezifischen Festigkeit der Fasern.
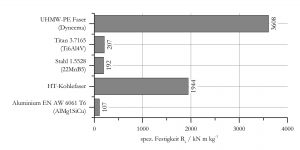
Abbildung 6: Spezifische Festigkeit verschie-
dener Leichtbauwerkstoffe
Dyneema wird bislang überwiegend als textiles Bauteil, d.h. als Seil oder Gurt sowie als Gewebematte, in Industrie, Luftfahrt und Sport eingesetzt. Die Herstellung fester Strukturteile als Faserverbund ist teuer, das Bruchverhalten spröd. Gleiches gilt für Kohlefasern. Aufgrund des Bruchverhaltens können die Bauteile kleine Beschädigungen in Betriebsalltag oder Produktion nicht einfach „wegstecken“, sondern müssen schon nach kleinen Blessuren vollständig ausgetauscht werden. Reparaturen sind nahezu unmöglich. Das Fügen von Faserverbünden ist teuer und erreicht an der Fügestelle selten die Festigkeit des Grundwerkstoffes. Daher sind Faserverbundbauteile als möglichst große, integrale Bauteile ausgelegt. Entsprechend groß ist der wirtschaftliche Schaden schon kleiner Beschädigungen. Es bleiben also die Metalle. Titan ist ein hochwertiger Leichtbauwerkstoff der auch höchsten Festigkeitsanforderungen entspricht und für die wichtigsten Umform- und Schweißverfahren geeignet ist. Allerdings sind der Werkstoff und seine Verarbeitung sehr teuer. Hauptgrund ist die große Affinität von Titan zu verschiedenen Gasen und Stoffen aus unvermeidlichen Schmutzanhaftungen. Peinlich genaue Sauberkeit und beste Formierung mit Schutzgas sind dementsprechend nötig. Aluminium ist wesentlich leichter zu verarbeiten und kostengünstiger, weist im Vergleich aber die schlechteste spezifische Festigkeit auf. Darüber hinaus hat Aluminium ein sehr schlechtes Rissauffangverhalten, d.h. einmal eingetretene Anrisse wachsen sehr schnell und das Bauteil kann versagen. So wurden fertigungsbedingte Mikrorisse an gestanzten Nietlöchern zusammen mit zu hoher Beanspruchung beispielsweise als Ursache einer Reihe von Abstürzen des Flugzeugmusters de Havilland Comet Mk. I in den 50er Jahren identifiziert. Daher muss die Beanspruchbarkeit von Aluminium in der Bauteilauslegung vergleichsweise konservativ angesetzt werden; in manchen Fällen verbietet sich der Einsatz von Aluminium ganz.
Überraschenderweise weist der vermeintliche Underdog, der Stahl, 92% der spezifischen Festigkeit des besten Metalles, dem Titan, auf. Allerdings kostet Stahl (gemessen am Schrottpreis) mit derzeit 0,15 €/kg nur etwa 3 % des Titans (5 €/kg). Das Element Eisen besitzt eine ausgeprägte Polymorphie, wodurch mittels Legierungselementen und Wärmebehandlung das jeweils benötigte Eigenschaftsprofil des Stahls gezielt gestaltet werden kann. Erst durch das Verfahren des Formhärtens ist z.B. der Einsatz höchstfester Legierungen in umformtechnisch hergestellten Bauteilen wirtschaftlich geworden. Das Fügen des Stahles auf dem Niveau der Grundwerkstofffestigkeit ist am wirtschaftlichsten durch Schweißen möglich, wobei jedoch immer auch das Eigenschaftsprofil des Grundwerkstoffes infolge der Schweißwärme verändert wird, meistens zum Schlechteren hin. Aus diesem Grund ist der Einsatz moderner Stähle immer im Hinblick auf die Fügeverfahren zu sehen. Beispielsweise erfolgt beim Widerstandspunktschweißen, dem wichtigsten Fügeverfahren der Automobilindustrie, die Wärmeeinbringung heute nach einem gezielten zeitlichen Profil, um so die Festigkeit und Duktilität der Fügestelle durch in-situ Wärmebehandlung zu verbessern. Anforderungen der industriellen Produktion, wie Beschichtungen, Toleranzen und Taktzeiten setzen diesen Maßnahmen enge Grenzen. Zeitgleich eröffnen neue Werkstoffkonzepte wie Quenched-Partitioning-Stähle neue Potentiale für den Leichtbauwerkstoff Stahl. In Zukunft wird daher der Druck auf die Fügetechnik zunehmen, durch intelligente Strategien der Wärmeeinbringung die spezifische Mikrostruktur des Grundwerkstoffes möglichst wenig zu verändern, oder noch besser, in-situ zu generieren. Diese Aufgabe ist nur lösbar, wenn zukünftig der Produktionsprozess als Ganzes gesehen, und Anforderungen der Fügetechnik von Anfang an in die Produktionsstrategie einbezogen werden, und umgekehrt. Nur auf diese Weise wird Stahl auch zukünftig ein kostengünstigster, aber auch hoch leistungsfähiger Leichtbauwerkstoff bleiben.
Literaturverzeichnis
[1] Brückner, E.; Georgi, W.; Gehde, M.; Mayr, P.: Relaxation Behavior of Metal-Polymer Hybrid Structures Mechanically Joined by Clinching. – In: ANTEC®2017: Conference Papers, ISBN: 978-0-692-88309-9, pp. 000-000, Anaheim, California USA, 2017
[2] Friedrich, S.; Georgi, W.; Gehde, M.; Mayr, P.: Hybrid Joining Technology – A New Method for Joining Thermoplastic-Metal-Mixed Components. – In: PROCEEDINGS OF PPS-29: The 29th International Conference of the Polymer Processing Society – Conference Papers, Volume number 1593, ISBN 978-0-7354-1227-9, Nürnberg, Deutschland, 2014
[3] Georgi, W.; Beitrag zum mechanischen Fügen von Metall-Kunststoff-Mischverbindungen. In Wissenschaftliche Schriftenreihe Chemnitzer Fügetechnik Band 1, Dissertation, ISBN 978-3-944640-15-0, Chemnitz 2014