Autor: Inès A. Melamies, Fachjournalistin, Bad Honnef
Moderne Nutzfahrzeugaufbauten werden heute in ihrer Struktur vollständig verklebt, um eine höhere Eigenfestigkeit und eine bessere Beständigkeit der Verbindungen bei geringeren Produktionskosten sicherzustellen. Auch resultiert diese Fügemethode in einer höheren Nutzlast sowie in einer Gewichtsreduzierung der Aufbauten, aus der wiederum eine Kraftstoffeinsparung und eine damit einhergehende Verminderung den CO2 Ausstoß über die gesamte Lebensdauer eines LKWs folgt. Die an das Strukturkleben gestellten Anforderungen sind hoch und nur mit einer zuverlässigen Vorbehandlung zu erfüllen.
Von den diversen Methoden für die Reinigung und Aktivierung von Materialoberflächen ist der Einsatz von umwelt- und gesundheitsgefährdenden Nass-Chemikalien weit verbreitet. Dass es aber auch umweltfreundlich und darüber hinaus weit effizienter geht, zeigt das Beispiel des Kühlfahrzeugeherstellers Schmitz Cargobull.

Bild 1: Moderne Kühlkofferaufbauten werden heute strukturell verklebt. Bei Europas führendem Hersteller wird bei der Vorbehandlung der Sandwichpaneele vor ihrer Verklebung auf organische Lösemittel schon seit vielen Jahren verzichtet.
Foto: Schmitz Cargobull AG
Bei Europas führendem Unternehmen für LKW-Auflieger wird bei der Vorbehandlung der Sandwichpaneele für die großen Kühlkofferaufbauten auf organische Lösemittel schon seit vielen Jahren verzichtet (Bild 1). Über 16000 neue Kühlsattelauflieger rollen heute im westfälischen Vreden jährlich vom Werkhof. Für eine umweltschonende, schnelle und prozesssichere Vorbehandlung der 13,50m langen, 2,60m breiten und 2,80m hohen Aufbauten kommt bei Wänden und Decken der Fahrzeuge vor dem strukturellen Klebprozess die Openair-Plasma-Technologie zum Einsatz.
Neue Hafteigenschaften
Das von Plasmatreat, Steinhagen 1995 entwickelte und heute weltweit eingesetzte atmosphärische Plasmaverfahren erfüllt bei dem Trailerbauer entscheidende Aufgaben: Integriert in den Produktionsprozess, sorgt es für eine mikrofeine Reinigung und simultane Aktivierung der zu verklebenden Oberflächen (Bilder 2 und 3). Bei einer Plasmaaktivierung wird die Oberfläche gezielt auf molekularer Ebene modifiziert. Dieser Effekt verleiht dem Material völlig neue Hafteigenschaften und bewirkt – ohne den zusätzlichen Einsatz von Chemie oder Aufrauprozessen – eine deutliche Erhöhung der Oberflächenenergie und eine daraus resultierende homogene Benetzbarkeit des Substrats.
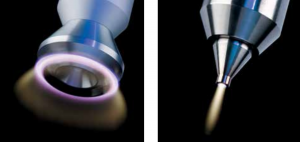
Bild 2+3: Die mikrofeine Reinigung und simultane Aktivierung der Paneeldeckschichten erfolgt bei
Schmitz Cargobull sowohl mit großflächig rotierenden (links) wie auch kontourgenau arbeitenden
statischen (rechts) Plasmadüsen.
Foto: Plasmatreat
Die Plasmabehandlung erlaubt Schmitz Cargobull die Verwendung lösemittelfreier Klebstoffe und sorgt für eine besonders hohe und langzeitstabile Haftung der Klebeverbindungen. Die auf einem Düsenprinzip basierenden Systeme arbeiten hier allesamt inline. Das Verfahren ist prozesssicher und reproduzierbar. Es läuft computergesteuert, mit hoher Geschwindigkeit und – anders als beim Niederdruckplasma (Vakuumkammer) – unter normalen Umgebungsluftbedingungen. An Verbrauchsstoffen werden für den Betrieb der Anlagen allein elektrische Energie und Druckluft benötigt, womit umweltschädigende VOC-Emmissionen gar nicht erst entstehen.
Vorbehandlung in nur einem Schritt
„Auf die Technologie von Plasmatreat wurden wir bereits vor etwa 15 Jahren auf einer internationalen Fachtagung aufmerksam“, berichtet Reinhard Beelmann, seit 25 Jahren bei Schmitz Cargobull und seit über 10 Jahren Technischer Leiter des Vredener Werks. „Die Leistungsmerkmale dieses damals noch jungen Vorbehandlungsverfahrens entsprachen exakt unseren Vorstellungen, die wir beim Bau einer neuen Verklebungsanlage realisieren wollten.“ Das primäre Ziel war, die bisher eingesetzten organischen Lösemittel im Klebprozess vollständig zu eliminieren und damit das mögliche Risiko einer Umweltbelastung von vornherein auszuschließen. Gleichzeitig sollten die bis dato manuelle Verrichtung der Oberflächenreinigung und das manuelle Aufrauen durch einen industriellen Prozess ersetzt werden. Die Bedingung: Beide Anforderungen sollte das neue Verfahren in einem einzigen Arbeitsschritt erfüllen können.
In Zusammenarbeit mit der Universität Kaiserslautern erfolgte zunächst eine sechs Monate dauernde Testphase. Die Schutzbeschichtung der metallenen Außendeckschicht der Sandwichpaneele besteht aus einem Polyester- bzw. Polyurethanlack. Messungen mit Testtinten ergaben, dass die Oberflächenspannung von 32 – 34mN/m im unbehandelten Zustand auf 42 – 44mN/m nach der Plasmaaktivierung angestiegen war. Dieselben Steigerungswerte zeigten sich auch auf der Hart-PVC-Folie, die die Beschichtung der Stahl-Innendeckschicht der Wand- und Deckenpaneele bildet. Getestet wurde neben den Wechselbeziehungen zwischen Atmosphärendruckplasma, 2K-Klebstoff und dem Werkstoff auch die Stärke eventueller Emissionen, da mehrere Plasmasysteme gleichzeitig zum Einsatz kommen sollten.
Rationalisierung in der Fertigung
Nach den zufrieden stellenden Testergebnissen, erfolgte die Projektierung der gesamten Anlagentechnik inklusive der Inline-Plasmaanlage und des Klebprozesses. Als 2003 die erste Großanlage mit Plasmabehandlung für das strukturelle Kleben von Kühlfahrzeugaufbauten bei Schmitz Cargobull in Betrieb genommen wurde, bedeutete diese neue Anwendung eine bahnbrechende Rationalisierung bei der Fertigung. Waren zuvor getrennte Arbeitsstationen erforderlich, konnten nun Vorbehandlung und Klebstoffbeschichtung in einem Arbeitsgang zusammengelegt werden, da das Plasmasystem in das Portal der Klebstoff – Misch- und Dosieranlage integriert worden war. Beelmann: „Die besonderen Vorteile der Plasmatechnik bestanden nicht nur in ihrer platzeinsparenden Einsatzweise und der großen Prozesssicherheit, sondern vor allem darin, dass aufgrund der Feinreinigung und hohen Aktivierung mittels Plasma, sowohl die Nassentfettung wie auch die Aufrauhung entfallen konnten. Durch die Substitution des Lösemitteleinsatzes konnte eine erhöhte Zufriedenheit bei unseren Mitarbeitern erreicht werden.“ Bereits ein Jahr später rüstete der Hersteller eine zweite Klebstation mit Plasmaanlagen aus.
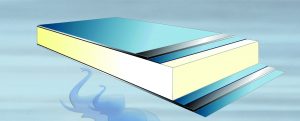
Bild 4: Die beschichteten Stahldeckschichten der patentierten Wand- und Deckenpaneele der Kühltransporter werden vor dem Verkleben mit Atmosphärendruckplasma vorbehandelt.
Bild: Schmitz Cargobull AG
Plasma auf großen Flächen
Die von Schmitz Cargobull gefertigten Kühlsattelauflieger sind selbsttragende Systeme, der gesamte modulare Aufbau erfolgt schrauben- und nietfrei. Die Klebetechnik schafft kraft- und formschlüssige Verbindungen ohne verlustreiche Wärmebrücken. Wände und Decken bestehen aus einer Sandwichkonstruktion. Hierbei handelt es sich um eine unter dem Namen Ferroplast patentierte dampfdiffusionsdichte Platte mit zwei beschichteten Stahlblech-Deckschichten (Bild 4) und einem dazwischen liegenden hochdichten Polyurethan-Hartschaumkern. Die selbsttragende Eigenschaft entsteht durch die Verklebung der Großpaneele in Aluwinkelschienen. Für eine besonders hohe Haltbarkeit und Dichtigkeit der Klebeverbindungen werden die Paneele im Bereich der Klebeflächen mit Atmosphärendruckplasma vorbehandelt.
Von den heute im Werk Vreden betriebenen vier Plasma-Behandlungsstationen, die über insgesamt 32 teils rotierende, teils statische Plasmaerzeuger verfügen, dient die erste ausschließlich der Vorbehandlung der Wand- und Deckenpaneele. Die Dreiachsanlage, mit dem integrierten Plasmasystem sowie dem Misch- und Dosierkopf für den Klebstoffraupenauftrag, läuft nach dem Aufrufen des Bearbeitungsprogamms zur Steuerung und der Einregelung des Abstandes zum Objekt vollautomatisch ab. Die Plasmaanlage selbst besteht aus zwei Düsensystemen, die jeweils rechts und links am äußeren Rand derselben Verfahreinheit montiert sind, auf der auch Misch- und Dosierkopf für den Klebstoffraupenauftrag sitzen.
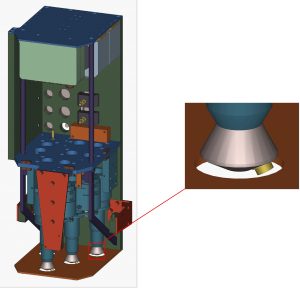
Bild 5: Speziell für die großflächige Anwendung konstruiert: Plasmasystem mit vier versetzt
angeordneten Rotationsdüsen, die das Plasma in einem Winkel von 45° bei einer Behandlungsbreite von 47mm pro Düse verteilen.
Bild: Plasmatreat
Jedes der beiden Systeme enthält vier versetzt angeordnete Rotationsdüsen. Nachdem ein Transportkran das Paneel abgelegt hat, setzt sich die Achse mit den nun aktiven Plasmadüsen in Bewegung und fährt mit einer Geschwindigkeit von 20m/min am äußeren Rand des Paneels entlang. Die speziell für großflächige Anwendungen konstruierten Rotationssysteme verteilen das Plasma in einem Winkel von 45° bei einer Behandlungsbreite von 47mm pro Düse (Bild 5). Je nach Richtung können so in einem Durchlauf 150–180mm der Oberfläche mikrofein gereinigt und aktiviert werden. Beelmann: „Es geht immer darum, durch die Vorbehandlung auf den kunststoffbeschichteten Stahlblechoberflächen einen zuvor festgelegten Referenzzustand herzustellen, denn es ist nicht auszuschließen, dass die Bauteile durch den Transport nicht doch feine Verunreinigungen aufweisen. Damit würden sie aber den Referenzanforderungen nicht mehr entsprechen.“
Die Vorbehandlung muss auf einer Mindestbreite von 300mm über die gesamte Länge bzw. Breite des Paneels erfolgen (Bild 6), was pro Wandpaneel 32,60m ausmacht. Dies ist die Fläche, auf die im direkten Anschluss drei Raupen 2K-PU (Polyurethan)- Klebstoff aufgetragen werden. Aus Sicherheitsgründen werden bei der Vorbehandlung großzügige Überlappungen einberechnet. Das Plasmasystem fährt insgesamt in drei Durchläufen über die zu verklebenden Flächen. Sofort nach Beendigung des Klebstoffauftrags übernimmt ein Transportkran die großen Paneele und legt sie in die nebenan wartenden Aluminiumprofile.
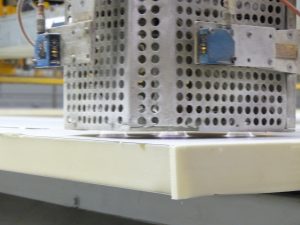
Bild 6: Die Vorbehandlung mit Plasma muss auf einer Mindestbreite von 300mm über die
gesamte Länge bzw. Breite des Paneels erfolgen. Foto: Schmitz Cargobull AG
Einsatz rund um die Uhr
Aufgrund der angestiegenen Nachfrage nach Kühlfahrzeugen baute Schmitz Cargobull in jüngster Zeit eine weitere Produktionshalle. Die kontinuierliche Fertigung wurde von Maschinenbauingenieur Beelmann platzsparend auf zwei übereinander liegenden Ebenen konzipiert, wobei die Bauteile vollautomatisch von der einen zur anderen Ebene transportiert werden. Gearbeitet wird im Drei-Schicht-Betrieb. In einem neuen Fertigungsprozess werden in der sogenannten Blechstrecke die Innen-Deckschichten der Paneele mit den Ladungssicherungs- und Doppelstockschienen aus verzinktem Stahl verklebt. Rund um die Uhr führen hier besonders kontourgenau und mit hoher Geschwindigkeit arbeitende statische Plasmadüsen millimetergenau die Vorbehandlung der Klebeflächen unmittelbar vor dem Klebstoffauftrag durch. Auch bei diesen Koffereinbauteilen wird durch die Plasmabehandlung ein zuvor festgelegter Referenzzustand hergestellt. Bei der weiteren Verarbeitung wird so sichergestellt, dass die Verklebung des umgeformten Stahls, welcher flächenbündig in die metallene Deckschicht des Paneels integriert wird, den Anforderungen sicher standhält (Bild 7). Bei einer mittleren Ausstattungsquote beträgt die Gesamtlänge der plasmabehandelten Flächen allein in diesem Fertigungsbereich circa 4,2 km pro Tag. Plasmatreat Key Account Manager Leonhard Enneking, der die Konzeption der Plasmaanwendung von Beginn an begleitete, zollt Lob: „Schmitz Cargobull“, so sagt er, „hat es geradezu meisterhaft verstanden, unsere Technologie direkt aus dem Stadium der Prozessentwicklung in seine anspruchsvollen Serienproduktionsanlagen zu integrieren.“
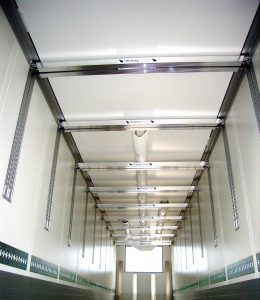
Bild 7: Die Ladungssicherungsschienen werden in die metallenen Deckschichten der Paneele flächenbündig integriert. Die Plasmavorbehandlung sichert die hohe Haftung der Klebverbindungen.
Foto: Blue Rondo International
Fazit
Die an eine strukturelle Verklebung im Fahrzeugbau gestellten Anforderungen sind hoch und nur mit einer zuverlässigen und reproduzierbaren Vorbehandlung zu erfüllen. Die Behandlung mit atmosphärischem Plasma ersetzt in diesem Bereich erfolgreich konventionelle Vorbehandlungen wie das mechanische Aufrauen und die Aktivierung mit umweltbelastenden Lösungsmitteln. Der Beitrag zum Umweltschutz, den Schmitz Cargobull bei der Fertigung der Kühlsattelauflieger leistet, ist beeindruckend: Mindestens 20 Tonnen Nasschemikalien im Jahr werden durch den Einsatz der Openair-Technik eingespart. Darüber hinaus ermöglichen die in den Prozessablauf integrierten Plasmasysteme nicht nur eine prozesssichere, sondern auch höchst effektive und wirtschaftliche Vorbehandlung.
Kontakt: www.plasmatreat.de
Weitere Informationen: www.cargobull.com