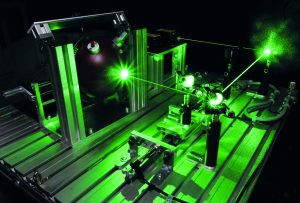
Abbildung 1: Versuchsaufbau zur Messung des Einkoppelgrades mithilfe einer Ulbrichtkugel
Anhand innovativer Systemtechnik soll die Prozesseffizienz und die Schweißnahtqualität beim Laserstrahlschweißen von Kupferwerkstoffen gesteigert werden. Hierzu wird im Rahmen des Forschungsprojektes ProLasKu von der TRUMPF Laser GmbH eine neuartige Strahlquelle entwickelt. Diese emittiert im grünen Wellenlängenbereich mit einer Ausgangsleistung von bis zu 1,5 kW. Um die Vorteile von grüner Laserstrahlung darzulegen, wurden am iwb Methoden zur Beurteilung der Effizienz und der Stabilität des Schweißprozesses entwickelt.
Ressourcenschonendes Fügen von Kupferbauteilen mit grüner Laserstrahlung
Durch den zunehmenden Trend hin zu erneuerbaren Energien und zur Elektromobilität herrscht in diesen Industriezweigen ein steigender Bedarf an dem Werkstoff Kupfer. Speziell die Fügetechnik spielt bei der Verarbeitung von Kupfer eine große Rolle, wobei Laserstrahlschweißen wegen der kurzen Prozesszeiten und der hohen Flexibilität an Bedeutung gewinnt. Bei der Verwendung von herkömmlichen Laserstrahlquellen stellt das Laserstrahlschweißen von Kupfer aufgrund der physikalischen Eigenschaften dieses Werkstoffs eine große Herausforderung dar. Neben der großen Wärmeleitfähigkeit ist der geringe Absorptionsgrad besonders problematisch. Dieser beträgt bei Raumtemperatur für infrarote Laserstrahlung (1030 nm) weniger als 5 %, bei grüner Laserstrahlung (515 nm) liegt dieser jedoch bei ca. 35 %. Um diesen Vorteil der erhöhten Absorption nutzen zu können, wird von der Firma TRUMPF Laser GmbH eine im grünen Wellenlängenbereich emittierende Strahlquelle entwickelt, mit welcher eine Ausgangsleistung von bis zu 1,5 kW im Dauerstrichmodus möglich ist. Der Einsatz dieser Strahlquelle verspricht einen effizienten Schweißprozess, es wird also ein großer prozentualer Anteil der Strahlleistung im Werkstück in Wärme umgesetzt. Zudem wird ein deutlich vermindertes Auftreten von Schweißspritzern erwartet. Um diese Vorteile zu belegen, wurden am iwb ein Versuchsaufbau zur Messung der Einkoppelgrade, ein numerisches Modell zur Bestimmung der Prozesseffizienz und ein kamerabasiertes Prozessüberwachungssystem erarbeitet. Im Folgenden werden diese Methoden nach einer kurzen Vorstellung der Strahlquelle näher beschrieben.
Entwicklung einer grünen Strahlquelle
Die Grundlage des neuen Lasersystems besteht in der Technologie eines frequenzverdoppelten Scheibenlasers mit kontinuierlich emittierender Laserstrahlung. Mit Hilfe aufeinander abgestimmter optischer Bauelemente im Resonator und gleichzeitiger Entwicklung neuer Komponenten zur Wellenlängenstabilisierung wird eine bisher nicht erreichte Laserleistung im grünen Wellenlängenbereich realisiert. Neben der Strahlquelle wird auch ein geeignetes Scannersystem für den entsprechenden Wellenlängenbereich entwickelt. In der aktuellen prototypischen Umsetzung steht eine Ausgangsleistung von 1 kW zur Verfügung. Zum Ende der Projektlaufzeit (Ende 2019) soll die Leistung bis auf 1,5 kW gesteigert werden.
Vergleich der Einkoppelgrade von grüner und infraroter Laserstrahlung
Um das Potential von grüner Laserstrahlung darlegen zu können, wurde der Einkoppelgrad am Werkstoff Kupfer experimentell für infrarote und grüne Laserstrahlung untersucht. Der Einkoppelgrad definiert sich über das Verhältnis der vom Werkstück absorbierten Energie zur Energie der Laserstrahlung. Durch die hohe Leistungsklasse bildet sich eine Dampfkapillare aus, was charakteristisch für einen Tiefschweißprozess ist. Innerhalb dieser Dampfkapillare wird der Laserstrahl mehrfach reflektiert und an den Wandungen absorbiert. Aus diesem Grund ist der Einkoppelgrad bei einem Tiefschweißprozess gegenüber einem Wärmeleitungsschweißprozess deutlich gesteigert und hängt direkt von dem Aspektverhältnis (Tiefe/Breite) der Dampfkapillare ab. Für die messtechnische Bestimmung des Einkoppelgrades wurde ein Versuchsstand (siehe Abbildung 1) aufgebaut, um das Werkstück sowohl mit grüner als auch mit infraroter Strahlung bestrahlen zu können.
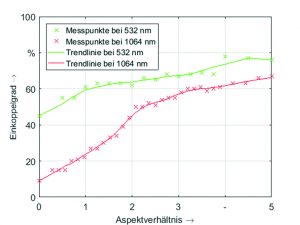
Abbildung 2: Gemessener Einkoppelgrad für infrarote und grüne Laserstrahlung in Abhängigkeit des Aspektverhältnisses
Als Strahlquellen dienten Diodenlaser mit einer maximalen Ausgangsleistung von 300 mW. Die Reflexionen wurden mithilfe einer Ulbrichtkugel gemessen. Dabei handelt es sich um eine innen diffus reflektierende Hohlkugel mit drei Öffnungen. An einer Öffnung wird das Werkstück befestigt. Durch die zweite Öffnung wird das Werkstück mit der Laserstrahlung beleuchtet, so dass im Inneren der Kugel ein homogenes Lichtfeld entsteht. Dieses kann durch einen Detektor an der dritten Öffnung gemessen werden, wodurch die gesamte reflektierte Laserstrahlung erfasst wird. Ziel der Untersuchungen war es, den Einfluss des Aspektverhältnisses der Dampfkapillare auf den Einkoppelgrad zu untersuchen. Die Dampfkapillare wurde dabei durch ein Bohrloch abgebildet. Die Bohrtiefe wurde in Schritten von 0,1 mm erhöht und es wurde jeweils der Einkoppelgrad für grüne und infrarote Laserstrahlung gemessen. Die Messpunkte sowie die dazugehörigen Trendlinien dieser Messreihen sind in Abbildung 2 dargestellt.
Ohne Bohrloch (Aspektverhältnis = 0) geben die Messwerte sehr gut die theoretischen Werkstoffkennwerte für reines Kupfer wieder, wobei der Absorptionsgrad der grünen Laserstrahlung deutlich oberhalb dem der infraroten Laserstrahlung liegt. Mit steigendem Aspektverhältnis lässt sich bei beiden Kurven ein Anstieg des Einkoppelgrades erkennen, was sich auf die Mehrfachreflexionen zurückführen lässt. Für größer werdende Aspektverhältnisse nähern sich beide Kurven einander an, jedoch zeigt sich stets ein höherer Einkoppelgrad für grüne Laserstrahlung. Die Untersuchungen belegen somit das große Potential grüner Laserstrahlung zum Schweißen von Kupferwerkstoffen.
Bewertung der Prozesseffizienz
Neben dem Einkoppelgrad gilt es auch den thermischen Wirkungsgrad zu untersuchen. Dieser gibt das Verhältnis der zum Aufschmelzen verwendeten Energie zur insgesamt absorbierten Energie wieder und ist besonders bei Kupferwerkstoffen aufgrund der hohen Wärmeleitfähigkeit von großer Bedeutung. Zur Untersuchung wurde ein numerisches Prozessmodell aufgebaut, mit dem für eine fest vorgegebene Dampfkapillare das Temperaturfeld berechnet wird. Hierbei wird die Schmelzbadströmung berücksichtigt, indem die thermische Konvektion, die Marangonie-Konvektion und die Metalldampf-Konvektion simuliert werden. Anhand der berechneten Schmelzbadgeometrie wird der thermische Wirkungsgrad ermittelt. In Abbildung 3 sind für unterschiedliche Schweißgeschwindigkeiten die Verläufe des thermischen Wirkungsgrades in Abhängigkeit der Einschweißtiefe dargestellt. Dabei gilt es zu beachten, dass eine tiefere Dampfkapillare in einer erhöhten absorbierten Energie (vgl. Abbildung 2) resultiert.
In Bezug auf einen effizienten Schweißprozess ist somit eine große Einschweißtiefe wünschenswert. Diese resultiert neben dem gesteigerten Absorptionsgrad auch in einem erhöhten thermischen Wirkungsgrad. Eine steigende Vorschubgeschwindigkeit wirkt sich ebenfalls positiv auf den thermischen Wirkungsgrad aus, jedoch muss beachtet werden, dass dies mit einer verringerten Einschweißtiefe einhergeht. Der erhöhte Absorptionsgrad von grüner Laserstrahlung im Vergleich zu infraroter Laserstrahlung resultiert bereits bei geringen Laserleistungen in einer größeren Einschweißtiefe, was sich positiv auf die Energieeffizienz auswirkt.
Bewertung der Prozessstabilität
Das Fügen von Kupferwerkstoffen ist besonders für die Fertigung von elektrisch leitenden Bauteilen von großer Bedeutung. In diesem Anwendungsgebiet werden im Hinblick auf die hohe Prozessgeschwindigkeit und die flexible Strahlpositionierung bevorzugt Scanner-Optiken eingesetzt. Bei diesem Remoteprozess gilt es insbesondere, Poren und Schweißspritzer zu vermeiden. Dadurch wird einerseits sichergestellt, dass die Schweißverbindung die gewünschte Leitfähigkeit erreicht. Andererseits werden durch Spritzer bedingte Kurzschlüsse auf dem Bauteil ausgeschlossen. Um eine Inline-Prozessüberwachung hinsichtlich der Schweißspritzer zu ermöglichen, wird die Prozesszone mit einer Kamera koaxial durch die Schweißoptik beobachtet. Die Kamera wurde für Spritzer mit einem minimalen Durchmesser von 100 µm und einer maximalen Geschwindigkeit von 10 m/s ausgelegt. Die speziell für diese Anwendung entwickelte Software ermöglicht eine Auswertung der Aufnahmen in Echtzeit. Eine große Herausforderung war dabei die robuste und vollautomatisierte Ermittlung der Spritzergröße und der Spritzeranzahl. Anhand dieser beiden Größen wird für jeden Schweißprozess eine Qualitätskennzahl berechnet. Diese erlaubt dem Anwender eine sofortige Identifizierung von Bauteilen, welche den Qualitätsanforderungen nicht genügen. Zusätzlich können die Qualitätskennzahlen in einer Datenbank abgespeichert werden, was dem Anwender einen Qualitätsnachweis ermöglicht. Mit diesem System ist es zukünftig möglich, den Nachweis zu erbringen, dass mithilfe grüner Laserstrahlung der Schweißprozess nicht nur effizient, sondern auch spritzerarm ausgelegt werden kann.
Zusammenfassung
Durch die zunehmende Elektrifizierung im Bereich der Individualmobilität und den Trend zu erneuerbaren Energien steigt der Bedarf an Kupferwerkstoffen. Deren industrielle Verarbeitung erfordert eine effiziente Produktionstechnik, welche besonders in der Fügetechnologie eine große Herausforderung erfährt. Eine mögliche Lösung stellt der Einsatz einer im grünen Wellenlängenbereich emittierenden Laserstrahlquelle dar. Grüne Wellenlängen werden von Kupfer deutlich besser absorbiert als infrarotes Laserlicht, was zu einem effizienten und robusten Prozess führt. Es konnte gezeigt werden, dass besonders für kleine Aspektverhältnisse der Dampfkapillare der Einkoppelgrad für grüne Laserstrahlung deutlich größer ist als für infrarote Laserstrahlung. Anhand eines numerischen Simulationsmodelles wurden zudem effiziente Prozessparameter identifiziert. Neben den Effizienzbetrachtungen wurde ein Inline-Überwachungssystem entwickelt, welches Rückschlüsse auf die Prozessstabilität durch die automatisierte Zählung der Schweißspritzer zulässt.
Danksagung
Das diesem Bericht zugrundeliegende Vorhaben wurde mit Mitteln des Bundesministeriums für Bildung, und Forschung unter dem Förderkennzeichen 13N13916 gefördert. Die Verantwortung für den Inhalt dieser Veröffentlichung liegt bei den Autoren.
Autoren
Andreas Ganser, Martin Haubold, Michael F. Zäh
Institut für Werkzeugmaschinen und Betriebswissenschaften
Boltzmannstraße 15
85748 Garching b. München
www.iwb.mw.tum.de