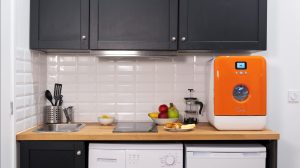
Bild 1: Der Geschirrspüler Bob
Bob, das ist nach den Worten der Erfinder „der kleinste Geschirrspüler der Welt!“. Das Gerät wurde von der Daan Technologies SAS entwickelt und zielt nicht nur auf kleine Haushalte, sondern auch auf den Camping- und Freizeitmarkt ab. Neben den geringen Abmessungen ist an Bob vor allem interessant, dass er ohne feste Installation auskommen kann und über neueste Netzwerktechnologie verfügt. Für die Produktion der Reinigungskartusche „Bob Cassette“ setzt das Unternehmen auf das wirtschaftliche Laser-Kunststoffschweißen.
Das französische Unternehmen Daan Technologies SAS, das innovative elektronische Geräte entwickelt, herstellt und vermarktet hat mit dem kleinen Geschirrspüler Bob den Zeitgeist getroffen und setzt neue Maßstäbe. Mit Abmessungen, die etwas größer sind als die einer Mikrowelle passt der Geschirrspüler nahezu überall hin, d.h. nicht nur in die Küche, sondern auch auf den Messestand oder in das Wohnmobil. Bob zeichnet sich insbesondere dadurch aus, dass er auch autonom ohne Wasseranschluss betrieben werden kann. Dafür ist das Gerät mit einem Wassertank ausgestattet, der bequem von vorne befüllt wird. Alternativ kann Bob auch mit einer Wasserversorgung betrieben werden.
Der Minigeschirrspüler glänzt auch noch durch weitere Punkte, so kann er das tägliche Geschirr für ein bis zwei Personen innerhalb von 20 Minuten abwaschen. Dabei verbraucht er dafür fünf Mal weniger Wasser als beim Abwaschen von Hand. Und natürlich meistert Bob auch die ökologischen Anforderungen, die heute an solche Produkte gestellt werden. Er ist für eine Lebensdauer von mindestens zehn Jahren ausgelegt und besteht teilweise aus recyceltem Kunststoff.
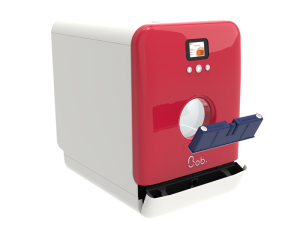
Bild 2: Bob mit Bob Cassette (Daan Technologies SAS)
Kernelement von Bob ist die optionale Bob Cassette, eine Kartusche zur Abgabe von Geschirrspülmittel. Dadurch muss man nicht bei jedem Spülgang aufs Neue Spülmittel hinzufügen, da die Cassette für 30 Spülgänge alles im Griff hat. Sie enthält bereits das Spülmittel und einen Klarspüler. Was einfach klingt, ist in der technischen Umsetzung eine anspruchsvolle Aufgabe. Die Kammern enthalten neben den Reinigungsflüssigkeiten auch eine kleine Elektronik, die für die Steuerung der Spülmittelzufuhr und die Füllstandsmessung zuständig ist. Alle drei Kammern müssen somit zu 100% zuverlässig gegeneinander abgedichtet sein, um Ausfälle und Leckagen zu verhindern. Da die Cassette von einer großen Anzahl von Endkunden genutzt wird, ist außerdem die Festigkeit der Schweißverbindung von entscheidender Bedeutung. Ein weiterer Clou der Cassette ist die Wiederverwendbarkeit. Leere Cassetten können zurück ins Werk geschickt und dort neu befüllt werden, was durch eine zuverlässige und langlebige Schweißverbindung erst ermöglicht wird.
Für das Laserschweißen der Baugruppe sprachen neben der kurzen Taktzeit insbesondere der geringe Platzbedarf des Fügeverfahrens sowie die hohe Prozesssicherheit und die Möglichkeit, den Prozess online zu überwachen. Auch die Werkzeugkosten für einen Laserschweißprozess sind im Vergleich zu Alternativverfahren gering, Verbrauchsmaterial benötigt das Verfahren nicht. Herkömmliche Schweißverfahren wurden nicht weiter in Erwägung gezogen, da sie die Anforderungen an die erforderlichen Genauigkeiten nicht erreichen und für die innenliegende Elektronik ein Risiko darstellen. Durch die sehr geringe Wärmeeinflusszone bei der Laserbearbeitung können die geforderten engen Toleranzen eingehalten werden. Da die Energieeinbringung berührungslos erfolgt werden empfindliche Elektronikbaugruppen durch den Schweißprozess nicht beeinträchtigt.
Das Laserschweißen von Kunststoffen wird heute überwiegend im Durchstrahlverfahren eingesetzt. Dabei wird die Laserstrahlung durch den für die Laserwellenlänge transparenten Kunststoff hindurch auf das absorbierende Formteil fokussiert, wodurch es oberflächlich aufschmilzt. Über Wärmeleitung wird auch der transmissive Partner plastifiziert, so dass es zu einer Verbindung kommt. Während des Schweißvorgangs müssen die beiden Fügepartner gespannt werden.
Beim Laser-Kunststoffschweißen wird zwischen Kontur-, Simultan- und Quasisimultanschweißen unterschieden. Für die Bob Cassette wird das Quasisimultanschweißen eingesetzt. Das bedeutet, der Laser wird mit sehr hohen Geschwindigkeiten entlang der Schweißkontur geführt. Ziel dabei ist es, die Kontur mehrfach so schnell abzufahren, dass die Schweißnaht quasi gleichzeitig erwärmt und aufgeschmolzen wird. Dadurch bietet sich die Möglichkeit, einen Fügeweg zum Ausgleich von Formteiltoleranzen zu überbrücken.
Bei der Materialauswahl fiel die Entscheidung auf ein Polypropylen-Copolymer. Neben der geringen Feuchtigkeitsaufnahme zeichnet sich dieser Werkstoff durch eine hervorragende chemische Beständigkeit, insbesondere gegen Löse- und Entfettungsmittel aus. Um sowohl den optischen Ansprüchen des Herstellers als auch den Anforderungen des Schweißprozesses gerecht zu werden, hat man sich für ein schwarzes Gehäuse und einen weißen Deckel entschieden.
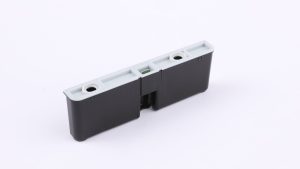
Bild 3: Ansicht der Bob Cassette (EVOSYS)
Aufgrund des kompakten Aufbaus der Cassette und der Schweißverbindungen zwischen den einzelnen Kammern, können für den Prozess keine normalen Spannwerkzeuge eingesetzt werden (Bild 3). Geschweißt wird mit der MICD-Technologie, d.h. ein sogenanntes Spiegelwerkzeug leitet den Laserstrahl mittels standardisierter Spiegelelemente auch in schwer zugängliche Zonen des Schweißbereichs. Diese robuste Technik wird seit Jahren erfolgreich in Serienprozesses eingesetzt. Für die Fertigung des Bauteils wurde in Zusammenarbeit mit dem Anlagenhersteller ein geeignetes Produktionssystem ausgewählt. Die Cassette, bestehend aus Gehäuse, Elektronik und Deckel muss in der Einlegestation montiert und danach in einer zweiten Station geschweißt werden. Die Aussortierung von Gut- und Schlechtteilen erfolgt ebenfalls in der Einlegestation.
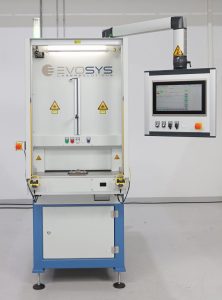
Bild 4: Kundenangepasste Laserschweißstation EVO 2800 (EVOSYS)
Aufgrund unterschiedlicher Varianten und der manuellen Bestückung ist ein Komplettsystem prädestiniert für die Produktion. Die kompakte EVO 2800 der Evosys Laser GmbH eignet sich aufgrund des intuitiven Bedienkonzepts, der leichten Prozessumstellung mittels der Prozesssoftware EvoLaP und der integrierten Prozessüberwachung besonders. Die Laserschweißanlage greift auf standardisierte Out-of-the-box Module aus dem Sortiment des Schweißanlagenherstellers zurück.
Zentrales Modul des Systems ist der Laser mit nachfolgender Strahlformung und -führung. Der Strahl wird mit einem speziellen Optikaufbau in einen Galvanometerscanner geleitet. Danach folgt eine F-Theta-Linse, die den Strahl in die Bearbeitungsebene fokussiert. Dabei wird der Strahl, wie zuvor beschrieben, über ein Spiegelwerkzeug in den Schweißbereich geführt.
Ein weiteres für die Fertigung unerlässliches Modul ist die Positionier- und Spanneinheit für die beiden zu fügenden Bauteile. Wechselbare, bauteilspezifische Aufnahmen und Spannbrillen sorgen für eine exakte Positionierung der Bauteile vor dem Schweißvorgang. Sobald beide Fügeteile in der korrekten Lage sind, erfolgt das Spannen mit einem Pneumatikzylinder, der die gesamte Baugruppe von unten gegen die Spannbrille drückt und die erforderlichen Kräfte für den Schweißprozess dosiert. Während des Schweißvorgangs erfolgt eine Online-Prozesskontrolle mittels Fügewegüberwachung. Der reine Schweißvorgang benötigt trotz der anspruchsvollen Geometrie nur etwas mehr als drei Sekunden.
Eine benutzerfreundliche Bedienung der Anlage im Produktionsalltag gewährleistet das Human-Machine-Interface auf Basis einer Industrie-SPS. Die HMI übernimmt auch die Visualisierung und Auswertung der Prozessdaten, die Speicherung von Datensätzen und weitere Systemfunktionen. Ergänzt durch die Kontursoftware EvoLaP wird die Flexibilität der Anlage erhöht. Der Anwender kann schnell die Daten für Schweißkontur, Vorschubgeschwindigkeiten und Laserleistung einprogrammieren. Aufgrund der intuitiven Bedienoberfläche, die speziell für die Nutzung auf Touchbildschirme ausgelegt ist, kann der Benutzer direkt starten.
Fazit
Die Herstellung der Cassette für den Bob zeigt, dass das Laserschweißen ein extrem zuverlässiges Verfahren ist. Die Erfahrungen in der Serienproduktion – sowohl mit dem Verfahren Laserschweißen von Kunststoffen, als auch mit der eingesetzten Schweißanlage EVO 2800 – sind durchweg positiv. Der saubere und robuste Prozess garantiert eine hohe Ausbringung und die Anlage selbst zeigt eine hohe Verfügbarkeit bei extrem niedrigen Folgekosten. Dazu tragen der wartungsarme Laser und die zuverlässigen mechanischen und elektrischen Komponenten bei.
Autoren:
Dipl.-Ing. Frank Brunnecker, Geschäftsführer & Gesellschafter, Evosys Laser GmbH
Dipl.-Ing. Christian Ebenhöh, Key Account Manager, Evosys Laser GmbH