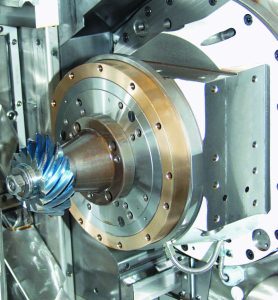
Bild: The Timken Company
Vertikale und horizontale Bearbeitungszentren sehen sich unterschiedlichsten Anforderungen ausgesetzt. Durch die Auswahl eines Lagers, das zur Erfüllung dieser Anforderungen konfiguriert ist, sowie durch seine ordnungsgemäße Installation lassen sich sowohl die Produktivität als auch die Leistung verbessern.
Produktivität ist ein Maß dafür, wie effizient wir Inputs in nützliche Outputs umsetzen können. Übertragen auf die Welt der maschinellen Bearbeitung lässt sich die Produktivität eines Prozesses zum Metallabtrag am besten steigern, indem die Zykluszeit reduziert und ungeplante Ausfallzeiten sowie Ausschuss eliminiert werden. Oder anders ausgedrückt: Wenn Sie mehr Produkte zu niedrigeren Stückkosten ausliefern, erhöhen Sie Ihren Gewinn.
Im ersten Teil dieses Beitrags beschrieb ich, wie sich durch die Auswahl der richtigen Lagerkonfiguration für die Spindel eines CNC-Bearbeitungszentrums die Leistung optimieren lässt. Eine unsachgemäße Installation oder die Verwendung der falschen Lagerausführung und -konfiguration kann die Zykluszeit steigern und möglicherweise sogar zum Totalausfall der Maschine führen.
In Fortsetzung dieser Veröffentlichung befasst sich der vorliegende Artikel mit acht wesentlichen Faktoren, die zur Maximierung der Bearbeitungsproduktivität optimiert werden können.
Nr. 1: Arbeitszyklus: Egal, ob Sie ein Konstrukteur von Werkzeugmaschinenspindeln eines Erstausrüsters oder eines Instandhaltungs-, Reparatur- und Überholungsdienstes sind – die Anforderungen der Endanwendung sind von entscheidender Bedeutung für die Lagerauswahl.
Die Lagerauswahl beginnt mit der Festlegung des Arbeitszyklus für den CNC-Automaten während der Produktion. Der Arbeitszyklus umfasst alle Vorgänge des Fräsens, Drehens, Bohrens, Gewindebohrens oder weitere Betriebsschritte innerhalb des Maschinenzyklus. Der Begriff Zykluszeit bezieht sich auf die Zeit, die zur Durchführung dieser Arbeiten benötigt wird.
Wie bereits erwähnt, kann ein Arbeitszyklus ein breites Spektrum von Betriebsschritten umfassen, die von Schrupparbeiten (hohe Lasten, niedrige Drehzahlen) bis zu Schlichtarbeiten (hohe Drehzahlen, niedrige Lasten) und allem dazwischen reichen. Selbst wenn ein CNC-Bearbeitungszentrum mit Spindellagern bestückt ist, die für einen bestimmten Arbeitszyklus zum Zeitpunkt des Einkaufs optimiert wurden, heißt das noch lange nicht, dass die Lager auch für zukünftige Arbeitszyklen optimiert sind. Wegen kleinerer Stückzahlen und häufigerer Produktwechsel ersetzen viele Betreiber Transferstraßen durch flexible CNC-Bearbeitungszentren. Aber diese Umrüstung ist auch mit häufig wechselnden Arbeitszyklen verbunden.
Nr. 2: Werkzeuglasten und -geschwindigkeiten: Die Abschätzung der Werkzeuglasten und -geschwindigkeiten ist wichtig, weil unterschiedliche Lagerausführungen und -konfigurationen unterschiedliche Mengen an Wärme und Spannung bei jeder Betriebsbedingung erzeugen – und das hat eine direkte Auswirkung auf die Lebensdauer und die Betriebstemperatur der Spindel.
Wenn der Arbeitszyklus festgelegt worden ist, müssen die Werkzeuglasten und -geschwindigkeiten für jeden Schritt bestimmt werden. Die spanende Bearbeitung und der Werkstoff bestimmen den Werkzeugtyp, die Werkzeuggeometrie, die Frästiefe und -breite und die Vorschubgeschwindigkeit. Die Werkzeuglasten und -geschwindigkeiten sind davon abhängig, ob die Maschine für Schrupp- oder Schlichtarbeiten verwendet wird. Das Werkstückmaterial (egal, ob Stahl, Aluminium, Titan, Nickel oder sonstige Werkstoffe) und seine Härte beeinflussen ebenfalls die Werkzeuglasten und -geschwindigkeiten.
Die zuverlässigste und genaueste Methode zur Bestimmung der Werkzeuglasten und -geschwindigkeiten ist die Interpretation der Prozessdaten tatsächlicher Zerspanungsvorgänge. Wenn die tatsächliche Motorleistung, die Spindeldrehzahl und der Werkstückdurchmesser bekannt sind, lässt sich die Zerspanungslast berechnen, indem die Zerspanungsleistung (Werkzeugkraft x Werkzeugdurchmesser x Geschwindigkeit) der tatsächlichen Motorleistung gleichgesetzt und die Gleichung für die Werkzeugkraft gelöst wird. Das gilt allerdings nur, wenn die spanende Bearbeitung und das Werkstückmaterial bzw. die Härte identisch sind. Die Erfassung der Prozessdaten über längere Zeit ist eine lohnende Investition und kann helfen, das Rätselraten bei der Bestimmung der Werkzeuglasten und -geschwindigkeiten zu eliminieren.
Ein analytischer Ansatz kann zur Verifizierung der erfassten Prozessdaten beitragen. Viele Werkzeuglieferanten können Werkzeuglasten und -geschwindigkeiten berechnen und Sie bei der Werkzeugauswahl beraten. Eine alternative analytische Methode zur Berechnung der Werkzeuglasten ist die Verwendung eines Referenzwerks für Werkzeugmaschinen. Zu meinen Favoriten gehört Technology of Machine Tools, 7th Edition von Steve Krar, Arthur Gill und Peter Smid. Die in diesem Buch enthaltenen Gleichungen erfordern die benutzerseitige Eingabe der Werkzeuggeometrie, der Zerspanungsparameter, der Verschleißfaktoren und weiterer Parameter. Die Nutzung dieser Gleichungen erfordert ein hohes Maß an Fachkenntnis – normalerweise besitzt Ihr Werkzeuglieferant entsprechende Erfahrungen und die benötigte Werkzeuggeometrie, um die Berechnungen durchzuführen und Ergebnisse ausreichender Genauigkeit zu erhalten.
Wenn keine der Inputs bekannt sind und keine Prozessdaten vorliegen, können die Zerspanungslasten auf Basis der statischen Tragfähigkeit des Lagers abgeschätzt werden. Zerspanungslasten reichen normalerweise von 5 Prozent (Schlichtbearbeitung) bis zu 25 Prozent (Schruppbearbeitung) der statischen Tragfähigkeit des Lagers; die Geschwindigkeiten reichen von 10 Prozent (Schruppbearbeitung) bis zu 90 Prozent (Schlichtbearbeitung) der zulässigen Spindeldrehzahl. In Abhängigkeit vom spanenden Bearbeitungsverfahren können diese Werte frei kombiniert werden. Hierbei handelt es sich jedoch lediglich um grobe Schätzwerte, die nur zur anfänglichen Lagerauswahl verwendet werden sollten.
Nr. 3: Lagerausführung und -konfiguration: Viele unterschiedliche Hochgeschwindigkeits-/Hochgenauigkeits-Schrägkugellager sind in zahlreichen ISO-Maßreihen im Handel erhältlich. In Werkzeugmaschinenspindeln werden die ISO-Maßreihen 19 und 10 am häufigsten eingesetzt.
Timken bietet drei verschiedene Lagerausführungen für die ISO-Maßreihe 10; das Lager HN7000 (Baureihe HN) mit kleinen Kugeln, das Lager HX7000 (Baureihe HX) mit mittelgroßen Kugeln und das Lager 7000 (Baureihe WI) mit großen Kugeln, siehe Abbildung 1.
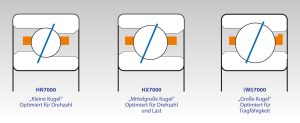
Abbildung 1: Lagerkonstruktion (Bild: The Timken Company)
Jede Lagerausführung hat deutlich unterschiedliche Kugelgrößen, Kugelbestückungen und Laufbahnkrümmungen, durch die die Tragfähigkeit, die maximale Drehzahl und die Steifigkeit des Lagers bestimmt werden. Normalerweise wird die Lagerausführung auf Basis der beabsichtigten Zerspanungsart – Schruppbearbeitung, Schlichtbearbeitung oder Mehrzweckbearbeitung – ausgewählt (siehe Abbildung 2). Das ist jedoch lediglich ein Ausgangspunkt; zur Bestätigung der Auswahl sollten Analysen durchgeführt werden.
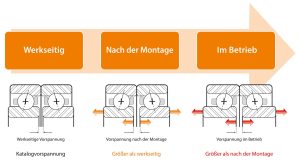
Abbildung 2: Auswahl einer Lagerausführung auf Basis der Zerspanungsart. (Bild: The Timken Company)
Die Lagerausführung bestimmt die Kugelgröße, die Kugelbestückung und die Laufbahnkrümmung, während die Lagerkonfiguration durch den Kugelwerkstoff (Stahl/Keramik), den Kontaktwinkel (15 ° oder 25°) und die Vorspannung (extraleicht, leicht, mittel und stark) bestimmt wird. Diese Lagerkonfiguration dient zur Feinabstimmung der Tragfähigkeit, der maximalen Drehzahl und der Steifigkeit; sie wird ausgewählt, um die Lagerleistung auf Basis der Drehzahlen und Lasten zu optimieren. Während die Lagerausführung die beabsichtigte Zerspanungsart berücksichtigt, basiert die Lagerkonfiguration auf dem Arbeitszyklus. Die beste Methode zur Optimierung der Konfiguration ist die analytische Modellierung der Spindel.
Timken nutzt firmeneigene Software zur präzisen Modellierung der Lager/Spindel-Einheit anhand unterschiedlicher Lasten, Drehzahlen und Umgebungsbedingungen. Diese Modellierung liefert die Kontaktspannungen zwischen den Kugeln und der Laufbahn unter Berücksichtigung der Vorspannung, externe Lasten und die Zentrifugalkraft der Kugeln aufgrund der Umlaufgeschwindigkeit.
Optimierung lässt sich durch Modulation der verschiedenen Konfigurationsparameter erzielen, so dass die Wärmeerzeugung in der Anwendung möglichst klein gehalten wird. Wärme entsteht in erster Linie durch die Gleitbewegung der Kugeln entlang der Laufbahn und durch die Rutschbewegung aufgrund der Lagerentlastung. Die Vorspannung hat den größten Einfluss auf die Wärmeerzeugung und dieser Parameter wird normalerweise zur Minimierung der Gleit- und Rutschbewegung verwendet. Die Vorspannung wird durch die resultierende Kontaktspannung zwischen Kugel und Laufbahn begrenzt. Die Höchstgrenze beträgt üblicherweise weniger als die Hälfte der für die plastische Verformung benötigten Spannung.
Das Kugelmaterial und der Kontaktwinkel beeinflussen ebenfalls die Wärmeerzeugung, haben aber einen geringeren Einfluss als die Vorspannung. Diese Faktoren werden normalerweise zur Feinabstimmung der Konfiguration auf Basis der Belastungsart (Axial- oder Radialbelastung) und der Geschwindigkeitsanforderungen verwendet. Zum Beispiel: Wenn im Arbeitszyklus überwiegend Axiallasten auftreten, wird ein Kontaktwinkel von 25° ausgewählt. Wenn die Geschwindigkeitsanforderungen die Nenndrehzahl für Stahlkugeln überschreiten, sollte die Umstellung auf Keramikkugeln erfolgen.
Die Fähigkeit zur Durchführung von Analysen bei unterschiedlichen Lasten, Drehzahlen und Umgebungsbedingungen eliminiert das Rätselraten bei der Auswahl des optimalen Lagers zur Maximierung der Spindelleistung.
Nr. 4: Fachgerechte Montage: Nach der Auswahl der richtigen Lagerausführung und -konfiguration muss das Lager fachgerecht montiert werden, um die gewünschte Leistung zu erzielen. Dabei sind die Größe und die geometrische Form der Welle und der Gehäuseaufnahme von entscheidender Bedeutung. Die Vorspannung kann sich drastisch ändern, wenn die tatsächlichen Einbauwerte außerhalb ihrer empfohlenen Grenzen liegen. Deshalbist es wichtig, einen ordnungsgemäßen Einbau durchzuführen, damit die Vorspannung korrekt angewandt wird.
Nr. 5: Wellen- und Gehäusepassungen: Die Wellenpassungen für Spindellager sind für den Betrieb bei Drehzahlkennwerten von 750.000 dN oder weniger ausgelegt (dN = Bohrung in mm x Drehzahl in Umin-1) und erfordern eine im Katalog angegebene Übergangspassung (geringfügig lose bis geringfügig eng, nomineller Linienkontakt). Das Lager auf der Arbeitsseite ist axial fixiert und das Gehäuse hat eine Spielpassung. Wenn das andere Ende axial im Gehäuse verschiebbar ist, wird eine besonders lose Passung benötigt.
Spindellager, die für den Betrieb bei Drehzahlkennwerten von mehr als 750.000 dN ausgelegt sind, erfordern eine Presspassung, deren Betrag von der Lagergröße, der Drehzahl und der Wellenbohrung abhängt. Das ist bedingt durch die Wirkung der Zentrifugalkraft, die dazu führt, dass sich der Innenring und die Welle in Radialrichtung elastisch ausdehnen. Wenn ein bei diesen Drehzahlen arbeitendes Lager mithilfe einer im Katalog angegebenen Übergangspassung montiert wird, wird die Passung bei der Auslegungsdrehzahl lose, was die Gefahr erhöht, dass der Wellenschlag zunimmt und der Innenring sich auf der Welle dreht.
Timken stellt seinen Kunden ein Tool zur Berechnung der drehzahlabhängigen Passung und des zugehörigen Distanzhülsenversatzes für unsere Linie von Superpräzisionsschrägkugellagern zur Verfügung – den Timken Precision Bearing Selector (TPBS), der von Timken.com heruntergeladen werden kann. Der TPBS enthält außerdem alle Katalogpassungen, Lagersteifigkeiten und vieles mehr. Die Gehäusepassungen ändern sich nicht in Abhängigkeit von der Wellendrehzahl.
Nr. 6: Mikrometercode: Alle Timken P4S-Lager enthalten Mikrometercodes, die anzeigen, um welchen Betrag in Mikrometern (µm) das Lager von der im Katalog angegebenen nominellen Bohrungsgröße und dem nominellen Außendurchmesser abweicht. Der Techniker kann dann Bohrung und Außendurchmesser bis auf +/- 1 µm genau bestimmen und den Lagersitz fertigschleifen, um die beabsichtigte Passung innerhalb eines Mikrometers zu erzielen.
Mikrometercodes werden außerdem verwendet, um einzelne Lager zu Lagersätzen von zwei oder mehr Lagern zu kombinieren. Im Idealfall hätte ein Betreiber gerne einen Lagersatz, bei dem alle Bohrungs- und Außendurchmessercodes identisch sind. Da dies aus produktionstechnischer Sicht jedoch nicht praktisch ist, sind kleine Toleranzen beim Zusammenbau von Lagersätzen zulässig. Die Toleranzen aufeinander abgestimmter Lagersätze sind abhängig von der Bohrungsgröße und dem Außendurchmesser. Je größer die Bohrung oder der Außendurchmesser, um so größer ist der zulässige Bereich der Mikrometercodes für den Zusammenbau des Lagersatzes.
Nr. 7: Geometrische Bemaßung und Toleranzen: Gute Konstruktion und gute Bearbeitung sind unerlässlich. Die enge Kontrolle der Lagerpassungen ist nur die halbe Miete – die geometrische Form von Welle und Gehäuse muss ebenfalls engen Toleranzen genügen. Je nach Größe der Bohrung und des Außendurchmessers liegt diese Toleranz zwischen 1 und 8 µm (normalerweise zwischen 2 und 4 µm). Diese Geometrie bezieht sich nicht nur auf den Lagersitz; sie gilt ebenso für alle angrenzenden Bauteile wie Kontermuttern, Distanzstücke und Endkappen.
Nr. 8: Vorspannung vom Werk bis zum Einsatz: Die im Katalog angegebene Vorspannung wird werkseitig in die Lagerstirnflächen eingeschliffen; sie ändert sich jedoch, wenn der Lagersatz mit Presspassung auf der Welle montiert wird. Wenn der Innenring auf die Welle aufgepresst wird, erhöht sich der Laufbahndurchmesser, was zur axialen Aufweitung des Innenrings führt und die Vorspannungseinstellung des montierten Lagers erhöht (siehe Abbildung 3). Im englischen Sprachgebrauch wird dieser Vorgang auch als „Telescoping“ bezeichnet.
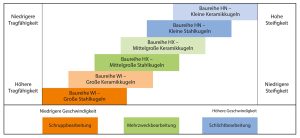
Abbildung 3: Vorspannung vom Werk bis zum Einsatz. (Bild: The Timken Company)
Wenn die Lager in Betrieb sind und ein Temperaturunterschied zwischen den Innen- und Außenringen vorliegt, wird die Vorspannung zusätzlich weiter erhöht. Wenn die Spindel im Betrieb ihre optimale Leistung erzielen soll, müssen bei der Einstellung der montierten Vorspannung die Betriebstemperaturen berücksichtigt werden.
Wenn eine optimierte Produktivität das Ziel ist, sollte die Lagerausführung unter Berücksichtigung der beabsichtigten Fräsarbeiten ausgewählt werden, während die beste Lagerkonfiguration durch Modellieren des Arbeitszyklus mit dem Ziel reduzierter Wärmeerzeugung aufgrund der Gleit- und Rutschbewegungen bestimmt werden kann. Darüber hinaus müssen die Lager korrekt auf der Welle und im Gehäuse montiert werden, wobei die Lagersitze enge geometrische Maßtoleranzen erfüllen müssen und mikrometercodierte Passungen zu verwenden sind.
Die Einhaltung dieser bewährten Praktiken trägt dazu bei, dass Spindellager wie erwartet funktionieren und dass die Betreiber von Werkzeugmaschinen ihre CNC-Bearbeitungszentren wie geplant einsetzen können.
Autor: Eric Faust
Eric Faust ist Spezialist für Anwendungstechnik bei The Timken Company. Sein Hauptarbeitsbereich ist die Unterstützung von Kunden bei der Auswahl, Konfiguration und Installation von Präzisionslagern in Werkzeugmaschinen. Er ist seit 20 Jahren für Timken tätig, hat zahlreiche Positionen in den Bereichen Maschinenbau und Programmverwaltung inne und ist Verfasser mehrerer Fachartikel zum Thema Lagerauswahl.