I. EINLEITUNG
A. State of the Art
Die polyurethanverarbeitende Industrie ist in den letzten Jahren enorm gewachsen. Speziell im Automotivebereich finden geschäumte Teile eine immer breitere Anwendung. Sei es für die Herstellung von Sitzen, Lenkrädern, Abdichtungen oder für die Säulenausschäumung der A-, B- oder C-Säule. Schäume kommen überall zum Einsatz, wo neben guten Dämpfungseigenschaften ebenso eine hohe Stabilität bei einem geringen Gewicht gefordert sind. [1] Der Einsatz von Polyurethanen (PUR) führt zur Notwendigkeit von Entformungshilfen wie den klassischen silikonbasierten Trennmitteln, speziellen Werkzeugbeschichtungen oder Foliensystemen. Eine Entformung des Schaumteils aus dem meist metallischen Schäumwerkzeug ist ohne diese nicht möglich. Da für den Einsatz von Werkzeugbeschichtungen und Foliensystemen einige besondere fertigungstechnische Restriktionen zu beachten sind, ist nach wie vor das klassische Trennmittel die am weitest verbreitete Entformungshilfe. Grundsätzliches Problem dabei ist jedoch das erhöhte stoffliche Gefährdungspotential des silikonbasierten Trennmittels.
B. Problemstellung
Allgemein basiert die Bildung von vernetzten Polyurethanen auf dem 3-Säulenmodell. Demnach wird gemäß Abbildung 1 durch eine Additionsreaktion zwischen dem Polyisocyanat, und Polyol (Alkohol) sowie Hilfsstoffen die PUR-Synthese ermöglicht. [3] Für einige dieser Schaumderivate konnten bereits umweltfreundliche Trennmittelsysteme auf Wasserbasis realisiert werden. Allerdings ist infolge der verlängerten Ablüftzeiten sowie des erhöhten Reaktionsniveaus der Isocyanatkompontenten einiger PUR-Derivate mit den wässrigen Anteilen des Trennmittels diese Möglichkeit lediglich bei bestimmten Schaum- und Prozessvarianten gegeben [2]. Der Entwicklungsaufwand zur Adaption des wasserbasierten Trennmittelsystems auf das jeweilige Schaum- und Produktionssystem übersteigen in vielen Fällen das Kostenbudget um ein Vielfaches. Zudem ist meist auch mit einer Verschlechterung der Oberflächenqualität zu rechnen. Bei komplexeren Schaumteilstrukturen, welche gegebenenfalls zusätzlich noch Einlegeteile aufweisen, sind manuelle Fertigungsschritte und damit der direkte Kontakt des Operators mit dem Trennmittel und den entstehenden Trennmittelaerosolen meist unabdingbar. Zudem führt ein manuell ablaufender Eintrennprozess dazu, dass die Auftragsmenge schwer zu regulieren ist und erheblich mehr Trennmittel eingesetzt wird als notwendig. Gleichzeitig verschlechtert sich aber auch das Eintrennergebnis. So soll dieser Beitrag verbesserte Systemkonzepte für den Umschäumungsprozess aufzeigen, die den Faktor Trennmittel soweit wie möglich ausschließen. Dabei wird auch ein besonderes Augenmerk auf eine generelle, schaumsystemunabhängige Einsetzbarkeit des Konzepts gelegt.
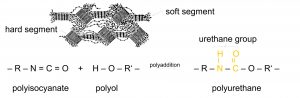
Abbildung 1: Morphologie der Polyurethane
II. MÖGLICHKEITEN DER TRENNMITTELREDUKTION
Im ersten Teil dieses Beitrags sollen die systemtechnischen Möglichkeiten aufgezeigt werden, um eine Trennmittelreduktion im Fertigungsprozess von Schaumteilen zu erreichen. Durch ein intelligentes Systemengineering mit Hilfe am Markt etablierter Einzeltechnologien soll ein innovatives Gesamtsystem entworfen werden. Der Investitionsaufwand soll dabei möglichst niedrig gehalten werden, um sowohl eine attraktive Option für kleine und mittelständische Betriebe als auch für die Massenfertigung darzustellen. Alle zugrundeliegenden Berechnungen und Auslegungsdaten beziehen sich dabei auf einen ausgewählten Serienfertigungsprozess eines großen Automobilzulieferers.
A. Auftragsoptimiertes semi-permanentes Trennmittelsystem
Untersuchungen an Werkzeugsystemen unterschiedlicher Komplexität haben gezeigt, dass beim Trennmittelauftrag äußerste Präzision sowie ein gezieltes Eintrennen gefordert ist. Ein geschulter Operator ist daher ebenso wichtig wie das Vorhandensein von Erfahrungen im Bereich des Lack- und Trennmittelauftrags. Zur Kompensation der Ausbildungs- und Erfahrungsdefizite wird der Trennmitteleinsatz stark erhöht, um eine leichte Entformung des Schaumteils zu ermöglichen. Entsprechend ist eine Unterstützung wie beispielsweise durch Laserprojektorsysteme notwendig, die dem Operator bei der Führung der Sprühpistole durch die Visualisierung diverser Zusatzinformationen eine Hilfestellung bietet. Diese ermöglichen es dem Operator die werkzeugspezifisch optimale Eintrennbahn visuell anzuzeigen, sodass ein gezielter Auftrag des Trennmittels erfolgen kann. Die Trennmittelverbrauchsmenge kann so deutlich reduziert werden.
Auf Basis dieses Anforderungsprofils wurde ein Systemaufbau konzipiert, welcher sich gezielt der Thematik mehrerer linear angeordneter Schäumwerkzeuge widmet. Durch den Einsatz eines Linearführungssystems, an dem der Laserprojektor montiert ist, kann im Vergleich zur statischen Montage, ein deutlich größerer Projektionsbereich abgedeckt werden. Zusätzlich besteht die Möglichkeit, die Eintrenndauer – d.h. die effektive Sprühzeit mit der Sprühpistole – für den Operator zeitlich zu limitieren, um so einen möglichen Missbrauch des Systems vorzubeugen. Regelungstechnisch kann dies durch eine Dosiereinheit für den Trennmitteldruckbehälter umgesetzt werden.
Materialseitig kann die Konzeptidee durch den Einsatz von semi-permanenten Trennmittelsystemen unterstützt werden, wodurch mehrere Entformungszyklen ohne erneuten Trennmittelauftrag möglich sind. Die Entwicklung solcher zyklusstabilen, trennaktiven Systeme auf Basis von konventionellen Trennmitteln ist mit wesentlich geringerem Forschungs- und Validierungsaufwand verbunden, als die Entwicklung von gesundheits- und umweltfreundlichen Entformungshilfen (z.B. auf Wasserbasis). Nichtsdestotrotz kann durch die Kombination mit einer Laserprojektorapplikation gemäß Tabelle 1 die Verbrauchsmenge an Trennmitteln um bis zu 83 % reduziert werden. Einzusetzen ist dieses System bevorzugt bei komplexen und großflächigen Werkzeugsystemen mit einer verwinkelten Formgeometrie.
B. Integrative Eintrennautomation
Mit Hilfe der sog. integrativen Eintrennautomation wird der Trennmittelauftrag vollständig automatisiert. Das Auftreten von fehleranfälligen, monotonen Arbeitsinhalten kann für den Operator somit deutlich minimiert werden. Durch den Einsatz eines kooperativ arbeitenden Leichtbaurobotersystems und einem intelligenten Schutzsystem kann dabei eine in-line Integration in das bestehende Prozessdesign ermöglicht werden. Durch die vollständige Übernahme des Eintrennprozesses durch den Eintrennroboter kann zudem die Zykluszeit im Vergleichsprozess um mehr als 24 %, die Trennmittelverbrauchsmenge sogar um etwa 88 % reduziert werden (s. Tabelle 1). Damit können im Schaumbereich eventuell auftretende Bottleneck-Effekte umgangen und damit die Lieferfähigkeit gegenüber dem Kunden erheblich gesteigert werden.
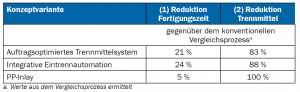
TABELLE 1: GEGENÜBERSTELLUNG FERTIGUNGSTECHNISCHER KENNGRÖSSEN FÜR DIE HERSTELLUNG VON SCHAUMTEILEN
Da der Prozess des Schäumens einen erhöhten Anteil an manuellen Tätigkeiten besitzt, ist der Einsatz komplexer Robotersysteme mit sehr hohem Engineering- und Investitionsaufwand verbunden. Kooperative Robotersysteme bieten hier infolge ihrer leichten Handhabbarkeit bei gleichzeitig großer Einsatzbreite und geringem Kostenaufwand ein hohes Potential für die vorliegende Anwendung. Zur Erhöhung der Prozessflexibilität kann je nach Prozess zwischen verschiedenen Arbeitsbereichen gewählt werden. Das System selbst verfügt dabei über diverse justierbare Sicherheitssysteme, welche die Mensch-Maschine Kooperation gewährleisten und gemäß der Gefährdungsbeurteilung nach Maschinenrichtlinien zu konfigurieren sind [4]. Die Erstellung einer Risikobeurteilung im Sinne der einschlägigen Normen [5], [6], [7] zur Schwachstellenidentifikation ist zwingend durchzuführen.
Im Vergleichsprozess besteht die Schäumanlage aus einer variablen Anzahl an linear angeordneten Schäumwerkzeugen. Um die bestehende Anlagen- und Werkzeugsysteme weiterhin nutzen zu können, wurde das Anlagenkonzept so konzipiert, dass der Eintrennroboter ohne größere Änderungen an Peripheriekomponenten in das bestehende System implementiert werden kann. Dazu wurde eine Linearführungseinheit mit entsprechendem Schleppkettensystem gewählt (Abbildung 2). Das gesamte System kann, in Abhängigkeit der Werkzeughöhe, auf Portalstützen gelagert werden. Um einen vollumfassenden Werkerschutz, auch während des Verfahrens der Anlage, gewährleisten zu können, ist an dem Schlitten der Lineareinheit ein Sicherheits-Laserscanner angebracht. Ein solches System eignet sich aufgrund des erhöhten Investitionsvolumens vor allem für hohe Stückzahlen und komplexe Werkzeuggeometrien. Der Schulungsbedarf für Mitarbeiter kann durch die Auslagerung des Eintrennprozesses erheblich vermindert werden. Der Operator übernimmt letztlich nur noch administrative Aufgaben, wie beispielsweise das Schließen des Werkzeugs oder das Entformen des Schaumteils.
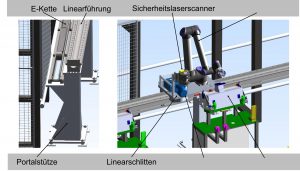
Abbildung 2: Systemaufbau integrativer Eintrennroboter
III. MÖGLICHKEITEN DER TRENNMITTEL-ELIMINIERUNG
Im nächsten Schritt soll eine Möglichkeit aufgezeigt werden, Trennmittel jeglicher Art aus dem Fertigungsprozess zu eliminieren. Basis des Konzepts bilden thermogeformte Polypropylenfolien mit einer Ausgangsmaterialstärke zwischen 1,5 und 2,0 mm (je nach Abformkomplexität) – auch PP-Inlay genannt. Ein entsprechendes Gebrauchsmuster [9] wurde bereits 2015 patentiert. Das Funktionsprinzip dahinter beruht auf der Minderung der Oberflächenenergie der Formwerkzeugoberfläche. Während für Aluminium und Stahlwerkstoffe in der Literatur Werte von über 800 mN/m für die Oberflächenenergie zu finden sind, besitzen polymere Oberflächensysteme aus Polypropylen Werte von etwa 29 mN/m. Eine Anhaftung bzw. eine starke Verschlechterung des Entformungsprozesses findet für die meisten PUR-Systeme ab einer wirkenden Oberflächenenergie von etwa 38 mN/m statt [8]. Demnach kann mit Hilfe des PP-Inlays eine Entformung ohne weitere Entformungshilfen stattfinden. Das Foliensystem ist mindestens über 150 Entformungszyklen stabil, was dem Prüfumfang der Studie entsprach.
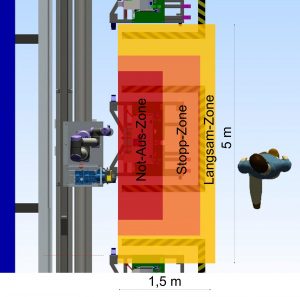
Abbildung 3: Einteilung der Sicherheitsbereiche des Laser-scanners (Draufsicht)
Eine größere Problematik stellt allerdings die Versteifung und Beheizung des flexiblen Foliensystems dar. Gemäß dem Gebrauchsmuster [9] soll als Werkzeugaufnahme für die PP-Folien ein gewöhnliches Formwerkzeug aus Aluminium herangezogen werden. Dies ist jedoch sowohl aus Sichtweise der Produktionsflexibilität als auch kostentechnisch nicht zielführend. Zur Lösung dieser Problematik soll daher das von der Fachhochschule Dortmund entwickelte fibretemp® System [10] genutzt und mit den PP-Einlegern verknüpft werden. Die eigentliche Technologie dahinter beschreibt die Herstellung von beheizbaren CFK-Formwerkzeugen für die energieeffiziente Temperierung von Formen in der Faserverbundfertigung z.B. für die Fertigung von Rotorblättern für Windkraftanlagen. Die entstehenden Formwerkzeuge besitzen dabei drei, für das Konzept der PP-Einleger, essentielle Eigenschaften: eine hohe Verwindungssteifheit, Möglichkeit das PP-Foliensystem in kürzester Zeit gleichmäßig auf 50 °C aufzuheizen sowie ein erhebliches Gewichtseinsparungspotential. Fertigungstechnisch lassen sich die beheizbaren CFK-Lagen auf der Rückseite des PP-Inlays aufbringen. Nach vollständiger Aushärtung des Systems ist es möglich das PP-Inlay einfach wieder herauslösen. Die Lebensdauer ist bei entsprechender Handhabung der Systemkomponenten nicht limitiert.
Zur Erhaltung der geforderten Bauteilqualität sowie zur Einhaltung evtl. notwendiger Toleranzen ist ein durchdachtes Werkzeugdesign (Abbildung 4) notwendig. Neben dem Thermoformen der Folien im Positivverfahren sind speziell auch weitere gestaltungstechnische Maßnahmen zu ergreifen. Zusätzlich zum Einplanen entsprechender Entlüftungskanäle ist auch ein Dichtungssystem vorzusehen. Dies umfasst neben Dichtungsbändern aus Silikon auch den Einsatz von Permanentmagneten, welche in den CFK-Formen verbaut sind und so eine primäre Fixierung der Formteilhälften ermöglichen.
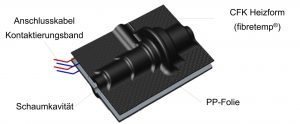
Abbildung 4: Konzeptdesign der PP-Inlays
Limitiert wird das System letztlich nur durch gestaltungstechnische Restriktionen des Thermoformprozesses. So sind Hinterschneidungen und sehr große Durchmessersprünge nicht abbildbar. Auch muss bei Stirnflächen auf die Existenz von leichten Entformungsschrägen (~1 °) geachtet werden, um ein leichtes Lösen der thermogeformten Folien vom Abformwerkzeug zu ermöglichen. Für das oben beschriebene System wurden bei der Entwicklung des Gesamtsystems Synergieeffekte zu anderen Bereichen genutzt, um ein in der Praxis anwendbares Produktionskonzept zu erreichen. Dabei wurde sich von allen bisher bekannten Systemdesigns im Bereich der Schaumteilherstellung gelöst und der Prozess grundlegend neu konzipiert. So kann auf diese Weise ein Wandel des arbeits- und trennmittelintensiven Fertigungsbereichs in eine smarte, trennmittelarme bzw. trennmittelfreie Bauteilfertigung erfolgen. Dabei ist das System der PP-Inlays speziell für Unternehmen geeignet, bei denen die Prozessflexibilität hohe Priorität besitzt.
IV. ZUSAMMENFASSUNG UND AUSBLICK
In diesem Beitrag konnte gezeigt werden, dass durch eine Rekombination am Markt etablierter Technologien und einem intelligenten Systemengineering eine wesentliche Optimierung der Prozessabläufe bei gleichzeitiger Trennmittelreduktion in der Schaumteilfertigung realisiert werden kann. Je nach Prozess ist es möglich, die Fertigungszeit pro Teil um bis zu 24 % zu verkürzen und gleichzeitig eine Reduktion der Trennmittelverbrauchsmenge um bis zu 88 % zu erzielen. Ein ganz neuer Ansatz des Fertigungskonzeptes wird durch die PP-Inlays verfolgt. Diese ermöglichen es durch Verzicht auf teure Aluminium- und Stahlwerkzeuge die Produktionsflexibilität zu erhöhen und gleichzeitig die Stückkosten zu minimieren. Zwar sind hiermit auch Risiken für das jeweilige Unternehmen verbunden, allerdings zeigten die ersten Ergebnisse sehr gute Eigenschaften bezüglich der resultierenden Bauteilqualität.
REFERENZEN
[1] N.N.: Polyurethane im Automobilbau. online unter: www.polyurethanes.basf.de/pu/solutions/de/content/group/Arbeitsgebiete_und_Produkte/Branchen/Automotive (2017-04-29).
[2] SCHWARZ, O. (Hrsg.); EBELING, F. W. (Hrsg.): Kunststoffkunde: Aufbau, Eigenschaften, Verarbeitung, Anwendungen der Thermoplaste, Duroplaste und Elastomere. 9., überarb. Aufl. Würzburg: Vogel Buchverl., 2007 (Vogel-Fachbuch).
[3] WOODS, G.: The ICI Polyurethanes book. 2nd ed. Chichester, New York: Published jointly by ICI Polyurethanes and Wiley, 1990.
[4] BG/BGIA-Empfehlungen für die Gefährdungsbeurteilung nach Maschinenrichtlinie: Gestaltung von Arbeitsplätzen mit kollaborierenden Robotern. Sankt Augustin, Februar 2011.
[5] DIN EN ISO 10218-1: Januar 2012, Industrieroboter – Sicherheitanforderungen –Teil 1: Roboter.
[6] DIN EN ISO 10218-2: Juni 2012, Industrieroboter – Sicherheitsanforderungen – Teil 2: Robotersysteme und Integration.
[7] DIN ISO/TS 15066: April 2017, Roboter und Robotikgeräte – kollaborierende Roboter.
[8] PACKHAM, D. E. (Hrsg.): Handbook of Adhesion. 2., Auflage. New York, NY: John Wiley & Sons, 2005.
[9] FDST Patentanwälte: Fertigungshilfe zur Herstellung eines Leitungssatzes. FDST Patentanwälte mbB. Anmeldenr. 202013104570.5, Deutschland. 19.02.2015. Deutschland. Veröffentlichungsnr. DE202013104570U12015.02.19.
[10] Funktionsweise: fibretemp. Bremen. online unter: www.fibretemp.de/de/ueber_fibretemp/funktionsweise/ (2017-06-08).
Autor:
Paul Heisler,
Lehrstuhl für Fertigungsautomatisierung und Produktionssystematik,
Friedrich-Alexander-Universität,
Erlangen-Nürnberg