G. Wötting, M. Knoch, W. Martin, F. Reißmann
Kurzfassung
Es werden SiC- basierende, intrinsisch heizende Elemente vorgestellt, bestehend aus einer Kombination von dichten SiC-Varianten mit hohem und geringem spezifischen elektrischen Widerstand. Aufgrund der sehr ähnlichen Zusammensetzung und Sintercharakteristik dieser Varianten sind diese Elemente druckunterstützt aber auch im Ko-Sinterprozess als Verbund (vor-) gesinterter Teile relativ kostengünstig herstellbar. Die Möglichkeit des Sinterns erweitert das herstellbare Formenspektrum gegenüber bislang verfügbaren keramischen Heizelementen und eröffnet eine Vielzahl neuer, innovativer Anwendungen.
1. Motivation und Zielsetzung dieser Entwicklungen
Heizelemente werden in technischen Apparaturen und Anlagen vielfältig genutzt, um lokal Wärme zu erzeugen. Die meisten dieser Elemente sind metallischer Natur und erzeugen die Wärme nach dem ohmschen Widerstandsprinzip mit stromdurchflossenen Drähten oder Stäben, den sogenannten Heizleitern. Sie können freistrahlend eingesetzt werden, oft ist jedoch eine (elektrische) Isolation gegenüber der Umgebung notwendig, was durch Einbettung der Heizleiter in einen mineralischen Isolierstoff, z.B. MgO erfolgt. Dieser Verbund wird aus Stabilitätsgründen noch mit einem metallischen Rohr aus z.B. Cu, Stahl oder auch Quarzglas umhüllt. Da die mineralischen Isolierstoffe häufig eine schlechte Wärmeleitfähigkeit aufweisen, ist die Leistung und der Wirkungsgrad derartiger Heizelemente begrenzt und die Trägheit hoch.
Die mit derartigen Heizleitern erzielbare Temperatur hängt primär von der Art des Heizelements aber auch von der Art der Hüllrohre ab. Als Maximum können mit bestimmten Konstellationen etwa 1000°C erreicht werden. Für noch höhere Temperaturen werden thermisch beständigere keramische Materialien als Heizleiter nötig wie z.B. SiC, MoSi2, Graphit. Diese ermöglichen als eigenständige Elemente deutlich höhere Temperaturen, müssen aber zum Teil selbst wieder geschützt werden, wie z.B. Graphit durch Schutzgas. Bei diversen Keramiken ist ein derartiger Schutz nicht nötig, sie weisen bei Temperaturen > 1000°C an Luft noch eine hohe Oxidationsbeständigkeit und Formstabilität auf. Dies sind natürlich primär Oxidkeramiken wie Al2O3, ZrO2 etc., aber insbesondere auch Nichtoxid-Keramiken wie Siliziumnitrid Si3N4 und Siliziumcarbid SiC. Letztere weisen gegenüber den Oxidkeramiken die generellen Vorteile einer geringeren Wärmedehnung und höheren Wärmeleitfähigkeit auf, was sich in deutlich besseren Thermoschock- Beständigkeiten widerspiegelt.
Über die diversen bereits existierenden technische Lösungen für keramische Heizelemente hinausgehend war es das Ziel der hier vorgestellten Arbeiten, Heizelemente größerer Abmessungen und / oder höherer Komplexität zu realisieren, was ein Sinterverfahren favorisiert. Eine freie Formgestaltung ermöglicht eine erweiterte Funktionalität und damit eine Vielzahl neuer Applikationen wie z.B. Werkzeugeinsätze in der Warmumformung von Metallen oder der thermoplastischen Formgebung von Kunststoffen etc. In diesen Technologiefeldern werden sie bislang kaum angewandt, obwohl ein großer Bedarf an mechanisch stabilen, korrosions- und oxidationsbeständigen Heizelementen besteht, die des weiteren schnell reagieren und eine hohe spezifische Leistung aufweisen sollten.
Auf Grund dieses umfangreichen Forderungskatalogs wurde als keramischer Werkstoff für die eigenen Entwicklungen dichtes, gesintertes SiC gewählt (bzw. spezielle SiC-TiB2 – Composite, s.u.), das z.B. gegenüber Si3N4 die folgenden Vorteile aufweist:
- eine wesentlich höhere Wärmeleitfähigkeit (bis zu 4 x höher)
- eine höhere Härte (bis 2600 Vickers) und umfassendere Korrosionsbeständigkeit
- vielfältige Formvarianten durch die Möglichkeit der pulvertechnologischen Herstellung durch Pressen, Grünbearbeiten, Sintern und Hartbearbeitung
Von den beiden erstgenannten Punkten wird eine höhere Aufheizgeschwindigkeit und Verschleißbeständigkeit erwartet, der letztgenannte Punkt bietet sowohl technologische als auch wirtschaftliche Vorteile gegenüber einer Herstellung durch Heißpressen.
2. Stand der Technik
Es gibt in der Literatur aber auch im freien Markt bereits eine Reihe von technischen Lösungen und auch Applikationen für keramische Heizelemente. Diese umfassen z.B. Varianten, bei denen in die isolierende Keramik ein metallischer oder keramischer Heizleiter eingesintert wird [Kue 13]. Alternativ wird eine intrinsische Leitfähigkeit durch eine Kombination von z.B. Si3N4 mit leitfähigen keramischen Phasen wie z.B. Titancarbid oder –nitrid, Molybdän- oder Wolframsilizid etc. erzeugt. Eine ausreichende elektrische Leitfähigkeit erfordert dabei Konzentrationen der leitfähigen Phase jenseits der Perkolationskonzentration, die abhängig von der Charakteristik der partikulären Sekundärphase bei ≥ 30 Vol. % liegt.
Eine weitere Lösung stellen diesbezüglich flächige, schichtförmig aufgebaute Heizer aus Siliziumnitrid oder Aluminiumnitrid dar, wie sie von der Fa. Bach RC gefertigt werden [Bac 09]. Darin wird ein isolierendes keramisches Basismaterial mit leitfähigen Phasen wie etwa Metall-Carbiden, -Boriden oder -Siliziden versehen und nach Ausstanzen als Leiterbahn in das Basismaterial eingebracht. Die notwendige Verdichtung dieses Schichtverbundes erfolgt in der Regel durch Heißpressen. Dieser Verbund aus elektrisch leitender Keramik und isolierender Keramik ermöglicht sehr hohe Leistungsdichten, eine gute Alterungs- und Verschleißbeständigkeit und damit eine herausragend lange Lebensdauer. Nachteilig sind der relativ hohe Herstellungsaufwand und die durch die Heißpress-Verdichtung gegebene beschränkte Formenvielfalt. Über ein ähnliches Heißpress-Verbundverfahren wurde ein keramischer „Power Heater“ auf der Basis von Si3N4 als Einsatz in einer Spritzgussform entwickelt und charakterisiert [Hag 11].
Die Leistungsfähigkeit der bereits verfügbaren vollkeramischen Heizelemente eröffnet sich am ehesten im Vergleich ihrer Vorteile gegenüber metallischen Heizelementen, wie:
- hohe Oberflächenleistung bis zu 150 W/cm2 und Strahlungsemission ε > 0,9 mit geringem Energiebedarf
- Temperaturen bis > 1.000 °C, kurze Aufheizzeiten, sehr gute Regelbarkeit dank geringer thermischer Masse
- weitgehend beständig gegen Oxidation, Säuren, Ätzgase, geringe Benetzung mit flüssigen Metallen
- hohe mechanische Festigkeit, Härte und Verschleißbeständigkeit, gute Wärmeleitfähigkeit, hoher Isolationswiderstand
- hohe Steifigkeit und Formstabilität infolge Festigkeits- und E-Modul-Konstanz bis ≥ 1000°
Somit ist ein Nachteil der vorgestellten keramischen Heizelemente ihre begrenzte Herstellbarkeit bezüglich Größe und / oder Formenvielfalt. Sie haben sich zwar in verschiedenen Anwendungen erfolgreich etabliert, werden bislang jedoch kaum in Technologiefeldern mit hohen mechanischen, abrasiven oder korrosiven Beanspruchungen angewandt, wie z.B. der Umformtechnik, wo ein großer Bedarf an schnell reagierenden Heizelementen hoher spezifischer Leistung besteht.
3. Ausgeführte Entwicklungsarbeiten und Ergebnisse
Ein erstes Ziel der Entwicklungsarbeiten bezog sich auf die Verbesserung von Umformwerkzeugen für Faserverbund-Kunststoffe. Dabei erfolgt jeweils ein Aufheizen der „Blanks“ in der Form, die eigentliche Umformung und das Abkühlen. Je rascher dies realisierbar ist, desto kostengünstiger ist der Prozess, weshalb in diesem Technologie-Sektor umfangreiche Entwicklungsarbeiten zur Realisierung schnell heizender und kühlender sogenannter variothermer Werkzeuge ausgeführt werden. Dabei soll innerhalb eines Prozesszyklusses von deutlich weniger als 10 Minuten das Werkzeug von ca. 100 °C auf max. ca. 450 °C geheizt und wieder auf 100 °C gekühlt werden. Keramik, insbesondere dichtes, gesintertes SiC bietet dabei gegenüber Werkzeugstahl eine wesentlich höhere Wärmeleitfähigkeit, Abrasionsbeständigkeit und geringere Wärmedehnung und somit das Potenzial, die Werkzeugdynamik, Lebensdauer und Abformpräzision deutlich zu steigern.
Das dabei mit SiC-Keramiken verfolgte Konzept ist die Kombination eines SiC- Basiswerkstoffes mit hohem spezifischem elektrischen Widerstand, in den Leiterbahnen aus einer SiC-TiB2- Variante mit geringem elektrischem Widerstand eingebracht werden. Die entsprechenden SiC- Werkstoffvarianten wurden bereits in [Woe 16] vorgestellt. Sie sind prinzipiell sinterbar, zeigen ein ähnliches Schwindungsverhalten und attraktive mechanische Eigenschaften. Eine Prinzipskizze und die Ausführung eines derartigen Heizelements, das für Tests im Bereich der variothermen Umformung von Faserverbund- Proben angefertigt und charakterisiert wurde, zeigt Abb.1.

Abb.1: Prinzipskizze des Aufbaus eines intrinsisch beheizten SiC-Elements (links) und die Ausführung als Oberstempel eines Testwerkzeugs (rechts)
Dieses Testwerkzeug wurde angefertigt, indem in eine gepresste Basisplatte aus hoch- ohm-igem SiC durch Grünbearbeitung die Kontur der gewünschten Leiterbahn eingearbeitet wurde. Die Leiterbahn selbst wurde separat aus einem Pressling aus nieder-ohmigem SiC-TiB2 herausgearbeitet, eingepasst und mit einer weiteren ebenen Platte aus hoch-ohmigem SiC abgedeckt. Alternativ können derart ausgelegte Heizelemente auch durch mehrfaches axiales Pulverpressen unter Verwendung von Platzhaltern für die leitfähige Phase hergestellt werden. Eine derartige Auslegung bereitet jedoch beim „freien“ Sintern Schwierigkeiten, so dass es angebracht ist und die Prozess-Sicherheit deutlich erhöht, wenn die Verdichtung druckunterstützt unter Verhinderung einer lateralen Schwindung erfolgt.
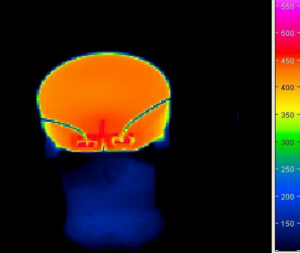
Abb.2: IR-Aufnahme der Wärmeverteilung im SiC- Verbundheizelement (FGK)
Für eine hohe Kühlgeschwindigkeit im Einsatz als variothermes Werkzeug können in die Deckplatte zusätzlich noch durchgängige oder im Kreis geführte Kühlkanäle eingebracht werden und die Verbindung durch Hartlöten erfolgen. Über die elektrische Leitfähigkeit des nieder-ohmigem SiC sowie dem Querschnitt des Heizleiters und der U/I-Strom-Spannungs-Versorgung kann die gewünschte Heizleistung in weiten Grenzen variiert werden, im Falle des Testwerkzeuges werden problemlos die angestrebten 500°C erreicht. Die Gleichmäßigkeit der Erhitzung zeigt die Thermokamera-Aufnahme in Abb.2.
Die Tests dieses keramischen Werkzeuges bestätigten auch die Erwartungen bezüglich eines rascheren Aufheizens und Abkühlens gegenüber Stahl aufgrund der wesentlich höheren Wärmeleitfähigkeit. Bei gleicher Heizleistung wird eine ca. 40% raschere Aufheizung auf die die Zieltemperatur erreicht und diese konstant über den gesamten Versuchszeitraum gehalten.
In gleicher Weise lassen sich wesentlich größere und auch komplexere SiC-Heizelemente ausführen, wie die folgende Prinzipskizze in Abb.3 zeigt.
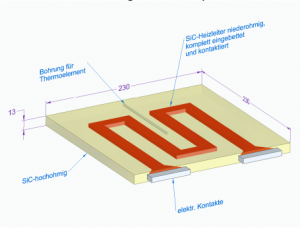
Abb.3: Prinzipskizze eines SiC-basierenden, intrinsisch beheizten Flächenheiz-Element (ohne Deckplatte)
Das niederohmige Heizleiter-SiC kann hier auch in die vorgesehene und vorbereitete Leiterbahn eingepresst werden. Zum Schutz und zur Isolation gegenüber der Umgebung wird noch eine Deckplatte aus hochohmigem SiC aufgebracht. Der gesamte Verbund wird wiederum unter axialem Druck unter Vermeidung einer lateralen Schwindung zum Verbundelement verdichtet. Derartige, in ähnlicher Weise von der Halbleiter-Industrie nachgefragte Heizelemente können quadratisch, rechteckig oder auch rund ausgeführt werden, wobei bezüglich der Abmessungen bei FCTI nur eine Begrenzung durch die verfügbare Heißpresse besteht (max. Ø 400 mm).
Als weiterer Demonstrator wurde ein Umformwerkzeug für Mg-Bleche mit intrinsisch beheizten SiC- Aktivelementen entwickelt und getestet. Das Konzept für diese thermisch aktiven Keramikteile war wiederum ein Werkstoffverbund aus elektrisch leitfähigen sowie isolierenden SiC-Varianten, die die benötigte Wärmemenge durch direkten Kontakt an das umzuformende Blechteil abgeben. Dadurch kann eine definierte Wärmeeinleitung und Temperaturregelung realisiert werden. Dies ist für die Umformung von Mg wichtig, da es aufgrund der hexagonalen Gitterstruktur bei Raumtemperatur nur ein geringes Verformungsvermögen aufweist. Dies verbessert sich mit steigender Temperatur, so dass ab ca. 225°C eine hohe Formänderungsfähigkeit vorliegt, aus anderen Gründen sollte hier jedoch eine Temperatur von 400°C nicht überschritten werden. Abb.4 zeigt den prinzipiellen Ablauf des dreistufigen Verfahrens, Abb.5 das zur Eignungsprüfung und zur Qualifizierung der Keramik- Aktivelemente eingesetzte Technikums-Werkzeug und Testteil [Kol 10].
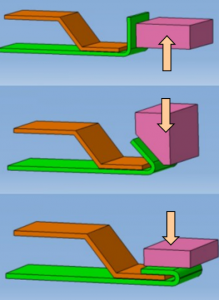
Abb.4: Schematische Darstellung des angewandten thermischen Falzvorgang von Mg-Blechen mit Abkanten, Vorfalzen und Fertigfalzen (WHZ)
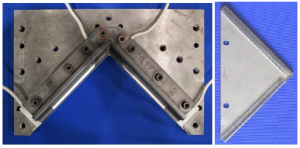
Abb.5: Oberteil des Testwerkzeuges mit SiC-Aktivteil (links, siehe leichte Mg-Adhäsion) und gefalztes Mg- Testteil (rechts); (Bilder: WHZ)
Aufgrund des mehrstufigen Verfahrens waren für die Testwerkzeuge 11 individuell gestaltete leistenförmige SiC- Aktivelemente notwendig mit jeweils für die einzelnen Aufgaben unterschiedlichen Profilen. Beispiele dafür zeigt Abb.6, wobei die eingefügten keramischen Heizelemente rot gekennzeichnet sind.
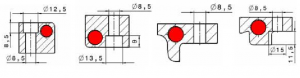
Abb.6: Profile der leistenförmigen SiC-Aktivteile der verschiedenen Falzwerkzeuge
Dieses Design und die ganze konstruktive Auslegung erfordern für einen vertretbaren Herstellungsaufwand eine möglichst endkonturnahe Vorbearbeitung im Grünzustand (inklusive Tiefloch-Bohren) sowie eine Verdichtung durch druckloses Sintern was die ausgewählten SiC-Varianten ermöglichen. Zur Einhaltung exakter Abmessungen sowie von Form- und Lagetoleranzen erfolgt noch eine abschließende Hartbearbeitung. Dadurch unterscheidet sich das hier angewandte Herstellungsverfahren prinzipiell von dem der beschriebenen heißgepressten Si3N4- Heizelemente und ermöglicht eine wesentlich erweiterte Formen- und Gestaltungs- Vielfalt bis hin zu Freiform-Flächen.
Wie anhand der Profilzeichnungen in Abb.6 zu ersehen, wird hier das niedrig- ohmige SiC- Heizelement als Stab in die leistenförmige, hochohmige SiC-Komponente eingebracht. Dies kann einerseits im Grünzustand erfolgen mit sich anschließender Ko-Sinterung. Dabei wird das Endmaß des Heizstabes geringfügig größer auslegt als die Bohrung, so dass die umgebende Komponente beim Sintern auf den Stab aufschwindet und eine sehr gute stoffschlüssige Bindung ausbildet. Es ist aber andererseits auch möglich, den Heizstab separat vorzusintern, auf das erwünschte Endmaß zu schleifen und so in das zu sinternde Basisteil einzusetzen. Dies hat den Vorteil, dass sich auch kleine Heizleiter-Durchmesser realisieren lassen und die Prozesssicherheit erhöht wird. Zum Nachweis der Temperaturgleichmäßigkeit derartiger SiC-Aktivteile wurden Testteile mit 6 Bohrungen für T- Testmessungen konzipiert (Abb. 7 links), Abb.7 rechts zeigt das realisierte SiC-Aktivelement mit eingesintertem Heizelement.
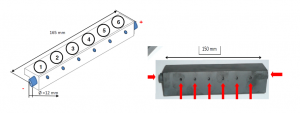
Abb.7: Schematische Darstellung eines intrinsisch beheizten SiC-Aktivteils mit Messbohrungen (links) und das entsprechend gefertigte SiC-Verbundteil (rechts)
Das mit dieser Anordnung erzielte Messergebnis zeigt Abb.8:
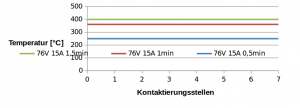
Abb.8: Erwärmungsverhalten des SiC-Aktivelements entlang der Messstellen bei vorgegebener Spannung und Stromstärke (WHZ)
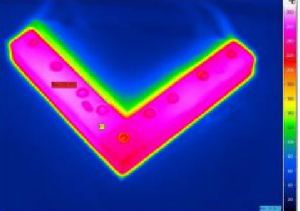
Abb.9: Thermographisches Bild zur T-Gleichmäßigkeit des unteren SiC-Aktivteils des Testwerkzeuges (WHZ)
Mit den gewählten U/I-Werten wurde hierbei nach ca. einer halben Minute eine Temperatur erreicht, wie sie für das Mg-Falzen benötigt wird. Die Homogenität der Erwärmung entlang des Aktivteils erweist sich aufgrund der exzellenten Wärmeleitfähigkeit des SiC als äußerst gleichmäßig. Die weitere Erwärmung auf 400°C wird mit der gewählten SiC- Werkstoff- Kombination und Leistungsversorgung nach 1,5 Minuten erreicht und könnte durch andere Parameter- Kombinationen sicher noch gesteigert werden. Die erzielte sehr hohe Gleichmäßigkeit der Erwärmung der SiC-Aktivteile im Umformwerkzeug zeigt die thermographische Aufnahme Abb.9.
Prinzipiell läßt sich durch die Wahl der niederohmigen SiC-Variante, dem Querschnitt des Heizstabes sowie der angelegten elektrischen Leistung das Aufheizverhalten und die maximal erzielbare Temperatur in weiten Bereichen steuern. Dabei ist wichtig und anwendungsrelevant, dass niederohmige Heizleiter auf Basis SiC-TiB2, wie sie bei diesen Versuchen eingesetzt wurden, zumindest bis nahe 700°C einen positiven T-Koeffizienten (PTC) aufweisen, im Gegensatz zu einem üblicherweise negativen T-Koeffizienten von monolithischen S-SiC [Woe 16]. Dies ist sehr vorteilhaft, da sich mit diesen Compositen als Heizleiter bei einer konstant angelegten elektrischen Spannung eine Selbstregulierung ergibt und eine unkontrollierte Überhitzung vermieden wird.
4. Fazit
Mit den neu entwickelten SiC- basierenden Heizelementen mit arteigener, intrinsischer Beheizung eröffnen sich eine ganze Reihe neuer, innovativer Anwendungen, da durch die Kombination sinterfähiger SiC-Werkstoffvarianten die Form- und Gestaltungsvielfalt gegenüber den bislang kommerziell angebotenen keramischen Heizelementen wesentlich erweitert wird. Getestet wurden diese Heizelemente in Form von Aktivteilen in Werkzeugen für das Ur- und Umformen von Kunststoffen, Compositen und Leichtmetallen. Gegenüber metallischen Heizelementen liegen die Vorteile der SiC-basierenden Elemente in einer nahezu umfassenden Korrosions- und Abrasionsbeständigkeit sowie sehr hohen Wärmeleitfähigkeit. Letzteres ermöglicht eine hohe Temperaturwechsel- Dynamik der Elemente beim Einsatz in variothermen Prozessen mit entsprechenden wirtschaftlichen Vorteilen.
Durch die Wahl der niederohmigen SiC-Variante, dem Querschnitt des Heizleiters sowie der angelegten elektrischen Leistung läßt sich das Aufheizverhalten und die maximal erzielbare Temperatur in weiten Bereichen steuern. In der Kombination mit der erweiterten Formenvielfalt durch die Sinterfähigkeit der SiC-Werkstoffe, werden diverse neue, innovative und ressourcenschonende Anwendungen mit entsprechenden technischen und wirtschaftlichen Vorteilen eröffnet.
FCT Ingenieurkeramik GmbH,
96528 Frankenblick;
www.FCTI.de
Literatur
[Bac 09] Bach, J.P.: „Wärme gezielt dorthin bringen, wo sie benötigt wird“, cfi/Ber.DKG 86 (2009_6) D12-D-13
[Hag 11] Hagen, J. et al.: “Ceramic Power Heater”, cfi/Ber.DKG 88 (2011_4) E23 – E26
[Kol 10] Kolbe, M.: Grundlagenuntersuchungen zu neuen Lösungen gefalzter Erzeugnisse aus Magnesiumflachprodukten. Wachstumskern „TeMaK“, BMBF-Forschungsbericht, 2010
[Kue 13] Kühl, H.: “Hot Stuff – Ceramics for Industrial Heating Applications“, Ceramic Appli cations 1 (2013_2) 60-65
[Woe 16] Wötting, G., Knoch, M., Martin, W.: „Neuartige SiC-TiB2 Composite-Keramiken mit technisch interessanten Eigenschaften“; Werkstoffe 2/2016, 28-31
Die beschriebenen Entwicklungen wurden dankenswerter Weise partiell seitens AiF-ZIM im Rahmen der Projekte „CompoMold“ FKZ KF2288202AG3 (Partner IVW, KL u. FGK, H-Gh) sowie FaMaKer FKZ KF22882003US4 (Partner WHZ, Zwickau) gefördert