Für eine sichere und langzeitstabile Haftung von Verklebungen und Beschichtungen ist eine gute Vorbehandlung auf vielen Materialoberflächen zwingend erforderlich. Der Einsatz von Atmosphärendruckplasma ist ein umweltfreundliches Verfahren, das nicht nur „inline“ die Reinigung, Aktivierung und Nano-Beschichtung auf höchstem Niveau ermöglicht, sondern dazu noch besonders wirtschaftlich arbeitet.
Die sichere Haftung einer Verklebung oder Beschichtung von Materialien wie Kunststoffen, Metallen oder Glas setzt voraus, dass zum einen die Materialoberfläche feinstgereinigt ist, zum andern die Oberflächenenergie des Festkörpers möglichst größer ist, als die Oberflächenspannung des flüssigen Klebstoffs oder Lacks. Es gibt für beide Anforderungen unterschiedliche Vorbehandlungsverfahren, wobei der Einsatz nass-chemischer Substanzen das nach wie vor häufigste ist.
Ein Verfahren, das eine chemische Vorbehandlung komplett ersetzen kann, ist eine von dem westfälischen Anlagenbauer Plasmatreat vor 20 Jahren entwickelte und heute in nahezu allen Industriesparten weltweit eingesetzte Plasmadüsentechnologie. Das Openair-Plasma-Verfahren bewirkt in einem einzigen sekundenschnellen Arbeitsschritt die chemiefreie mikrofeine Reinigung und simultane Aktivierung von Materialoberflächen, insbesondere von Kunststoffen, Metall, Glas und Keramik. (Bild 1)
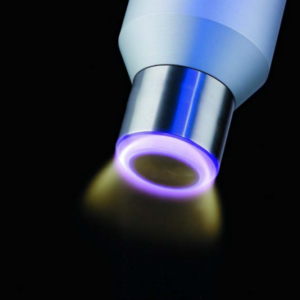
Bild 1: Foto Plasmatreat
Die Plasmatechnologie Openair bewirkt auf umweltfreundliche Weise die mikrofeine Reinigung, hohe Aktivierung und Nanobeschichtung von Materialoberflächen.
Die Folge ist eine hohe Benetzbarkeit der Oberfläche und eine langzeitstabile Haftung von Klebstoffen, Lacken, Farben oder Schäumen. Das Verkleben, Bedrucken oder Lackieren kann unmittelbar nach der Behandlung vorgenommen werden. Das Verfahren ist im voll automatisierten und kontinuierlichen Produktionsprozess einsetzbar. Die Vorbehandlung erfolgt wahlweise inline oder auch außerhalb der Fertigungslinie unter normalen Luftbedingungen. Benötigt werden für den Betrieb allein Druckluft und elektrische Energie, wodurch in der Produktion Emissionen von VOC (Volatile Organic Compounds / leichtflüchtige Kohlenwasserstoffe) von vorneherein vermieden werden.
Reinigen und Aktivieren in einem Schritt
Ohne die hohe Aktivierung, die beispielsweise ein unpolarer Kunststoff wie ein Polypropylen durch den Plasmaprozess erfährt, gäbe es Benetzungsprobleme, die eine Beschichtung unmöglich machen würden. Dr. Alexander Knospe, Innovationsleiter bei Plasmatreat erläutert die chemischen Vorgänge: „Bei der Plasmavorbehandlung wird die Oberflächenenergie des Kunststoffes stark erhöht, indem polare Gruppen, wie Hydroxylfunktionen, auf der Oberfläche erzeugt werden. Dadurch wird zum einen die vollflächige Benetzung mit einem gegebenen Lack oder Klebstoff möglich und zum anderen deren kovalente Bindung, d.h. eine sehr stabile Atombindung, an die Oberfläche.“ Die Folge sind homogene Lackverläufe und eine langzeitstabile Haftung von Verklebungen und Beschichtungen auch bei sehr hoher Beanspruchung. Versuche bei Plasmatreat haben ergeben, dass durch die Plasmavorbehandlung von Kunststoffen in vielen Fällen Oberflächenenergiewerte über 72 mJ/m² möglich werden (Bild 2).
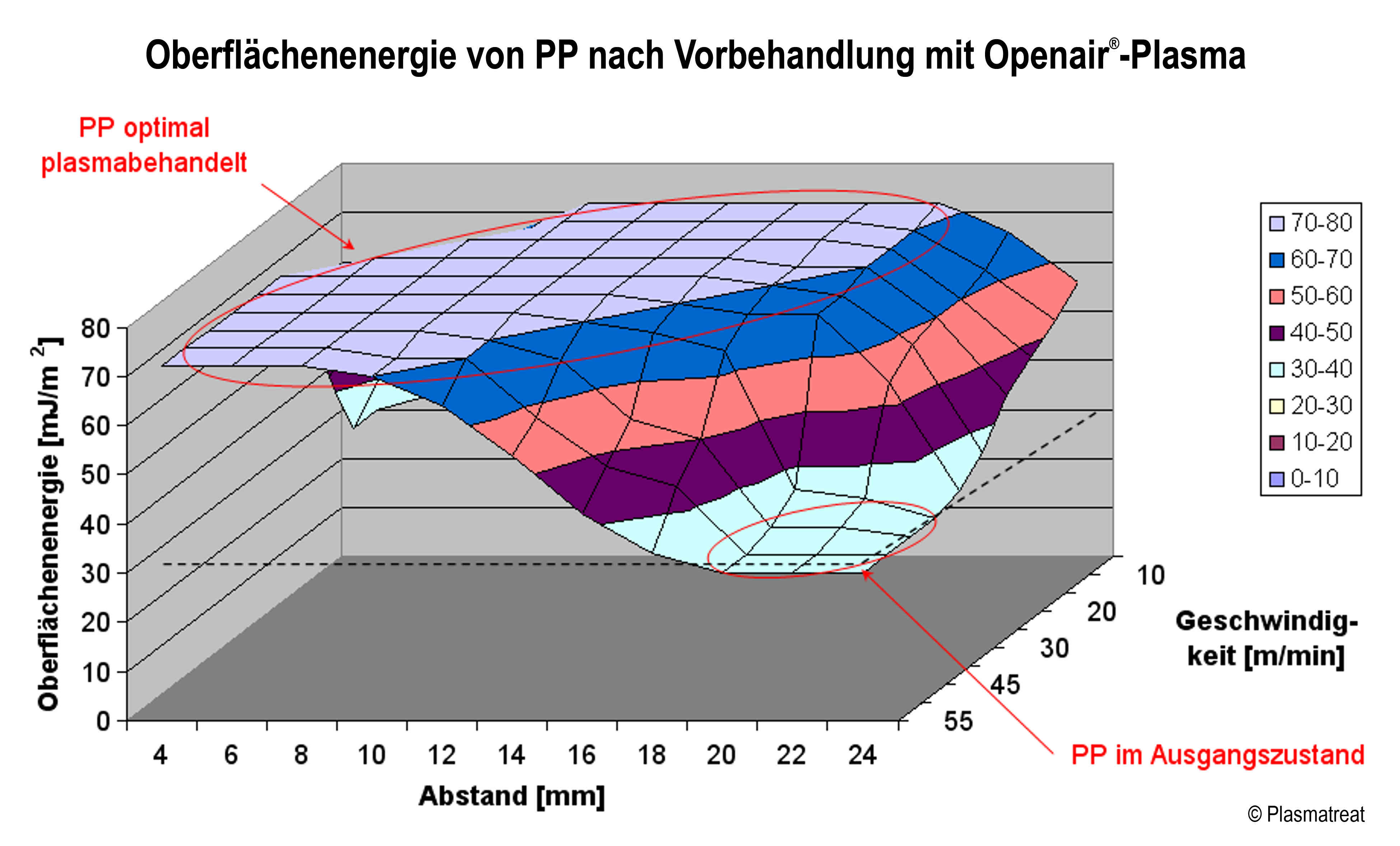
Bild 2. Grafik Plasmatreat
Die Graphik zeigt eine unpolare Kunststoffoberfläche, die in Abhängigkeit von Abstand und Geschwindigkeit mit Plasma vorbehandelt wurde. Die Oberfläche wird nach der Behandlung polar und die Oberflächenenergie steigt auf >72mJ/m² bei großem Prozessfenster.
Statische Entladung
Trifft das Plasma auf eine Oberfläche, können die elektrischen Ladungsträger des statisch aufgeladenen Werkstücks gegen Erde abfließen, d. h. es erfolgt eine statische Entladung. Ein großer Vorteil, da Unreinigkeiten aus der Umgebungsluft nun von der im Folgeprozess zu verklebenden oder zu lackierenden Oberfläche nicht mehr angezogen werden. Die Intensität der Plasmabestrahlung ist so hoch, dass Bearbeitungsgeschwindigkeiten von mehreren 100m/min erreicht werden können.
Beschichtung
Plasmatreat gelang es vor wenigen Jahren als erstem Unternehmen weltweit, eine unter Atmosphärendruck erfolgende Plasmabeschichtung in der Industrie zur Serienreife zu bringen. Die in enger Zusammenarbeit mit dem Fraunhofer IFAM, Bremen entwickelte und patentierte PlasmaPlus -Technologie ermöglichte erstmals die ortsselektive funktionale Beschichtung von Materialoberflächen unter Atmosphärendruck. Schichtfunktionen sind beispielsweise die Haftvermittlung oder ein hoher Korrosionsschutz. Zur Erzeugung einer Schicht wird dem Plasma eine siliziumorganische Verbindung beigemischt. Durch die hochenergetische Anregung im Plasma wird diese Verbindung fragmentiert und scheidet sich auf einer Oberfläche als glasartige Schicht ab. Die chemische Zusammensetzung kann je nach Anwendungsfall variiert werden, um auf unterschiedlichen Materialien die jeweils besten Resultate zu erzielen.
Lösemittelfreie Verklebung von Kunststoffen
Zieltechnologien für eine Openair-Plasmabehandlung in der Kunststoffindustrie sind das 2K-Spritzgussverfahren sowie vor- und nachgeschaltete Prozesse wie das Lackieren, Verkleben, Bedrucken, Schäumen und Beschichten von Kunststoffoberflächen. Durch die hohe Aktivierungsfähigkeit des Plasmas können bislang inkompatible Substrate verbunden werden. Auch können Maskierungsprozesse, die z.B. bei der Vorbehandlung mit Flamme häufig erforderlich sind, komplett entfallen, da die Plasmadüse ortselektiv arbeitet, d.h. ganz gezielt nur die gewünschten Bereiche aktiviert (Bild 3).
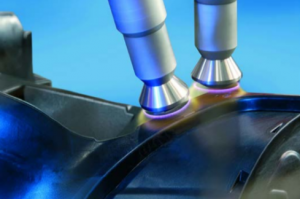
Bild 3, Foto: Plasmatreat
Die robotergesteuerten ortsselektiv arbeitenden Plasmadüsen machen Maskierungsprozesse bei der Vorbehandlung von Kunststoffen unnötig.
Ebenso bedeutend ist, dass nun die Haftung von wasserbasierenden, also lösemittelfreien Klebstoff- oder Lacksystemen auf sehr klebstoffunfreundlichen (unpolaren) Kunststoffen möglich ist. Darüber hinaus besitzt die Technik ein großes Potential zur Feinreinigung und Verbesserung der Adhäsion in der Mehrkomponententechnik bei Kunststoff-Metall-Verbunden.
Eine neue Plasma-Großpaneelanlage erlaubt u.a. die großflächige Aktivierung von Honeycomb-Verbundpaneelen – genauer gesagt die Behandlung der feinen Stege der Polypropylen-Wabenkernschicht – ohne jeglichen Einsatz von Primer. Damit wird selbst die langzeitstabile Verklebung von Deckschichten aus Stahl gewährleistet. Das Verfahren gilt als Durchbruch für die zukünftig kostengünstige Herstellung von Verbundpaneelen, deren Kernmaterial nun auch mit weit günstigeren Materialien, wie z.B. recycelten Kunststoffen, variiert werden kann.
Plasmabeschichtung von Aluminium
Übliche automatisierte Chromatierungsverfahren behandeln das gesamte Bauteil. Nicht zu beschichtende Stellen müssen durch Masken abgedeckt oder die Schicht muss in einem folgenden Arbeitsschritt wieder entfernt werden. Da meist nur ein kleiner Bereich des gesamten Bauteils überhaupt mit dem Klebstoff in Verbindung kommt, wäre eine automatisierte, ortsselektive Vorbehandlung für die Hersteller von großem Interesse. Die Vorbehandlung der zu verklebenden Oberflächen erfolgt sehr häufig durch den manuellen Auftrag von lösemittelhaltigen Reinigern, von Beize oder Haftvermittlern. Ein kostenintensives, unbeständiges und darüber hinaus für den Bediener möglicherweise gesundheitsgefährdendes Verfahren.
Das PlasmaPlus Verfahren bietet hier eine umweltfreundliche und hocheffiziente Alternative, die heute bereits im Fahrzeugbau und in der Solarindustrie zur Anwendung kommt. Die abgeschiedene antikorrosiv wirkende Haftvermittlerschicht bewirkt nicht nur einen hohen Korrosionsschutz, sondern ist auch ein exzellenter Haftgrund für viele Klebstoffe (Bild 4).
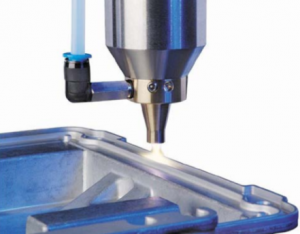
Bild 4. Foto Plasmatreat
Die mit der PlasmaPlus-Technik abgeschiedene antikorrosiv wirkende Haftvermittlerschicht bewirkt nicht nur einen hohen Korrosionsschutz, sondern ist auch ein exzellenter Haftgrund für viele Klebstoffe.
Die Korrosionsschutzwirkung ist besonders effektiv bei Aluminiumlegierungen: Die Schicht vermag das Aluminium mehrere Tage lang gegenüber direktem Salzsprühnebel (DIN 50021) zu schützen, ohne dass das Metall optisch beeinflusst wird. Bei TRW Automotive, Weltmarktführer für Fahrzeug-Sicherheitssysteme, wird die PlasmaPlus Technik bei Motor-Pumpengehäusen seit Jahren zur Lenkunterstützung eingesetzt. Zur Vermeidung von Korrosion werden bei diesem sicherheitsrelevanten Bauteil Klebenähte metallischer Bauteiloberflächen im vollautomatischen Produktionsprozess plasmabeschichtet.
Potentialfreier Plasmastrahl für die Elektronik
Eine Besonderheit des Openair Verfahrens ist der elektrisch nahezu neutrale Plasmastrahl. Eine Eigenschaft, die seine Anwendbarkeit stark erweitert und vereinfacht. In der Elektronikindustrie gehört die Technologie deshalb zu den neuen Verfahren, um Bauteile und Schaltkreise während der Herstellung und/oder Konfektionierung zu bearbeiten. Hohe Reinheitsanforderungen werden dabei ebenso realisiert wie eine potentialfreie Behandlung, d.h. die Schaltungen kommen während der Plasmabehandlung nicht mit elektrischer Spannung in Berührung. Bei elektronischen Bauteilen setzt der Hersteller besonders schonend arbeitende patentierte Rotationsdüsen ein, die die Vorbehandlungswirkung durch das Rotationsprinzip sehr gleichmäßig auf die Arbeitsflächen verteilen. Dabei wird die Oberfläche mehrmals kurzzeitig, pulsartig überstrichen, was eine äußerst effektive Form der Reinigung und Aktivierung bei gleichzeitig geringem Wärmeeintrag darstellt.
Von allergrößter Wichtigkeit ist die Potentialfreiheit des Plasmas beispielsweise bei dem Avionikspezialisten Rohde & Schwarz. Die kunststoffummantelten Bauteile der bestückten Leiterplatten von Flugfunkgeräten für Langstreckenflugzeuge werden hier zur Haftungserhöhung der Schutzlackierung (Conformal Coating) mit der Plasmatechnik aus Westfalen vorbehandelt. Die hochsensible Elektronik nimmt dabei nicht den geringsten Schaden.
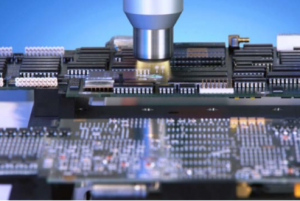
Bild 5, Foto: Plasmatreat
Das potentialfreie Plasma aktiviert die kunststoffummantelten Baugruppen vor dem Conformal Coating ohne die hochsensible Elektronik zu beschädigen.
In der Automobilindustrie schützen namenhafte Zulieferer mit dem Verfahren ihre hochsensiblen Sensoren und Steuerungselemente. Diese übernehmen wichtige Aufgaben, wie z.B. das Motor- oder Klimamanagement, regeln Brems- und Fahrwerksysteme oder steuern das Beleuchtungssystem. Gemäß der IEC-Norm und den IP-Schutzarten müssen die Sensoren und Steuerungselemente vor dem Eindringen von Feuchtigkeit und Verschmutzung geschützt werden. Die Anforderungen an die Dichtigkeit der Schutzgehäuse aus Kunststoff oder Aluminium sind entsprechend hoch. Die Plasmabehandlung gewährleistet hier die absolute Dichtigkeit im Klebprozess.
Zusammenfassung
Die Openair- Plasmatechnik ist ein umweltfreundliches und besonders wirtschaftliches Vorbehandlungsverfahren. Mit ihm können nicht nur Arbeitsschritte eingespart und Betriebskosten gesenkt, sondern auch Durchsatz und Produktqualität entscheidend erhöht werden. Alle verwendeten Düsensysteme sind uneingeschränkt roboterkompatibel und können vom Anwender immer in-line, also direkt in die neue oder auch bereits bestehende Fertigungslinie, integriert werden. Das Verfahren ist im voll automatisierten und kontinuierlichen Produktionsprozess einsetzbar und zeichnet sich nicht nur durch seine Effektivität, sondern vor allem auch durch eine hohe Prozesssicherheit und Reproduzierbarkeit aus.
Autor: Inès A. Melamies ist freie Fachjournalistin und Inhaberin des internationalen Pressebüros Facts4You, www.facts4you.de
Fachartikel aus Werkstoffe in der Fertigung 5/2015