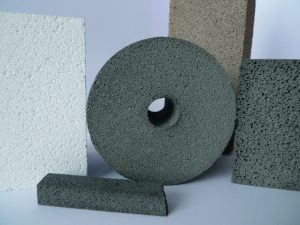
Bild 1: Direktgeschäumte keramische Bauteile aus verschiedenen Materialien mit unterschiedlicher Porosität.
Die Aufgabe des Fraunhofer-Instituts für Keramische Technologien und Systeme IKTS ist es, neueste Entwicklungen auf dem Gebiet keramischer Werkstoffe und Technologien in marktfähige, international führende Produkte und Prozesse umzusetzen. Die Bandbreite reicht dabei von traditionellen Keramiken für Strukturanwendungen bis hin zu komplexen Mischsystemen in der Funktionskeramik oder Energietechnik.
Bauteile aus poröser Hochleistungskeramik stellen eine besondere Werkstoffgruppe dar. Die Erzeugung der Poren ist über unterschiedlichste Verfahren mit nahezu allen Werkstoffen möglich. Für den erfolgreichen Einsatz müssen die Fertigungstechnologien für den entsprechenden Markt angepasst werden. Die speziellen Eigenschaften der Keramik werden verstärkt in der Umwelt und Verfahrenstechnik eingesetzt. Oberflächenbehandlungen und Reinigungsverfahren profitieren ebenso von Innovationen wie Meßtechnik- und Überwachungsaufgaben. Das Potential wird nur von der Kreativität der Anwender begrenzt.
Direktschäumung keramischer Suspensionen
Mit angepassten Technologie wurde am Fraunhofer IKTS eine Vielzahl keramischer Schäume aus verschiedensten Materialien mit angepasster Porenstruktur entwickelt. Diese werden unter anderem für Wärme- oder Schalldämmanwendungen, im Leichtbau, als Filtermaterial oder zur Reduktion der Wärmekapazität eingesetzt.
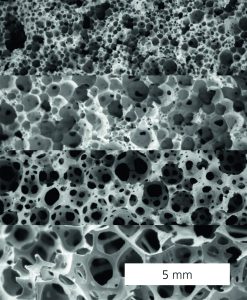
Bild 2: Porenmorphologie verschiedener direktgeschäumter Keramiken.
Das Direktschaumverfahren ermöglicht beispielsweise die Herstellung hochporöser Keramiken mit geschlossener oder (teilweise) offener Porosität. Die Poren können durch verschiedene Methoden direkt in die strukturgebende Phase eingebracht werden. Hierfür nutzt man chemisch wirkende Treibmittelprozesse oder physikalische Dampfdruckerzeugung. Ein besonders ökonomisches und ökologisches Verfahren ist das Einbringen von Luft durch Begasen und/oder mechanisches Einrühren der Gasphase in eine Suspension unter Verwendung von Tensiden. Der entstandene Nassschaum wird anschließend in eine Form gefüllt, getrocknet, entformt und wärmebehandelt.
Am Fraunhofer IKTS wurde ein Schaumgenerator entwickelt und patentiert. Dieser erlaubt eine kontinuierliche und im Vergleich zu herkömmlichen Rotor-Stator-Systemen nahezu verschleißfreie Erzeugung geschäumter Keramiksuspensionen. Im Inneren des Geräts werden die durch eine Pumpe zugeführte Suspension und die über ein Begasungsrohr eingebrachten Luftblasen mit einem statischen Mixer zu einem homogenen Schaum vermischt. Die Porosität des resultierenden Schaums kann über das Volumenstromverhältnis von Suspension und Luft genau eingestellt werden auf Werte zwischen 30 und 95 Vol.-%. Die Porengröße ist von den verbauten Komponenten (Porengröße des Begasungsrohres und Durchmesser des statischen Mischers) abhängig und kann im Bereich zwischen 100 µm und 2 mm variiert werden. Mit dem entwickelten Schaumgenerator ist eine getaktete Produktion von 10 bis 300 l/h Nassschaum möglich.
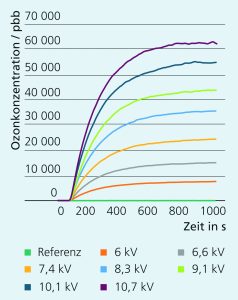
Bild 3: Entwicklung der Ozonproduktion über die Zeit.
Keramikelektroden und Kaltplasma – Kombination für effiziente Abwasser- und Oberflächenbehandlung
Die Reinigung anfallenden Abwässer oder funktionaler Oberflächen erfordert neue Techniken und Verfahren, um den wachsenden Anforderungen gerecht zu werden. Umweltschutz und Energieeffizienz erhalten hier steigende Bedeutung. Einen Ansatz zur Beseitigung problematischer chemischer und biologischer Kontaminationen bietet die Kaltplasmatechnik. Kalte Atmosphärendruckplasmen können energetisch effizient und mit technisch alltagstauglicher Ausrüstung bereitgestellt werden. Allerdings sind die Anlagen dieser relativ neuen Technologie noch nicht so weit ausgereift, dass ein wartungs- und fehlerfreier Betrieb über längere Zeiträume möglich ist. Damit Plasma zur kommerziellen Reinigung eingesetzt werden kann, sind insbesondere werkstoffliche und konstruktive Anpassungen an den elektrisch wie chemisch-korrosiv stark beanspruchten Elektroden essenziell. Plasmaelektroden bestehen aus zwei funktionalen Grundkomponenten – einem elektrischen Isolator und einem elektrischen Leiter. Insbesondere der Isolator definiert mit seinen werkstofflichen Eigenschaften die Qualität und Ausprägung des erzeugten Plasmas, welches primär über die elektrischen Parameter Spannung und Frequenz generiert wird. Die elektrische Permittivität und die Durchschlagfestigkeit des Isolators bieten die Möglichkeit, entweder sehr hohe Frequenzen oder auch elektrische Hochspannungen auf einem niedrigen Level einzusetzen. Innerhalb des Plasmas entstehen so extrem hohe Elektronentemperaturen, ohne dass die eigentliche Gastemperatur der Luftbestandteile wesentlich über 40 °C liegen muss. Durch dieses Phänomen wird es möglich, selbst Mikroorganismen, schädliche chemische Substanzen oder Radikale auf temperaturempfindlichen Unterlagen zu beseitigen. Als Nebeneffekt kann Ozon (O3 ) entstehen, das als reaktive Substanz zahlreiche Schadstoffe neutralisieren kann. Die Nutzung des Plasmas z.B. zur Abwasserreinigung erfordert die Umgestaltung der Plasmaelektrode, z. B. eine Kombination mit zellularen oder porösen Komponenten. Alternativ kann die Wassereinbringung als Aerosol im Plasma eine Option sein. Am Fraunhofer IKTS wurden Untersuchungen mit titanoxidbasierten Keramikwerkstoffen durchgeführt. In Kooperation mit der Hochschule für Angewandte Wissenschaft und Kunst HAWK Göttingen liefen erste Versuche zur Kaltplasmageneration mit derartigen Elektroden (FKZ: IGF 20546 BG). Die Ergebnisse sind vielversprechend, vergleicht man beispielsweise die Ozonentstehung als Effizienzindikator mit anderen bisher eingesetzten Isolatorwerkstoffen. Gegenüber Kunststoffen bieten keramische Isolatoren zudem eine deutlich längere Alterungsbeständigkeit, so dass die bisher erforderlichen Wartungsintervalle in Zukunft vollständig entfallen könnten.
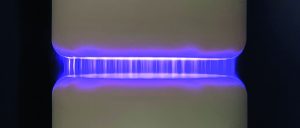
Bild 4: Kaltplasma, im Bild lila (Quelle: Hochschule für Angewandte Wissenschaft und Kunst Göttingen).
Füllstände von Behältern mit geführten Wellen präzise online bestimmen
Die präzise Kenntnis der Füllstände in nicht einsehbaren Behältern ist vor allem in der chemischen Industrie oft eine große Herausforderung. Dabei können mit diesem Wissen Prozesse optimiert und Systemausfälle oder Havarien vermieden werden. Ein permanenter Messbetrieb ist hierbei in verschiedensten Betrieben notwendig. Die meisten kommerziellen Füllstandmessverfahren, wie Schwimmkörper, Drucksensoren, Ultraschall Pulse-Echo-Verfahren, geführte Radarwellen oder kapazitive Messungen sind nicht in der Lage, Mehr- und insbesondere Feststoffphasen zuverlässig zu messen. Oft müssen Messungen der mehrphasigen Füllstände im laufenden Betrieb durchgeführt werden, während die Behälter hohen Drücken ausgesetzt sind oder korrosive Medien enthalten. Es ist auch möglich, dass die Behälter zusätzlichen Sicherheitsvorschriften unterliegen, wie Hochdrucktanks in der Öl- und Gasindustrie, die verschiedene Phasen des Rohölstroms gravitativ voneinander trennen. Ablagerungen oder schnelle Änderungen der Zusammensetzung des Zuflusses können die Betriebseffizienz verringern oder unerwünschte, kostspielige Ausfallzeiten verursachen. Das ließe sich durch eine zuverlässige nicht-invasive Online-Messung ausschließen. Ein neuer Ansatz für Füllstandsmessung basiert auf der am Fraunhofer IKTS entwickelte Lösung durch den Einsatz von geführten elastischen Wellen. Diese werden an der Außenwand eines Behälters durch eine skalierbare Anordnung von piezoelektrischen Aktuatoren angeregt und anschließend gemessen. Entlang ihres Laufweges auf der Außenwand interagieren die aktiv angeregten geführten Ultraschallwellen mit dem Medium im Inneren des Behälters – je nach dessen viskoelastischen Eigenschaften, der Wellenmode sowie dem angeregten Frequenzbereich. Dadurch können zahlreiche Messeffekte genutzt und kombiniert werden, wobei der Haupteffekt eine scheinbare Dämpfung durch Konvertierung in Raumwellen und andere Oberflächenwellen ist. Ein tomographischer Ansatz ermöglicht ein virtuelles Abbild der scheinbaren Dämpfung auf der Außenwand, das dem Behälterinhalt entspricht (Dämpfungstomographie). Das entwickelte Messsystem ist für Behälter verschiedener Geometrien mit und ohne Isolierung geeignet. Zusätzlich verfügt es über eine elektromechanische Selbsttestroutine sowie die Fähigkeit, Wanddickenänderung durch Korrosion und strukturelle Defekte mittels geführter Wellen zu erfassen. Es gibt viele weiter Anwendungen keramischer Werkstoffe in der Fertigung über die wir an dieser Stelle gerne laufend berichten. Sie bilden Schlüsselkomponenten für weitere Innovationen.
Weitere Informationen: www.ikts.fraunhofer.de