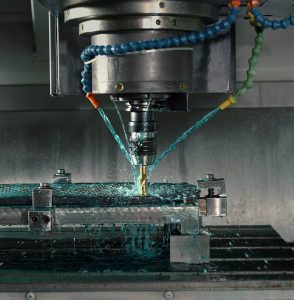
Das richtige Wälzlager optimiert Produktivität und Leistung (Bild: The Timken Company)
Vertikale und horizontale Bearbeitungszentren sehen sich unterschiedlichsten Anforderungen ausgesetzt. Durch die Auswahl eines Lagers, das zur Erfüllung dieser Anforderungen konfiguriert ist, lassen sich sowohl die Produktivität als auch die Leistung verbessern.
Es ist noch gar nicht so lange her, dass ein typisches Werk für Automobilmotoren oder -getriebe zahlreiche Maschinen betrieb, von denen jede einem spezifischen und eng definierten Zweck diente. Diese Ansammlung von Einzweckmaschinen wurde in eine Transferstraße integriert, auf der ein unbearbeitetes Werkstück transportiert wurde, wobei jede Maschine einen eng definierten Satz von Fräs-, Bohr- oder Gewindebohrarbeiten ausführte – auch als Arbeitszyklen bezeichnet – die den Rohling in ein Fertigteil verwandelten. Die Spindellager in diesen Maschinen wurden für den jeweiligen spezifischen Arbeitszyklus optimiert.
Aber die Zeiten haben sich geändert und die typischen Werksanlagen ebenso. In den heutigen Werksanlagen wurden die Transferstraßen durch flexible CNC-Bearbeitungszentren ersetzt, um die Effizienz für kleinere Stückzahlen und häufigere Produktwechsel zu erhöhen. Diese weltweit eingesetzten CNC-Automaten umfassen 3- bis 9-achsige Fräsen (typisch sind fünf Achsen) und verwenden automatische Werkzeugwechsler, Magazine, Karusselle und robotische Transportanlagen für Werkstücke, um eine Reihe von Arbeitsschritten durchzuführen, die Zykluszeiten zu reduzieren und einen effizienten Betrieb der Fertigungsanlage zu gewährleisten.
Aber in der Welt der maschinellen Bearbeitung haben unterschiedliche Aufgaben verschiedene Anforderungen. Viele dieser unterschiedlichen Arbeitsschritte und Werkstoffe haben genau entgegengesetzte Anforderungen an die Frässpindel und somit an das Frässpindellager. Werkstoffe können von herkömmlichen hochlegierten Stählen und Gusseisen bis zu Aluminium-, Titan- und Nickellegierungen reichen. Der Werkstoff und das spanende Bearbeitungsverfahren bestimmen die anzuwendenden Lasten und Drehzahlen, was weitere Konsequenzen für das Lager mit sich bringt.
Es gibt nur wenige Einzelkomponenten, die die Gesamtleistung so stark beeinflussen wie das Frässpindellager. Die Lager bestimmen die Drehzahl, die Tragfähigkeit, die Präzision und die Steifigkeit. Die Lager tragen zur Betriebstemperatur der Spindel bei und sind mitverantwortlich für Vibrationen und die Geräuschentwicklung während des Betriebs. Werkzeugmaschinen müssen äußerst genau und zuverlässig arbeiten und dabei hohe Produktivität erreichen können. Die Präzision eines Lagers hat einen erheblichen Einfluss auf seine Fähigkeit, in typischen Fertigungsumgebungen bestehen zu können. Bei einem Lagerausfall muss die gesamte Maschine zur Reparatur außer Betrieb genommen werden.
Die optimale Leistung ist in hohem Maße abhängig von der Auswahl des richtigen Lagers für die jeweilige Bearbeitungsanwendung. Egal, ob Sie ein Konstrukteur von Werkzeugmaschinenspindeln eines Erstausrüsters oder eines Instandhaltungs-, Reparatur- und Überholungsdienstes sind – die Anforderungen der Endanwendung sind von entscheidender Bedeutung für die Lagerauswahl.
Vergleich der Anforderungen unterschiedlicher Aufgaben
Für eine gegebene Bearbeitungsanwendung können Drehzahlen, Lasten und weitere Faktoren erhebliche Unterschiede aufweisen.
Die Schlichtbearbeitung wird verwendet, um eine optimale Oberflächenbeschaffenheit bei minimalem Rattern zu erzeugen, während bei der Schruppbearbeitung die maximale Materialmenge in der kürzesten Zeit entfernt wird. Das Schlichten erfolgt oberflächlich und präzise mit einem kleinen Werkzeugdurchmesser bei sehr hoher Spindeldrehzahl und niedriger Vorschubgeschwindigkeit (Lineargeschwindigkeit des Werkzeugs durch das Werkstück). Die erzeugten Werkzeuglasten sind somit sehr klein, die Spindel muss jedoch gute Leistung bei sehr hohen Drehzahlen aufweisen. Beim Schruppen werden Fräsen mit großem Durchmesser verwendet, die bei relativ niedrigen Spindeldrehzahlen und sehr hohen Vorschubgeschwindigkeiten arbeiten, wodurch eine erheblich höhere Last auf das Werkzeug wirkt, das durch die Spindellager unterstützt wird.
Optimale Lagerauswahl
Die oben beschriebenen unterschiedlichen Bedingungen haben jeweils eigene Anforderungen an das Frässpindellager.
Die Anforderungen für Schruppen und Schlichten sind entgegengesetzt und deshalb ist eine unterschiedliche Lagerleistung erforderlich (niedrige Drehzahl/hohe Lasten bzw. hohe Drehzahl/niedrige Lasten). Der Grund: Bei zunehmender Drehzahl erhöht sich in allen Anwendungen auch die Zentrifugalkraft auf die einzelnen Kugeln innerhalb des Spindellagers.
Diese Zentrifugalkraft wirkt radial vom Mittelpunkt der Lagerdrehung nach außen (unter Annahme eines sich drehenden Bezugssystems), wobei die äußere Laufbahn verhindert, dass die Kugeln aus dem Lager herausgeschleudert werden. Als Folge der zunehmenden Zentrifugalkraft an diesem Punkt erhöht sich die Kontaktspannung zwischen der Laufbahn und den Kugeln. Die erhöhte Zentrifugalkraft verschiebt außerdem den Punkt, an dem jede Kugel die äußere Laufbahn berührt, zum unteren Ende der Laufbahn hin. Genau das Gegenteil passiert jedoch zwischen der Kugel und der inneren Laufbahn, mit dem Ergebnis, dass die inneren und äußeren Kontaktwinkel nicht gleich sind. Dieses Phänomen wird als Kontaktwinkel-Verschiebung bezeichnet. Weil die Kugel ein Festkörper ist, kann sie nur eine Drehachse besitzen und die erhöhte Kontaktwinkel-Verschiebung führt deshalb zu einer Gleitbewegung, mehr Wärmeerzeugung, höheren Betriebstemperaturen und einem höheren Oberflächenverschleiß der Kugeln.
Eine Methode zur Minimierung der Auswirkungen der höheren Zentrifugalkraft besteht darin, das Gewicht der Kugeln zu reduzieren. Dies lässt sich auf zweierlei Weise erreichen: 1) Reduzierung der Kugelgröße und/oder 2) Umrüstung von Stahl- auf Keramikkugeln, die 40 Prozent leichter sind als die entsprechenden Stahlkugeln. Die leichteren Kugeln erzeugen eine geringere Zentrifugalkraft, die die höhere Kontaktspannung aufgrund des höheren Elastizitätsmoduls des Keramikwerkstoffs nicht vollständig kompensiert. Die geringere Zentrifugalkraft reduziert jedoch die Kontaktwinkel-Verschiebung, was zu weniger Wärmeerzeugung aufgrund der Gleitbewegung führt.
Eine zweite Methode ist die Vergrößerung des Laufbahnradius. Das Verhältnis von Laufbahnradius zu Kugeldurchmesser wird als Laufbahnkrümmung bezeichnet und in Prozent ausgedrückt. Bei einem Laufbahnradius von 0,5 mm und einem Kugeldurchmesser von 1 mm beträgt die Laufbahnkrümmung beispielsweise 50 Prozent. Eine Laufbahnkrümmung von 50 Prozent bedeutet Umfangskontakt und das Lager würde sich nicht frei drehen, so dass Krümmungen immer größer als 50 Prozent sind. Krümmungen unter 54 Prozent werden als geschlossen bezeichnet, während größere Krümmungen als offen bezeichnet werden. Lager mit geschlossenen Krümmungen zeichnen sich durch höhere Tragfähigkeiten aus, erzeugen jedoch mehr Wärme, während offene Lager schneller laufen können, aber reduzierte Tragfähigkeiten besitzen.
Durch die Verwendung jeder dieser beiden Maßnahmen zur Erhöhung der „Drehzahlfähigkeit“ kann die Tragfähigkeit des Lagers drastisch reduziert werden und somit auch die Fähigkeit der Spindel zur Schruppbearbeitung. Normalerweise stehen für eine gegebene ISO-Maßreihe zwei bis drei Ausführungen zur Verfügung, die zur Leistungsoptimierung eines bestimmten Fräsprofils unterschiedliche Kugelgrößen und Krümmungen aufweisen. Deshalb ist es wichtig, den beabsichtigten Arbeitszyklus einer Werkzeugmaschine zu berücksichtigen, damit die beste Konstruktion und das optimale Kugelmaterial ausgewählt werden können.
Einige Beispiele
Schruppbearbeitung und maximaler Metallabtrag. Spindeln für schwere Werkzeuglasten sollten Lager mit den für den Lagerquerschnitt größtmöglichen Stahlkugeln besitzen (>50 Prozent des Lagerquerschnitts) und eine geschlossene Krümmung aufweisen, um die Kontaktspannung zwischen der Laufbahn und den Kugeln zu reduzieren. Der große Kugeldurchmesser und die geschlossene Krümmung sind gut geeignet für die beim Schruppen auftretenden schweren Lasten und niedrigeren Drehzahlen, die je nach Fräsendurchmesser, Zeitspanungsvolumen und Werkstückmaterial zwischen 500 und 1.000 Umin-1 liegen. Die meisten Spindeln zur Schruppbearbeitung sind fettgeschmiert und je nach Maschinengröße für Drehzahlen von 3.500 Umin-1 bis 7.500 Umin-1 ausgelegt.
Schlichtbearbeitung und maximale Drehzahlen. Bei der Entwicklung von Spindeln für höhere Drehzahlen zur Schlichtbearbeitung sollte die Minimierung der Wärmeerzeugung das Leitprinzip sein. Dabei ist die oben beschriebene Kombination aus großen Kugeln und geschlossener Krümmung aufgrund der konstruktionsbedingt übermäßig starken Wärmeerzeugung weniger wünschenswert. Durch Auswahl kleinerer Kugeln (<50 Prozent des Lagerquerschnitts) und einer offenen Krümmung lässt sich die Wärmeerzeugung und somit die Spindeltemperatur reduzieren. Hochgeschwindigkeitsspindeln zur Schlichtbearbeitung arbeiten bei Drehzahlen zwischen 7.500 Umin-1und 24.000 Umin-1 und werden mithilfe präzise dosierter Luft-Öl-Schmierung geschmiert. Die meisten Spindeln zur Schlichtbearbeitung sind je nach Maschinengröße für Drehzahlen von 15.000 Umin-1 bis 30.000 Umin-1 ausgelegt.
Mehrzweckanwendungen – Optimiert für Last und Drehzahl. Wenn das Designziel eine Spindel ist, die sowohl grobe Bearbeitung bei niedrigen Drehzahlen als auch Feinbearbeitung bei hohen Drehzahlen ausführen kann, ist es wichtig, ein Lager auszuwählen, dass diese beiden gegensätzlichen Anforderungen erfüllen kann. Diese Anforderungen – und alles was dazwischen liegt – sind bei vertikalen Bearbeitungszentren üblich. Hier sollten die Entwickler ein Präzisionslager mit ausgewogenen Eigenschaften auswählen, das die Lücke zwischen den beiden Extremzuständen schließen kann. Ein Lager mit mittelgroßen Kugeln (ca. 50 Prozent des Lagerquerschnitts) und mit mäßig offener Krümmung ergibt eine relativ niedrige Wärmeerzeugung und eine angemessene Tragfähigkeit. Bei Fräsen, die sowohl Schrupp- als auch Schlichtarbeiten ausführen müssen, können Drehzahlen von 500 Umin-1 bis zu 12.500 Umin-1 auftreten. Sie werden entweder mit Fett oder mit einer präzise dosierten Luft-Öl-Mischung geschmiert. Mehrzweckspindeln sind normalerweise je nach Maschinengröße für Drehzahlen von 7.500 Umin-1 bis 15.000 Umin-1 ausgelegt.
Keramikkugeln. Keramikkugeln werden oft ausgewählt, wenn der Arbeitszyklus der Spindel in erster Linie aus Schlichtbearbeitungsschritten bei hohen Drehzahlen besteht. Neben ihrer geringeren Dichte bzw. ihrem kleineren Gewicht haben Keramikkugeln ein höheres Elastizitätsmodul als entsprechende Stahlkugeln, was zu einer kleineren Kontaktellipse (der Umriss der Kontaktfläche zwischen Kugel und Laufbahn, verursacht durch die elastische Verformung der Kugeln und Laufringe) führt. Je kleiner die Kontaktfläche, um so größer ist die Kontaktspannung zwischen Kugel und Laufbahn bei derselben Belastung. Wenn die externe Belastung nicht zu übermäßig starker Spannung zwischen Kugel und Laufbahn führt, erzeugt das Lager aufgrund der kleineren Kontaktfläche weniger Wärme.
Die Lagerkonfiguration, die die bestmögliche Balance der dynamischen Betriebszustände über den gesamten Arbeitszyklus einer gegebenen Anwendung ergibt, ist die optimale Lagerlösung. Timken hat umfassende Prüfungen und Analysen eigener Lagerlösungen durchgeführt, um Kunden zu helfen, möglichst gut informierte Kaufentscheidungen zu treffen. Das umfassende Angebot hat sich in einer Vielzahl von Werkzeugmaschinenanwendungen bewährt und Timken Experten stehen Herstellern von Originalteilen, Instandhaltungsbetrieben oder Endanwendern beim Auswahlprozess zur Seite.
Autor: Eric Faust
Eric Faust ist Spezialist für Anwendungstechnik bei The Timken Company. Sein Hauptarbeitsbereich ist die Unterstützung von Kunden bei der Auswahl, Konfiguration und Installation von Präzisionslagern in Werkzeugmaschinen. Er ist seit 20 Jahren für Timken tätig, hat zahlreiche Positionen in den Bereichen Maschinenbau und Programmverwaltung inne und ist Verfasser mehrerer Fachartikel zum Thema Lagerauswahl.
Teil 2 des Beitrags: https://werkstoffzeitschrift.de/maximale-produktivitaet-ist-abhaengig-von-der-lagerauswahl-und-der-lagerinstallation-teil-2/