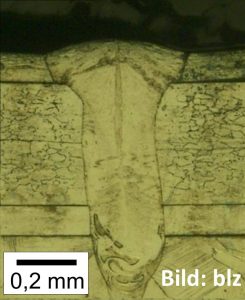
Abbildung 1: Querschliff eines laserstrahlgeschweißten Folienstapels aus korrosionsbeständigen Stählen
Autor: Vincent Mann, M.Sc., SFI
Moderne Produkte enthalten heutzutage eine Vielzahl an Kontaktstellen, durch die einzelne Komponenten miteinander verbunden sind. Neben form- und reibschlüssigen Fügeverfahren, wie beispielsweise dem Verschrauben, spielen stoffschlüssige Verbindungen eine wichtige Rolle. Insbesondere im Kontext des Leichtbaus oder steigender Anforderungen an die Baugruppen kann durch den Einsatz stoffschlüssiger Fügeverfahren das Gewicht durch den Wegfall von Verbindungselementen wie Schrauben oder Nieten reduziert oder zumindest konstant gehalten werden. Dabei stellt das Schweißen neben dem Hart- und Weichlöten die bedeutendste Fügetechnologie dar. Diese untergliedert sich wiederum in eine Vielzahl verschiedener Verfahren, deren Eignung für den jeweiligen Anwendungsfall geprüft werden muss. Aktuell kommen im Stahl- und Kranbau hauptsächlich konventionelle Verfahren, wie das MSG-, WIG- und E-Hand-Schweißen zum Einsatz, da die Stückzahlen gering sind und der Schweißprozess meist durch Fachpersonal manuell durchgeführt werden muss. Für den Fall hoher geforderter Stückzahlen und schneller Vorschubgeschwindigkeiten zum Beispiel in der Automobil- und Zulieferindustrie hat sich jedoch seit einigen Jahrzehnten das Laserstrahlschweißen am Markt etabliert. So wurden bereits in den 1980er und 1990er Jahren Fahrzeugkarosserien und Türmodule mit Hilfe von CO2-Lasern im Multikilowattbereich geschweißt. Diese kamen darüber hinaus auch in der Getriebefertigung zum Schweißen von Welle-Nabe-Verbindungen zum Einsatz. Eine weitere Anwendung war die Herstellung sogenannter Tailored Banks, die aus laserstrahlgeschweißten Zuschnitten unterschiedlicher Blechdicke oder verschiedener Werkstoffe hergestellt werden. Dabei erfolgt die Auswahl der Werkstoffe beziehungsweise Blechdicken in Abhängigkeit der lokalen Belastung der Schweißbaugruppe. Durch den sehr geringen Energieeintrag beim Laserstrahlschweißen bleiben dabei die Umformeigenschaften der Platinen weitestgehend erhalten, sodass eine Formgebung erst nach dem Schweißprozess stattfinden kann.
Seit diesen Jahrzehnten haben sich das Spektrum der Anwendungen des Lasers zum Fügen von metallischen Bauteilen, wie auch die verfügbaren Strahlquellen und Bearbeitungsoptiken jedoch deutlich erweitert. So können, wie in Abbildung 1 dargestellt, mittlerweile Folien mit einer Dicke von weniger als 100 µm genauso prozesssicher verschweißt werden, wie Bleche mit einer Dicke von mehr als 20 mm. Durch die Entwicklung und Umsetzung einer geeigneten Schweißstrategie und Strahlquellen mit einem Fokusdurchmesser des Laserstrahls von weniger als 50 µm konnten am Bayerischen Laserzentrum sehr schlanke, tiefe Schweißnähte beim Schweißen von Folienstapeln auch im Dauerstrichbetrieb der Strahlquelle erzeugt werden. Hierbei wird der sogenannte Tiefschweißeffekt ausgenutzt. Dieser tritt beim Überschreiten einer werkstoffabhängigen Leistungsdichte auf und beschreibt die Entstehung einer Dampfkapillare, innerhalb derer die Metallschmelze durch den verdampfenden Werkstoff verdrängt wird, wodurch die Einschweißtiefe bei konstanter Schweißnahtbreite deutlich erhöht werden kann. Im Fall der Folienstapel konnte dabei durch die Verwendung sehr geringer Streckenenergien und der Anwendung einer eigens entwickelten Einspann- und Hefttechnologie der thermisch bedingte Verzug sowie die Aufwölbung der Folien deutlich verringert werden. Zum Einsatz kommen die Folien in sogenannten Mikropumpen, mit deren Hilfe Zellreaktoren aus der Medizintechnik mit der notwendigen Nährlösung versorgt werden.
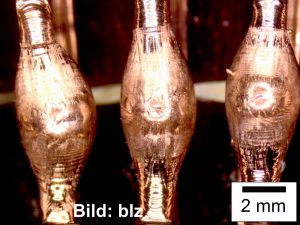
Abbildung 2: Aufsicht auf laserstrahlgeschweißte Schweißnähte an Kupfermassivdrahtstäben
Quelle: BLZ
Neben dem Mikroschweißen im Dauerstrichbetrieb kommt in der Elektronikproduktion und Feinwerktechnik auch das Laserstrahlpunktschweißen mit gepulsten Strahlquellen zur Anwendung. Diese verhältnismäßig kostengünstigen Strahlquellen stellen hohe Pulsspitzenleistungen für eine geringe Pulsdauer von einigen Millisekunden bereit, wodurch sich die benötigte mittlere Leistung gering halten lässt. Eine Aneinanderreihung mehrerer Laserpulse ermöglicht jedoch auch mit diesen Systemen mediendichte Schweißnähte zu erreichen. Daneben verbessert die hohe Intensität der Laserpulse die Einkoppelbedingungen für die durch den Laserstrahl bereitgestellte Energie, beispielsweise für Werkstoffe mit einer niedrigen Absorption für die industriell oftmals verwendeten infraroten Wellenlängen. Ein zutreffendes Beispiel für ein solches Material ist Kupfer, wie es in der Elektronikproduktion und Anwendungen aus der Elektromobilität verwendet wird. Dieser Werkstoff zeichnet sich neben einer hohen elektrischen Leitfähigkeit durch eine hohe Wärmeleitfähigkeit aus, weshalb Schweißprozesse mit einer hohen Energiedichte, wie beispielsweise Strahlprozesse, konventionellen Prozessen mit einer niedrigen Energiedichte überlegen sind, da die Bauteile schnell und nur lokal erwärmt werden können und so die nicht zum Aufschmelzen des Werkstoffes genutzte Wärme- oder Verlustenergie reduziert werden kann.
Insbesondere für elektrische Antriebs- und Speichertechnologien innerhalb von Fahrzeugen werden jedoch oftmals große stromtragfähige Querschnitte gefordert, die durch das gepulste Laserstrahlschweißen meist nicht oder nicht in der vorgegebenen Taktzeit erzielt werden können. Für diese Schweißaufgaben stehen heutzutage Multikilowatt-Laserstrahlquellen mit hervorragender Strahlqualität zur Verfügung, die durch ihre verfügbare Laserleistung und die kleinen erreichbaren Fokusdurchmesser sehr gut geeignet sind, auch in Schweißbaugruppen aus Kupfer Schweißnähte mit einem hohen Anbindungsquerschnitt in Taktzeiten von typischerweise unter 1 Sekunde erzielen zu können. Die Strahlablenkung wird dabei zumeist über sogenannte Scanner-Optiken, bei welchen zwei, durch sogenannte Galvanometerantriebe bewegte, Spiegelelemente realisiert, die für die Ablenkung des Laserstrahls innerhalb des Bearbeitungsfeldes zuständig sind. Dabei erreicht der Strahl innerhalb der Bearbeitungsebene Relativgeschwindigkeiten von bis zu 20 m/s, wodurch eine sehr schnelle Neupositionierung des Laserstrahls vom Ende der durchgeführten Schweißnaht zum Beginn der darauffolgenden Schweißnaht möglich wird. Die beschriebene Systemtechnik wurde am Bayerischen Laserzentrum beispielsweise im Rahmen eines öffentlich geförderten Forschungsprojektes eingesetzt, innerhalb dessen die Schweißprozesse und -strategien für die elektrische Kontaktierung der in Abbildung 2 dargestellten Statorwicklungen eines 48 V-Mildhybrid-Motors in Zusammenarbeit mit den Continental-Standorten Nürnberg, Regensburg und Berlin entwickelt wurden. Die entsprechenden 48 V-Hybrid-Motoren werden aktuell in den Modellen Scénic und Grand Scénic des Automobilherstellers Renault verbaut.
Neben der Reduzierung der Taktzeit bieten die hochdynamischen Strahlablenkungssysteme weitere Vorteile. So erlaubt die hohe Positioniergeschwindigkeit einen nahezu quasisimultanen Schweißprozess, mit dem sich Bauteile beispielsweise heften lassen, bevor ein prozessbedingter Verzug auftreten kann. Auf diese Weise lässt sich die Genauigkeit geschweißter Baugruppen und damit einhergehend die anfallende Nacharbeit nach dem Schweißprozess auf ein Minimum reduzieren. Ein weiterer Vorteil der hochdynamischen Strahlablenkung ist die Möglichkeit der sogenannten Strahloszillation beim Schweißen.
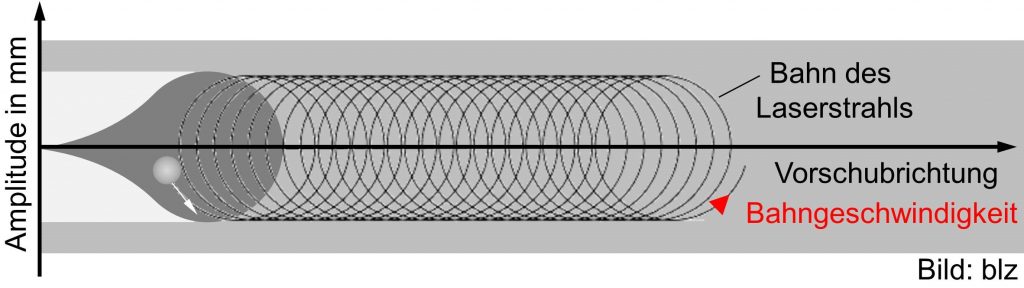
Abbildung 3: Schematische Darstellung der Bahnkontur beim Laserstrahlschweißen mit Strahloszillation
Quelle: BLZ
Bei dieser Prozessvariante wird der linearen Vorschubbewegung eine zweite Bewegungskomponente überlagert, sodass wie in Abbildung 3 für eine Kreisfigur dargestellt, ein meist regelmäßiges Oszillationsmuster entlang der Schweißnahtkontur entsteht. Anstelle der Kreisfigur kommen oftmals weitere harmonische Figuren, beispielsweise sinus- oder achtförmige Muster, sogenannte Leminskaten, aber auch nicht harmonische, aber dennoch periodische Zickzack-Figuren zum Einsatz. Mit dieser Technologie lassen sich durch eine gezielte Wahl der Oszillationsparameter wesentliche Schweißnahteigenschaften, wie beispielsweise die Schweißnahtform, die Einschweißtiefe oder die Schweißnahtbreite beeinflussen, wodurch sich beispielsweise der Anbindungsquerschnitt oder die überbrückbare Fügespaltbreite im Stumpf- und Überlappstoß steigern lässt. Darüber hinaus wird am Bayerischen Laserzentrum aktuell untersucht, inwiefern sich Schweißnahtdefekte durch Anwendung von Strahloszillation beim Laserstrahlschweißen vermeiden lassen. Dabei ergeben sich durch Strahloszillation Möglichkeiten, um beispielsweise die Energiedeposition ins Werkstück und auch die Schmelzbaddynamik zielgerichtet zu beeinflussen und somit die Schweißbarkeit von bedingt schweißbaren Legierungen allein durch prozesstechnische Maßnahmen ohne die Verwendung von Zusatzwerkstoffen zu verbessern.
Allgemein lässt sich durch den geringen Wärmeeintrag auch beim konventionellen Laserstrahlschweißen die Schweißbarkeit vieler bedingt schweißbarer Werkstoffe verbessern, sodass auch diese Werkstoffe stoffschlüssig gefügt werden können. In diesem Zusammenhang stellen auch Mischverbindungen ein langjähriges Kompetenzfeld des Bayerischen Laserzentrums dar. So zeigen beispielsweise Erkenntnisse eines kürzlich abgeschlossenen, öffentlich geförderten Forschungsprojektes, dass Mischverbindungen aus austenitischen und ferritischen korrosionsbeständigen Stählen trotz der unterschiedlichen Wärmeleitfähigkeit und Wärmeausdehnungskoeffizienten miteinander verschweißt werden können. Dabei trägt unter anderem die Verwendung titanstabilisierter Zusatzwerkstoffe durch die enthaltenen Kornfeiner zur Erhöhung der Korrosionsbeständigkeit der Schweißzone bei. Gleichzeitig können durch diese Maßnahme die Umformeigenschaften der geschweißten Platinen verbessert werden. Demgegenüber kann die Korrosionsbeständigkeit der Mischverbindungen in der Wärmeeinflusszone, wie in Abbildung 4 gezeigt, durch die Verwendung wasserstoffhaltiger, reduzierender Schutzgase erhöht werden. Darüber hinaus können durch den Einsatz des Laserstrahlschweißens auch Schwarz-Weiß-Mischverbindungen aus niedrigen legierten Stählen und korrosionsbeständigen Stählen sowie Stahl- und Kupferlegierungen realisiert werden. Dabei ermöglicht die hohe Leistungsdichte der Laserstrahlung trotz der zum Teil stark unterschiedlichen Wärmeleitfähigkeiten ein gleichzeitiges Aufschmelzen beider Fügepartner, noch bevor die Prozesswärme ausschließlich in einen Fügepartner abgeführt wird.
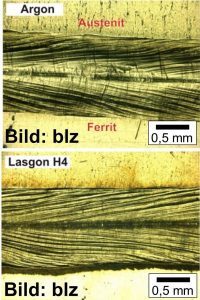
Abbildung 4: Vergleich der Aufsichten von Mischverbindungen aus korrosionsbeständigen Stählen, geschweißt mit verschiedenen Schutzgasen. Oben Argon, Unten: Lasgon H4 (10% Wasserstoff)
Quelle: BLZ
Ein Beispiel für Mischverbindungen, die nur mithilfe eines Hybridverfahrens stoffschlüssig gefügt werden können, stellen Stahl-Aluminium-Mischverbindungen dar. Diese können lediglich durch den Prozess des sogenannten Schweißlötens miteinander verbunden werden, da im Prozess lediglich einer der Grundwerkstoffe durch den Laserstrahl aufgeschmolzen wird und den zweiten Fügepartner dabei lediglich benetzt. Dabei kann beispielsweise im Karosseriebau durch die Verwendung verzinkter Bleche auf weitere Flussmittel verzichtet werden, da die Zinkschicht im Prozess anschmilzt und somit als Flussmittel an der Stahl-Aluminium-Schnittstelle dienen kann.
Als Alternative zu diesem Hybridprozess lassen sich durch das Strahlwerkzeug Laser selbstverständlich auch reine Hartlötprozesse realisieren. So wird beispielsweise aktuell die Heckklappe vieler Fahrzeugkarossen zweiteilig ausgeführt und nach dem Umformen durch das Laserstrahlhartlöten verbunden, wobei auch hier im Fall von Stahlfeinblechen oftmals die Zinkschicht als Flussmittel wirken kann. Die Technologie des Laserstrahlhartlötens zeichnet sich gegenüber dem Laserstrahlschweißen durch eine bessere Oberflächenqualität der Lötnaht gegenüber der Schweißnaht aus und erfordert aus diesem Grund eine geringere Nacharbeit vor der kathodischen Tauchlackierung. Darüber hinaus wird durch den geringeren Energieeintrag im Prozess auch der thermische Verzug der Blechbauteile reduziert. Als sinnvolle systemtechnische Verbesserung des Laserstrahlhartlötens hat sich dabei ein in einer Kooperation aus ERLAS – Erlanger Lasertechnik GmbH und dem Bayerischen Laserzentrum entwickeltes Zwei-Strahl-Systems mit koaxialer Drahtzufuhr erwiesen. Dieses System ermöglicht eine Vorwärmung der Fügepartner vor dem Auftreffen des Lotwerkstoffes im Fügespalt und eine Nachwärmung der Lötnaht, um einerseits, wie in Abbildung 5 dargestellt, den Anbindungsquerschnitt und damit die Belastbarkeit der Verbindung zu erhöhen und andererseits die Oberflächenrauigkeit der Lötnaht zu verringern und damit die optische Anmutung der Fügeverbindung zu verbessern.
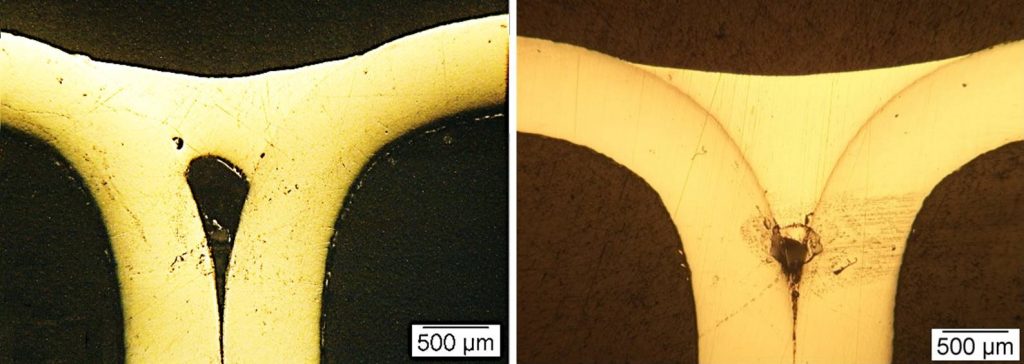
Abbildung 5: Vergleich der Querschliffe von mit verschiedenen Lötoptiken gelöteten Lötnähten. Links: Einstrahlsystem. Rechts: Vergrößerter Nahtquerschnitt durch Verwendung des Zweistrahlsystems Erlas Coax-Mini
Quelle: BLZ
Durch die aufgezeigten Prozessvarianten besteht die Möglichkeit, eine gegenüber konventionellen Schweißverfahren deutlich erhöhte Anzahl an Werkstoffkombinationen und eine große Vielfalt an Bauteilgeometrien stoffschlüssig mithilfe von Laserstrahlung fügen zu können. Darüber hinaus kann der Einsatz des Lasers durch die Flexibilität und die weitreichenden Einsatzmöglichkeiten moderner Strahlquellen, wie beispielsweise der Versorgung mehrerer Bearbeitungsstationen durch eine Strahlquelle oder der gleichzeitigen Eignung zum Laserstrahlschweißen und -schneiden, auch für kleine und mittlere Unternehmen attraktiv werden.
Kontakt und weitere Informationen:
Bayerisches Laserzentrum GmbH,
Konrad-Zuse-Straße 2-6,
91052 Erlangen
Telefon: 09131/97790-0,
E-Mail: info@blz.org,
URL: www.blz.org