Innerhalb des Fachartikels werden aktuelle Untersuchungen zum Flach-Clinch-Kleben vorgestellt. Dieses Umformfügeverfahren ist besonders für Leichtbaukonstruktionen in Mischbauweise geeignet, da es die Möglichkeit bietet, eine Vielzahl verschiedener Materialien zu fügen. Basierend auf dem Stand der Technik werden experimentelle und numerische Untersuchungen zum konventionellen Flach-Clinchen von Metall-Metall-Verbindungen sowie das neuentwickelte Verfahren Flach-Clinch-Kleben präsentiert.
Ausgangssituation
Das Ziel moderner Fertigungs- und Produktkonzepte ist die Einsparung von Rohstoffen, Kosten und Energie sowohl bereits bei der Herstellung als auch bei der späteren Nutzung von Produkten. Durch den Einsatz aktueller Leichtbaustrategien werden besonders im Automobilbereich zunehmend verschiedene, an die jeweiligen Gewichts- und Festigkeitsanforderungen angepasster Werkstoffe verwendet [1]. Ein Problem dieses sogenannten Material-Leichtbaus ist das zuverlässige Fügen der verschiedenen Materialien. So können konventionelle Technologien, wie z. B. das Schweißen, nicht für die Verbindung von Metallen und Kunststoff verwendet werden. Weiterhin erfordern thermische Fügeverfahren eine teilweise aufwendige Vor- und Nachbereitung der Schweißnaht und können zum Auftreten von unerwünschten Effekten, wie z. B. thermischer Verzug oder Gefügeveränderungen, führen. Vor diesem Hintergrund gewinnen mechanische Fügeverfahren zunehmend an Bedeutung.
Ein häufig in der Automobilindustrie eingesetztes mechanisches Fügeverfahren ist das Clinchen. Hierbei werden zwei oder mehr Bleche lokal umgeformt und somit eine form- und kraftschlüssige Verbindung hergestellt. Trotz der zahlreichen Vorteile, wie z. B. Materialvielfalt, kurze Taktzeiten und geringer Aufwand für die Fügestellenvorbereitung, besteht der entscheidende Nachteil von Clinch-Verbindungen in der prozessbedingten matrizenseitigen Überhöhung der Fügestelle. Aufgrund dieser Überhöhung können konventionelle Clinch-Verbindungen nicht in Sichtbereichen (z. B. Außenhaut von Fahrzeugen) oder Funktionsbereichen (z. B. Dicht- oder Gleitflächen) eingesetzt werden [2].
Neben den mechanischen Fügeverfahren werden im Automobilbau auch zunehmend Klebverbindungen eingesetzt. Im Vergleich zu den mechanischen punktförmigen Fügeverfahren weist das Kleben hierbei eine höhere Belastbarkeit gegenüber schwingender und schlagartiger Beanspruchung sowie eine höhere Verbindungsfestigkeit unter quasistatischer Scherzugbeanspruchung auf [3]. Nachteilig am Kleben ist jedoch die geringe Handhabungsfestigkeit des unausgehärteten Klebstoffs. Dies führt bei der Herstellung der Produkte zu verlängerten Taktzeiten, da die Bauteile bis zum vollständigen Aushärten der Klebschicht in ihrer Lage zueinander fixiert werden müssen.
Um die Vorteile des mechanischen Fügens und Klebens miteinander zu verbinden, werden sogenannte Hybridfügeverfahren eingesetzt. Industrielle Anwendungen verwenden hierfür überwiegend die Fixiermethode, bei der in einem ersten Schritt Klebstoff auf ein oder beide Fügepartner aufgetragen wird. Anschließend werden die Teile zueinander positioniert und mechanisch gefügt. Aufgrund der mechanischen Verbindung müssen die Bauteile nicht zusätzlich in ihrer Lage fixiert werden, sondern können direkt weiterverarbeitet werden. Die Aushärtung des Klebstoffs kann daher in einem späteren Prozessschritt erfolgen. Weiterhin führt die Kombination der klebtechnischen und mechanischen Fügeverfahren zur Nutzung von Synergieeffekten hinsichtlich der Fertigung und Eigenschaften der entstehenden Verbindungen, wodurch sich neue Verbindungsmöglichkeiten ergeben [3].
Flach-Clinchen
Das an der TU Chemnitz entwickelte und patentierte Flach-Clinchen bietet die Möglichkeit, artgleiche sowie artfremde Werkstoffe in einem einstufigen Prozess unmittelbar ohne zusätzliche Vorarbeiten und Hilfselemente mechanisch miteinander zu verbinden. Im Gegensatz zum konventionellen Clinchen wird anstelle der formgebenden Matrize ein planer Amboss als Gegenwerkzeug verwendet und somit können einseitig ebene Clinch-Verbindungen hergestellt werden (siehe Abbildung 1).
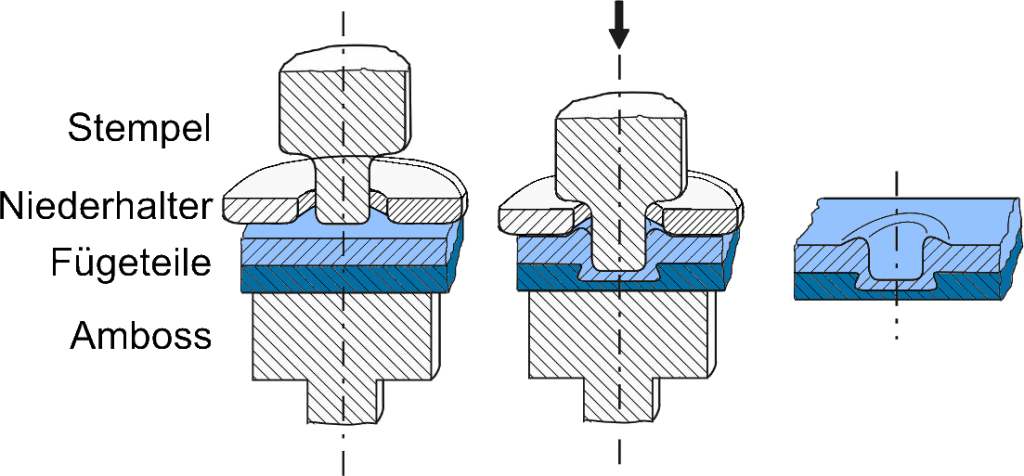
Abbildung 1: Verfahrensablauf des Flach-Clinchens
Abbildung 2 stellt schematisch die Verbindungsquerschnitte sowie die geometrischen Kenngrößen (Hinterschnitt f, Halsdicke tn, Restbodendicke tb und Überhöhung p) einer konventionellen Clinch-Verbindung und einer Flach-Clinch-Verbindung gegenüber. Während des Flach-Clinchens wird der Werkstofffluss gezielt gesteuert, sodass es innerhalb der Materialebene zur Ausbildung eines für Clinch-Verbindungen charakteristischen Hinterschnittes zwischen den Fügepartnern und dem daraus resultierenden Form- und Kraftschluss kommt. Der entscheidende Vorteil der Flach-Clinch-Verbindungen ist die ambossseitige Ebenheit, die es ermöglicht, dieses Fügeverfahren auch im Bereich von Sicht- und Funktionsflächen einzusetzen.

Abbildung 2: Schematische Darstellung der Verbindungsquerschnitte:
a) konventionelle Clinch-Verbindung, b) Flach-Clinch-Verbindung
Die numerische Analyse des Werkstoffflusses zeigt, dass innerhalb der Fügezone überwiegend Druckspannungen vorherrschen. Aufgrund dieses Spannungszustandes können mittels Flach-Clinchen nicht nur Metall-Metall-Verbindungen hergestellt werden, sondern auch zahlreiche Materialien gefügt werden, die infolge ihrer Zugspannungsempfindlichkeit nicht mittels konventionellen Clinchens fügbar sind [2, 4, 5] (siehe Abbildung 3).
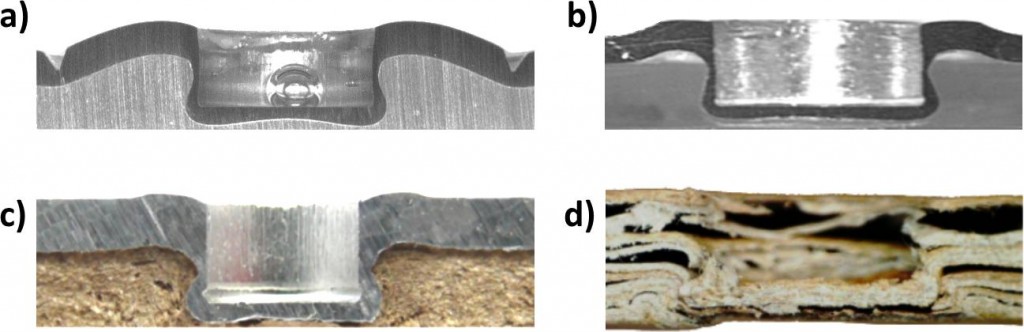
Abbildung 3: Multimaterialdesign: a) Stahl-Aluminium, b) Aluminium-Polystyrol, c) Aluminium-MDF (mitteldichte Faserplatte), d) Kartonage-Kartonage
Flach-Clinch-Kleben
Zielsetzung
Ziel des Flach-Clinch-Klebens ist die Optimierung der Verbindungseigenschaften durch die Ausnutzung der Vorteile der elementaren Fügeverfahren Flach-Clinchen und Kleben. Aufgrund der großflächigen Klebstoff-Zwischenschicht erfolgt eine gleichmäßigere Spannungsverteilung im Fügebereich und es werden somit die Schwingfestigkeit und Verbindungssteifigkeit deutlich erhöht [3]. Weiterhin wird der Fügespalt gegenüber Gasen und Flüssigkeiten abgedichtet. Zusätzlich kann die beim Fügen von Metallen mit hoher Potentialdifferenz auftretende Kontaktkorrosion durch die elektrochemische Isolation der Fügepartner (Klebstoff-Zwischenschicht) vermieden werden. Die Taktzeiten des konventionellen Klebprozesses können verkürzt werden, da die mechanische Verbindung die Bleche in ihrer Lage zueinander fixiert, sodass eine zusätzliche Fixierung der Bauteile bis zur vollständigen Klebstoffaushärtung entfallen kann. Weiterhin entlastet der mechanische Fügepunkt die Klebverbindung gegenüber Schälbeanspruchung [3].
Stahl-Aluminium-Verbindung
Für die Untersuchung des Flach-Clinch-Klebens von DC04 (stempelseitig, Blechdicke 1,0 mm) und EN AW 1050A (ambossseitig, Blechdicke 1,5 mm) wurde als Klebstoff-Zwischenschicht der thermisch aushärtende Strukturklebstoff Betamate 1620 der Firma Dow Automotive Systems verwendet. Nach der Herstellung der Flach-Clinch-Klebverbindungen wurden die Proben einer Wärmebehandlung (T = 180 °C, t = 30 min) unterzogen, um den Einkomponenten-Epoxidharzkleber auszuhärten.
In ersten experimentellen Versuchen wurde der Klebstoff als 3 mm Raupe appliziert. Während des Fügeprozesses setzt der Niederhalter zeitlich vor dem Stempel auf, dabei wird ein Teil des Klebstoffs zwischen den Blechen eingeschlossen. Während der anschließenden Umformung kann das eingeschlossene Klebstoffvolumen nicht weiter aus der direkten Fügezone verdrängt werden, sodass es zur Entstehung von Klebstofftaschen kommt. Diese Taschen behindern die Hinterschnittausbildung und führen letztendlich zu einem Halsabriss und damit zum Versagen der Flach-Clinch-Verbindung (siehe Abbildung 4, links). Anhand der experimentellen Vorversuche wurde das Flach-Clinch-Kleben mithilfe der FEM-Software Simufact.forming numerisch abgebildet und kalibriert. (Abbildung 4, rechts). Die Abweichung zwischen Simulation und Experiment betrug hierbei sowohl für die Prozesskräfte als auch die geometrischen Kenngrößen Hinterschnitt, Halsdicke und Restbodendicke weniger als 10 %.
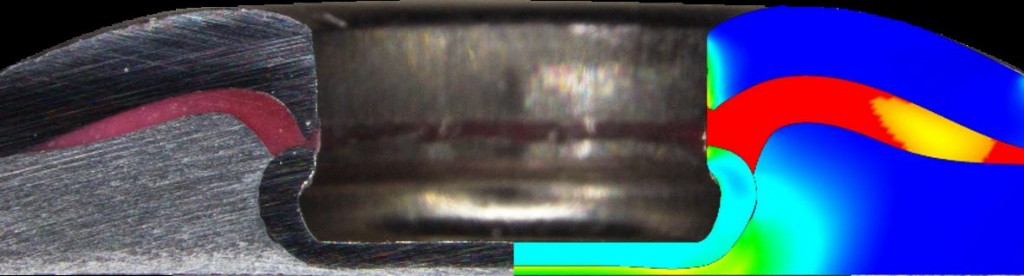
Abbildung 4: Halsabriss bei Applikation einer 3 mm Klebstoff-Raupe: Gegenüberstellung Experiment und Simulation (Oberblech DC04, t = 1,0 mm; Unterblech EN AW 1050A, t = 1,5 mm; ; Stempeldurchmesser 5 mm; Restbodendicke 0,35 mm)
Aufbauend auf den Vorversuchen konnten die Einflussparameter auf das Fügeergebnis untersucht werden. Durch eine gezielte Anpassung der Fügeparameter (Stempelgeschwindigkeit, Werkzeug-Haltezeit und Niederhalterkraft) war es möglich, die Verteilung des Klebstoffs in der Fügezone und somit die Ausbildung des Hinterschnittes positiv zu beeinflussen. Im Hinblick auf die minimale Ausbildung der Klebstofftaschen hat sich der homogene Klebstoffauftrag mit einer Schichtdicke von 75 µm als vorteilhaft erwiesen. Die dünne Klebstoffschicht wird während der Umformung aus der direkten Fügezone verdrängt. Es kommt zur Ausbildung minimaler Klebstofftaschen, die jedoch lediglich einen geringen Einfluss auf die Verbindungskennwerte Halsdicke und Hinterschnitt besitzen. Der kombinierte Einsatz von experimentellen und numerischen Untersuchungen ermöglichte es somit, hochwertige Flach-Clinch-Klebverbindungen herzustellen (Abbildung 5).
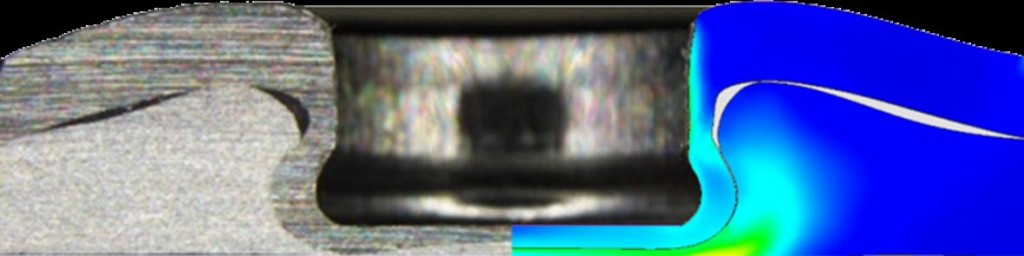
Abbildung 5: Flach-Clinch-Klebverbindung: Gegenüberstellung Experiment und Simulation (Oberblech DC04, t = 1,0 mm; Unterblech EN AW 1050A t = 1,5 mm; Klebstoffschichtdicke 75 µm; Stempeldurchmesser 5 mm; Restbodendicke 0,35 mm)
Um die Verbindungseigenschaften der hybriden Flach-Clinch-Klebverbindungen im Vergleich zu konventionellen Flach-Clinch-Verbindungen zu beurteilen, wurden Scher- und Kopfzugversuche nach DIN EN ISO 12996 bzw. DIN ISO 16237 durchgeführt. Tabelle 1 gibt einen Überblick über die hierbei erzielten Verbindungsfestigkeiten. Die in Klammern angegebenen prozentualen Veränderungen beziehen sich jeweils auf die elementare Flach-Clinch-Verbindung ohne Klebstoff-Zwischenschicht.
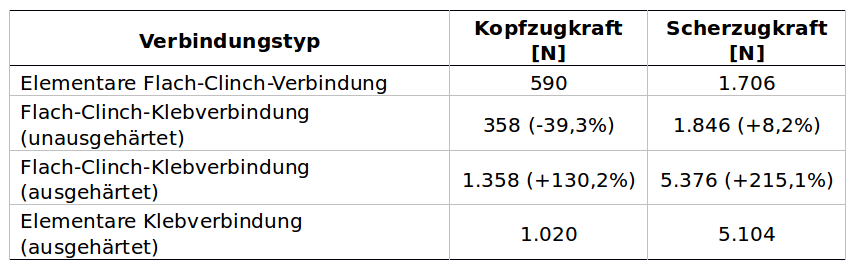
Tabelle 1: Mechanische Eigenschaften von konventionellen und hybriden Flach-Clinch-Verbindungen
Die Auswertung der Tabelle 1 zeigt, dass der unausgehärtete Klebstoff die Verbindungsfestigkeit der Flach-Clinch-Verbindung beeinflusst. Im Falle einer Kopfzugbelastung wirkt der Klebstoff wie eine Art Schmiermittel und es kommt zum Ausknöpfen der Verbindung. Die Scherzugkraft wird hingegen aufgrund der geringeren Abstreckung im Halsbereich der Verbindung geringfügig erhöht. Nach dem vollständigen Aushärten des Klebstoffs ist die Beanspruchbarkeit der Flach-Clinch-Verbindung sowohl gegen Kopfzug- als auch gegen Scherzugbelastung deutlich erhöht. Der Vergleich der Verbindungsfestigkeit der elementaren Klebverbindung und der vollständig ausgehärteten Flach-Clinch-Klebverbindung zeigt, dass die finale Festigkeit (Gebrauchsfestigkeit) überwiegend aus der Klebverbindung resultiert. Dennoch trägt die zusätzliche mechanische Verbindung zu einer Steigerung der Kopfzugkraft um 33,1 % und der Scherzugkraft um 5,3 % bei.
Erweiterung des Anwendungsgebietes
Aktuelle Untersuchungen beschäftigen sich mit der Erweiterung des Anwendungsgebietes des Flach-Clinch-Klebens. So soll bspw. durch die Verwendung unterschiedlicher metallischer Werkstoffe der Festigkeitseinfluss der Grundwerkstoffe auf die Klebstoffverdrängung und die damit verbundene Ausbildung der Klebstofftaschen während des Fügens ermittelt werden. Weiterhin werden Klebstoffe mit unterschiedlichem Fließverhalten (Viskositäts-Scherraten-Kennlinien) untersucht. Hierfür werden u.a. Zweikomponenten-Klebstoffe verwendet, wie sie typischerweise für Reparaturanwendungen im Automobilbau eingesetzt werden.
Tabelle 2 zeigt die erzielbaren Festigkeitssteigerungen für die Kombination von zwei Blechen aus EN AW 1050A mit einer Ausgangsdicke von 1,0 mm (stempelseitig) bzw. 1,5 mm (ambossseitig) und dem 2K-Klebstoff Teroson EP 5055 (Henkel AG & Co. KGaA) als Klebstoff-Zwischenschicht. Die in Klammern angegebenen prozentualen Veränderungen beziehen sich jeweils auf die elementare Flach-Clinch-Verbindung.
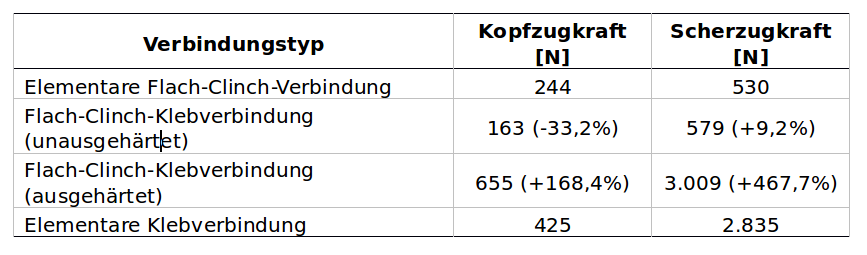
Tabelle 2: Mechanische Eigenschaften von konventionellen und hybriden Flach-Clinch-Verbindungen
Die Auswertung der Tabelle 2 zeigt ein ähnliches Verhalten wie für den Klebstoff Betamate 1620. Im Vergleich zur konventionellen Flach-Clinch-Verbindung führt der unausgehärtete Klebstoff zu einer Verringerung der Kopfzugkraft, während die Scherzugkraft geringfügig erhöht wird. Nach der vollständigen Aushärtung des Klebstoffs ist die Beanspruchbarkeit der Flach-Clinch-Verbindung sowohl gegen Kopfzug- als auch gegen Scherzugbelastung signifikant erhöht. Ebenso resultiert die Gebrauchsfestigkeit der vollständig ausgehärteten Flach-Clinch-Klebverbindung überwiegend aus der Klebverbindung. Gegenüber der elementaren Klebverbindung führt die zusätzliche mechanische Verbindung zu einer Steigerung der Kopfzugkraft um 54,1 % und der Scherzugkraft um 6,1 % bei.
Zusammenfassung
Mithilfe des Flach-Clinchens können sowohl artgleiche als auch artfremde Werkstoffe in einem einstufigen Prozess unmittelbar ohne zusätzliche Vorarbeiten und Hilfselemente gefügt werden. Im Gegensatz zum konventionellen Clinchen ist die Flach-Clinch-Verbindung einseitig komplett eben, sodass dieses Fügeverfahren auch im Bereich von Sicht- und Funktionsflächen eingesetzt werden kann. Weiterhin können aufgrund des vorherrschenden Druckspannungszustandes nicht nur Metall-Metall-Verbindungen hergestellt werden, sondern auch zahlreiche Materialien gefügt werden, die infolge ihrer Zugspannungsempfindlichkeit nicht mittels konventionellen Clinchens fügbar sind.
Durch den kombinierten Einsatz mit Klebstoff können die Verbindungseigenschaften von Flach-Clinch-Verbindungen weiter verbessert werden. So weisen diese Hybridfügeverbindungen eine höhere Belastbarkeit gegenüber schwingender und schlagartiger Beanspruchung sowie eine höhere Verbindungsfestigkeit unter quasistatischer Kopf- und Scherzugbeanspruchung auf. Nach dem Fügen wird die Handhabungsfestigkeit bis zum Aushärten des Klebstoffs durch die mechanische Verbindung der Bleche erzielt. Somit kann die Taktzeit verkürzt werden und die Bauteile direkt weiterverarbeitet werden. Die endgültige Gebrauchsfestigkeit der Verbindung wird nach dem vollständigen Aushärten des Klebstoffs erreicht.
Um eine größtmögliche Flexibilität im Fertigungsprozess zu gewährleisten, wurde bei der Verfahrensentwicklung darauf geachtet, dass sowohl Flach-Clinch-Verbindungen mit als auch ohne Klebstoff-Zwischenschicht mit demselben Werkzeugsatz herstellbar sind.
Danksagung
Das Forschungsvorhaben wurde mit Mitteln der Deutschen Forschungsgemeinschaft (DFG) finanziert. Für diese Förderung danken die Autoren.
Autoren
Dipl.-Ing. Thoralf Gerstmann¹, M.Sc. Stephan Lüder¹, Prof. Dr.-Ing. habil. Birgit Awiszus¹,
Dr.-Ing. habil. Frank Riedel²
1 Technische Universität Chemnitz, Professur Virtuelle Fertigungstechnik
2 Fraunhofer-Institut für Werkzeugmaschinen und Umformtechnik (IWU) Chemnitz
Fachartikel zum Thema neue Verfahrenstechnologie aus Werkstoffe in der Fertigung 5/2015
Literatur
[1] Kienzle, S.: Leichtbau bei Mercedes-Benz. Leichtbau-Gipfel 2015. Würzburg, 2015.
[2] Gerstmann, T.; Awiszus, B.: Recent developments in flat-clinching. In: Computational Materials Science 81 (2014), S. 39–44.
[3] Merkblatt DVS/EFB 3450‑1: Hybridfügen – Clinchkleben – Stanznietkleben – Überblick. Düsseldorf: Verlag für Schweißen und verwandte Verfahren DVS-Verlag GmbH, 2007.
[4] Beyer, U.: Multi-Material-Fügen mittels Flach-Clinch-Technologie. Dissertation. Technische Universität Chemnitz, 2012.
[5] Lüder, S.; Gerstmann, T.; Awiszus, B.: Innovative Fügetrends: Flach-Clinchen. In: wt Werkstatttechnik online 10/104 (2014), S. 625–630.