Eine Möglichkeit zur Kostenreduzierung von keramischen Faserverbundwerkstoffen (CMC) bietet die Verwendung kostengünstiger Basalt- oder Glasfasern anstelle von Keramikfasern – in Kombination mit bei niedrigen Prozesstemperaturen ausgehärteten oder gesinterten Matrices. Anders als herkömmliche CMC, die üblicherweise bei Temperaturen über 1000 °C eingesetzt werden können, sind diese Low-Cost-CMC für den Einsatz bei mittleren Temperaturen zwischen 300 °C und 800 °C ausgelegt. Der vorliegende Artikel gibt einen Überblick über das Thema und beleuchtet einige damit verbundene Aktivitäten des Fraunhofer-Zentrums für Hochtemperatur-Leichtbau HTL.
Einleitung
CMC besitzen eine hohe mechanische Festigkeit, Bruchzähigkeit, chemische Beständigkeit und eine geringe Dichte, sodass sie sich ideal als Leichtbauwerkstoff in rauer Umgebung eignen. Im Vergleich zu monolithischen Keramiken liegt der Hauptvorteil von CMC in der hohen Dehnung bei mechanischer Beanspruchung, was zu einem schadenstoleranten Verhalten führt. CMC werden durch Einbettung von keramischen Verstärkungsfasern in eine keramische Matrix hergestellt. Üblicherweise werden entweder nicht-oxidische Keramikfasern aus SiC oder Kohlenstofffasern in Kombination mit einer nicht-oxidischen Matrix verwendet, oder oxidische Keramikfasern werden in eine oxidkeramische Matrix eingebettet. Die entsprechenden CMC werden als nicht-oxidisch bzw. oxidisch bezeichnet. Zur Auslegung der Schadenstoleranz ist ein mechanisch schwaches Faser-Matrix-Interface (weak interface bei nicht-oxidischen CMC) oder eine schwache Matrix mit einer mechanisch stabilen Anbindung an die Fasern (weak matrix bei oxidkeramischen CMC) erforderlich. Beides führt zur Rissauslenkung bzw. zum Faserauszug und zur Energieabsorption beim Bruch. Diese Effekte ermöglichen eine Umlagerung des Gefüges, wenn äußere Spannungen auftreten. Die schwache Faser-Matrix-Grenzfläche bzw. die schwache Matrix erhält man durch eine Faserbeschichtung oder durch Erzeugung einer porösen Matrix. Oxidische CMC können dauerhaft bei Temperaturen bis ca. 1100 °C – bedingt durch Degradationsvorgänge wie Kornwachstum in der Faser – und nicht-oxidische CMC bis ca. 1400 °C eingesetzt werden. Noch höhere Einsatztemperaturen können durch Wärmedämmschichten und Kühlkonzepte erreicht werden. CMC sind beständig gegen Thermoschock und Temperaturgradienten. Ihre Eigenschaften können in Abhängigkeit vom Faservolumengehalt, der Faserausrichtung und den Grenzflächen- und Matrixeigenschaften maßgeschneidert werden. Hohe Faservolumengehalte von ca. 50 % und die Ausrichtung der Fasern in Belastungsrichtung führen zu einer hohen Zugfestigkeit. Eine Übersicht über die Eigenschaften von handelsüblichen CMC wird in [1] gegeben.
Der Nachteil von handelsüblichen CMC liegt in ihren hohen Kosten. Zum einen hängen diese mit den Preisen der keramischen Verstärkungsfasern zusammen. Die Preise für verschiedene Fasern, die als 2D-Laminate angeboten werden, sind in Tabelle 1 aufgeführt. Die gebräuchlichsten oxidkeramischen Fasern für CMC-Anwendungen stammen von 3M™ mit dem Handelsnamen Nextel™ 312, 440, 610 und 720. Der Preis ist stark abhängig von der Anzahl der Filamente im Faserbündel, dem sogenannten Titer in tex (g/1 km) oder denier (g/9 km) und kann z. B. für Gewebe aus Nextel™ 610 von > 300 €/m² bis > 900 €/m² variieren. Eine andere Art von oxidkeramischen Fasern sind ALF von Nitivy mit einem Preis von ca. 400 €/m². Kommerziell erhältliche, nicht-oxidkeramische Fasern sind typischerweise SiC-Fasern von NGS vom Typ Nicalon NL, High Nicalon oder High Nicalon Typ S – oder die Typen S, ZMI, LOX-M oder SA4 von UBE Industries. Der Preis ist abhängig vom Sauerstoffgehalt und Kristallinitätsgrad und kann von > 1.000 €/kg für Generation 1 bis > 8.000 €/kg für Generation 3 variieren. Die Basis von Low-Cost-CMC sind daher Low-Cost-Fasern, die in Tabelle 1 mit einem Nextel™-Fasergewebe verglichen werden. Diese Low-Cost-Fasern werden typischerweise für die Herstellung von kohlenstoff-, glas- oder basaltfaserverstärkten Polymeren (CFK, GFK und BFK) verwendet und sind als Rovings oder 2D-Laminate erhältlich. Der Einsatz dieser Faserverbundkunststoffe (FVK) ist jedoch aufgrund ihrer Kunststoffmatrizen auf niedrige Temperaturen bis 300 °C beschränkt. Außerdem ist die Verwendung von Kohlenstofffasern durch ihre Anfälligkeit für Oxidation eingeschränkt.
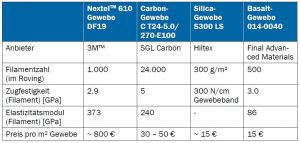
Tabelle 1: Eigenschaften von handelsüblichen keramischen Low-Cost-Geweben und deren Marktpreise.
Andererseits ist der Herstellprozess von Bauteilen aus CMC-Werkstoffen kostenintensiv, da er viele manuelle Prozessschritte beinhaltet. Zudem werden für die Faserbeschichtung und die Matrixbildung nicht-oxidischer CMC oft langsame und teure Gasphasenprozesse wie die chemische Gasphasenabscheidung (CVD) oder die chemische Gasphaseninfiltration (CVI) eingesetzt. Die Aushärtung und Verdichtung der Matrix bei oxidischen CMC wird oft durch Autoklavenprozesse als Batchprozesse bewerkstelligt, die aufgrund ihres geringen Materialdurchsatzes teuer sind. Gegenwärtig wird ein breiterer Einsatz von Hochtemperatur-CMC aus Kostengründen verhindert. Es besteht nach wie vor ein großer Bedarf an neuartigen CMC, die die Lücke zwischen FVK und herkömmlichen CMC schließen, d. h. für Temperaturen im Bereich zwischen 300 °C und 800 °C. Viele thermische Prozesse in der Metall-, Glas-, Chemie- und Energieindustrie erfordern korrosionsbeständige und schadenstolerante Werkstoffe in diesem Temperaturbereich. Handelsübliche CMC sind jedoch zu teuer für einen breiten Einsatz in diesen Branchen.
Eine drastische Reduzierung der Herstellkosten wird bereits durch die Substitution der keramischen Verstärkungsfasern durch Glas- oder Basaltfasern erreicht (Tabelle 1). Allerdings halten diese Fasern Temperaturen über 1000 °C nicht stand. Daher sind die Infiltration eines keramischen Schlickers und die anschließende Sinterung bei hohen Temperaturen, wie sie bei der üblichen Herstellung von oxidischen CMC zur Erzielung einer angemessenen Matrixfestigkeit eingesetzt wird [2], in der Regel nicht realisierbar. Als alternative Matrix stehen Geopolymere zur Verfügung. Sie sind preiswert und können bei Raumtemperatur ausgehärtet werden. Darüber hinaus können auch andere preiswerte Precursoren oder Suspensionen mit niedrigen Aushärtungs- bzw. Sintertemperaturen verwendet werden. Um eine stabile und kostengünstige Fertigung zu ermöglichen, werden Rolle-zu-Rolle-Verfahren und Spritzgießen vorgeschlagen. Der große Vorteil liegt in automatisierten und kontinuierlich arbeitenden Prozessen für wichtige Schritte wie die Faserbeschichtung, die 2D- oder 3D Textilherstellung und das Prepregging (Abbildung 1). Weiterhin sollen Out-of-Autoclave-Techniken wie Bandwickeln und axiales Pressen konsequent eingesetzt werden, um die Produktionskosten niedrig zu halten.
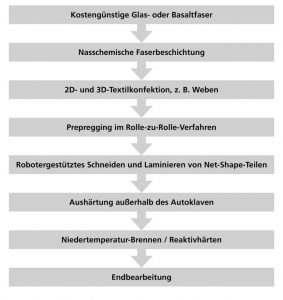
Abbildung 1: Prozesskette zur Herstellung von Low-Cost-CMC in einem geschlossenen Prozesskreislauf.
Technische Basis zur Herstellung von kostengünstigen CMC
Grundlage zur Herstellung kostengünstiger CMC-Bauteile ist neben der Verwendung kostengünstiger Rohstoffe und dem Verzicht auf Hochtemperaturprozesse die vollständige Automatisierung aller Produktionsschritte. Faser-Matrix-Zwischenschichten können durch nasschemische Beschichtung in einem schnellen Rolle-zu-Rolle-Verfahren aufgebracht werden. Der Prozessaufbau ist in Abbildung 2 dargestellt. Im Gegensatz zu CVD-Beschichtungen ist die Abscheidegeschwindigkeit mit ca. > 500 m/h deutlich höher. Weitere Vorteile sind die mögliche Mehrschichtabscheidung eines Schichtwerkstoffes innerhalb eines Zyklus mit bis zu acht Schichten sowie die Integration der thermischen Behandlung wie Entschlichten und Pyrolyse. Eine große Vielfalt an oxidischen und nicht-oxidischen keramischen Schichten kann als Interphasenmaterial aufgebracht werden. Die aufgetragenen Beschichtungen müssen eine sehr gute Haftung zur Oberfläche aufweisen, damit sie im nachfolgenden Webschritt ohne mechanische Beschädigung verarbeitet werden können. Außerdem müssen die Beschichtungen einen geringen Grad an Brückenbildung zwischen den Fasern aufweisen, um einen Faser- oder Beschichtungsbruch zu vermeiden [3].
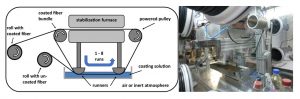
Abbildung 2: Faserbeschichtung durch nasschemische Abscheidung in einem schnellen Rolle-zu-Rolle-Verfahren. Quelle: Fraunhofer-Zentrum HTL
Im nächsten Schritt werden aus den Fasern textile Preformen hergestellt. Durch 3D-Weben und Flechten können neue Designs hergestellt werden. Auf diese Weise können maßgeschneiderte Halbzeuge für eine bestimmte Anwendung hergestellt werden, die zu einer kostengünstigen Produktion beitragen. Das Fraunhofer-Zentrum HTL verfügt über eine breite Palette von Anlagen für textile Fertigungsprozesse und bietet z. B. eine Doppelgreifer-Webmaschine mit Einzelfadenbetrieb, eine neue Option zur Herstellung von Geweben (Abbildung 3). Auf dieser Webmaschine werden anorganische und kohlenstoffbasierte Fasern verarbeitet. Mithilfe der Variationsflechttechnik können sehr komplexe Geflechte für diverse Anwendungsbereiche hergestellt werden (Abbildung 4). Der Entwicklungsschwerpunkt liegt in beiden Bereichen auf mehrdimensionalen textilen Preformen für die belastungsgerechte Bauteilgestaltung. Unterstützt durch eine Finite-Elemente-Simulation wird die Faserverstärkung optimal auf die Beanspruchung des späteren Bauteils ausgelegt und bei der Herstellung der Preform gezielt umgesetzt. Sowohl die textile Fertigung komplexer Formen als auch die lastkonforme Faseranordnung reduzieren die Kosten durch Einsparung teurer Fasern und Vermeidung von Fügeschritten bei der finalen Systemintegration.
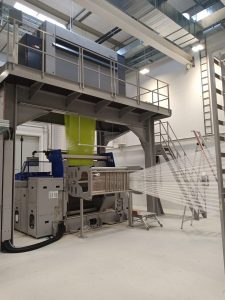
Abbildung 3: Doppelgreifer-Webmaschine mit Einzelfadenbetrieb. Quelle: Fraunhofer-Zentrum HTL
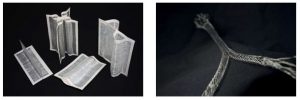
Abbildung 4: Beispiele für keramische Halbzeuge, die durch 3D-Weben und Flechten hergestellt wurden. Quelle: Fraunhofer-Zentrum HTL
Am Fraunhofer-Zentrum HTL steht eine vollautomatische Prepreg-Anlage zur Verfügung, um die benötigten Faser-Prepregs kostengünstig und in großen Mengen bereitzustellen (Typ KTF-S, Mathis, Schweiz). Die Anlage basiert auf einem Rolle-zu-Rolle-Verfahren, bei dem Fasergewebebänder bis zu einer maximalen Breite von 600 mm kontinuierlich von der Rolle mit einem flüssigen Medium getränkt und beschichtet werden und auf diese Weise die Matrix bilden. Das so entstandene Prepreg wird anschließend getrocknet und als Rollenware wieder aufgewickelt. Precursoren in flüssiger Form, z. B. Geopolymere, die durch Zugabe von Füllstoffen in ihrer Zusammensetzung variiert werden können, werden während des Prozesses imprägniert und nach der thermischen Verarbeitung zur Bildung der Matrix eingesetzt.
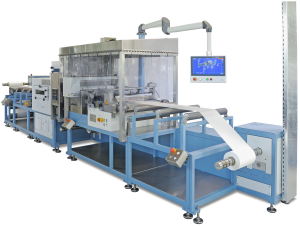
Abbildung 5: Prepreg-Anlage am Fraunhofer-Zentrum HTL. Quelle: Mathis AG
Mit Glas- und Kohlefasergeweben können vollimprägnierte Nass-Prepregs mit Flächengewichten von bis zu 700 g/m² erreicht werden. Zur Imprägnierung des Gewebes mit dem Precursor wird eine Floulard-Coater/Tauchbad Einheit verwendet. Die Homogenität der Prepregs über die Bahnbreite und -länge kann mit Versuchsproben nach DIN EN 2557 nachgewiesen werden. Die Abweichungen liegen bei < 5 %. Die Prepregs können mittels axialer Heißpresstechnik zu ebenen und delaminationsfreien Platten verpresst oder auch als Bänder abgelegt werden. Die homogene Verteilung der Matrix im Prepreg und deren Bindungsfähigkeit im Verbundwerkstoff können durch Prüfung der interlaminaren Scherfestigkeit nach DIN EN ISO 14130 nachgewiesen werden.
CMC-Bauteile werden während ihrer Entwicklung und – stichprobenartig – während der Produktion zerstörungsfrei geprüft (Abbildung 6). Das Fraunhofer-Zentrum HTL betreibt dazu eine hochmoderne Computertomographie (CT)-Anlage. Das System besteht aus einer Kombination von drei Röntgenröhren und einem schnellen Flächendetektor, sodass sowohl Untersuchungen an großen Bauteilen als auch Gefügeanalysen an kleinen Materialproben durchgeführt werden können. Delaminationen und Faserbrüche sowie andere Gefügefehler können bereits in der Produktionskette erkannt werden, was eine effiziente Beseitigung von Produktionsfehlern ermöglicht [4].
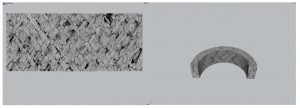
Abbildung 6: CT-Analysen von CMC-Material. Quelle: Fraunhofer-Zentrum HTL
Kostengünstige CMC-Systeme für mittlere Temperaturen
Drei Firmen, Walter E.C. Pritzkow Spezialkeramik, Pyrotek und InovaCeram, bieten bereits preisgünstige CMC für den Metallguss an. Sie basieren auf einer Silica- bzw. Glasfaserverstärkung. Pyrotek verwendet verschiedene Matrices aus Kalzium- oder Zirkoniumsilikat, Quarzglas oder Siliziumkarbid unter dem Markennamen „reinforced fibreglass material“ (RFM®). Das Material kann in dünnwandigen, komplexen Formen hergestellt werden [5]. Auch Walter E.C. Pritzkow Spezialkeramik und InovaCeram sind Anbieter für Aluminiumgussvorrichtungen, bei denen Silicafasern in Aluminiumoxid-Siliziumdioxid-Matrices eingebettet sind [6] (Abbildungen 7 und 8).
Im ZIM Verbundprojekt BaMox entwickelt das Fraunhofer-Zentrum HTL derzeit kostengünstige CMC für den Metallguss, die auf Basaltfasern basieren und in Geopolymermatrices eingebettet sind: sogenannte GMC. Projektpartner sind die TU Chemnitz, InovaCeram und die Metallgießerei Chemnitz. Im Rahmen des Projektes werden Zugfestigkeit, Bruchzähigkeit und thermomechanische Eigenschaften unter Verwendung unterschiedlicher Basaltgewebequalitäten in Kombination mit verschiedenen Geopolymermatrices optimiert. Die Entwicklung eines Handgusstiegels und eines Gießtrichters als Prototypen sollen die Möglichkeiten aufzeigen, die dieser neu konzipierte Werkstoff bietet. Die thermische und chemische Beständigkeit werden unter realem Einsatz im Aluminiumguss verifiziert (Abbildungen 9, 10).
- Abbildung 7: Glasfasern verstärken die Gussrinne. Quelle: InovaCeram
- Abbildung 8: Glasfaserverstärkte Gussrinne, abgeschirmt durch ein Stahlgehäuse. Quelle: InovaCeram
- Abbildung 9: Metallischer Gießtiegel. Quelle: Metallgießerei Chemnitz
- Abbildung 10: Gebrauchter Gießtiegel mit Keramikgewebeauskleidung. Quelle: Metallgießerei Chemnitz
Danach soll das Herstellungsverfahren in die Automatisierung überführt werden. Dazu entwickelt die TU Chemnitz ein Spritzgussverfahren, bei dem der Precursor in das eingelegte Basaltgewebe eingepresst wird. Neben Gießtiegeln sollen auch Feederboxen – Anlagenkomponenten bei der Serienherstellung von Komponenten aus Leichtmetallschmelzen – und Gießrinnen für den Einsatz in der Aluminiumgussindustrie hergestellt werden. Das GMC soll kostengünstig und langzeitbeständig gegen den Angriff der Schmelze und Ablagerungen sein und einen optimalen Gießerfolg ermöglichen, unterstützt durch eine geringe Wärmeabgabe. Außerdem soll seine nichtmetallische Oberfläche verhindern, dass die Schmelze nicht durch Abplatzen oder Auslaugen verunreinigt wird, was ein wichtiges Kriterium für einen hohen Qualitätsstandard ist. Eine weitere Anwendung von kostengünstigen CMC sind Stützstrukturen für metallische Bauteile, die bei Zwischentemperaturen anfällig für Kriechvorgänge sind. So wurden in einem weiteren Verbundprojekt, FaRo, CMC-Verstärkungen für hochbelastete Stahlrohre in Kraftwerken entwickelt. Projektpartner sind Schunk Kohlenstofftechnik, Bilfinger Piping Technologies GmbH, TÜV SÜD Industrie Service GmbH, Großkraftwerk Mannheim, Technion – Israel Institute of Technology, Materialprüfungsanstalt Stuttgart und Universität Bayreuth. In Dampfkraftwerken werden diese Stahlrohre mit einem hohen Innendruck von 350 bar bei Temperaturen von 650 °C belastet.
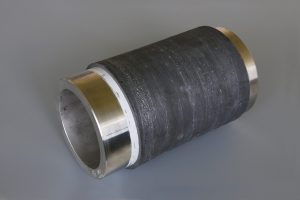
Abbildung 11: CMC-Bewehrung für Kraftwerksstahlrohre.
Quelle: Fraunhofer-Zentrum HTL
Unter diesen Bedingungen zeigt der Stahl ein tertiäres Kriechen, das durch eine um das Rohr gewickelte CMC-Struktur gestoppt werden kann (Abbildung 11), da das CMC eine wesentlich bessere Kriechbeständigkeit aufweist. Dieses CMC kann je nach Anforderung aus verschiedenen Faser- und Matrixsystemen und deren Kombinationen hergestellt werden. Neben hochpreisigen Fasertypen aus dem Korund- oder Mullitsystem können in vielen Anwendungen auch Basaltfasern oder Glasfasern eingesetzt werden. Die Matrix besteht aus Precursoren wie Polysiloxanen, Polycarbosilanen oder Polysilazanen, die in einem Temperaturbereich von 350 °C bis 800 °C [7] in amorphe Keramik überführt werden, die mit den preiswerten Fasern kompatibel ist.
Unabhängig von den genauen Marktanforderungen gibt es verschiedene Möglichkeiten für den Einsatz von preiswerten CMC bei mittleren Temperaturen. Wie ihre Hochtemperaturversionen benötigen sie eine hohe Bruchzähigkeit und gute chemische Beständigkeit. Werkstoffkonzepte und Gefügedesigns, die bereits für herkömmliche CMC entwickelt wurden, können direkt auf die Low-Cost-Composites übertragen werden. Schwache Grenzflächen oder schwache Matrices ermöglichen eine hohe Bruchzähigkeit, und eine lastangepasste Faseranordnung erhöht die Festigkeit. Im Vergleich zu handelsüblichen CMC tragen die Herstellungskosten relativ stark zur Gesamtkostenreduktion bei, da die Rohstoffkosten deutlich geringer sind. Es wird davon ausgegangen, dass kostengünstige CMC eine treibende Kraft für eine preiswertere und stärker automatisierte CMC-Produktion sein werden, die sich danach auch auf Hochtemperatur-CMC übertragen lässt.
Danksagung
Die Autoren bedanken sich für die finanzielle Unterstützung durch den Projektträger Jülich (PtJ) des BMWi im Verbundprojekt „Faserverstärkte Werkstoffsysteme“ (FaRo, FKZ 03ET7029C) und durch den Projektträger AiF des BMWi im Verbundprojekt „Entwicklung einer basaltfaserverstärkten Mischoxidkeramik als innovativer Verbundwerkstoff für kostengünstige Fertigungshilfsmittel in der Aluminiumgussindustrie“ (BaMox FKZ 16KN091322).
Literatur
- Raether, F. Ceramic Matrix Composites – an Alternative for Challanging Construction Tasks. Ceramic Applications. 2013, 1, S. 45-49.
- Nöth, A., Rüdinger, A., Pritzkow, W. Oxide Ceramic Matrix Composites – Manufacturing, Machining, Properties and Industrial Applications. Ceramic Applications. 2015, 3, S. 48-54.
- Maier, J., Nöth, A., Schönfeld, K. BN-Based Fibre Coatings by Wet-Chemical Coating. Key Engineering Materials. 2019, Vol. 809, S. 421-426.
- Seifert, G., Hausherr, J. M. Monitoring and Assessment of the Effect of Defects in Ceramics. Ceramic Forum International. 2020, Vol. 7-8, S. 37-40.
- www.pyrotek.com. Pyrotek Incorporated [Zitiert: 20 02 2021.].
- www.inovaceram.de. InovaCeram Technische Keramik [Zitiert: 20 02 2021.].
- Eckardt, C., Friedrich, M., Wamser, T., Wolff, N., Metzger, K. Faserverstärkte Keramik-Armierungen für den Rohrleitungsbau: Gut gerüstet gegen Druck und Hitze. Chemie Technik. April 2019, S. 38-40.
Autoren:
P. Vierhaus, J. Schmidt, A. Rüdinger
Fraunhofer-Zentrum für Hochtemperatur-Leichtbau HTL