Prof. Dr.-Ing. Christian Hopmann, Dipl.-Ing. Stefan Haase
Institut für Kunststoffverarbeitung (IKV) in Industrie und Handwerk an der RWTH Aachen
Die Nutzung von elektrisch leitfähigen Kunststoffen ermöglicht vielversprechende Lösungen für die integrierte Fertigung von elektrischen oder elektronischen Funktionsbauteilen. Dabei können durch das Umspritzen metallischer Kontakte von standardisierten Funktionsbauteilen wie LEDs, Widerständen oder Kontaktpins diese kontaktiert und somit komplexe Schaltungen realisiert werden.
Einleitung
Kunststoffe kommen oftmals aufgrund ihrer hervorragenden isolierenden Eigenschaften zum Einsatz. Durch Zugabe von elektrisch leitfähigen Füllstoffen ist es möglich, dem Werkstoff eine gewisse elektrische Leitfähigkeit zu verleihen und ihn so für Anwendungen, beispielsweise zur Ableitung elektrostatischer Aufladungen in explosionsgefährdeten Bereichen, nutzbar zu machen. Sollen jedoch eine höhere Leitfähigkeit erzielt oder elektrische Leistung übertragen werden, sind Kunststoffcompounds mit nur einem elektrisch leitfähigen Füllstoff zumeist nicht ausreichend [1-3].
Um diese Anforderungen mit spritzgegossenen Bauteilen zu erfüllen, werden daher derzeit noch gestanzte metallische Einleger verwendet oder Molded Interconnect Devices (MID)-Strukturen aufgebracht. Dies erfordert jedoch jeweils zusätzliche, vor- und nachgelagerte Verfahrensschritte, die zu höheren Fertigungskosten führen [1-5].
In den letzten Jahren wurden daher am Institut für Kunststoffverarbeitung (IKV) in Industrie und Handwerk an der RWTH Aachen ternäre Compounds entwickelt, die aus einem Matrixwerkstoff und zwei unterschiedlichen elektrisch leitfähigen Füllstoffen bestehen. Als Füllstoffe kommen dabei mikroskalige Kupfer- oder Carbonfasern sowie nanoskalige Carbon Nanotubes (CNT) oder Ruße zum Einsatz. Durch die Kombination von Füllstoffen unterschiedlicher Größe wird ein Synergieeffekt hervorgerufen, bei dem zunächst die mikroskaligen Füllstoffe ein leitfähiges Netzwerk ausbilden, dessen Lücken dann durch in der Matrix fein verteilte Nanofüllstoffe geschlossen werden. So werden mehr mikroskalige Füllstoffe in das leitfähige Netzwerk eingebunden und die Leitfähigkeit der ternären Compounds kann bis in den Bereich der metallischen Leiter gesteigert werden (> 106 S/m)
[1, 3, 6, 7].
Die Bereitstellung von spritzgießfähigen elektrisch leitfähigen Compounds allein ist jedoch für die Produktion komplexer elektrischer Strukturen nicht ausreichend. Es ist darüber hinaus erforderlich ein Verständnis für den elektrischen und mechanischen Verbund dieser Werkstoffe mit metallischen Kontakten von elektrischen oder elektronischen Funktionselementen zu entwickeln. Der elektrisch leitfähige hybride Verbund muss dabei neben einer guten elektrischen Leitfähigkeit auch eine ausreichende Verbundfestigkeit der Kontaktfläche aufweisen. Gleichzeitig ist es für den technischen Einsatz von Bedeutung, welche Ströme übertragen werden können und wie groß dabei die Verlustleistung bzw. die resultierende Materialerwärmung ist.
Elektrische Leitfähigkeit kontaktierter Leiterbahnen
Für die Auslegung leitfähiger Verbindungen zwischen elektrischen oder elektronischen Bauelementen und leitfähigen Compounds fehlt es derzeit noch an Kennwerten für die zu erwartenden die elektrischen und mechanischen Eigenschaften. Zur Bestimmung dieser Kennwerte wurden aus Compounds, die aus den in Tabelle 1 gelisteten Matrixmaterialien und Werkstoffen erstellt wurden, durch Umspritzen metallischer Einleger Probekörper erstellt und diese analysiert. Die Zusammensetzung der untersuchten Compounds kann Tabelle 2 entnommen werden.
Aus den Compounds wurden auf einer Spritzgießmaschine vom Typ Allrounder 370 A 600-170/170 der Firma Arburg GmbH + Co, Loßburg durch Umspritzen von glatten verzinnten Kupferdrähten Probekörper hergestellt. Als Werkzeug wurde ein modular aufgebautes Spritzgießwerkzeug verwendet. Die Geometrie der Probekörper und des Werkzeugeinsatzes ist in Abbildung 2 dargestellt. Der Probekörper hat die Abmessungen 40 x 20 x 4 mm³. Die metallischen Einleger sind im Abstand von 30 mm angeordnet.
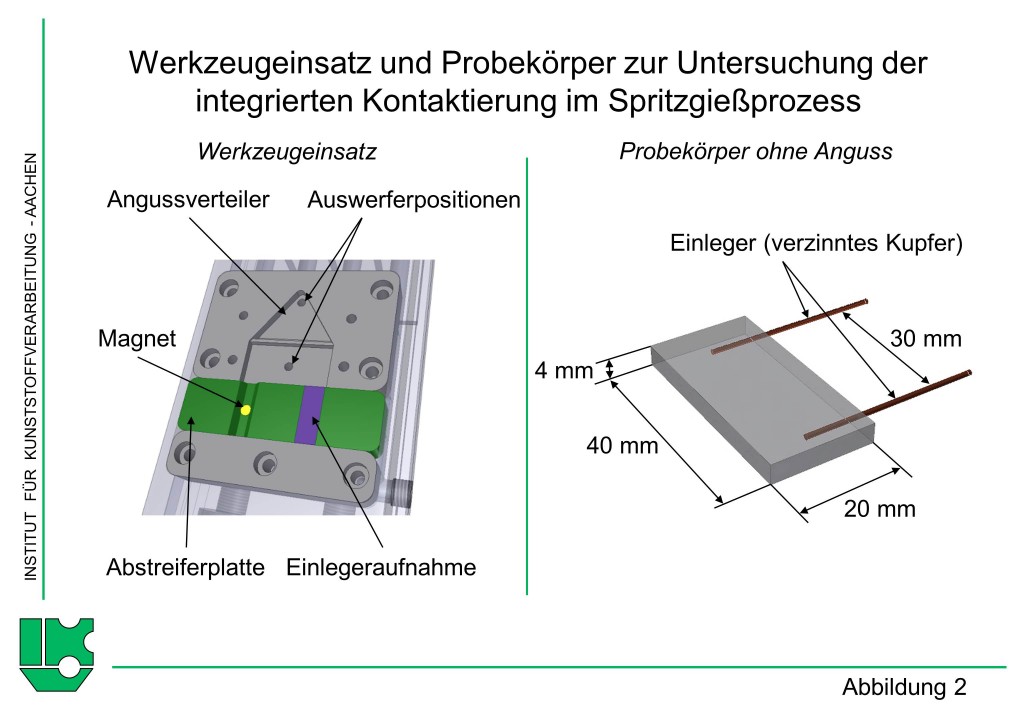
Abbildung 2 Werkzeugeinsatz und Probekörper zur Untersuchung der integrierten Kontaktierung im Spritzgießprozess
Die elektrischen Durchgangsleitfähigkeiten der Compounds sind in Abbildung 3 dargestellt. Es zeigt sich der bereits bekannte Effekt, dass durch Zugabe von nanoskaligen Füllstoffen die Leitfähigkeit signifikant gesteigert werden kann. Dabei wir durch die Zugabe von 15 Vol.-% Ruß (PA-CuF-Ruß) eine Steigerung der elektrischen Leitfähigkeit von über einer Größenordnung erzielt. Wird stattdessen der Anteil der Kupferfasern um ebenfalls 15 Vol.-% erhöht, so bleibt der Anstieg der Leitfähigkeit etwa 50 % unter diesem Wert. Die höchste elektrische Leitfähigkeit wird bei einem Compound auf Basis von Kupferfasern und einer niedrig schmelzenden Metalllegierung (PA-CuF-MCP) gemessen und liegt bei ca. 2 x 105 S/m [7].
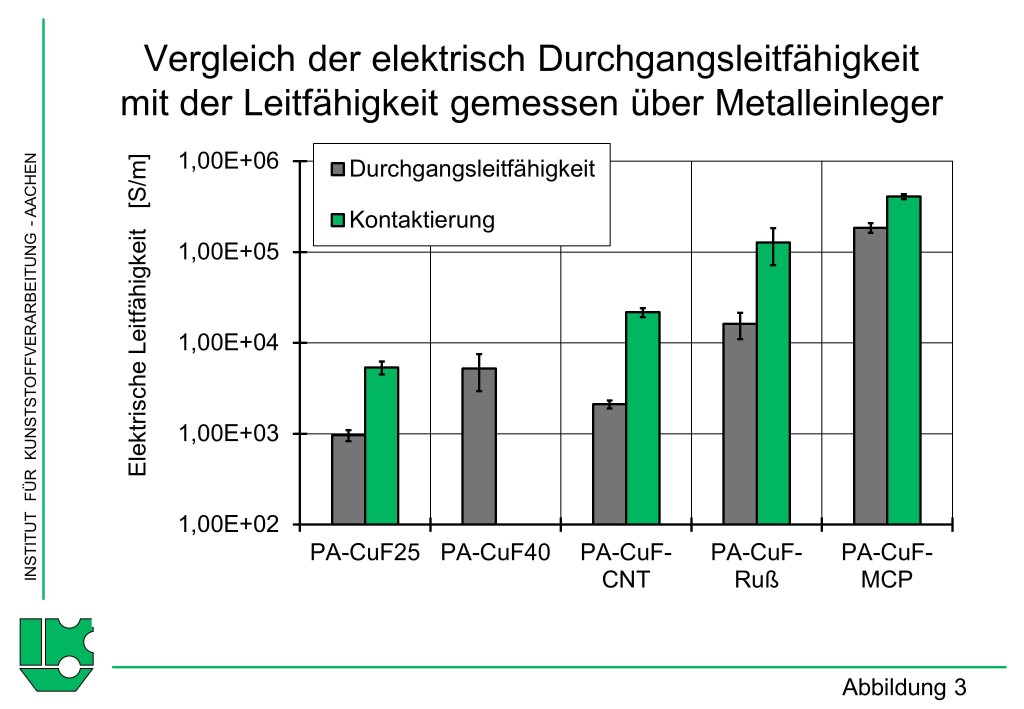
Abbildung 3 Vergleich der elektrisch Durchgangsleitfähigkeitmit der Leitfähigkeit gemessen über Metalleinleger
Vergleichend dazu ist die Leitfähigkeit dargestellt, die sich bei Messung über zwei umspritzte verzinnte Kupferdrähte von 1,2 mm Durchmesser bei 10 mm umspritzter Länge ergibt. Es ist ersichtlich, dass die gemessene Leitfähigkeit für jedes mit Metalleinleger kontaktierte Material oberhalb der Messung der Durchgangsfähigkeit des Compounds liegt. Dies kann auf die Messung der Durchgangsleitfähigkeit des reinen Compounds durch Aufpressen von Elektroden zurückgeführt werden, bei der ein erhöhter Übergangswiderstand auftritt. Zugleich verdeutlicht dieser Effekt die Eignung der Kontaktierung durch Umspritzen der metallischen Kontakte. Das Compound mit dem erhöhten Kupferfaseranteil dient hier lediglich als Vergleich und wurde nicht zu kontaktierten Probekörpern verarbeitet [8].
Für die Messung der Leitfähigkeit zwischen den Einlegern wurde eine große Kontaktfläche zwischen Einleger und Compound von über 38 mm² gewählt. Dies ist für viele industrielle Anwendungen jedoch nicht zu realisieren. Es wurde daher die Abhängigkeit der Leitfähigkeit sowohl vom Durchmesser der metallischen Einleger als auch der umspritzten Länge untersucht.
Die Ergebnisse sind in Abbildung 4 und 5 dargestellt. Abbildung 3 zeigt die ermittelte elektrische Leitfähigkeit über der Kontaktfläche zwischen Einleger und leitfähigem Compound bei Variation des Einlegerdurchmessers. Dabei wird jeweils eine Länge von 10 mm des Einlegers aus verzinntem Kupfer umspritzt. Die Leitfähigkeit wird dabei bestimmt zu:
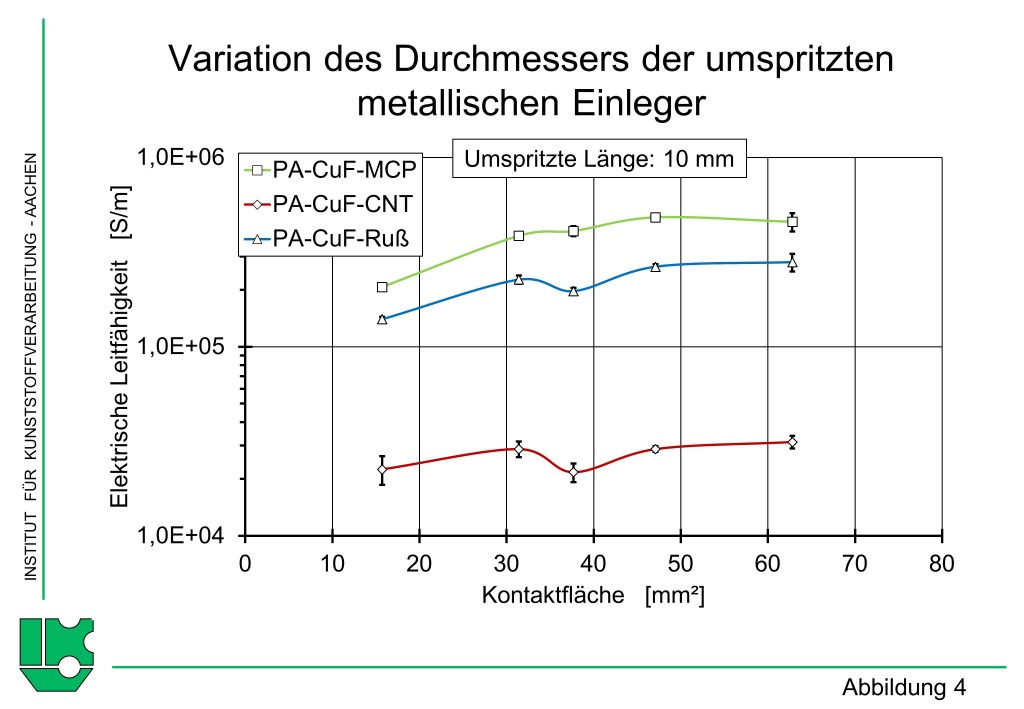
Abbildung 4 Variation des Durchmessers der umspritzten metallischen Einleger
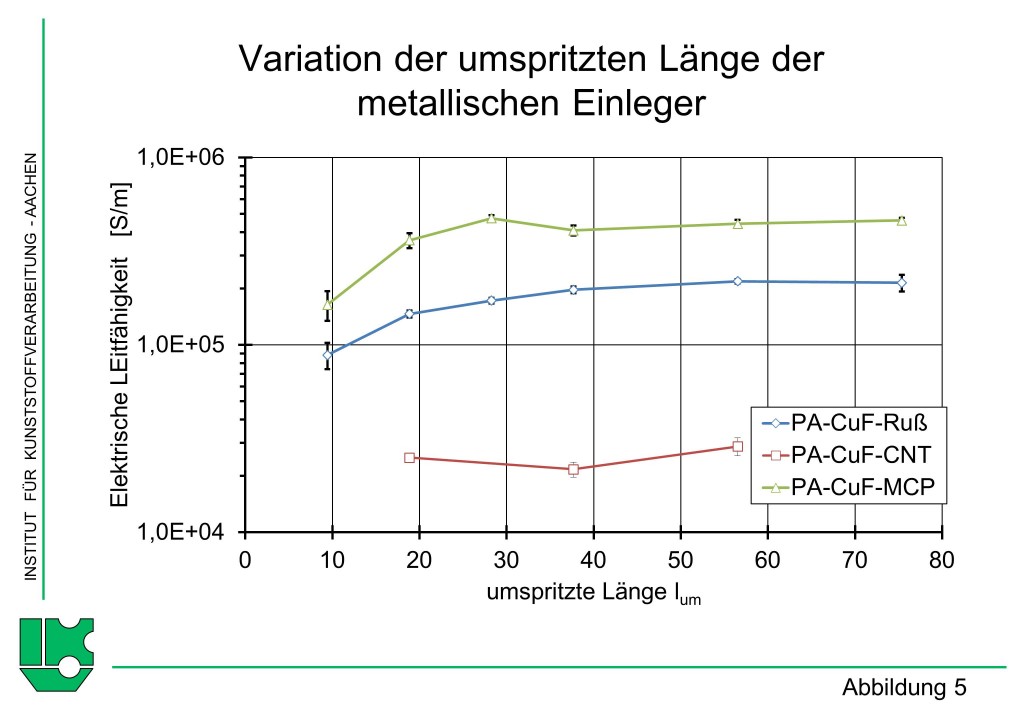
Abbildung 5 Variation der umspritzten Länge der metallischen Einleger
Für alle untersuchten Compounds geht eine größere Kontaktfläche mit einer höheren elektrischen Leitfähigkeit einher. Im Verlauf der elektrischen Leitfähigkeit zeigt sich ein Knick bei den Proben mit einem Durchmesser von 1,2 mm bzw. einer Kontaktfläche von ca. 38 mm². Dieses Phänomen kann derzeit nicht abschließend erklärt werden. Da es jedoch bei allen Proben mit 1,2 mm² Durchmesser auftritt, wird angenommen, dass es auf die metallischen Einleger zurückzuführen ist.
Abbildung 4 zeigt die elektrische Leitfähigkeit zwischen den umspritzten Einlegern bei Variation der umspritzten Länge und einem konstanten Durchmesser der Einleger von 1,2 mm. Auch hier steigt die elektrische Leitfähigkeit mit zunehmender Kontaktfläche an. Die Kurvenverläufe sind denen bei Variation des Einlegerdurchmessers sehr ähnlich. Es kann daher vermutet werden, dass die elektrische Leitfähigkeit eines Einleger-Kunststoffcompound-Verbundes primär durch die Kontaktfläche bestimmt wird. Für beide Fälle zeigt sich dabei ein Anstieg der Leitfähigkeit bis ca. 48 mm². Es ist anzunehmen, dass sich der Wert bei weiterer Steigerung der Kontaktfläche weiter an Leitfähigkeit des Compounds asymptotisch annähert.
Verbundfestigkeit metallischer Einleger mit leitfähigen Kunststoffcompounds
Neben Untersuchungen zur elektrischen Leitfähigkeit wurde auch die Verbundfestigkeit zwischen metallischem Einlegern und elektrisch leitfähigen Compounds analysiert. Dabei wird ein linearer Zusammenhang zwischen der Kontaktfläche und der Auszugskraft festgestellt. Die Steigung der maximalen Auszugskraft über der Kontaktfläche entspricht näherungsweise der mittleren Schubspannung an der Oberfläche des Einlegers. Sie nimmt für die untersuchten Werkstoffe Werte zwischen 3,3 N/mm² (PA-CuF) und 2,6 N/mm² (PA-CuF-CNT) an.
Vorbehandlung der Einleger
Zur Steigerung der Verbundfestigkeit wurden im weiteren Verlauf die folgenden unterschiedlichen Vorbehandlungsmethoden der Einleger untersucht:
- Reinigen mit Aceton
- Beflammen
- Plasmavorbehandeln
- Aufrauen der Oberfläche
- Variotherme Prozessführung mit Induktion
Dazu wurden die Einleger vor dem Umspritzen mit einem der Verfahren vorbehandelt. Zur Ermittlung der Ausszugskraft wurden die Probekörper in eine Zugprüfmaschine vom Typ Z010 der Firma Zwick GmbH & Co KG, Ulm eingespannt und die Einleger bei konstanter Traversengeschwindigkeit bis zum Versagen der Verbindung belastet. Die höchste dabei gemessene Auszugskraft wird als Kennwert für die Verbundfestigkeit von Einleger und Kunststoffcompound herangezogen.
Zunächst wurde in Voruntersuchungen der Einfluss der Reinigung der Einlegeroberfläche mit Aceton untersucht. Es zeigt sich dabei, dass das Entfetten der Oberfläche nahezu keinen Einfluss auf die elektrische Leitfähigkeit hat. Die Verbundfestigkeit kann jedoch signifikant gesteigert werden (26 %). Die Ergebnisse für die gereinigten Einleger dienen als Vergleichswert für die Wirksamkeit der anderen Vorbehandlungsverfahren. Die Ergebnisse der Versuche für die elektrische Leitfähigkeit sind in Abbildung 6 dargestellt. Es zeigt sich, dass es durch Vorbehandlung der Oberfläche mit den untersuchten Verfahren nicht möglich ist, die Leitfähigkeit im Bereich der Kontaktfläche gezielt zu erhöhen. Im Gegenteil wird durch die Aktivierung der Oberfläche mit der Plasmabehandlung (Atmosphärendruckplasma, Argon) eine deutliche Reduktion der Leitfähigkeit um ca. 70 % bewirkt. Dies wird auf die Entstehung von reaktiven aber weniger leitfähigen Schichten auf der Oberfläche der metallischen Einleger durch die Plasmabehandlung zurückgeführt.
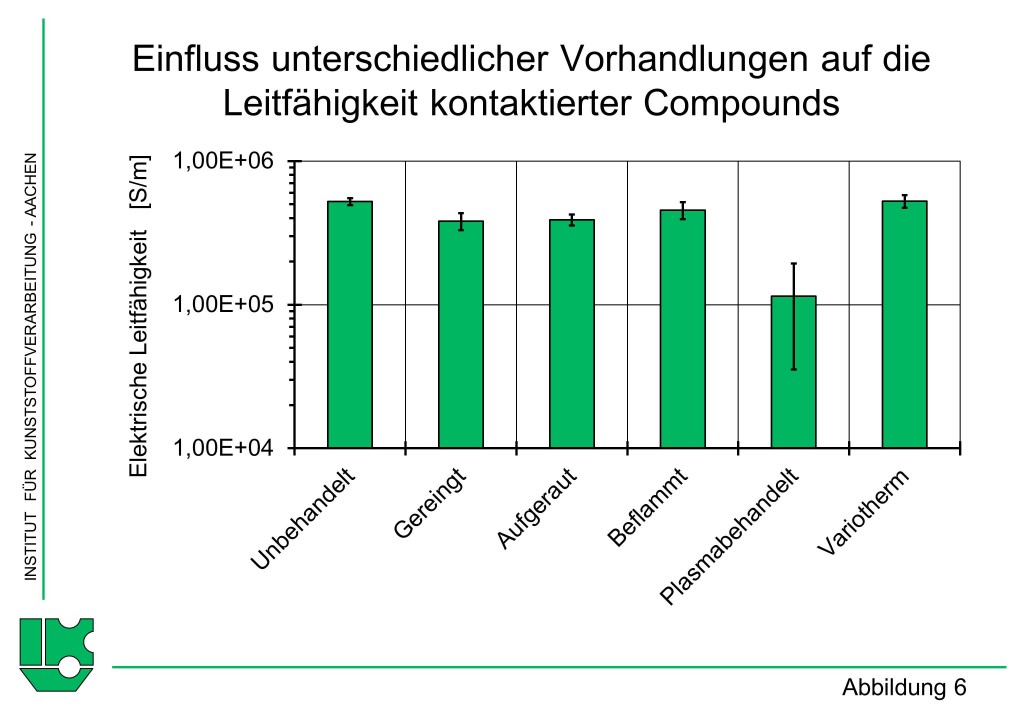
Abbildung 6 Einfluss unterschiedlicher Vorhandlungen auf die Leitfähigkeit kontaktierter Compounds
Die Vorbehandlung der Oberflächen kann jedoch für eine Verbesserung der Verbundfestigkeit genutzt werden. Abbildung 7 zeigt die gemessenen maximalen Auszugskräfte in Abhängigkeit der Vorbehandlungsverfahren. Mit allen Verfahren kann eine Verbesserung der Verbundfestigkeit erzielt werden. Die besten Ergebnisse werden dabei mit aufgerauten Einlegern (Erhöhung der Rauheit von 0,85 µm auf 7,5 µm) und bei variothermer Prozessführung (Induktor, 167 °C Oberflächentemperatur des Einlegers gegenüber 80 °C bei herkömmlicher Prozessführung) erzielt. Die Verbundfestigkeiten können dabei um über 200 % gesteigert werden. Insbesondere das Aufrauen der metallischen Oberfläche führt zu einer deutlichen Steigerung der Verbundfestigkeit. Dies steht im Einklang mit bisherigen Ergebnissen zur Verbundfestigkeit von Kunststoff-Metall-Verbünden. Es stellt sich jedoch die Frage, wieso die höhere tatsächliche Oberfläche und die entstehenden Hinterschnitte nicht mit einer Verbesserung der elektrischen Leitfähigkeit einhergehen. Bei mikroskopischer Betrachtung der Kontaktfläche zwischen Einleger und leitfähigem Compound zeigt sich eine füllstofffreie Randschicht um die Einleger (Abbildung 8). Diese Randschicht wird sich auch bei aufgerauten Oberflächen einstellen. Da sie keine Kupferfasern enthält, ist die elektrische Leitfähigkeit des Compounds im Bereich der Randschicht lokal vermindert. Gleichzeitig sind die Kupferfasern zu groß, um in die Bereiche der Hinterschnitte einzudringen, sodass der Abstand zwischen metallischem Einleger und den Kupferfasern steigt. Die vergrößerte wirkliche Oberfläche hat daher keine Auswirkungen auf die elektrische Leitfähigkeit.
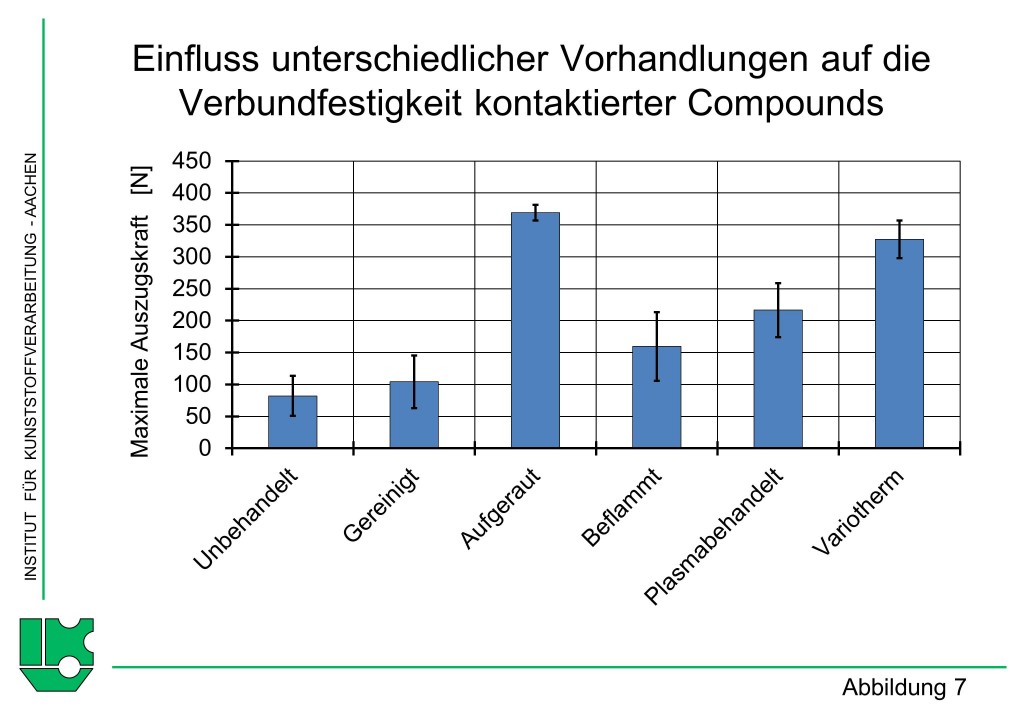
Abbildung 7 Einfluss unterschiedlicher Vorhandlungen auf die Verbundfestigkeit kontaktierter Compounds
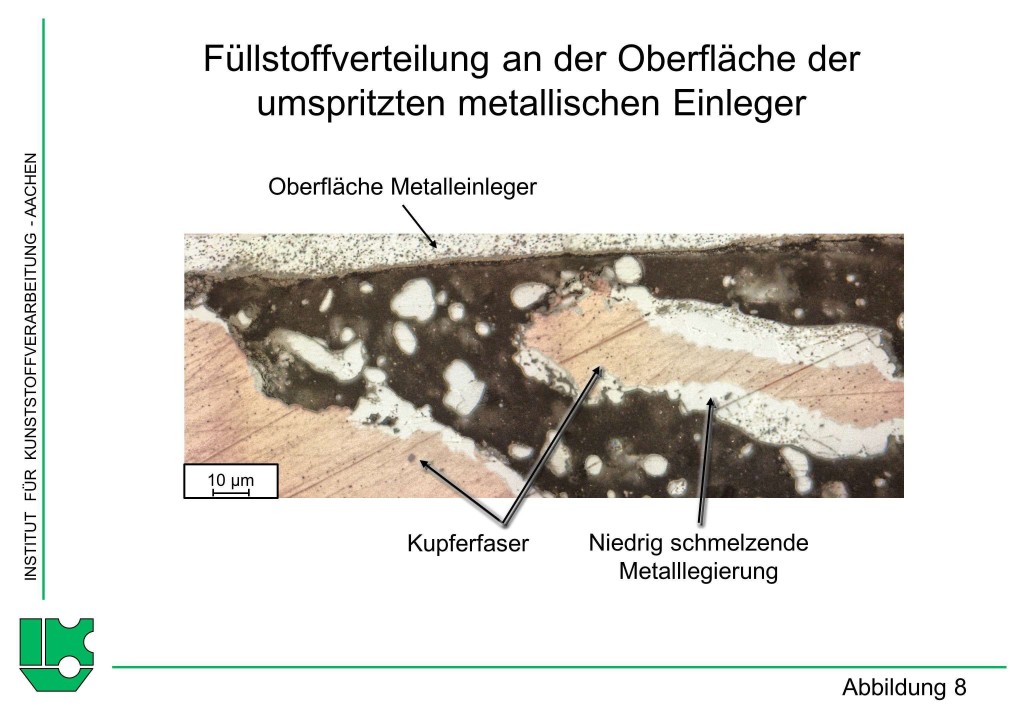
Abbildung 8 Füllstoffverteilung an der Oberfläche der umspritzten metallischen Einleger
Fazit und Ausblick
Mit der integrierten Fertigung von elektrischen oder elektronischen Bauteilen im Spritzgießprozess können elektrische Funktionselemente in Leiterbahnen eingebunden und somit komplexe Schaltungen erzeugt werden. Durch die Vermeidung von Prozessschritten wie dem Stanzen von Leiterbahnen oder dem Löten der elektrischen Kontakte ergeben sich dabei insbesondere wirtschaftliche Vorteile.
Für die Ausnutzung des vollen Potenzials der hohen elektrischen Leitfähigkeit müssen vergleichsweise große Kontaktflächen geschaffen werden. Die Verbundfestigkeit der Metalleinleger-Kunststoffcompound-Verbünde kann durch gezielte Vorbehandlung der Einleger stark gesteigert werden. Insbesondere raue Oberflächen zeichnen sich hier aus. Auch die variotherme Prozessführung ist geeignet, da sie jedoch in der Regel mit einer erhöhten Zykluszeit einhergeht, sollten raue Einleger bevorzugt werden.
In weiteren Untersuchungen wird am IKV der Einfluss alternativer niedrig schmelzender Metalllegierungen untersucht werden. Ziel der Forschungen wird eine höhere Verbundfestigkeit bei weiterhin guter elektrischer Leitfähigkeit und sinkenden Materialkosten sein.
Dank
Das IGF-Vorhaben 17053 N der Forschungsvereinigung Kunststoffverarbeitung wurde über die AiF im Rahmen des Programms zur Förderung der Industriellen Gemeinschaftsforschung (IGF) vom Bundesministerium für Wirtschaft und Energie aufgrund eines Beschlusses des Deutschen Bundestages gefördert.
Unser Dank gilt ebenfalls den Firmen Arburg GmbH & Ko KG, A. Schulman GmbH, BASF SE, Coperion Werner & Pfleiderer GmbH & Co. KG, Nanocyl SA, Orion Engineerd Carbons, Phoenix Contact GmbH & Co. KG und Sabic Europe, die durch wertvolle Hinweise sowie Bereitstellung von Materialien, Maschinen und sonstigen Mitteln diese Arbeiten unterstützt haben.
Die Autoren
Prof. Dr.-Ing. Christian Hopmann, geb. 1968, ist Inhaber des Lehrstuhls für Kunststoffverarbeitung der RWTH Aachen und Leiter des Instituts für Kunststoffverarbeitung (IKV) seit dem 01. April 2011
Dipl.-Ing. Stefan Haase, geb. 1985, ist seit 2013 wissenschaftlicher Mitarbeiter des Instituts für Kunststoffverarbeitung (IKV) und leitet die Arbeitsgruppe Sonderwerkstoffe in der Abteilung Spritzgießen
Kontakt
Institut für Kunststoffverarbeitung
Dipl.-Ing. Stefan Haase
Pontstr. 49, 52062 Aachen
haase@ikv.rwth-aachen.de
www.ikv-aachen.de
Fachartikel zum Thema elektrisch leitfähige Kunststoffe aus Werkstoffe in der Fertigung 3/2015
[1] Pfefferkorn, T. G.: Analyse der Verarbeitungs- und Materialeigenschaften elektrisch leitfähiger Kunststoffe auf Basis niedrig schmelzender Metalllegierungen. RWTH Aachen, Dissertation, 2009 – ISBN: 978-3-86130-864-5
[2] Pfeiffer, B.: Überblick über leitfähige Kunststoffe. Umdruck zur Fachtagung Elektrisch leitfähige Kunststoffe, Regensburg 2010
[3] Hopmann, Ch.; Fragner, J.: Verbesserte Leitfähigkeiten von Kunststoffen. Kunststoffe 101 (2011) 12, S. 27-30
[4] Mair, H. J.; Roth, S.: Elektrisch leitende Kunststoffe. München, Wien: Carl Hanser Verlag 1989
[5] Weckermann, A.: DFG Sonderforschungsbereich 694 – Integration elektronischer Komponenten in mobile Systeme. Aachen: Shaker Verlag, 2010
[6] Micheali, W.; Kamps, T.; Fragner, J.; Pfefferkorn, T.: Hybridtechnologie Spritzgießen: Verfahrensintegration für Mikrobauteile und Verbindungstechniken. Konstruktion 63 (2011) 5, S. 67-72
[7] Hopmann, Ch.; Fragner, J.: Integration von Elektronik. Plastverarbeiter 64 (2013) 8, S. 48 – 50
[8] Hopmann, Ch.; Fragner, J.; Haase, S.: Elektrisch leitfähige Kunststoffe und metallische Einlegeteile. Kunststoffe 103 (2013) 10, S. 178 – 182