Einleitung
Herkömmliche nichtrostende austenitische Stähle (FeCrNi) enthalten als wesentliche Legierungselemente Chrom (ca. 18 Ma.-%) und Nickel (ca. 8 Ma.-%). Ein ausreichend hoher Chromgehalt führt zur Ausbildung einer dünnen, dicht haftenden Passivschicht, welche die Korrosionsbeständigkeit gewährleistet. Nickel dient hauptsächlich der Stabilisierung der austenitischen Phase [1]. Im Allgemeinen ergeben sich für FeCrNi-Austenite als charakteristische Eigenschaften eine hohe Korrosionsbeständigkeit sowie sehr gute Zähigkeit und Duktilität. Demgegenüber steht eine für viele Anwendungen ungünstige relativ geringe Festigkeit. Eine Festigkeitssteigerung ist durch Kaltverfestigung möglich, dies kann jedoch mit einer verformungsbedingten Phasenumwandlung von Austenit in Martensit einhergehen. Eine weitere Möglichkeit stellt die Zugabe von (interstitiellen) Zwischengitterelementen, insbesondere Stickstoff, dar, wodurch eine höhere Festigkeit, bessere Kaltverfestigung und gleichzeitig eine Stabilisierung der austenitischen Phase erreicht werden kann, so lange die interstitiellen Elemente im Metallgitter gelöst vorliegen. In diesem Zusammenhang ist zu beachten, dass die Löslichkeit von Stickstoff in FeCrNi-Stählen begrenzt ist, jedoch durch eine (teilweise) Substitution von Nickel durch das ebenfalls austenitstabilisierende Element Mangan erhöht werden kann. Hierdurch können höhere Stickstoffmengen bis ca. 0,6 Ma.-% zugesetzt werden („High Nitrogen Steels“ („HNS“)) [2].
Hohe Stickstoffgehalte > 0,6 Ma.-% können jedoch kostenintensive Maßnahmen erfordern. Diese können die Zugabe weiterer stickstofflöslichkeitssteigernder Legierungselemente oder druckmetallurgischer Maßnahmen beinhalten. Neuere Entwicklungen zielten daher auf die Zugabe hoher Mengen an interstitiellen Elementen bei Umgebungsdruck ab, was durch Zugabe von Kohlenstoff beziehungsweise den teilweisen Ersatz von Stickstoff durch Kohlenstoff erreicht wurde. Die so genannten austenitischen „High Interstitial Steels“ (HIS) kombinieren hervorragende mechanische Eigenschaften mit guter Korrosionsbeständigkeit und können mit konventioneller Metallurgie hergestellt werden [3].
HNS und HIS behalten infolge ihrer sehr hohen Austenitstabilität auch bei hohen Kaltverformungsgraden ein vollständig austenitisches Gefüge, folglich sind sie nicht magnetisierbar. Diese Eigenschaften ermöglichen den Einsatz in anspruchsvollen Anwendungen, beispielsweise in der Öl- und Gasexploration, in Unterwasserumgebungen oder im medizinischen Sektor. Andererseits können die mechanischen Eigenschaften von HNS und HIS, insbesondere die Kombination aus hoher Zähigkeit und intensiver Kaltverfestigung, bei der Bearbeitung zu Herausforderungen in Bezug auf Spanbildung und Werkzeugverschleiß führen. Das vergleichsweise hohe Verfestigungsvermögen kann hingegen auch im Anschluss an die spanende Bearbeitung in Form eines Walzprozesses genutzt werden, um die Bauteilfestigkeit signifikant zu steigern. Die nachfolgend vorgestellten technologischen Untersuchungen sollen die Besonderheiten dieser Werkstoffgruppe bei der spanenden und walzenden Bearbeitung darstellen und hierbei insbesondere die Einflüsse der verschiedenen Prozessschritte auf die Randzone sowie die Werkstückoberfläche fokussieren. Die Betrachtungen umfassen hierbei die Bearbeitung von zwei austenitischen hochfesten nichtrostenden Stählen.
Experimentelle Randbedingungen
Als Werkstoffe wurden der HNS X3MnCrNiMoN19-16-5-3 (Magnadur 601) sowie der HIS X30CrMnN18-18 (Magnadur CN0,85) des Stahlherstellers Deutsche Edelstahlwerke Specialty Steel GmbH & Co. KG verwendet. Die kommerziell erhältliche Variante Magnadur 601 findet unter anderem in der Öl- und Gasexploration Einsatz. Der im Rahmen eines öffentlich geförderten Forschungsprojektes in Kooperation mit dem Lehrstuhl für Werkstofftechnik an der Ruhr-Universität Bochum hergestellte Stahl CN0,85 findet zum Beispiel Einsatz als rostfreier Lagerstahl. Die Werkstücke (Stabstahl, 60 mm Durchmesser) befinden sich im lösungsgeglühten Zustand, sodass ein vollständig austenitisches, ausscheidungsfreies Gefüge gewährleistet wird. Die sich daraus ergebenden Eigenschaften (geprüft an in Längsrichtung entnommenen Zugproben) sowie die chemischen Analysen werden in Abbildung 1 dargestellt.
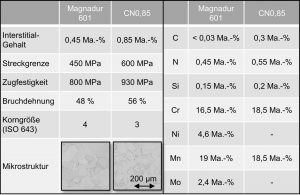
Abbildung 1: Chemische Zusammensetzung und Eigenschaften der untersuchten Werkstoffe
In den experimentellen Untersuchungen wurden Wendeschneidplatten der Anwendergruppe ISO-M für die Bearbeitung von austenitischen Stählen der Fa. Seco Tools verwendet (Vgl. Abbildung 2). Die Wendeschneidplatte des Typs CNMG120408-MF4 TM2501 wird für Schruppversuche und der Typ VBMT160404-F1 TM2501 für Schlichtbearbeitungen eingesetzt. Beide Wendeschneidplatten bestehen aus demselben Schneidstoff und bieten eine hohe Schneidkantenstabilität und Verschleißfestigkeit für die Bearbeitung austenitischer rostfreier Stahlsorten. Der Werkzeugtyp CNMG120408-MF4 zeichnet sich durch eine offene, negative Geometrie mit einem Hauptfreiwinkel von α = 0° und einem Schneidkantenradius von rβ = 36 mm aus. Im Vergleich dazu hat die positive Schlichtplatte vom Typ VBMT160404-F1 einen ähnlichen Schneidkantenradius, aber einen Freiwinkel von α = 5°. Für die walzende Nachbearbeitung wird das hydrostatische Werkzeug HG6-9 der Fa. Ecoroll verwendet. Das Walzelement umfasst eine Hartstoffkugel, einen Kugeleinsatz sowie ein Nachführsystem. Die Druckbeaufschlagung des Werkzeugs erfolgt über das Schneidöl der Drehmaschine und wird mittels eines externen Hydraulikaggregats eingestellt.
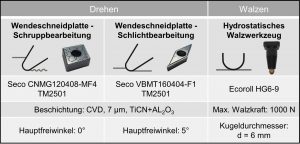
Abbildung 2: Eingesetzte Werkzeuge für die Dreh- und Walzbearbeitung
Die Versuchsreihen wurden auf der CNC-Drehmaschine Monforts RNC200A durchgeführt, die eine Antriebsleistung von Pmax = 13 kW aufweist. Das eingesetzte Schneidöl des Typs Blasomill 13 der Blaser Swisslube AG ist auf mineralischer Basis und verwendet Anti-Wear- sowie Extreme-Pressure-Additive. Für die Untersuchungen der Oberflächengüte sowie Randzonenintegrität wurden ein Rauheitsmessgerät (Hommel Etamic W5), ein Härteprüfer (Shimadzu HMV-G) und ein Lichtmikroskop (Zeiss Axio Imager M1m) verwendet.
Technologische Untersuchungen
Die Bearbeitung der nichtrostenden, amagnetischen Stähle weist durch die zuvor beschriebenen Eigenschaften besondere Charakteristika auf. In den Untersuchungen wurden die Werkstücke hierbei mittels eines Außenlängsdrehprozesses geschruppt und geschlichtet sowie durch einen Walzprozess mechanisch nachbearbeitet. Für die Schruppbearbeitung wurden mit der dargestellten CNMG-Wendeschneidplatte zunächst geeignete Schnittparameter unter Berücksichtigung der Spanform und des Werkzeugverschleißes erarbeitet. Bei einem Vorschub von f = 0,3 mm, einer Schnitttiefe von ap = 1,5 mm und einer Schnittgeschwindigkeit von vc = 50 m/min kann eine hohe Prozesssicherheit bei gegebener Werkzeugstandzeit gewährleistet werden. Ebenso erfolgte eine Parameteridentifikation für einen Schlichtprozess mit einer VBMT-Wendeschneidplatte, hierbei wird insbesondere die Oberflächengüte und der Spanabtransport fokussiert. Herausfordernd stellt sich aufgrund der hohen Materialduktilität die Spanbildung und –form dar. Ein prozesssicherer Spanabtransport und eine hohe Oberflächengüte können in diesem Zusammenhang mit einem Vorschub von f = 0,1 mm und einer Schnitttiefe von ap = 0,4 mm eingestellt werden. Der Walzprozess erfolgt mit dem hydrostatischen Walzwerkzeug unter einem Druck von pw = 600 bar bei einem Vorschub von vw = 0,1 mm. Im Anschluss an die Bearbeitung erfolgte die Analyse der Oberflächengüte sowie der Mikrohärte in der Werkstückrandzone. Die Ergebnisse zeigen hierbei den signifikanten Einfluss der Prozesse sowie der Prozessparameter auf das Werkstück auf (Vgl. Abbildung 3).
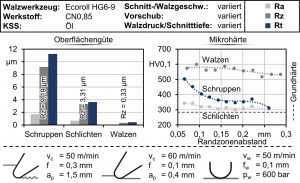
Abbildung 3: Einfluss der eingesetzten Prozesse auf Rauheit und Verfestigung des Werkstoffes CN0,85
Ausgehend vom Schruppprozess können die Rauheitskennwerte durch den Schlichtprozess mit verringertem Vorschub bereits etwa um den Faktor drei reduziert werden. Im Anschluss kann durch einen Walzvorgang eine effektive Einebnung der beim Drehprozess hervorgerufenen Rauheitsspitzen erzielt werden. Weiterhin werden die Profiltäler angehoben, sodass die ermittelten Werte zur Rauheit im Vergleich zum Schlichtvorgang auf ein Zehntel gesenkt werden können. Die Walzbearbeitung kann folglich in diesem Zusammenhang als zielführender Glattwalzprozess beschrieben werden.
Bei Analyse der Mikrohärte in der Randzone zeigt sich bereits bei der Drehbearbeitung der Einfluss der interstitiellen Elemente auf die Verfestigung. Hierbei wurde für den Schruppprozess eine Aufhärtung bis zu einem Randzonenabstand von s = 0,2 mm ermittelt. Weiterführende Untersuchungen zur Schruppbearbeitung konnten zeigen, dass eine weitere Steigerung der Schnittparameter in Form höherer Vorschübe und Schnittgeschwindigkeiten zu einer stärkeren Aufhärtung und einer Verschiebung des Mikrohärteverlaufs führt. Die eintretende Verfestigung begrenzt in diesem Zusammenhang auch die einsetzbaren Parameter bei der Drehbearbeitung des Werkstoffes CN0,85 durch die hohe mechanische Werkzeugbelastung. Beim Schlichtvorgang wirken geringere Kräfte auf das Werkstück, folglich tritt auch eine deutlich reduzierte Aufhärtung und Aufhärtungstiefe, die sich nur geringfügig oberhalb der Grundhärte befindet, auf. Im Vergleich der drei eingesetzten Prozesse weist das Werkstück nach dem Walzen die stärkste Randzonenaufhärtung sowie die höchste Aufhärtungstiefe auf. Die auf die Oberfläche wirkenden Kräfte sind in das Werkstück orientiert und stellen in dieser Weise Druckkräfte dar. Diese begünstigen das Gleiten von Versetzungen, wobei dieses durch Hindernisse im Gefüge behindert wird. Zu erkennen ist diese Versetzungsbewegung an der Bildung von Gleitlinien. Im Gefüge des vorliegenden Werkstoffes stauen sich die Versetzungen vorwiegend an Korn- und Zwillingsgrenzen auf. Zudem bewirken die interstitiellen Elemente zusätzlich eine Mischkristallverfestigung. Hieraus resultiert eine Randzonenverfestigung, die durch höhere Kräfte, wie sie durch die Walzbearbeitung eingebracht werden können, gesteigert werden kann. Verdeutlicht werden diese Effekte bei der Betrachtung der Gefüge, welche bei der Schlicht- und Walzbearbeitung entstehen (Vgl. Abbildung 4). Die Gleitlinien des Werkstückes nach dem Schlichten befinden sich vorwiegend im unmittelbaren Randbereich. Nach der Walzbearbeitung sind hingegen Gleitlinien bis zu einer Aufhärtungstiefe von s = 1 mm zu erkennen.

Abbildung 4: Gefüge in der Randzone nach einem Schlicht- bzw. Walzprozess des Werkstoffes CN0,85
Mittels einer Parametervariation wurde der Einfluss des Walzvorschubes sowie des Walzdruckes auf Rauheit und Verfestigung für die Werkstoffe CN0,85 sowie Magnadur 601 untersucht. Bei Betrachtung der Oberflächengüte des Werkstoffes Magnadur 601 ergeben sich keine signifikanten Unterschiede zwischen den eingesetzten Druckstufen, hingegen sollten kleinere Vorschübe (f = 0,1 mm) für eine gleichmäßige Einebnung des Oberflächenprofils verwendet werden (Vgl. Abbildung 5). Die Variation des Walzdruckes zeigt sich hingegen bei Analyse der Mikrohärte, wobei ein gesteigerter Walzdruck die Aufhärtungstiefe erhöhen kann.
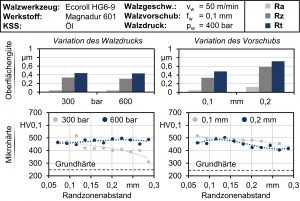
Abbildung 5: Parametervariation bei der Walzbearbeitung des Werkstoffes Magnadur 601
Der Werkstoff CN0,85 weist im Vergleich bereits eine höhere Grundhärte und zudem ein stärkeres Verfestigungsvermögen auf (Abbildung 6). Letzteres ist durch den höheren Anteil an interstitiellen Elementen zu begründen, welche wie erwähnt unter anderem Mischkristallverfestigung und planares Versetzungsgleiten bewirken. Hierbei ist eine Festigkeitssteigerung von bis zu 300 HV0,1 zu erreichen, wobei ein höherer Walzdruck sowohl die maximale Aufhärtung als auch die Aufhärtungstiefe steigern und darüber hinaus die Oberfläche stärker glätten kann. Weiterhin ist für einen konstanten Fest- und Glattwalzprozess für diesen Werkstoff ebenfalls ein Vorschub von f = 0,1 mm zu empfehlen.
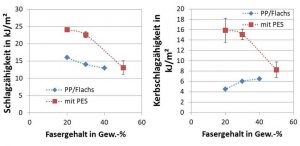
Abbildung 6: Parametervariation bei der Walzbearbeitung des Werkstoffes CN0,85
Zusammenfassung und Ausblick
Die nichtrostenden, amagnetischen Werkstoffe weisen bei der Zerspanung durch ihre hohe Duktilität und Festigkeit sowie die durch den Prozess hervorgerufene Kaltverfestigung besondere Herausforderungen auf. Insbesondere Drehprozesse mit hohem Zeitspanvolumen gehen mit starken mechanischen sowie thermischen Werkzeugbelastungen einher und rufen eine Randzonenverfestigung hervor. Eine an die Drehbearbeitung angeschlossene Walzbearbeitung kann sowohl einen Fest- als auch einen Glattwalzprozess realisieren. Durch die Legierungszusammensetzung der amagnetischen Stähle kann dabei eine signifikante Verfestigung über eine hohe Aufhärtungstiefe umgesetzt werden. Zusammenfassend ermöglicht die mechanische Nachbearbeitung die gezielte Einstellung der Oberflächenintegrität. Hierdurch können in Bezug auf spätere Anwendungsfelder Spannungsrisskorrosion vermieden sowie mechanische Festigkeitssteigerungen erreicht werden. Diese positiven Effekte weisen insbesondere großes Potential für Hightech-Anwendungen auf, bei denen eine gesteigerte Festigkeit und Korrosionsbeständigkeit erforderlich sind.
Literatur
[1] Berns, H.; Theisen, W.: Eisenwerkstoffe Stahl und Gusseisen. 4. Auflage, Springer Verlag, Berlin 2008
[2] Gavriljuk, V.; Berns, H.: High Nitrogen Steels, Springer Verlag, Berlin 1999
[3] Berns, H.; Gavriljuk, V.; Riedner, S.: High Interstitial Stainless Austenitic Steels. Springer Verlag, Berlin Heidelberg 2013, https://doi.org/10.1007/978-3-642-33701-7
Autoren:
Rinschede, T., Felinks, N., Niederhofer, P., Herrera, C., Biermann, D.