„Mit diesem Konzept haben wir 2014 wieder ein neues Level erreicht“, verkündet Vertriebsleiter Andreas Goseberg. Denn für die Schmale Maschinenbau GmbH ist die inzwischen beim Kunden installierte Anlage nicht nur das größte Einzelprojekt, das die Firma bisher realisiert hat. Die neue Produktionslinie zur Warmumformung von Draht bis zu einem Durchmesser von 24 mm kann zudem mit einigen Highlights aufwarten. „Und sie ist geradezu ein Paradebeispiel für die Vielfalt und die Spannbreite der Technologien, die unser Baukasten abbilden kann“, fügt Goseberg an.
Das Unternehmen aus Altena schnürt für jedes individuelle Fertigungsproblem ein passgenaues Paket. „Jede Technologie kann dazu nach dem Baukasten-Prinzip mit anderen kombiniert werden und ist bei uns an kein bestehendes Maschinenkonzept gebunden“, erläutert der Vertriebsleiter. Das aktuelle Projekt zeige dies in beeindruckender Weise, u. a. mit der verwendeten Servo- und Pressentechnik, einer integrierten Induktionsanlage, einem Tunnelofen sowie einem speziellen Bunkermagazin, das Stillstandszeiten vermeidet.
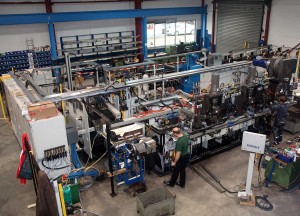
Typisches Beispiel für den Schmale-Baukasten: Die Warmumformungsan-
lage fertigt bis zu 1,5 kg schwere Biegeteile aus einen 24-mm-Stahldraht.
(Fotohinweis: Schmale Maschinenbau)
Signifikante Steigerung der Produktivität
Die erste Herausforderung ergab sich für das Schmale-Team gleich zu Beginn der Fertigungslinie. Durch das hohe Produktgewicht von bis zu 1,5 kg wird ein Coilwechsel alle ein bis anderthalb Stunden notwendig, was einen Anlagenstillstand von jeweils mindestens 20 Minuten zur Folge hätte. Die Sauerländer entwickelten deswegen ein Bunkermagazinsystem, das die Anlage automatisch befüllt und Material zwischenpuffert. Direkt vom Haspel durch ein Richtwerk gezogen und danach abgeschnitten, wird das Coilmaterial als fertig gelängte Stäbe in einem Magazin gebunkert. Die Maschine läuft bis hierhin mit einer höheren Taktgeschwindigkeit als der weitere Bearbeitungsprozess, um eine ausreichende Reserve für die Phasen der häufigen Coilwechsel aufzubauen. „Damit haben wir es geschafft, den Zeitverlust von täglich mehreren Stunden zu eliminieren“, so Andreas Goseberg. „Unterm Strich steht eine signifikante Steigerung der Produktivität.“
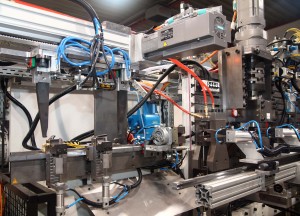
Übernahmestation: Die durch Induktion auf rund 650 Grad erwärmten Stab-
abschnitte werden an den normalen Maschinentransfer übergeben.
Von Raumtemperatur auf 650 Grad Celsius
Wie bereits die Bestückung des Bunkermagazins erfolgen die Entnahme und Zuführung der Stababschnitte in die sich anschließende Induktionsanlage über servoelektrisch angetriebene Handlings. Im Gegensatz zum eigentlichen Bearbeitungszentrum erfordert die Erwärmung des Materials auf 650 Grad Celsius einen erheblichen Energieeinsatz. Der bis zu 1,5 kg schwere Artikel muss auf der gesamten Länge durchgehend temperiert werden. Bei einer Taktleistung von 30 Stück bedeutet dies, dass bis zu 45 kg Stahl in der Minute zu erhitzen sind. Sämtliche Werkzeugkomponenten des folgenden Produktionsprozesses müssen nun mittels eines geschlossenen, internen Systems aktiv gekühlt werden. Die Übergabe der heißen Stäbe erledigt wiederum ein entsprechend mit Kühlbohrungen ausgestattetes, servoelektrisch angetriebenes Handling.
Servo-Aggregate für Drahtdurchmesser von 24 mm
Von der Übernahmestation geht es über einen servoelektrischen Lineartransfer zur ersten Bearbeitungsstation der erwärmten Abschnitte. Hier wird eine Fase an einem Ende der Stäbe angepresst und ein Produktcode aufgestempelt. Den beiden Fertigungstechnologien schließt sich eine Besonderheit an, wie der Firmensprecher betont. „Zwei nacheinander folgende servoelektrische Drehbieger erzeugen je eine 180-Grad-Biegung in nur einem Schritt.“ Zudem sei dabei nicht zu vergessen, dass sämtliche Aggregate sehr robust ausgelegt sein müssen, um Drahtdurchmesser von 24 mm problemlos bewältigen zu können. Das gilt natürlich auch für die nächste Station mit Linearbiegeschiebern. Den letzten Bereich im eigentlichen Umformungsprozess bildet eine 120-t-Servopresse, die neben ihrer Funktion als Kalibrierpresse zusätzliche Prägungen am Artikel vornimmt. „Das Durchtakten durch verschiedene Stationen mit gleichzeitig mehreren Operationen ist sehr typisch für unsere Maschinenbauweise und ermöglicht die relativ hohen Taktleistungen“, erklärt der leitende Schmale-Mitarbeiter. Zum Schluss werden die Drahtbiegeteile einem Tunnelofen zugeführt und auf Härtetemperatur gebracht – Goseberg: „Und damit haben wir ein vom Coil durchlaufend auf der Maschine gefertigtes und vergütetes Endprodukt.“
Pressefotos und Pressetexte als Download unter
www.schmale-gmbh.de/presse