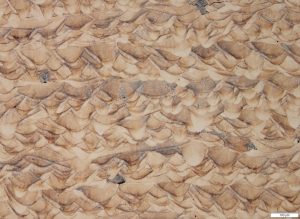
Bild 1: Gefüge von 3D-gedrucktem Stellite Celsit 21, geätzt mit Murakami (Fem18)
Stellite als Verschleißschutzlegierungen aus Kobalt, Chrom, Wolfram oder Molybdän, Nickel, Eisen und 0,3 bis 3,2 % Kohlenstoff haben sich einen festen Platz in der Technik gesichert. Erzeugt werden sie durch Gießen, Sintern oder als Beschichtung durch verschiedene Schweiß- oder Strahlverfahren. So besitzen Stellite bei Beanspruchungen auf abrasiven, adhäsiven und korrosiven Verschleiß Eigenschaften, die sie für eine Reihe von anspruchsvollen Anwendungen interessant machen. Durch die bisherigen Fertigungsverfahren war es nicht möglich, filigrane Strukturen wie oberflächennahe Kühlkanäle oder Ähnliches zu realisieren.
In einem gemeinsamen Forschungsprojekt des Instituts für Werkzeugforschung und Werkstoffe Remscheid (IFW) und dem Institut für Umformtechnik und Umformmaschinen der Leibniz-Universität Hannover (IFUM) ist es den Remscheider Mitarbeiter*innen gelungen, Stellitepulver für das selektive Laserstrahlschmelzen (LPBF/SLM) zu qualifizieren. Genutzt wurden Pulver der Deutschen Edelstahlwerke (DEW) vom Typ Celsit 21 und Celsit F. Dabei war es möglich, Celsit 21 ohne Vorwärmung mit einer Härte von 42 HRC und einer relativen Dichte von > 99,75 % zu drucken.
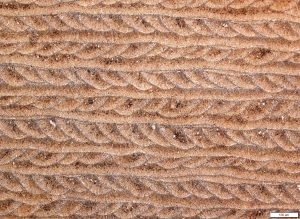
Bild 2: Gefüge von 3D-gedrucktem Stellite Celsit F, geätzt mit Murakami (Fem18)
Für den rissfreien Druck des mit 56 HRC deutlich härteren und mit 1,9 % deutlich kohlenstoffreicheren Celsit F wurde das Pulverbett auf 800 °C vorgewärmt. Auch hier wurde eine ähnliche relative Dichte von > 99,9 % erzielt.
Das Forschungsprojekt befasst sich mit der Entwicklung und Erprobung von Schmiedegesenken mit konturnaher Kühlung der besonders verschleißgefährdeten Konturbereiche. Beim Warmmassivumformen beträgt die Temperatur des Rohlings 1200 bis 1250 °C. Zwischen den Schmiedehüben wird das Gesenk zur Kühlung und Schmierung mit einer Emulsion besprüht, sodass die Oberfläche extremen Temperaturwechseln ausgesetzt ist, die in relativ kurzer Zeit zu einer Gefügezerrüttung, Herausbrechen von Stahlkörnern und letztendlich zu Rissbildung führen. Verstärkt wird der Prozess an den Stellen der Kontur mit besonders hoher thermomechanischer Belastung sowie mit hohen Gleitwegen. Auch die abrasive Wirkung von Zunderpartikeln der Rohlinge, die hohe Adhäsionsneigung von temporär austenitisierten Oberflächen sowie die Schubspannung in diesen Bereichen sorgen für eine hohe Beanspruchung des Werkzeugs. In Schnellschmiedeprozessen beträgt die Lebensdauer der Gesenke meist nur eine halbe bis eine ganze Schicht. Da der Gesenkwechsel etwa eine Stunde Zeit in Anspruch nimmt, senken die Rüstkosten die Produktivität um bis zu 25 %.
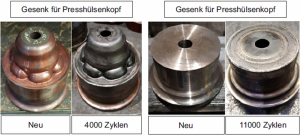
Bild 3: Zwei Gesenke für Presshülsen-Köpfe aus nitriertem Warmarbeitsstahl, neu und verschlissen nach 4000 Zyklen und 11000 Zyklen
Der Ansatz des Forschungsprojekts ist es deshalb, ein Material mit höherer Warmhärte und geringerer Adhäsionsneigung zu qualifizieren und darüber hinaus mit einer innenliegenden Kühlung der kritischen Kontur für eine gleichmäßigere Gesenktemperatur zu sorgen, um so der Gefügezerrüttung entgegenzuwirken.
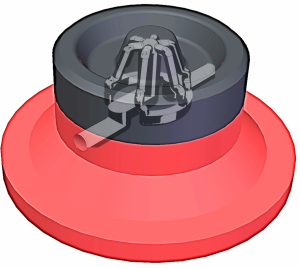
Bild 4: Prinzipskizze des hybriden Schmiedegesenks mit Kühlkanälen
Zur Reduzierung der Herstellkosten des 3D-gedruckten Bauteils wurde auf eine hybride Bauweise zurückgegriffen. Die Basis des Gesenks ist aus einer Nickelbronze gefertigt, die einen dem gedruckten Stellite ähnlichen Wärmeausdehnungskoeffizienten besitzt und Wärme gut leitet und damit verteilt. Die Verbindung erfolgt durch eine Hochtemperaturlötung.
Testweise wurde ein gedrucktes Stellitegesenk mittels Diamantdraht aufgetrennt, um die Druckqualität der Kühlkanäle zu kontrollieren. Die Oberflächenqualität wird als ausreichend beurteilt, soll aber noch durch ein Strömungsschleifen verbessert werden. Dazu wird ein abrasivhaltiges Polymer mit hohem Druck durch die Kühlkanäle gepresst, sodass Oberflächenqualitäten von geschliffen bis poliert erreicht werden können.
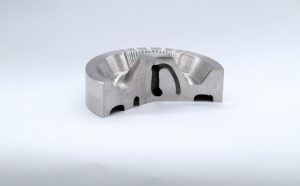
Bild 5: 3D-gedrucktes Gesenk aus Stellite, aufgetrennt zur Sichtbarmachung der Kühlkanäle
Neben den Anwendungen in der Warmumformtechnik werden auch Applikationen in der gekühlten/gespülten Bohrtechnik für abrasive Materialien, in der Einspritztechnik von Verbrennungsanlagen, für hochbeanspruchte druckgeschmierte Gleitlager und zahlreiche weitere technische Herausforderungen erwartet. Mit der vorhandenen 3D-Druckanlage, der Aconity MIDI mit Bauraumheizung, können Teile bis zu 170 mm Durchmesser und 190 mm Höhe hergestellt werden, sodass ein weiter Bereich von Applikationen abgedeckt werden kann.
Das IGF-Vorhaben 20773 N der Forschungsvereinigung Forschungsgemeinschaft Werkzeuge und Werkstoffe e.V. (FGW), Papenberger Straße 49, 42859 Remscheid wurde über die AiF im Rahmen des Programms zur Förderung der Industriellen Gemeinschaftsforschung (IGF) vom Bundesministerium für Wirtschaft und Energie aufgrund eines Beschlusses des Deutschen Bundestages gefördert.
Autoren:
Hans-Jürgen Gittel, Robin Roj, Jan Hendrick Verhrs
Institut für Werkzeugforschung und Werkstoffe e.V. (IFW), Remscheid
Institut für Umformtechnik und Umformmaschinen (IFUM), Leibniz Universität Hannover