Möglichkeiten der Zerspansimulation
Mit fortschreitender Digitalisierung in der Produktionstechnologie gewinnt auch die Zerspansimulation bei der Entwicklung von Präzisionswerkzeugen zunehmend an Bedeutung. Die überwiegend auf der Finite Elemente Methode (FEM) basierenden Ansätze erlauben es, komplexe Geometrievarianten mit wenig Aufwand im frühen Entwicklungsstadium zu simulieren. Die Ergebnisse ermöglichen eine Beurteilung hinsichtlich der Spanbildung sowie der thermomechanischen Belastungen an der Schneidkante und dem Werkzeugkörper. Der Simulationseinsatz bietet Einsparpotenziale in der Entwicklung, da vielversprechende Designs frühzeitig identifiziert und die Anzahl realer Prototypen und Maschinentests verringert werden können. Abb. 1 stellt exemplarisch die mechanische Belastung eines Kugelfräswerkzeugs durch Zugspannungsanteile am Übergang der Schneide zum Werkzeugkörper bei unterschiedlichen Schnittbedingungen gegenüber.
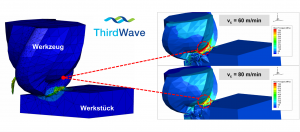
Abb. 1: Mechanische Belastung (Max. Hauptnormalspannung) eines Werkzeugs bei unterschiedlichen Schnittgeschwindigkeiten, berechnet mit dem kommerziellen System AdvantEdge v7.7 (Third Wave Systems, Inc. USA)
Grundvoraussetzung für den erfolgreichen Einsatz simulativer Methoden sind vor allem valide Ergebnisse. Aber auch stabile Berechnungsläufe sowie einfache und intuitive Simulations-Setups, die helfen den komplexen Eingriff der Werkzeugschneide zu definieren, sind notwendig. Die letzten Punkte sind Stand der Technik und häufig Bestandteil moderner Softwarepakete, wie beispielsweise dem in Abb. 1 genannten System AdvantEdge. Die Validität der Simulationsergebnisse hängt wesentlich von den verwendeten physikalischen Basisdaten ab. Hier sind insbesondere das Werkstoffmodell sowie die werkstoffspezifischen Kennwerte als Haupteinflussfaktoren zu nennen [1].
Herausforderungen bei der Bestimmung von Materialkennwerten
Typische in FEM Software genutzte empirische Werkstoffmodelle beschreiben die Fließspannung des Werkstoffs als Funktion der lokal vorliegenden Dehnungen, Dehnraten und Temperaturen. Die Herausforderung bei der Bestimmung der Materialkennwerte liegt darin, dass diese Zustandsgrößen bei Zerspanprozessen stark lokalisiert und überlagert in der Scherzone des Materials vor der Schneidkante vorliegen. Die Werte der Dehnung, Dehnrate und Temperatur übersteigen dabei in vielen Fällen die in klassischen Werkstoffprüfungen erreichbaren Zustände um ein Vielfaches. Für die Zerspanung werden beispielsweise Dehnungen von bis zu 10, Dehnraten zwischen 103 und 106 s-1 und Temperaturen bis zu
90 % der Schmelztem-peratur genannt [2]. Werden Zylinderstauchversuche oder auch Split-Hopkinson Versuche als Basisexperimente der Kennwertermittlung eingesetzt, sind daher Extrapolationsfehler möglich. Alternative inverse Ansätze basieren demgegenüber auf Zerspanversuchen. Diese können das reale Lastkollektiv im Material bestmöglich annähern. Extrapolationsfehler können so reduziert werden. Gegenüber Werkstoffprüfverfahren ist aber die konkrete messtechnische Erfassung der thermischen und mechanischen Lastbedingungen im Material vor der Schneidkante deutlich erschwert. In Werkstoffprüfversuchen, wie dem Zylinderstauchversuch zur Bestimmung von Fließkurven, sind die exakten Probenabmessungen bekannt. Die Spannungen und Dehnungen im Material können so präzise bestimmt werden. In Zerspanversuchen ist das nicht möglich, da die für die Materialverformung verantwortlichen Kräfte und die resultierenden Dehnungen nicht direkt gemessen werden können. Ein neuer Ansatz zur Weiterentwicklung inverser Kennwertermittlungsmethoden basiert daher auf digitalen Bildkorrelationsverfahren (engl. Digital Image Correlation, DIC). Ziel ist es, die lokalisierten Dehnungsfelder vor der Schneidkaten optisch zu erfassen und zusammen mit Prozesskraftmessungen für die Kennwertermittlung nutzbar zu machen [3].
Inverse Kennwertermittlung durch digitale Bildkorrelation
Die besondere Herausforderung bei dem Einsatz der DIC-Methodik in der Zerspanung besteht darin, die lokalisierten Dehnungsfelder mit einer hinreichenden Auflösung und in Zeitabständen von wenigen µs zu erfassen. Erst dadurch wird eine Anwendung von Bildkorrelationsverfahren möglich, die prinzipiell auf einer Mustererkennung und -verfolgung basieren. Hierzu wurde ein neuer Versuchsaufbau entwickelt, der in Abb. 2 dargestellt ist und auf einem linear-orthogonalen Zerspanprozess basiert.
![Abb. 2: Experimenteller Aufbau zur inversen Bestimmung von Materialkennwerten durch linear-orthogonale Zerspanversuche [4]](https://werkstoffzeitschrift.de/wp-content/uploads/2021/05/Abbildung2-300x238.png)
Abb. 2: Experimenteller Aufbau zur inversen Bestimmung von Materialkennwerten durch linear-orthogonale Zerspanversuche [4]
![Abb. 3: Ergebnis einer Scherdehnungsmessung nach [5]](https://werkstoffzeitschrift.de/wp-content/uploads/2021/05/Abbildung3-300x151.png)
Abb. 3: Ergebnis einer Scherdehnungsmessung nach [5]
Weitere Versuchsmöglichkeiten mit dem in Abb. 2 dargestellten System liegen im Bereich der Grundlagenuntersuchungen zur Zerspanung. Beispielsweise wird der Einfluss der thermophysikalischen Eigenschaften von Beschichtungssystemen auf Spanbildung und Einsatzverhalten von Präzisionswerkzeugen untersucht [7]. Die Möglichkeiten der Versuchsgestaltung sind flexibel erweiterbar. Neben den DIC-Messungen können auch Temperaturmessdaten auf Basis pyrometrischer oder thermografischer Messsysteme ermittelt und zusammen mit Prozesskräften synchron erfasst werden.
Reduzierung von Extrapolationsfehlern
Da die mit den linear-orthogonalen Versuchen erzeugten Umformbedingungen im Material nahe an realen Spanbildungsprozessen liegen, können Kennwerte mit hoher Abbildungsgüte berechnet werden. Auf diesen Modellparametern basierende Simulationen zeigen eine verbesserte Abbildungsgüte im Vergleich mit Simulationsrechnungen, die Kennwerte verwenden, welche aus Stauch- und Split-Hopkinson Versuchen stammen [4]. Die Abbildungsgüte beschreibt dabei den Grad an Übereinstimmung zwischen Simulationsergebnissen und realen Versuchsdaten. Als Vergleichsgrößen werden die Prozesskräfte und die Spandicke genutzt. Die patentierte Methodik zur Kennwertermittlung wird im Rahmen eines Spin-off (solid flow GmbH) weiterentwickelt und in Lizenz im industriellen Kontext genutzt.
Literatur
[1] Klocke, F., Lung, D. und Buchkremer, S.: Inverse Identification of the Constitutive Equation of Inconel 718 and AISI 1045 from FE Machining Simulations. Procedia CIRP, 8 (2013), 212-217
[2] Jaspers, S. P. F. C.: Metal Cutting Mechanics and Material Behaviour. Dissertation, Technische Universität Eindhoven 1999
[3] Thimm, B., Steden, J., Reuber, M. und Christ, H. J.: Using Digital Image Correlation Measurements for the Inverse Identification of Constitutive Material Parameters applied in Metal Cutting Simulations. Procedia CIRP, 82 (2019), 95-100
[4] Thimm, B.: Werkstoffmodellierung und Kennwertermittlung für die Simulation spanabhebender Fertigungsprozesse. Dissertation, Universität Siegen 2018
[5] Thimm, B., Glavas, A., Reuber, M. und Christ, H.-J.: Determination of Chip Speed and Shear Strain Rate in Primary Shear Zone Using Digital Image Correlation (DIC) in Linear-Orthogonal Cutting Experiments. Journal of Materials Processing Technology, 289 (2020)
[6] Agmell, M., Ahadi, A., and Ståhl, J.-E.: Identification of Plasticity Constants from Orthogonal Cutting and Inverse Analysis. Mechanics of Materials, 77 (2014), 43-51
[7] Glavas, A., Thimm, B., Teppernegg, T. und Czettel, C.: Investigation of the Influence of Different Hard Coatings on Chip Formation and Process Forces When Machining Duplex Steel 1.4462. MIC Procedia, (2020), 13-19
Autoren
Benedikt Thimm
Institut für Werkzeug- und Fertigungstechnik
Rheinische Fachhochschule Köln
Mail: benedikt.thimm@rfh-koeln.de
Tel. +49(0)221/54687-737
Martin Reuber
Institut für Werkzeug- und Fertigungstechnik
Rheinische Fachhochschule Köln
Mail: martin.reuber@rfh-koeln.de
Tel. +49(0)221/54687-749
Hans-Jürgen Christ
Institut für Werkstofftechnik
Universität Siegen
Mail: Hans-Juergen.Christ@uni-siegen.de
Tel. +49(0)271/740-4658